粉末噴涂工序少,產生的問題的環節也少。主要工序只有前處理、靜電噴涂和烘烤三個工序。其中影響質量的主要工序應屬前處理工序。然而許多生產廠家對此沒引起足夠的重視,以致帶來許多后患。有些隱患還不是短期內能反映出來。一般較先進的工藝、用在前處理上的花費約占總費用的25%以上。
從生產工藝中出現的各種問題分析。我認為設備的先進程度和原料的好壞,對產品質量又起著決定性作用,兩者缺一不可。我們作為工程技術人在這個問題上應該建立共識,決不能在上新噴粉生產線時。只圖一時省錢就湊和,采用低標準的生產設備和工藝、材料,必將給長期生產帶來許多后患,甚至生產不出高質量產品。不少廠家上了涂粉生產線,應用不久就被迫下馬或跟換新設備,概出于以上原因。我們??吹絿猱a品表面涂裝很漂亮,其主要原因之一是他們不斷地采用先進的設備和新工藝新材料。
從這個意義上分析,對涂粉設備及涂料生產廠家來講,在當今市場競爭條件下,非優質設備和涂料是沒有發展前途的。特別是在國內上百個噴粉設備和粉末涂料生產廠家競爭條件下,更是如此。僅我們陜西省已經有近十家設備及粉末涂料生產廠轉產或倒閉。
產生缺陷的分析探討
(一)前處理方面:
1、除油除銹不徹底
首先我不主張用除油除銹二合一的工藝。二合一工藝本身容易產生這個問題。因為通常用的除油、除銹液配方事項互消弱的,而不是相輔相成的,因此很難搞出合理的二合一或三合一工藝(包括磷化)配方。另一工藝方發式用金屬清凈劑處油,更不能徹底除油。因為金屬清洗劑除油效果差,一般只能是油脂浮到金屬機體表面上,要除掉它,還需一種機械力,如沒有這種外加機械力,就會造成處油不徹底,可見金屬清洗劑不適合于工業化批量生產。我主張用堿化學除油。堿液對動植物油去除效果很好,因其產生皂化反應。但對礦物油去除效果較差,為去除礦物油,還需加乳化劑。另外水洗質量對去油效果影響較大,一是水質,二是水溫。三是要分級翻動,三項均良好,目的只有一個,就是用純凈水清洗油脂。最后一級最好用去離子水清洗。
2、磷化膜粗糙等問題
鋼鐵件噴粉前必須磷化,國外普遍采用的是噴沙磷化工藝。我們用的磷化液,許多是不夠理想的,這就直接影響到磷化膜質量。比較常見的是磷化膜粗糙問題。對此我想從三個方面進行分析:第一是選好磷化液,這是保證質量的根本。首先涉及的問題是選高、中、低溫那種類型?從其發展史來看,開始是有高溫厚膜型,現已進展到中、低溫薄膜型。國內低溫磷化液,由于溶液不夠穩定,維護困難,磷化膜附著力較差,有的甚至不耐水沖洗等,較少被采用。有的低溫磷化液較理想,但價格又較貴。盡管低溫磷化是發展方向,但達到普遍應用的效果,還有待于新的突破。目前祥和磷化(成都)公司已成功的解決了常溫磷化(鈍化)粉劑問題,并已批量供貨。目前普遍采用的還是中溫磷化工藝。其次是選鋅系,鐵系\鋅鈣系等那一種磷化液?相比之下,我認為鋅鈣系磷化液較好,對噴塑前處理要求薄涂層磷化膜來考慮,鐵系亦是一種較好的選擇。它除了鋅系的一些優點外還具有耐熱性好。中溫條件下水解少,沉渣較少,溶液易維護,機械強度好,耐蝕性強,膜較厚時結晶仍很細。而鐵系的磷化鐵膜,耐蝕性較差??傊x中溫鋅鈣系磷化液較好。第二是必須隨時調整磷化液,主要是調整酸度比和含鋅量,這兩個因素都直接影響成膜率和結晶的粗細度。必需根據工作量定期和不定期的分析溶液,及時加以調整,無分析數據,盲目補充料液是不科學的。第三是控制膜層的厚度各類磷化膜都有其最佳厚度,例如鋅系和鈣鋅系最佳膜厚為1.5~2克每平方米,而鐵系為0.5~0.7克每平方米,在這個范圍內其防腐性能最好,晶粒最細如過厚著影響膜的柔韌性和附著力,晶粒也變粗。通常生產中出現的問題是磷化膜偏厚。下面就如何克服晶粒變粗問題談幾點意見。
第一是用表面調整劑的辦法使晶粒變細化。即在工件磷化前進行一次表面調整處理,使金屬表面吸附一層膠體粒子,形成一層“活化中心”,進而磷化時,在次“活化中心”上繼續成長,這樣可使磷化晶粒明顯變細,特別是低溫磷化之前,表調是不可少的一步處理方法。
第二是往磷化液中加晶粒細化劑,如鈣、鎳等鹽類作改進劑,最好用復和型鹽類,效果更好,同時可降低低沉渣量。
第三是磷化后進行鈍化處理,使磷化膜上面形成的峰窩結構,從而提高耐蝕性能,同時提高涂層的附著力。
第四是隨時調整磷化液的酸度比和鋅含量。前面已談過了。
(二)靜電噴粉方面:
1、噴粉不均主要是供粉桶內粉末流化不均勻所致。應更換微孔板或調節微孔板下的供氣系統,使使粉層恢復正常沸騰狀態,即可消除。有是氣壓偏低,則加大氣壓即可消除。另一可能是管道堵塞,包括文丘里咀堵塞,則需清理管路。若文丘里經常堵塞,則屬文丘里的積粉咀用材(如黃銅等)不當,只要把他改成聚四佛乙烯材料,就可以解決,噴槍頭堵塞也可用同樣的方法解決,如果供粉同捅不是流化床型的,則需改善攪拌器或加裝振湯器,防止粉層出現空洞,供不上涂料。 2、粉末上粉率低:
(1)電壓低或無高壓是主要原因之一。需調高輸出電壓或維修高壓靜發生器。
(2)工件接地不良,掛鉤或低層電阻大;如噴第二遍粉時或膩予不導電,都會使低層電阻大。用普通噴槍噴第二遍粉時必須把工件預熱到104℃左右,進行熱噴,利用熱溶吸附的原理。熱噴作業還有利于粉末流平,用變色龍噴槍,可以克服低層電阻大的問題,第二遍噴涂可以實現冷噴。它是利用附加板行成噴室恒定靜電場的原理實現的。
(3)粉末荷電量過大或小也影響上粉率。對環氧型粉末實驗結果;當粉末帶電電量為1.6微庫侖/克時,上粉率可達百分之九十五以上。而電暈放電噴槍只能使粉料帶電0.8~0.9微庫侖,所以上粉率只達百分之八十五左右。這個數椐說明帶電量對上粉率的影響。因此摩擦噴槍不如靜電噴槍上粉率高。一般控制電流不須過大,60微庫侖左右已夠用了,否則荷電量太大,也容易引起過流斷電,過大反而容易引起法拉第屏遮效應。一般是荷電量影響上粉率,荷電量小原因,除了不同粉末涂料的自身反電離效應有差別外,主要原因是由于高壓靜電發生器故障引起,需進行維修,使恢復高壓。
(4)氣壓過大:會抵消靜電引力。使付在工件上的粉末被吹掉,降低上粉率。實驗結果表明;當輸送空氣量為3升/秒時,上粉率百分之就九十五左右,而加大氣量時,而輸粉空氣量每增加一升/秒時,則上粉率降低百分之二到三。
3、施工時打火這個問題一般不存在了,因為高壓靜電發生器現在大多裝有恒壓、恒流保護線路。老式噴槍有著個問題。打火原因如下:
(1)槍與工件距離太近和粉末在靜電場內濃度大,超過了極限濃度,是重要原因。
(2)內電阻小,導致電流過大。
(3)電壓太高:實驗證明:場強在1kv/cm時,吸附效率已接近飽和。此后場強再增加三倍,涂覆效率只增加百分之三到五。所以電壓太高不可取,反而容易引起打火。一般控制在60kv已夠用了。
4、涂層有縮坑:
(1)多數情況是由工件表面不撤底引起,有的是壓縮空氣中含油引起。因為油點明顯影響粉層固化時的表面張力。
(2)粉末涂料的內在應素如混入了不同廠家或批次的粉粒,引入硅塵,也會影響其固化時表面張力的均勻性,造成縮坑。
5、涂層有針孔起泡:涂層下面的氣體在烘干過程中到達涂層表面,突破界面者為針孔,來不及排除者為氣泡。涂層中的氣體可以是空氣、水蒸氣或氫氣(鍍鋅層中帶來的)等。根本解決方法是噴涂前徹底排除氣體。小量的無法排除的氣體,也可用控制烘干和噴涂條件的方法避免產生針孔或氣泡。據計算,排除涂層的空氣需要26秒,在除膜開始固化前的安全熔融流平段(100~135℃)升溫慢些。給予足夠的排氣時間?;虿扇」ぜA熱后噴粉的方法,均有效果。
6、涂層有橘皮:產生橘皮的主要原因來自粉末涂料自身的流平性差。施工也有影響,是屬次要因素。
更多關于材料方面、材料腐蝕控制、材料科普等等方面的國內外最新動態,我們網站會不斷更新。希望大家一直關注中國腐蝕與防護網http://www.ecorr.org 責任編輯:王元 《中國腐蝕與防護網電子期刊》征訂啟事
投稿聯系:編輯部
電話:010-62313558-806
郵箱:ecorr_org@163.com
中國腐蝕與防護網官方 QQ群:140808414
免責聲明:本網站所轉載的文字、圖片與視頻資料版權歸原創作者所有,如果涉及侵權,請第一時間聯系本網刪除。
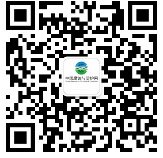
官方微信
《中國腐蝕與防護網電子期刊》征訂啟事
- 投稿聯系:編輯部
- 電話:010-62316606-806
- 郵箱:fsfhzy666@163.com
- 中國腐蝕與防護網官方QQ群:140808414