露點腐蝕是由于工業氣體在金屬表面溫度低于露點而凝聚所導致的腐蝕過程,在鍋爐和各種燃氣爐中,現場取樣、切管,觀察腐蝕產物后發現[1]:其橫截面呈明顯的分層結構,大致為3層:外層疏松、多孔,呈灰黑色,由大量灰顆粒和熔狀物質堆積而成;中間層為灰沉積層,分布大量黑點和高亮條帶狀物質;內層為腐蝕反應層,致密,呈白亮色。
國內外學者對燃煤電廠的露點腐蝕研究結果表明[2,3,4,5,6,7,8,9]:燃料中的S在燃燒后絕大部分生成SO2,其中有一部分在Fe2O3或V2O5 (煙氣或受熱面金屬表面中含有此成分) 的催化作用下轉化成SO3,SO3與水汽結合而在溫度低于硫酸露點的構件表面凝結成H2SO4,造成設備嚴重腐蝕。在省煤器、空氣預熱器、煙囪[10,11,12,13,14,15,16,17]等所有與含S氣體接觸的低溫設備中,都有可能發生硫酸露點腐蝕,將導致大量管道和煙道的更換,造成經濟上的巨大損失。
近年來,我國燃氣-蒸汽聯合循環發電技術 (以下簡稱燃機電站)[18,19,20,21,22,23,24]發展迅速,它具有效率高、安全可靠、單位千瓦造價低及低排放等特點,預計到2020年,我國燃氣-蒸汽聯合循環裝機容量將達到5.5×107 kW,是1951~2000年已建成的同類機組裝機容量的25倍;余熱鍋爐是燃機電站的重要組成部分,起著承上啟下的作用,其性能對發電效率影響甚大;目前全國各地余熱鍋爐事故頻發,表現為管壁減薄甚至爆管泄露,位置多發于低溫蒸發段,現場取管切割后顯示壁面為均勻腐蝕,腐蝕產物表征表明,S含量增加,推測管壁減薄的主要原因是硫腐蝕,即露點腐蝕。
對國內部分地區燃煤與燃氣進行元素分析的結果表明,燃機電站與燃煤電站中露點腐蝕有所差別:(1) 燃料中元素量的差別,燃煤比燃氣的S含量高,燃料中的硫分越多,則煙氣中所產生的SO3含量也就越高,SO3的存在使煙氣的露點顯著升高,影響電廠設置排煙溫度;(2) 灰分的差別,燃煤燃燒后排氣含有更多的粉塵 (含未燃燒碳等),粉塵對于露點有兩方面的影響,一是對SO2轉變為SO3有催化效果,二是對SO3具有物理吸附和化學吸附作用,粉塵中的堿性氧化物可以和SO3反應生成鹽,另外,含塵濃度高、吸附表面積大,也為SO3的凝結和吸附創造條件。
隨著清潔能源的發展,越來越多的燃氣-蒸汽聯合循環機組建成投產,由金屬腐蝕造成的受熱面金屬失效現象也越來越多,對燃機電站的露點腐蝕研究已經刻不容緩。
1 硫酸露點腐蝕模擬試驗的研究現狀
國外早在20世紀40年代就發現了低溫露點腐蝕,并進行了大量研究,主要研究方法有3種:酸浸泡實驗、實驗室模擬實驗以及現場腐蝕實驗。露點腐蝕的本質是材料在酸性液膜下的電化學腐蝕[5,9],與酸浸泡實驗的腐蝕機理顯然不同,導致酸浸泡實驗的結果遭受質疑。現場腐蝕試驗的機會比較少,如果沒有大量平行實驗作為基礎,將導致實驗結論出現偏差。因此,人們把精力轉向實驗室模擬實驗中,實驗的難度在于如何獲得模擬氣體。
文獻[25]公開了一種模擬硫酸露點腐蝕的實驗裝置及測試方法,該裝置模擬氣體產生特征在于把H2SO4溶液裝入蒸發瓶,啟動電加熱套對蒸發瓶加熱,電加熱套的控制溫度為60~200 ℃,在液體沸騰后產生腐蝕氣體,該發明認為所產生的腐蝕氣體為SO3,并以此模擬氣體來研究硫酸露點腐蝕。由文獻[17]可知,該發明的主要問題在于:稀H2SO4溶液在200 ℃以下沸騰蒸發所產生的主要氣體為水蒸氣,而腐蝕氣體SO3極少,如表1,因此,該項研究效率較低,需要耗費大量的人力和物力。
表1 硫酸的沸騰溫度-蒸汽相成分
文獻[26]公開了一種測試材料耐硫酸露點腐蝕的試驗裝置,該裝置模擬氣體產生特征在于通過分液器加入一定量濃H2SO4溶液進入試驗腔體底部,使其與NaHSO3溶液反應生成SO2氣體,隨后通過調節分液器控制硫酸溶液,持續產生SO2。該發明產生SO2作為腐蝕介質,而實際工況中是SO3與水蒸氣凝結成硫酸的腐蝕介質,顯然用SO2來模擬硫酸露點腐蝕是不準確的,專利文獻[27]也出現了類似的問題。
陳華等[28]設計了一種高溫露點實驗裝置,其中提到了從發煙硫酸中獲取SO3的方法;Thibault等[29]在研究鈣鎂氧化物對SO3的吸附性能時,也采用了往恒溫起泡器中加入發煙硫酸獲取SO3的方式。發煙硫酸是一種含有過量SO3的硫酸,化學式:H2SO4·xSO3,無色至淺棕色粘稠發煙液體,其密度、熔點、沸點因SO3含量不同而異,當它暴露于空氣中時,揮發出來的SO3與空氣中的水蒸氣形成硫酸的細小霧滴,所以稱為發煙硫酸。大量證據顯示可以通過發煙硫酸的揮發制取模擬氣體,但因為發煙硫酸是一種危險物品,氣密性要求高,此外生成的SO3量難以控制,所以實際運用難度很大。
趙瀚辰等[30]設計并搭建了小型低溫煙氣冷凝試驗臺,其中一部分功能是實現SO3的制取,SO3制取系統特征在于將SO2與O2氣體通入550 ℃的電加熱爐中,以鉑金屬絲作為催化劑反應生成SO3,SO3轉化率可保持在40%。該發明不足之處在于實驗設備價格昂貴,氣密性要求高,高溫危險,不適合裝配在一般的實驗室里。
趙欽新等[31]搭建了一套實驗系統,各種氣體經過質量流量計后在混合器內混合,在高溫管式爐中被加熱后腐蝕金屬試樣,其中O2、N2、CO2以及SO2均采用標準氣體配置,而SO3和水蒸氣是根據稀溶液成分等于其飽和蒸汽成分的原理,采用稀H2SO4溶液在一定溫度下蒸發,通過N2為載氣帶出得到的,根據實際煙氣中的比例,配置質量分數為0.856%的稀硫酸溶液,設置電熱恒溫箱的溫度為58.6 ℃。實際上稀硫酸溶液的蒸發得到SO3的量極少,即使在N2為載氣的帶動下,硫酸蒸汽的產量依舊很少,不符合實驗預期效果,如表2所示,而且在如此低的溫度下,實驗難度更加巨大。
表2 硫酸溶液蒸汽中的H2SO4含量 (mass fraction / %)
閆君等[32]對SO3酸霧發生方法進行了探討。選用超聲波霧化器作為SO3酸霧的發生方法,并輔助以高壓射流噴霧器作為比較,制取特征在于:可以通過控制調節所使用的稀硫酸濃度來控制混入煙氣中有效的SO3。硫酸露點腐蝕[33]是分階段性的,腐蝕過程是一個變溫變濃度的復雜的大氣腐蝕過程。這種通過霧化的方式得到的酸霧粒徑不均勻,并且酸霧表征的是小液滴的腐蝕,最終將導致實驗結果與現場真實的氣體腐蝕情況相違背,應用于硫酸露點腐蝕的機理研究將會導致結論出現偏差。
根據電廠實測數據,不同類型的電廠酸露點溫度不同,普遍在100 ℃左右[19]。文獻[34,35,36]表明:當溫度低于200 ℃時,煙氣中的SO3明顯地轉變成硫酸蒸汽,而且溫度越低轉化率越大。當溫度低于110 ℃時,SO3轉變為硫酸蒸汽的轉化率接近100%,如圖1所示。本文通過對硫酸蒸發特性進行系統研究,利用濃硫酸蒸發氣體作為模擬氣體,從而提供一種硫酸露點腐蝕模擬氣體產生方法。
圖1 SO3轉變為H2SO4蒸汽的轉化率與溫度的關系
2 實驗方法
主要試劑為濃硫酸 (AR),硫酸鈉 (AR),氯化鈉 (AR)、碳酸鈉 (AR)、碳酸氫鈉 (AR),實驗用水為高純水 (電阻率為18.25 MΩ·cm)。
圖2為模擬氣體產生裝置示意圖,工作流程:把濃硫酸裝入特制蒸發瓶,打開油浴鍋對蒸發瓶進行加熱,濃硫酸在高溫下蒸發,但由于其在這種蒸發情況下產生的硫酸蒸汽量少,所以設置通入N2為載氣,N2將蒸發出來的硫酸蒸汽帶出,在穩定的N2流速下,硫酸蒸汽的產生保持穩定和持續,保證了后續硫酸露點腐蝕模擬氣體的用量,考慮到硫酸蒸汽遇冷極易凝結,所以設置輸送玻璃管道外壁包覆絕熱層,并嚴格控制玻璃輸送管路的長度,降低硫酸蒸汽在輸送過程中因凝結所產生的損失。
圖2 模擬氣體產生裝置示意圖
在包覆絕熱層的玻璃導管后設置吸收瓶,吸收瓶內裝有250 mL的高純水,取出部分吸收液用883 Basic IC plus型離子色譜儀 (配Metrosep A Supp 4-250/4.0陰離子交換分析柱) 檢測后,吸收液的電導率數值可以間接反映瓶內單一陰離子濃度,并做不同濃度硫酸溶液對應的電導率曲線,通過比對,研究硫酸溶液的蒸發特性。
3 結果與討論
3.1 結果分析
3.1.1 離子色譜的測定結果
圖3為高純水和蒸發實驗后吸收液的離子色譜圖,通過混標繪制標準曲線,得出常規陰離子的定性方法,平行實驗結果表明:吸收液里僅存的特征陰離子是硫酸根離子,從而證明高濃度硫酸在通入載氣的情況下,可以得到硫酸蒸汽。
圖3 高純水和蒸發實驗后吸收液的離子色譜圖
3.1.2 不同濃度硫酸溶液的電導率結果
通過離子色譜結果得知,吸收液的特征陰離子是硫酸根,實驗可以通過電導率的變化來表征吸收液單一陰離子的離子濃度,從而表征硫酸的蒸發效果,如表3所示,電導率-濃度對應曲線離子濃度的檢測范圍:10-6~10-2 mol/L。
表3 不同濃度硫酸溶液對應的電導率數據
3.2 影響因素分析
3.2.1 體積的影響
實驗采用質量濃度為98.3%的濃硫酸溶液,并通入流速為200 mL/min的N2,蒸發瓶體積為250 mL,溫度為140 ℃。由圖4可知,當硫酸溶液體積為5~30 mL時,硫酸蒸汽的蒸發效果隨著濃硫酸用量增加而增加,當硫酸溶液體積為30~40 mL時,蒸發效果的增加已經不明顯了,即當硫酸溶液的體積與容器體積比為325以上時,再加溶液,蒸發效果變化不大,考慮到硫酸蒸發實驗的危險性,建議溶液的體積與容器體積比在225~325。
圖4 不同體積硫酸溶液,吸收液的電導率數據
3.2.2 濃度的影響
實驗采用體積為20 mL的硫酸溶液,硫酸的濃度梯度為0.1,1,10和18.4 mol/L,并通入流速為200 mL/min的氮氣,蒸發瓶體積為250 mL,溫度為140 ℃。由圖5可知,低濃度硫酸的蒸發難以獲取硫酸蒸汽,實際蒸發的氣體大多為水蒸氣。由參考文獻[17]可知:蒸發質量分數低于85%的液體,取得的主要成分為水蒸氣,在85%~100%的質量濃度硫酸溶液,得到的是水蒸氣與硫酸蒸汽的混合物,與本文的實驗結果相一致。
圖5 不同濃度硫酸溶液下吸收液的電導率數據
3.2.3 溫度的影響
實驗采用體積為20 mL的硫酸溶液,質量濃度為98.3%,在N2流速為0、200和300 mL/min時,分別設置實驗溫度為140、160和180 ℃,蒸發瓶體積為250 mL。由圖6可知:隨著溫度的升高,產生硫酸蒸汽的量增大,這是因為溫度升高加快了液體表面的劇烈相變反應,促進了硫酸從液相到氣相的轉變,以此提高了硫酸蒸汽產生效率,由圖6c可知:在該流速下,溫度的改變對實驗效果的影響不大,這是因為相變反應在此時的環境中 (溶液的體積、壓力等條件下) 已經達到極限,載氣帶動硫酸蒸汽流出的過程已然成為此時的主要影響因素。
圖6 不同流速時吸收液的電導率數據
3.2.4 流速的影響
實驗采用體積為20 mL的硫酸溶液,質量濃度為98.3%,在140、160和180 ℃時,分別通入流速為0、200和300 mL/min的氮氣,蒸發瓶體積為250 mL。由圖7可知高濃度硫酸溶液在不通載氣的情況下,難以獲取穩定、持續流動的硫酸蒸汽,在通入載氣后,隨著流速的加快,產生硫酸蒸汽的量越多,這是因為高流速載氣加快帶動硫酸蒸汽的流出,推動了蒸發反應由液相向氣相的轉變,以此提高硫酸蒸汽產生效率,建議可以根據實驗需要,改變發生裝置玻璃管路口徑的大小,來設置合適的流速獲取模擬氣體。
圖7 不同溫度下吸收液的電導率數據
4 硫酸露點腐蝕驗證實驗
以燃機電站余熱鍋爐硫酸露點腐蝕為例,收集了國內某兩個燃機電站現場監測數據,獲得的排氣成分數據列于下表4。
表4 燃機電站排氣成分表 (volume fraction / %)
硫酸露點腐蝕驗證實驗主要研究在H2O、N2和H2SO4蒸汽的氣體環境下,ND鋼和20G鋼的抗腐蝕性能。通過質量流量計控制氣體的流速,混合后通過含有目標材質的試驗箱,并通過失重法和XRD進行評價。表4中的數據顯示實際環境中氮氣和水蒸氣體積比約為73∶9,因此設置混合氣體對應的流速 (mL·min-1) 為VN2+H2SO4∶VH2O=200∶25,以12和24 h為時間梯度,并控制模擬氣體產生裝置的溫度為160 ℃,試驗箱溫度為室溫。
如圖8所示,結果表明ND鋼的耐硫酸露點腐蝕性能明顯強于20G鋼,另外,隨著時間的增長,兩種鋼片的腐蝕速率都出現了一定程度的降低。圖9為試片表面的XRD圖譜,分析結果表明:試片表面形成了FeSO4·5H2O等晶體,這些晶體易吸附在試片表面,會一定程度減緩了硫酸溶液的侵蝕過程,進而影響試片的腐蝕速率,實驗結果與張知翔等[11]一致。
圖8 ND和20G鋼的腐蝕速率
圖9 試片表面的XRD譜
5 結論
比對了國內外硫酸露點腐蝕模擬氣體的產生方法,分析其產生特征和不足。通過對硫酸蒸發特性進行研究,探討出一種硫酸露點腐蝕模擬氣體產生的新方法,結果表明:
(1) 硫酸溶液的體積和濃度對硫酸蒸汽的產生效果有影響,其中溶液的體積與容器體積比在225~325最佳,低濃度硫酸蒸發得到的主要氣體為水蒸氣,高濃度硫酸蒸發才能得到硫酸蒸汽,其中硫酸蒸發效果最佳的質量濃度為98.3%。
(2) 加熱溫度對硫酸蒸汽的產生效果有影響:溫度越高,相變反應越劇烈,硫酸蒸汽產生的效率越高。
(3) N2的流速對硫酸蒸汽的產生效果有影響:不通載氣不能獲取流動的硫酸蒸汽,N2的流速越快,帶動了硫酸蒸汽的流出,加快了硫酸溶液的蒸發速率。在高濃度硫酸+載氣 (N2) 的情況下,才能獲取穩定、持續流動的硫酸蒸汽,這種模擬氣體產生的新方法有助于硫酸露點腐蝕的研究。
(4) 以實際燃機電站余熱鍋爐排氣成分為例,驗證了載流法用于硫酸露點腐蝕的研究是可行的。
免責聲明:本網站所轉載的文字、圖片與視頻資料版權歸原創作者所有,如果涉及侵權,請第一時間聯系本網刪除。
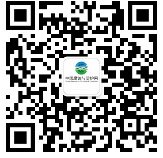
官方微信
《中國腐蝕與防護網電子期刊》征訂啟事
- 投稿聯系:編輯部
- 電話:010-62316606-806
- 郵箱:fsfhzy666@163.com
- 中國腐蝕與防護網官方QQ群:140808414