鈦合金的比強(qiáng)度較高、抗腐蝕性優(yōu)異以及高溫性能良好,在航空航天領(lǐng)域得到了廣泛的應(yīng)用。同時(shí),鈦合金與碳纖維復(fù)合材料具有相近的電極電位,成為復(fù)合材料結(jié)構(gòu)連接的首選材料。隨著對(duì)新型航空航天器結(jié)構(gòu)減重、抗疲勞、耐腐蝕的要求逐漸提高和復(fù)合材料用量的大幅度增長(zhǎng),對(duì)鈦合金緊固件的需求日益增加。對(duì)緊固件用材料的靜強(qiáng)度和動(dòng)強(qiáng)度都有嚴(yán)格的要求,這就較大地限制了可選擇的鈦合金種類。因此,近50多年來航空航天緊固件行業(yè)普遍使用的鈦合金只有Ti-6Al-4V。
Ti-6Al-4V鈦合金緊固件受到強(qiáng)度(1100 MPa級(jí))和淬透性(最大可使用尺寸約19 mm)方面的限制,很難滿足新型航空航天器主承力結(jié)構(gòu)減重、可靠性和長(zhǎng)壽命的要求。針對(duì)更高強(qiáng)度等級(jí)(1240 MPa級(jí)以上級(jí))鈦合金緊固件的需求,近年來開展了大量的探索工作[1,2,3,4]。目前有望成為用以制造1240 MPa級(jí)以上緊固件的高強(qiáng)鈦合金大多為應(yīng)力缺口敏感性材料,對(duì)表面的完整性要求較高。許多表面因素,如污染、劃傷、夾雜、腐蝕等均能誘發(fā)疲勞裂紋的萌生和擴(kuò)展,使緊固件斷裂[5,6],這就使許多在研中的高強(qiáng)鈦合金緊固件的疲勞性能難以滿足要求。因此,系統(tǒng)分析表面缺陷引起的疲勞失效以及增壽機(jī)理,對(duì)鈦合金緊固件的可靠使用有重要的意義。
Ti-3Al-8V-6Cr-4Mo-4Zr(Ti-38644)合金作為一種亞穩(wěn)型β鈦合金,具有比強(qiáng)度高、耐腐蝕性能好和室溫成型性能強(qiáng)等優(yōu)點(diǎn),是制造高性能航空緊固件的理想材料。經(jīng)過固溶+時(shí)效處理的Ti-38644鈦合金其室溫抗拉強(qiáng)度可達(dá)1380 MPa,通過控制時(shí)效溫度和時(shí)間可在一個(gè)較寬的范圍內(nèi)調(diào)整其抗拉強(qiáng)度,從而滿足不同強(qiáng)度級(jí)別緊固件的需要。
本文用Ti-38644材料研制1240 MPa級(jí)鈦合金高鎖螺栓,對(duì)斷裂螺栓進(jìn)行觀察分析,通過力學(xué)性能檢測(cè)、顯微組織檢測(cè)、斷口形貌觀察、斷口組織和能譜分析等方法確定螺栓斷裂的性質(zhì)和原因,探討Ti-38644高鎖螺栓增壽機(jī)理并提出改進(jìn)措施。
1 實(shí)驗(yàn)方法
實(shí)驗(yàn)用?6mm的Ti-38644合金絲材的名義成分為Ti-3Al-8V-6Cr-4Mo-4Zr,相變點(diǎn)約730℃。退火態(tài)Ti-38644鈦合金絲材的微觀組織主要由β相基體構(gòu)成,在晶界處存在少量初生α相,如圖1所示。退火態(tài)Ti-38644鈦合金抗拉強(qiáng)度為1067 MPa,屈服強(qiáng)度約為995 MPa,延伸率為9.4%,斷面收縮率為47.3%。
圖1 退火態(tài)Ti-38644合金的光學(xué)照片和掃描電鏡照片
經(jīng)熱鐓鍛—熱處理—機(jī)加工—磨削---螺紋滾壓等工藝制備的輕型鈦合金高鎖螺栓,其結(jié)構(gòu)如圖2所示。在服役承載過程中螺栓頭下圓角產(chǎn)生應(yīng)力集中,在交變載荷作用下疲勞裂紋易在該位置萌生。為了抑制疲勞裂紋的形核提高螺栓疲勞壽命,將鈦合金螺栓在滾壓強(qiáng)化設(shè)備上進(jìn)行了頭下圓角部位擠壓強(qiáng)化處理,以提高螺栓頭桿結(jié)合處的抗疲勞強(qiáng)度。
圖2 1240 MPa級(jí)輕型鈦合金高鎖螺栓實(shí)物
制備的Ti-38644鈦合金高鎖螺栓性能達(dá)到Q/9S288-2013《1240 MPa級(jí)抗拉型平頭鈦合金高鎖螺栓》和Q/9S289-2013《1240 MPa級(jí)輕型鈦合金高鎖螺栓通用規(guī)范》的要求。疲勞試驗(yàn)依據(jù)GJB 715.30A-2003《緊固件拉伸試驗(yàn)方法疲勞》,利用QBG-100N0.2高頻疲勞試驗(yàn)機(jī)進(jìn)行高鎖螺栓疲勞試驗(yàn),疲勞高載=10.89 kN,低載為高載的10%,頻率=100 Hz。疲勞斷裂試樣保留斷口原貌,使用SUPRATM55型掃描電鏡進(jìn)行斷口分析和顯微組織觀察。將斷口觀察后的試樣沿對(duì)稱中徑面剖開,高度截取5 mm,制金相樣。依次經(jīng)過180目、500目、800目和1200目的碳化硅砂紙機(jī)械研磨,然后使用0.04 μm粒度的二氧化硅膠體溶液多次短時(shí)重復(fù)進(jìn)行拋光。將光潔的試樣表面浸入Kroll's腐蝕液中進(jìn)行侵蝕,約5 s后取出,進(jìn)行顯微組織檢查和EDS元素組成分析。
2 結(jié)果和分析
2.1 疲勞壽命
圖3a和b給出了失效后的Ti-38644合金高鎖螺栓,可見兩個(gè)螺栓均在頭下圓角處斷裂,并具有相似的宏觀損傷模式。疲勞實(shí)驗(yàn)結(jié)果表明,未經(jīng)頭下圓角強(qiáng)化后的高鎖螺栓承受51700次循環(huán)加載后即發(fā)生斷裂,而經(jīng)圓角強(qiáng)化后的高鎖螺栓疲勞壽命達(dá)到2783000次,其疲勞壽命提高幅度超過前者50倍。由此可以推斷,圓角擠壓強(qiáng)化工藝顯著提高了Ti-38644高鎖螺栓的疲勞壽命,但是擠壓強(qiáng)化工藝對(duì)高鎖螺栓疲勞失效位置沒有影響,高鎖螺栓頭下仍然是薄弱部位。
圖3 強(qiáng)化后的高鎖螺栓和未經(jīng)強(qiáng)化的高鎖螺栓的疲勞失效試樣
2.2 螺栓的顯微組織
圖4給出了Ti-38644高鎖螺栓的金相顯微結(jié)構(gòu),清晰地反應(yīng)了經(jīng)固溶+時(shí)效處理后的高鎖螺栓微觀組織中各物相的形貌及其分布。從圖4a可以看出,Ti-38644鈦合金高鎖螺栓的微觀組織由大量次生α相和β轉(zhuǎn)變基體組成,次生α相以兩種形態(tài)存在,即位于β晶粒的邊界處存在的晶界α相,其在晶界連續(xù)存在,使β晶界清晰。另一種則是處于晶內(nèi)縱橫交錯(cuò)的短片層狀次生α相。晶內(nèi)析出的次生α相具有較為固定的位相關(guān)系,不同取向的片層狀α相之間的夾角為60℃,并形成了網(wǎng)狀結(jié)構(gòu),如圖4b所示。彌散分布的晶內(nèi)次生α相和連續(xù)的晶界α相阻礙位錯(cuò)在晶內(nèi)和晶間的運(yùn)動(dòng),對(duì)Ti-38644鈦合金有強(qiáng)化作用。但是,很多研究顯示,相界和晶界作為金屬微觀組織中的薄弱位置,容易萌生裂紋。對(duì)于Ti-38644合金,雖然晶界α相和晶內(nèi)次生α相能阻礙位錯(cuò)的滑移從而提高鈦合金的強(qiáng)度,但是大量的界面也為裂紋的萌生創(chuàng)造了條件。裂紋一旦在界面處形成就沿界面擴(kuò)展,并彼此橋接形成常裂紋。此外,基體中的α相在循環(huán)加載的條件下與基體β相的變形協(xié)調(diào)性差,易在發(fā)生較大塑性變形時(shí)出現(xiàn)早期斷裂。這表明,Ti-38644合金中起彌散強(qiáng)化的α相雖然可提高材料的整體強(qiáng)度,但是也可能顯著影響疲勞裂紋的萌生。
圖4 Ti-38644高鎖螺栓的微觀組織和β轉(zhuǎn)變基體放大
2.3 疲勞斷口形貌
圖5給出了Ti-38644高強(qiáng)鈦合金高鎖螺栓拉伸疲勞斷口宏觀形貌。可見強(qiáng)化前后的高鎖螺栓斷口具有相似的特征,由于組織細(xì)小斷口的形貌比較平整。在頭下圓角部位分布有多處疲勞裂紋源。主裂紋源的區(qū)間范圍比較寬,裂紋擴(kuò)展較快。除主裂紋源外,沿頭下圓角周向分布有多處裂紋源,在多裂紋源的共同作用下裂紋迅速擴(kuò)展,致使頭部斷裂。對(duì)比圖5a和b可見,在圓角擠壓強(qiáng)化后的高鎖螺栓的斷口處保留了更多的殘余材料。兩個(gè)試樣的斷口具有相似的特征,均為線性疲勞源。疲勞斷口可分為裂紋萌生區(qū)、裂紋擴(kuò)展區(qū)和瞬斷區(qū)三個(gè)部分。斷口形貌SEM觀察結(jié)果表明,高鎖螺栓兩個(gè)試樣雖然疲勞壽命有明顯的差異,但是疲勞的源位置基本相同,即疲勞裂紋在頭下圓角表面發(fā)生形核。裂紋源從材料表面及次表面多處薄弱部位起裂,主裂紋源呈放射狀并向中央擴(kuò)展。在疲勞擴(kuò)展區(qū)有細(xì)小的放射棱線和清晰的疲勞條帶,失效方式以解理斷裂為主伴有少量韌窩,如圖5c和d所示。這個(gè)階段的裂紋尺寸擴(kuò)大到晶粒尺寸的數(shù)十倍,進(jìn)入宏觀裂紋擴(kuò)展階段。擴(kuò)展區(qū)斷面光滑、平整,可觀察到清晰的疲勞弧線和細(xì)密的疲勞條帶。擴(kuò)展區(qū)占面積較大,循環(huán)加載時(shí)位于該區(qū)的材料反復(fù)變形,裂開的兩個(gè)面不斷張開、閉合并相互摩擦直至進(jìn)入下一階段。瞬斷區(qū)具有明顯的韌性斷裂特征,是疲勞裂紋擴(kuò)展到臨界尺寸后失穩(wěn)擴(kuò)展形成的區(qū)域。雖然高鎖螺栓頭下圓角部位在螺栓的制造加工過程中進(jìn)行了冷擠壓強(qiáng)化[7,8],但是實(shí)際的工藝是通過三個(gè)滾輪的自轉(zhuǎn)和徑向進(jìn)給實(shí)現(xiàn)的。現(xiàn)有的加工設(shè)備很難避免擠壓不均勻或擠壓力不足的情況,致使頭下圓角應(yīng)力集中部位仍存在相對(duì)薄弱點(diǎn),為裂紋的萌生和擴(kuò)展提供了條件。
圖5 Ti-38644高鎖螺栓的拉伸疲勞斷口形貌
2.4 斷口表面層的組織和能譜分析
圖6給出了高鎖螺栓斷裂位置微觀組織SEM照片。可以看出,未經(jīng)頭下圓角強(qiáng)化的高鎖螺栓的微觀組織形態(tài)與固溶+時(shí)效后的Ti-38644鈦合金原始材料基本相同,如圖6a所示。而經(jīng)擠壓強(qiáng)化處理后的高鎖螺栓頭下圓角處的Ti-38644合金表層,在劇烈塑性變形作用下次生α相和β轉(zhuǎn)變基體形態(tài)呈明顯的纖維狀,兩者在SEM照片下較難分辨。如圖6b所示。沿表層向中心處觀察,滾壓工藝對(duì)微觀組織的影響逐漸降低,其內(nèi)部的次生α相與β轉(zhuǎn)變基體恢復(fù)至固溶+時(shí)效處理后的形態(tài)。由此可見,滾壓工藝產(chǎn)生的微觀組織轉(zhuǎn)變主要集中在表層區(qū)域,并形成一個(gè)厚度小于2 μm的變形層。其原因是,頭下表層材料在滾壓工裝提供的切應(yīng)力驅(qū)動(dòng)下發(fā)生塑性延伸造成的,且在滾壓過程中鈦合金與滾壓工裝接觸的部位產(chǎn)生的熱量使加工表面處于高溫。變形層就是在切應(yīng)力和高溫共同作用下形成的。結(jié)合疲勞測(cè)試結(jié)果可以推斷,由滾壓引入的表面變形層的厚度雖然較小(<2 μm),但對(duì)Ti-38644鈦合金高鎖螺栓壽命的影響十分顯著。
圖6 未經(jīng)擠壓強(qiáng)化高鎖螺栓和擠壓強(qiáng)化后的高鎖螺栓斷裂位置的微觀組織
高鎖螺栓強(qiáng)化層和基體能譜線掃描結(jié)果,如圖7所示。從圖7可見,表面變形層主要成份為Ti、Al、V、Mo、Cr、Si等元素,但其含量分布較為穩(wěn)定,所在位置的影響可以忽略。這表明,雖然表面變形層與合金基體的微觀組織形態(tài)的差異較大,但是元素組成基本相同。
圖7 強(qiáng)化后的高鎖螺栓的斷口表面層能譜分析
TEM觀察結(jié)果表明,晶粒內(nèi)的微觀組織有以下幾種形態(tài):(1) 在循環(huán)加載過程中,α/β晶界處形成的高密度位錯(cuò)纏結(jié)(圖8a)或“駐留滑移帶”。在交變載荷作用下駐留滑移帶形成“擠出”和“凹入”,進(jìn)一步產(chǎn)生應(yīng)力集中,高密度的位錯(cuò)使裂紋在滑移帶處萌生。(2) 較軟的次生α相提早發(fā)生塑性變形,在變形的累積作用下α相內(nèi)產(chǎn)生的大量位錯(cuò)塞積和層錯(cuò)(圖8b)造成應(yīng)力集中,最終導(dǎo)致α相破碎而形成微裂紋[9,10]。(3) α相發(fā)生孿生變形形成了孿晶(圖8c)。這種孿晶是鈦合金中α相的典型機(jī)械孿晶,孿晶與周圍組織變形不協(xié)調(diào)使孿晶界面開裂,是微裂紋萌生的原因之一[11]。(4) 晶界處是變形最薄弱的環(huán)節(jié),最早發(fā)生位錯(cuò)開動(dòng)。在晶界處產(chǎn)生大量平行排列的位錯(cuò)線[12] ,并向次生α相和β相內(nèi)滑移……兩者結(jié)構(gòu)和強(qiáng)度上的較大差異造成位于次生α相內(nèi)的位錯(cuò)線細(xì)小且密集,β相內(nèi)的位錯(cuò)線相對(duì)粗大且稀疏,少量位錯(cuò)線會(huì)在前端形成“Y”字形的分叉(圖8c和d)。層片狀的次生α相、晶界α相與β轉(zhuǎn)變基體的結(jié)構(gòu)和性能差別較大,使Ti-38644鈦合金的整體變形協(xié)調(diào)性差。晶界α相和次生α相是變形薄弱處,在承受交變載荷作用時(shí)晶界α相、次生α相和晶界處易堆積位錯(cuò)產(chǎn)生應(yīng)力集中,導(dǎo)致裂紋萌生。晶內(nèi)微裂紋沿相界面或較軟的α相擴(kuò)展長(zhǎng)大、橋接形成長(zhǎng)裂紋[13,14]。若微裂紋萌生于晶界處,則可沿較軟的晶界α和原始β晶界擴(kuò)展形成長(zhǎng)裂紋。由此說明,合金的顯微組織對(duì)高周疲勞裂紋萌生有顯著的影響。
圖8 疲勞試樣的微觀組織位錯(cuò)組態(tài)
2.5 增壽機(jī)理
疲勞斷裂實(shí)質(zhì)上是一個(gè)累積損傷過程,發(fā)生斷裂前經(jīng)歷了裂紋形成與擴(kuò)展兩個(gè)階段。構(gòu)件的疲勞壽命是裂紋形核壽命和擴(kuò)展壽命之和[15]。裂紋在表面的形核和擴(kuò)展主要受試樣表面形貌、微觀組織、材料性能及殘余應(yīng)力狀態(tài)四個(gè)因素的影響,而滾壓工藝對(duì)Ti-38644鈦合金高鎖螺栓的四個(gè)方面均有顯著的影響。
在滾壓過程中金屬表層金屬材料產(chǎn)生塑性流動(dòng),將表面不規(guī)則的凸出金屬填入波谷中,從而降低了表面粗糙度,如圖9所示。較為光滑的表面使高鎖螺栓在承受交變載荷時(shí)不易出現(xiàn)明顯的應(yīng)力集中區(qū)域,從而抑制裂紋在表面形核。觀察結(jié)果顯示,在由滾壓引入的塑形變形層內(nèi)晶粒組織嚴(yán)重變形,其內(nèi)部位錯(cuò)增殖、滑移、交割和纏結(jié),一部分在晶內(nèi)相互纏結(jié)形成位錯(cuò)塞積,另一部分排列成為亞晶界。這些亞結(jié)構(gòu)一方面以加工硬化的形式提高了Ti-38644鈦合金高鎖螺栓頭下區(qū)域的硬度,使其在循環(huán)加載時(shí)能夠降低交變載荷對(duì)材料的影響[16];另一方面,材料內(nèi)部的亞結(jié)構(gòu)使晶格發(fā)生畸變,并在周圍形成較大的應(yīng)力場(chǎng)。在交變載荷的作用下,滑移依然是金屬塑性變形的主要方式。在循環(huán)加載過程中,易滑移面上的位錯(cuò)首先開始滑移并隨循環(huán)次數(shù)的逐漸增加,當(dāng)其滑移至位錯(cuò)塞積和亞晶界附近時(shí)周圍的應(yīng)力場(chǎng)阻礙位錯(cuò)的繼續(xù)滑移或迫使的領(lǐng)先位錯(cuò)沿其它滑移面繼續(xù)滑移[17],降低了裂紋尖端開裂速度。后者分散了裂紋尖端能量,阻礙了裂紋的擴(kuò)展。此外,嚴(yán)重變形后的晶粒在徑向方向的單位長(zhǎng)度內(nèi)具有更多和更加曲折的晶界,也為裂紋的擴(kuò)展增加了難度,從而提高了高鎖螺栓的壽命。滾壓工藝不但使表層材料發(fā)生塑性變形而導(dǎo)致表面硬化,同時(shí)也在材料內(nèi)部引入殘余壓應(yīng)力,明顯改善材料的疲勞壽命。在材料中存在殘余壓應(yīng)力場(chǎng)時(shí),外加交變載荷中對(duì)裂紋張開起促進(jìn)作用的正平均應(yīng)力與殘余壓應(yīng)力相互抵消,使裂紋尖端應(yīng)力強(qiáng)度因子KI(張開型裂紋)下降,從而提高了裂紋擴(kuò)展門檻值,抑制裂紋源的形成。而已有的裂紋也將在殘余應(yīng)力較高的位置降低或停止擴(kuò)展,轉(zhuǎn)變成非擴(kuò)展裂紋,削弱裂紋群體效應(yīng)對(duì)裂紋擴(kuò)展的促進(jìn)作用。
圖9 Ti-38644鈦合金高鎖螺栓的疲勞強(qiáng)化機(jī)理示意圖
3 結(jié)論
(1) Ti-38644鈦合金高鎖螺栓的疲勞性能優(yōu)異,疲勞壽命達(dá)到2738000次,疲勞失效位置在頭下圓角處并沿周向分布,失效方式以解理斷裂為主伴有少量韌窩。
(2) Ti-38644鈦合金高鎖螺栓經(jīng)滾壓強(qiáng)化后在頭下表面形成強(qiáng)化層,其主要成分為Ti、Al、V、Mo、Cr、Si等,與基體一致。強(qiáng)化層的厚度約為1.5 μm,強(qiáng)化層內(nèi)的次生α相與β相劇烈變形,呈纖維狀排布。
(3) 在交變載荷作用下有強(qiáng)化層的Ti-38644鈦合金高鎖螺栓的疲勞壽命更高。滾壓強(qiáng)化工藝使高鎖螺栓表面的粗糙度更低,不利于疲勞裂紋在表面形核。同時(shí),引入的強(qiáng)化層因加工硬化和更加曲折的晶界阻礙了裂紋的擴(kuò)展。強(qiáng)化層中的殘余壓應(yīng)力降低了造成裂紋尖端應(yīng)力強(qiáng)度因子下降,使裂紋的擴(kuò)展減速甚至停止。
(4) 滾壓強(qiáng)化工藝對(duì)提高Ti-38644鈦合金高鎖螺栓疲勞性能的效果顯著。檢查強(qiáng)化后的表面強(qiáng)化層,可作為一種檢測(cè)方法和評(píng)價(jià)思路預(yù)估Ti-38644鈦合金緊固件的疲勞性能。
免責(zé)聲明:本網(wǎng)站所轉(zhuǎn)載的文字、圖片與視頻資料版權(quán)歸原創(chuàng)作者所有,如果涉及侵權(quán),請(qǐng)第一時(shí)間聯(lián)系本網(wǎng)刪除。
-
標(biāo)簽: 高強(qiáng)鈦合金高鎖螺栓, 疲勞裂紋, 解理斷裂
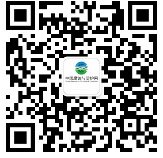
官方微信
《中國(guó)腐蝕與防護(hù)網(wǎng)電子期刊》征訂啟事
- 投稿聯(lián)系:編輯部
- 電話:010-62313558-806
- 郵箱:fsfhzy666@163.com
- 中國(guó)腐蝕與防護(hù)網(wǎng)官方QQ群:140808414