所謂帶鋼,通常是指那種對厚度和寬度有嚴格限制的產(chǎn)品。帶鋼在冷狀態(tài)(常溫)條件下,或在再結晶溫度以下,經(jīng)軋制后達到塑性變形的目的,通常稱為冷軋帶鋼,習慣上往往叫做冷帶。冷軋窄帶鋼生產(chǎn)畢竟有其簡便、靈活、投資少、收效快等特點。為適應我國國情,必須進一步提高冷軋窄帶鋼生產(chǎn)的技術水平。普碳鋼帶經(jīng)酸洗、水洗和干燥后,其表面應呈灰白色或銀白色。但因操作不當、酸洗工藝制度和某些機械設備不良的影響,往往會造成帶鋼的不同缺陷。這些缺陷主要有:酸洗氣泡、過酸洗、欠酸洗、銹蝕、夾雜、劃傷和壓痕等。這些缺陷占冷軋產(chǎn)品缺陷的2%左右,其中主要是欠酸洗、過酸洗和酸洗氣泡等。
(1)酸洗氣泡。酸洗氣泡是由于酸與裸露的金屬作用生成氫氣所造成的。它在冷軋時會發(fā)生噼啪的爆炸聲,它的外觀特征是呈條狀的小鼓泡,破裂后呈黑色細裂縫。經(jīng)過軋制后,氣泡裂縫會延伸擴大,致使產(chǎn)品的力學性能(沖擊韌性)降低。
酸洗氣泡產(chǎn)生的機理是:金屬和酸產(chǎn)生化學反應時,生成了部分氫原子,它滲透到金屬的結晶格子中,并使其變形,變形后使氫更向金屬內(nèi)擴散,其中一部分氫原子穿過金屬并分子化,從酸液中逸出,部分氫原子的分子化在晶格變形產(chǎn)生的“顯微空孔”邊界上,或金屬的夾雜及孔隙中進行,氫在空孔中的壓力可達到很大值(幾十兆帕),使金屬中產(chǎn)生了引起氫脆的內(nèi)應力。
防止產(chǎn)生氣泡的措施是:調(diào)整酸液的濃度;控制酸洗時溶液的溫度和帶鋼表面平直狀態(tài)等。
(2)過酸洗。金屬在酸溶液中停留時間過長,使其在酸溶液作用下,表面逐漸變成粗糙麻面的現(xiàn)象稱為過酸洗。
過酸洗的帶鋼延伸性大大降低,在軋制過程中,很容易斷裂和破碎,并且造成粘輥。過酸洗的帶鋼即使軋制成材也不能作為成品,因為它的力學性能大大降低了。
產(chǎn)生過酸洗的原因是:機組連續(xù)作業(yè)中斷,使酸洗失去連續(xù)性,或因帶鋼斷帶處理時間過長等。防止措施是盡量密切全機組的操作配合,保證生產(chǎn)正常進行。
(3)欠酸洗。鋼帶酸洗之后,表面殘留局部未洗掉的氧化鐵皮時稱為欠酸洗。欠酸洗的帶鋼(或鋼板),輕者在軋制之后產(chǎn)品表面呈暗色或花臉狀;嚴重時氧化鐵皮被壓入呈黑斑。此外,氧化鐵皮的延伸性較差,故在軋制后因延伸不均使產(chǎn)品出現(xiàn)浪形或瓢曲等缺陷。有時鐵皮可能牢固地貼附在軋輥表面,直接造成軋制廢品增多等。
造成欠酸洗的原因是:氧化鐵皮厚度不勻,較厚部分的氧化鐵皮需要較長酸洗時間,同時其中的Fe0分解成了較難溶解的Fe2O3(Fe3O4);帶鋼波浪度和鐮刀彎較大,在酸洗過程中,起浪部分或彎起部分沒有浸泡在酸液中通過,造成漏酸洗;酸洗前機械破鱗不完善,特別是帶鋼兩邊端鐵皮未被破碎等。
實際生產(chǎn)中欠酸洗多出現(xiàn)在帶鋼的頭尾段和兩側(cè)邊緣。根據(jù)實測數(shù)據(jù),欲酸洗掉大塊紅色鐵皮需要3~4倍的酸洗黑色氧化鐵皮的時間,此時已洗掉鐵皮的帶鋼將會形成過酸洗。因此處理欠酸洗的方法是:預先平整好板形,對于鐵皮較厚,而面積又不大的帶鋼,可采用先局部酸洗一次,而后再過酸洗線的方法去銹。
(4)銹蝕。原料酸洗后表面重新出現(xiàn)銹層的現(xiàn)象稱為銹蝕。
銹蝕形成的原因是:帶鋼(鋼板)酸洗后表面殘留少許的酸溶液,或帶鋼清洗后沒有達到完全干燥而使表面重新生銹。此外,帶鋼在酸洗后于高溫的清洗水中停留時間過長,也會產(chǎn)生銹蝕現(xiàn)象。
帶鋼銹蝕處的鋼板表面在軋制之后呈暗色,它促使成品在庫存時再次銹蝕,從而降低成品材的表面質(zhì)量,嚴重時使產(chǎn)品報廢。
防止銹蝕的措施是嚴格執(zhí)行酸洗、清洗操作規(guī)程,及時給表面涂油,并應堆放在干燥的地方。
(5)夾雜。帶鋼在酸洗后表面出現(xiàn)深陷的星羅棋布的黑點疵病稱為夾雜。它是由于熱軋時氧化鐵皮被壓入所形成的。這樣的缺陷不可能采取酸洗法除去。當它經(jīng)過冷軋后,黑點便擴展延伸呈黑色條狀,大大降低了成品鋼板的沖擊性能。
(6)劃傷。帶鋼在機組運行過程中新出現(xiàn)的劃傷,是由于卷取輥、彎曲輥的表面出現(xiàn)質(zhì)硬的異物,或帶鋼的浪形及折棱與導板成線接觸,或帶鋼在拆卷過程中拍打折頭刮板等,使表面劃出新的傷痕。另外也有部分傷痕出現(xiàn)在熱軋后冷卻和卷取的過程中。
帶鋼的劃傷可分為上表面劃傷和下表面劃傷。劃傷的原料經(jīng)冷軋后,在成品帶鋼表面將形成寬而長的黑條。帶鋼劃傷深度超過帶鋼厚度允許公差一半時,軋制后不能消除。
防止劃傷的措施是經(jīng)常檢查機組的滾動部件和導板,維護好設備。
(7)壓痕。壓痕是指帶鋼(鋼板)表面呈凹下去的壓跡。壓痕形成的原因是:并卷焊時的焊渣沒有吹凈,被帶鋼帶到拉輥上,而后在帶鋼表面壓出了痕;拉輥在帶鋼表面滑動造成粘輥,使帶鋼表面造成壓痕;熱軋過程中壓下失靈,突然壓下停車,而后抬起壓下軋制等。壓痕深度超過帶鋼厚度允許偏差一半時,冷軋之后,壓痕不能消除。
總之,上述帶鋼表面缺陷,只要精心操作,嚴格執(zhí)行酸洗工藝制度和操作規(guī)程,及時檢查和維修設備,是可以避免或減少的。
更多關于材料方面、材料腐蝕控制、材料科普等方面的國內(nèi)外最新動態(tài),我們網(wǎng)站會不斷更新。希望大家一直關注中國腐蝕與防護網(wǎng)http://www.ecorr.org
責任編輯:殷鵬飛
《中國腐蝕與防護網(wǎng)電子期刊》征訂啟事
投稿聯(lián)系:編輯部
電話:010-62313558-806
郵箱:fsfhzy666@163.com
中國腐蝕與防護網(wǎng)官方 QQ群:140808414
免責聲明:本網(wǎng)站所轉(zhuǎn)載的文字、圖片與視頻資料版權歸原創(chuàng)作者所有,如果涉及侵權,請第一時間聯(lián)系本網(wǎng)刪除。
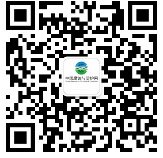
官方微信
《中國腐蝕與防護網(wǎng)電子期刊》征訂啟事
- 投稿聯(lián)系:編輯部
- 電話:010-62313558-806
- 郵箱:fsfhzy666@163.com
- 中國腐蝕與防護網(wǎng)官方QQ群:140808414