0 引言
鋼鐵材料力學性能的提高對降低資源、能源消耗大有裨益,一直都是研究的重點。目前國內大量生產和應用的結構鋼強度一般在400~800MPa,如能在保持塑性的同時將鋼的強度級別提高一倍,則實際生產中鋼材用量可大為減少,從而達到輕量化的目的[1-2]。特別是對汽車而言,高強度鋼材的運用可有效降低整車質量從而降低油耗和排放。研究表明,汽車質量每下降10%,油耗下降6%~8%,排放下降4%~6%[3],因此汽車輕量化也一直是新型鋼鐵材料不斷問世的推手之一。得益于相變理論的發展,自20世紀70年代以來,以固態相變作為強化和增塑機制的各類新型高強度鋼不斷問世,并逐漸取代部分傳統高強度低合金(HSLA)鋼在汽車工業中的應用。該類新型高強度鋼的顯微組織通常為兩相或兩相以上組織,如馬氏體、貝氏體、鐵素體、奧氏體等,形成復合組織,分別用來增強和提塑,由此使材料兼具高強度與高塑性的特性。雙相(DP)鋼、相變誘發塑性(TRIP)鋼、孿生誘發塑性(TWIP)鋼、淬火-配分(Q&P)鋼、淬火-配分-回火(Q-P-T)鋼以及貝氏體鋼等新型高強度鋼,主要添加硅和錳等價格低廉的合金元素,側重于利用這些合金元素改變相變規律,以優化顯微組織獲得優異的力學性能[4]。如中碳Q-P-T鋼在抗拉強度達到1500MPa時,其伸長率仍可維持在20%左右[5],顯示出良好的強塑性配合。
然而,鋼鐵材料在冶煉、酸洗、電鍍、焊接過程中以及隨后的服役時均存在氫滲入的幾率,從而導致先進高強度鋼存在發生氫脆的風險;再加上服役時應力梯度作用下氫易向高應力區(如相界等)富集,顯著增加了承載零部件(如螺栓、懸架彈簧等)或承載鋼結構(如壓力容器、建筑結構等)發生氫脆的可能性。關于鋼鐵中的氫脆,早在1875年,Johnson[6]就第一次證實氫會導致材料力學性能的顯著惡化,并產生無預警的脆斷。自此以后,氫對鋼鐵材料壽命的影響開始受到重視,并總結出氫脆存在如下幾個顯著特征:(1)惡化力學性能,特別是會顯著降低
伸長率和斷面收縮率;(2)改變斷裂機制,形成不同的斷口形貌,主要表現為隨材料中氫濃度的提高,斷裂模式由延性韌窩斷裂向脆性解理或沿晶斷裂轉變;(3)斷裂發生突然,無明顯征兆,因而往往引起嚴重后果。
鑒于以上原因,防止高強度鋼鐵材料的氫致脆性斷裂一直是材料科學領域研究的重點。對傳統鋼鐵材料的研究發現,氫脆主要取決于氫在金屬中的狀態。氫在金屬中的運動包括氫的吸附、擴散、富集等,并與顯微組織形成交互作用,以形成氫壓、弱化金屬原子鍵合力、降低表面能或促進局部塑性變形等方式促使材料提前失效,發生脆性斷裂[7],主要表現為力學性能的顯著下降。這些導致力學性能變化的氫常富集在陷阱中。金屬中氫陷阱種類的多樣性及與氫交互作用的多變性導致了金屬氫脆機理的復雜性。目前已知,氫脆敏感性隨鋼鐵材料強度的提高急劇增加,特別是當抗拉強度超過1000MPa[8]后,氫脆幾乎是不可避免的破壞性因素;此外,氫脆又具有組織敏感性的特征,尤其是作為強化相的馬氏體等非平衡組織引發氫脆的概率遠遠高于鐵素體等平衡組織。由于這些非平衡相往往是構成先進高強度鋼(AHSS)的基體組織,且AHSS的強度也很高,因此其氫脆問題同樣不容忽視。但是,由于AHSS出現的時間較晚,特別是某些類別的AHSS(如Q&P和Q-P-T等鋼種)問世才10a左右的時間,其氫脆機理雖受到一定關注,但還未得到深入研究,因此以下作者謹就AHSS的氫脆研究現狀作初步的綜述,供相關人員參考。
1雙相(DP)鋼的氫脆
DP鋼是20世紀70年代應汽車行業輕量化的急迫需求而開發出來的第一種先進高強度鋼,其顯微組織是在等軸(或條狀)鐵素體基體中分布有島狀馬氏體的雙相組織,具有低屈服強度、低屈強比、高均勻伸長率、高初始加工硬化速率和優良的疲勞極限等優點,因此DP鋼兼具高強度和良好的成型性及焊接性,廣泛應用于汽車加強板、連軸器加強體、輪盤、保險杠和懸掛系統等零部件。非沖壓成型DP鋼在建筑鋼筋、鋼絲繩等方面也取得了明顯的經濟效益。
更多內容請閱讀原文: 先進高強度鋼氫脆的研究進展.pdf
免責聲明:本網站所轉載的文字、圖片與視頻資料版權歸原創作者所有,如果涉及侵權,請第一時間聯系本網刪除。
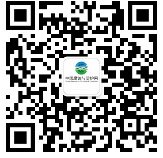
官方微信
《中國腐蝕與防護網電子期刊》征訂啟事
- 投稿聯系:編輯部
- 電話:010-62316606-806
- 郵箱:fsfhzy666@163.com
- 中國腐蝕與防護網官方QQ群:140808414