內容提要:介紹了5×104m3外浮頂原油罐在長期使用過程中內外壁金屬表面存在的腐蝕現象,對腐蝕原因進行了分析。對原油罐內外壁防腐涂層的材料進行了篩選,確定原油罐內壁采用成膜物為環氧系的防腐涂料,外壁采用環氧改性的氯磺化聚乙烯橡膠為成膜物的防腐涂料。收到了較好的效果。其中,重點對防腐涂裝的施工工藝及技術要求、施工過程進行了介紹。
關 鍵 詞:外浮頂原油罐;內外腐蝕;防腐涂料;防腐;施工
1、使用情況:
某廠50000m3外浮頂儲罐,規格為φ60.20×19.40米。浮盤形式為單盤式,即周邊有32個浮倉,中間一個浮倉,其浮盤為5mm鋼板,東西兩邊各一個積水槽,槽內有個DN150的排雨水單向閥,自96年11月份投用以來儲存過混渣(催化油漿、焦化甩油、抽出油、污油)、原油、渣油,儲存的油品組分復雜對罐底有一定的腐蝕;由于生產原因,儲罐無法倒出,長期運行,從未刷過罐。
由于該罐無法倒出近15年以來從沒有進行防腐維修,從罐的外觀檢查,曝露在大氣中的金屬表面防腐層已經粉化,部分漆膜脫落失去防腐作用。油罐內壁金屬表面浮盤下表面、罐底、罐底第一圈板,通過開罐檢查發現這些金屬表面存在大量的點蝕坑,有的腐蝕坑可以達到1~3毫米。
2、原油貯罐的內、外腐蝕特點
2.1罐內壁腐蝕
2.1.1罐底內腐蝕。沉積水中氯離子、溶解氧、硫酸鹽還原菌引起的腐蝕。沉積物中鹽類和有機淤泥,其粘性抑制氧的擴散。形成氧濃差電池產生的腐蝕,腐蝕速度一般為0.2~0.8mm/a。有沉積水的高鹽分污水引起電化學腐蝕、細菌腐蝕和垢下腐蝕,其腐蝕特征是斑點和坑蝕,腐蝕速度一般為0.4~0.8mm/a,最大可達2mm。
2.1.2浮盤下表面腐蝕。一是,由于氣溫的變化,水蒸氣易在罐頂內壁形成凝結水膜,罐內的二氧化硫、硫化氫、二氧化碳、揮發酸等雜質會溶解在凝結水中,形成含有多種腐蝕成分的電解溶液。二是,由于罐的呼吸作用,氧氣不斷進入罐內并很容易通過凝結后的薄層液膜擴散到金屬表面,從而發生主導性耗氧腐蝕。
2.2 罐外壁腐蝕
2.2.1防腐涂層的損壞[1]
當被保護的金屬表面,涂覆油性漆、醇酸漆等,因為環境中空氣中含有二氧化硫和二氧化碳等與潮濕的空氣中水作用,生成稀硫酸和碳酸,附著在防腐涂層表面。由于涂層的透氣性,它能自發地沿著涂層與金屬界面間擴展,而破壞涂層與金屬表面的附著力。在太陽光的照射下,致使以油料成膜物質涂層皂化,使涂層變軟、變脆而喪失原有的物理機械性能,導致涂層破壞。
2.2.2金屬表面腐蝕
在潮濕時,腐蝕速度常受到氧的補給速度所控制。由于電解液膜層的存在,在金屬表面的缺陷處發生電化學腐蝕,導致金屬表面出現麻坑和大量的銹蝕產物[2],氧在金屬表面上同金屬接觸,富氧區為陰極,貧氧區為陽極受到腐蝕。當涂料受到破壞時,金屬表面易受到腐蝕,產生銹瘤,形成一個類似半球形的蓋罩,使蓋罩下面的金屬缺氧面繼續受到腐蝕。因供氧程度的不同,銹瘤表層是紅褐色的高價鐵氧化物,內層是黑色的磁性氧化鐵或灰綠色的亞鐵和高鐵氧化物體的混合物。當金屬表面存在銹蝕層時,它就起了水和氧的儲槽作用,在一定的條件下腐蝕產物會影響大氣腐蝕的電極反應。Evans認為大氣腐蝕的銹蝕層處在濕潤的條件下,可以作為強烈的氧化劑。
所以說,金屬表面一旦形成銹蝕層,在氣體干濕交替的變化下,金屬表面的腐蝕將進一步加劇。根據原油罐的腐蝕情況,首先要選擇合適的防腐涂料和涂裝方法,進行防腐施工,獲得一個較好的防腐涂層,用來提高原油罐的使用壽命。
3、防腐設計原則
3.1內防腐涂層設計原則
要求防腐涂層,① 耐油性好、對油品無污染;有良好導電性、耐腐蝕性和耐熱性;韌性、附著力、抗沖擊、耐磨性好;② 選用環氧系抗靜電涂料;③ 防腐層為五層,干膜厚度≥220μm;④ 設計壽命不低于15年。另外,在設計時為排除原油貯存時油罐積累的靜電荷,原油儲罐內防腐層必須有良好導電性。因為進出油流摩擦形成靜電,在防腐層完整的情況下,如果使用非導靜電涂層,容易引起火災。根據油罐的腐蝕情況及考慮國家標準《液體石油產品靜電安全規定》BG13348-92規定,漆膜表面電阻率(Ω) ρs∠109、漆膜體積電阻率(Ω·m)ρv∠108。
3.2外防腐涂層設計原則
① 材料強度、硬度、附著力要好,具有優良的保光性抗老化性;② 選用高耐候防腐專用涂料;③ 防腐層為五層,干膜厚度≥180μm;④ 設計壽命不低于10年
4、儲罐防腐部位設計與材料選擇
4.1罐內壁材料選擇
通過現場的實際考察,結合儲油罐上的腐蝕與防護的管理經驗,認為該罐的腐蝕已經到了嚴重的腐蝕階段,也是金屬表面惡性循環腐蝕階段。所以應采取必要的防護措施,用來延長其設備的使用壽命。設計依據如下:
4.1.1罐內壁防腐部位:該腐蝕部位是在罐底與浮盤下表面和浮盤處于儲罐檢修狀態下的罐內壁的表面積。這些部位經常與油品與油氣接觸金屬表面腐蝕較厲害。
4.1.2罐內壁防腐材料的選擇依據
在多種涂料中篩選了“環氧型防腐防靜電鱗片涂料”該涂料由底漆與面漆配套組成。其中漆膜表面電阻率(Ω) ρs1.6×106、漆膜體積電阻率(Ω·m)ρv6.2×105,遠遠小于國家標準。
根據金屬表面腐蝕的情況采取環氧富鋅底漆兩道,(干膜厚度約70μm),環氧玻璃鱗片防靜電涂料面漆三道(干膜厚度150μm以上)。采用兩道底漆是因為所施工的是舊的油罐,金屬表面已經出現大量的蝕坑,大的有黃豆粒大,小的有小米粒大小,遍布金屬表面。另外,金屬表面處理的粗糙度40μm。如采用一道底漆只能獲得35μm厚度漆膜,有一部分金屬還沒有遮蓋住。這種條件情況下的金屬表面只能用兩道底漆用來解決覆蓋金屬表面的問題。如果金屬表面底漆覆蓋不住,這樣獲得不了金屬與防護涂層的最佳附著力。
采用環氧富鋅底漆做底漆與環氧玻璃鱗片防靜電涂料做面漆進行搭配。用在油罐內壁防腐是目前我國防腐方案中比較認可的方案。底漆主要是有機(環氧)富鋅漆,在防腐上有電化學保護作用。面漆主要成膜物質為環氧樹脂,它有良好的耐腐蝕性能。另外,在涂料中壁加入了玻璃鱗片,增加了抗腐蝕介質滲透的能力,這是傳統涂料無法比的【3】。
這一點在我廠4座10000立方米外浮頂汽油罐內壁實際使用已有15年漆膜不脫落、涂層效果很好,已經證明了這一點。
4.2儲罐外壁材料選擇
4.2.1罐外壁防腐部位
根據現場的實際調查,該罐的浮艙上表面、浮艙內表面、儲罐附件(與大氣接觸)、第七、八層圈板(不與介質接觸的部分)。防腐涂層已經脫落、起層、粉化起不到防腐蝕作用應該重新進行防腐蝕涂裝。
4.2.2罐外壁防腐材料的選擇
根據金屬表面重腐蝕的情況采取“高耐候外防腐專用涂料”底漆兩道,(干膜厚度約70μm),“高耐候外防腐專用涂料”面漆三道(干膜厚度120μm以上)。
⑴ 選擇依據 原采用的涂料從分子結構看,透氣、透水性強。從耐蝕性看,常規的油性材料耐老化不好、不耐酸堿及溶劑的侵蝕。雖然說,采用氯磺化聚乙烯涂料(以下簡稱氯磺化)能解決耐老化性等一些問題,但是涂料的強度、附著力、裝飾性等沒有很好的解決。
為了解決這些問題,近幾年來采用“高耐候外防腐專用涂料”,是一種較好的涂料。因為材料的保光性、抗老化性,特別是耐蝕性優于一般的氯磺化。因該材料在耐水、耐熱、耐化學品、單組分儲存穩定性、交聯速度、色穩定性、著色能力、耐污染、清漆成膜透明、涂料生產中易分散十個方面,與其它交聯體系的涂料相比,顯示了明顯的優越性,是國外公認十項技術性總積分最高的交聯劑型氯磺化性聚乙烯涂料。
⑵效果 1995年以來我廠在部分裝置的設備、金屬結結構等進行了防腐,累計35萬平方米。比原有的防腐涂料提高使用壽命2倍以上。所以說,該材料在化工系統的設備等方面使用,綜合效益是很好的【4】。
5、技術方案與技術要求
5.1技術方案
根據現場的實際情況設計了如下施工方案:內防腐施工工藝一覽表見表1;外防腐施工工藝一覽表見表2。
表1內防腐施工工藝一覽表
防腐部位 面積m2 涂層施工工藝 備注
罐底及第一層圈板 3300 環氧富鋅底漆兩道,干膜厚度70μm
油罐環氧玻璃鱗片防靜電涂料面漆三道,干膜厚度150μm
浮艙下表面 2845 環氧富鋅底漆兩道,干膜厚度70μm
環氧玻璃鱗片防靜電涂料面漆三道,干膜厚度150μm
儲罐附件(與原油接觸) 100 環氧富鋅底漆兩道,干膜厚度70μm
環氧玻璃鱗片防靜電涂料面漆三道,干膜厚度150μm
合計 6245
表2外防腐施工工藝一覽表
防腐部位 面積m2 涂層施工工藝 備注
第七、八層圈板 910高耐候涂料底漆兩道,干膜厚度70μm 不與介質接觸的部分。
高耐候涂料面漆三道,干膜厚度120μm
浮艙上表面 2845高耐候涂料底漆兩道,干膜厚度70μm
高耐候涂料面漆三道,干膜厚度120μm
浮艙內表面 500 高耐候涂料底漆兩道,干膜厚度70μm
高耐候涂料面漆三道,干膜厚度120μm
儲罐附件(與大氣接觸) 2000 高耐候涂料底漆兩道,干膜厚度70μm
高耐候涂料面漆三道,干膜厚度120μm
合計 6255
5.2 技術要求
5.2.1內壁
5.2.1.1底面處理:對于罐內壁進行機械噴砂處理。處理后的金屬表面達到 國家標準《涂裝前鋼材表面銹蝕等級和除銹等級》GB8923-88中Sa2.5 級。因為本次施工為舊罐,金屬表面附有大量的原油及銹蝕產物,采用一次噴砂達不到Sa2.5級,所以首先在清楚污油的情況下,然后采用河砂進行噴涂,去處金屬表面污油,特別是金屬表面凹坑的污油也可以除去。另外,在保證金屬表面達到要求的前提下,可以節約石英砂的成本。
5.2.1.2涂刷兩道底漆:底層涂料應在噴砂和清掃后進行。然后涂刷兩道導靜電防腐涂料,每道漆固化不小于24小時。
5.2.1.3中間漆一道:當底漆固化20小時后,涂刷導靜電防腐涂料。每道漆固化不小于24小時。
5.2.1.4面漆兩道:中間漆固化小于24小時后,涂刷兩道導靜電防腐涂料面漆,每道漆的固化時間為24小時。
以上5道漆膜的總厚度達到220μm以上。
5.2.2外壁
5.2.2.1底面處理:同內壁防腐底面處理相同,達到BG8923-88中Sa2.5級。
5.2.2.2底漆兩道:底面處理完后檢查合格,高耐候外防腐專用底漆二道。每道漆固化時間為12小時。
5.2.2.3中間漆一道:底漆固化12小時后,高耐候外防腐專用中間漆一道,要求顏色為淺灰色。
5.2.2.4面漆兩道:中間漆固化12小時后,高耐候外防腐專用面漆兩道,其中顏色要符合《石油化工設備罐道鋼結構表面色和標志規定》SH3043-2003規定。其中,梁、柱、支承、鋪板、踏板為藍灰色。欄桿、護攔、扶手為淡黃色,罐體為銀色。
5.3驗收
5.3.1該工程驗收包括中間驗收與竣工驗收。
5.3.2中間驗收是防腐工程開始后,每一道不同工序完成后所進行的驗收,即施工單位與使用單位對工程質量按化工部《化工設備、管道防腐蝕工程及驗收規范》HGJ229-91有關章節執行。
5.3.3竣工驗收做到:防腐涂層“涂層光滑平整,顏色一致、無氣泡、剝落、漏刷、返銹、透底和起皺等缺陷。”內、外壁防腐涂層厚度分別為≥220μm和≥180μm。
5.3.4施工單位根據通過公司審批后的施工工藝及技術要求編制施工方案,須經乙方審批并經甲方認可后方可實施。
6、施工
6.1施工前準備
6.1.1 根據現場情況,以準確、實際、安全、方便施工、保證質量、節省人力、物力、財力為原則編制實施方案。
6.1.2 編制施工機具、檢測儀器、計量儀器計劃,提出施工用料和施工手段用料計劃。
6.1.3 制定工時計劃,建立施工組織,制定全員培訓計劃。
6.1.4 規劃、繪制施工總平面圖,要含有施工、生活臨時設施、堆場、倉庫、工作間、機械設置、消防道路、用水用電。
6.1.5 搭設施工用臨時設施,保證垂直和水平運輸,人行通道,施工用料堆場。加工平臺,操作面腳手架搭設。
6.1.6 準備施工用的標準樣板,征得甲方的同意和甲方確定質量控制點,便于開展質量檢查工作,提出開工報告。
6.1.7材料準備
6.1.7.1石英砂:要求質堅、有棱角,無雜質,含水<1% ,超過1%時需進行烘干后方能使用。中號河沙:質堅、棱角較小,無雜質,含水<1% ,超過1%時需進行烘干后方能使用。
6.1.7.2防腐涂料:對檢驗合格的材料,合理存放,做好防雨、防火。
6.1.8機具準備
6.1.8.1空氣壓縮機、噴砂機四套,備用兩套;涂層測厚儀、溫度計各一個;高壓膠帶、噴槍嘴、勞保用品等各種配套物資按計劃用量備齊。
6.1.8.2把施工中所用的各種設備、機具提前進入施工現場,認真檢查,確保無誤;接通電源,調試完畢后待用。
6.2防腐施工
6.2.1施工工藝為:
機械噴河砂清油――清砂除塵――機械噴石英砂除銹――清砂除塵――涂刷防腐涂料。本次施工分為儲罐內外壁施工。
6.2.2儲罐金屬表面處理要求
質量標準控制:本次施工對于金屬表面需要涂裝防腐涂料的要達到GB8923-88Sa2.5級標準,即:鋼材表面應無可見的油脂、污垢、氧化皮、鐵銹和油漆涂層附著物,表面應顯示均勻的金屬光澤,并用吸塵器、干燥潔凈的壓縮空氣或刷子清除粉塵。表面無任何殘留物,同時表面有40μm 左右的粗糙度。根據表面粗糙度選用粒度應在0.4~3mm。為了節約成本噴砂作業時,先用河砂噴一遍然后用石英砂噴涂并控制表面粗糙度在40μm±10μm。
6.2.3機械噴砂施工
6.2.3.1操作準備要求
①應盡可能縮短風源與工作面。整個系統不應有漏氣部位存在,應盡量減少系統內接頭的數目,以利于減少漏氣、減低壓力降。
②準備標準長度的噴砂軟管,根據噴砂機與工作面的距離,選用合適長度的管子,以減少無用長度帶來的壓力降。
③噴砂磨料應存放在干燥處,且有防雨措施,如果受潮,必須烘干。
6.2.3.2輔助設備:
① 準備好表面粗糙度比較板;②粗糙度檢測儀。
6.2.3.3表面噴砂處理做到:
①噴砂用壓縮空氣必須干燥、無油,可將壓縮空氣向白紙上噴射20~30秒鐘之后,紙上不留下油或水的痕跡即可。
②噴砂機噴嘴處空氣壓力在0.6~0.8Mpa之間調整;
③噴砂機噴嘴到基體表面距離為80~100mm;
④噴嘴口徑6~8mm;
⑤噴射角度30~80度;
⑥噴砂后用凈化風吹凈基體表面附著的灰塵。
6.2.4涂料施工
6.2.4.1涂料配制,本次施工內、外壁采用的涂料均為雙組份材料,按以下要求進行。
①涂刷前才能將雙組分混合配制,配制前確認A、B組分以及稀釋劑是否配套,是否與要求施涂型號一致,是否失效。
②A組分配制前必須攪拌至底部無沉積且上下均勻。
③將均勻的A、B組分按說明書重量比稱取少量試涂,用稀釋劑調整粘度使涂敷工藝條件達最佳,保證單膜厚度和質量。
④根據涂敷面積和單涂膜厚度計算A、B組分以及稀釋劑用量、并控制配料量在說明書要求時間內用完,防止配量太多涂刷超時而過度熟化增稠影響涂膜質量。
⑤涂料如需稀釋,嚴格按產品說明書要求控制,按計算好的稀釋劑比例稱好后加入A組分中攪拌均勻,而后加入B組分攪拌5-10分鐘,使A、B組分熟化。而后靜置5-10分鐘,消除攪拌引入的空氣泡。攪拌與靜置時間的長短取決于配料量,料多時間長。
⑥混合好的涂料用100目濾網過濾后方可施涂。施涂過程中一旦涂料反應過度而發生增稠,要立即停止施涂。該涂料已報廢應重新配料。涂料反應過度時間與環境溫度有關,溫度高所需時間短,料要少配,反之溫度低所需時間長,配料量可適當增加。
⑦稀釋劑要用涂料配套稀釋劑,不得隨意選用其它稀釋劑。
6.2.4.2涂敷工藝
①相對濕度高于80%時,不宜施工
②表面預處理合格后至涂敷第一遍涂料的間隔時間內出現銹蝕現象,應重新進行表面預處理。
③涂敷施工,按至上而下的順序進行涂敷,罐底要做好保護,防止涂料落上成瘤、涂敷應均勻,不得漏涂。
④焊縫、邊角及表面凹凸不平部位應用刷子先涂敷一遍。
⑤每道涂料的涂敷間隔應不大于24h,下一道涂料宜在上道涂料表干后涂敷。最后一道面涂料涂敷完成后,應在常溫25℃下固化7d以上方可投入使用。如果固化溫度低于10℃,應固化15天以上方可投入使用。
6.2.4.3施工過程
①內壁
A、底面處理:對于罐內壁進行機械噴砂處理。處理后的金屬表面達到GB8923-88中Sa2.5 級。
B、涂刷兩道底漆:底層涂料應在噴砂和清掃后進行。然后涂刷兩道導靜電防腐涂料,每道漆固化不小于24小時。
C、中間漆一道:當底漆固化24小時后,涂刷導靜電防腐涂料。每道漆固化不小于24小時。
D:面漆兩道:中間漆固化小于24小時后,涂刷兩道導靜電防腐涂料面漆,每道漆的固化時間為24小時。
以上5道漆膜的總厚度達到220μm以上。
②外壁
A底面處理:金屬表面處理要達到BG8923-88中S2.5級。
B底漆兩道:底面處理完后檢查合格,EPH高耐候外防腐專用底漆二道。每道漆固化時間為8小時。
C中間漆一道:底漆固化8小時后,EPH高耐候外防腐專用中間漆一道,要求顏色為淺灰色。
D面漆兩道:中間漆固化8小時后,EPH-1高耐候外防腐專用面漆兩道,其中顏色要符合《石油化工設備罐道鋼結構表面色和標志規定》SH3043-2003規定。其中,梁、柱、支承、鋪板、踏板為藍灰色。欄桿、護攔、扶手為淡黃色。罐體為銀色。
6.2.4.4質量檢驗
施工過程質量檢驗,① 每涂敷完一道漆后,應檢查涂層的外觀和濕膜厚度,不得漏涂,每層厚度應均勻。出現漏涂或厚度不夠時,應及時補涂。② 后一道面漆實干后、固化前應對涂層的厚度進行檢查,厚度不合格應增加涂敷層數直至合格。
防腐層最終質量檢驗,①內防腐層全部涂敷完成并固化后,應對防腐層進行外觀、厚度、漏點和粘結力檢驗。檢驗結果應做好記錄。② 外觀檢查應做到,內表面的防腐層應全部目測檢查;防腐層表面應平整、光滑,且不得有漏涂、發粘、脫皮、氣泡和斑痕等缺陷存在。表面有缺陷的防腐層應按本方案的規定進行處理。
6.2.4.5 漏點檢查應符合下列規定:
①用5-10倍放大鏡檢查,無漏點者為合格。對焊縫處等薄弱環節應重點檢查,對有不合格點的相應部位應加大抽查比例。
②檢查數量:涂料層應符合GB16906-97附錄中的驗收程序規定,抽查率應等于或大于涂敷面積的5%,并應對焊縫處等薄弱環節重點檢查。
③質量標準:漏點數1個/m2允許修補,漏點數超過1個/m2應進行全面復涂。
6.3 衛生、安全和環境保護
6.3.1防腐涂料在裝卸及運輸過程中嚴禁劇烈碰撞,應防止雨淋、日光曝曬和包裝件損壞,運輸過程中不得與酸、堿等腐蝕性物品及柴草、紙張等易燃品混裝,并應符合運輸部門有關規定。
6.3.2防腐施工現場必須有完善、有效的消防措施。
6.3.3防腐施工人員應配備防護工作服、防護(防毒)面具、防護鞋及防護手套等。施工現場還應備有防護藥品。
6.3.4進入罐內的操作人員至少應有2人,進口處應設置標志,并應有專人負責安全監護。
6.3.5在罐內施工時,應采用防爆照明燈具。手持式照明燈其電壓不得高于36V,燈線必須采用橡套電纜。無照明條件不得進入罐內作業。嚴禁攜帶一切火種進入罐內。
6.3.6在罐內施工時,應強制通風。
6.3.7罐內防腐層涂敷的安全、環境保護應符合《涂裝作業安全規程 涂漆前處理工藝安全》GB7692及《涂裝作業安全規程 涂漆前處理工藝通風凈化》GB7693的規定。
6.3.8離地面2m以上進行施工時,必須制定高處作業的安全防護措施,并嚴格執行。
6.4交工資料
防腐施工結束后,施工單位應提供下列文件:
6.4.1涂料出廠合格證及檢驗報告;
6.4.2防腐層涂敷施工記錄;
6.4.3防腐層質量檢驗報告;
6.4.4修補與復涂記錄,包括修補地點、原因、方法、數量及檢驗結果;
6.4.5其他有關記錄。
7.效果
2010年8月對我廠輸轉車間1座60000m3的原油罐進行了施工。通過檢查,防腐涂層整體性完好,涂層表面有光澤,無起皮、起泡、龜裂、脫落等現象。防腐涂層表面沒有任何銹蝕產物附著在表面。現正在繼續使用。
8.結論
10.1原油罐內壁防腐涂料,耐水、耐腐蝕性優異。表面氣孔率低,在該條件下使用抗滲透性優異,不易龜裂、耐磨、強度好;該材料漆膜堅韌、附著力強,其中硬度,漆膜致密,韌性好,漆膜光亮性、色澤鮮艷。
所以說該防腐涂層長期在含有酸性介質的水溶液中使用,解決了金屬表面腐蝕的難題【5】。
10.2原油罐外壁漆膜堅韌、硬度、抗老化性、耐寒性、抗裂性,優于一般的氯磺化聚乙烯涂料;在一般化工大氣中使用,比一般的常規涂料,如:醇酸調和漆、酚醛樹脂等使用壽命長;比一般氯磺化聚乙烯涂料耐蝕性提高了許多,特別是防腐后表面裝飾大為改觀。可以與有機氟涂料相媲美;表面氣孔率低,所以在潮濕的條件下抗滲性優異,是其它常規涂料不能比的;該材料的底漆在金屬表面涂刷時比氯磺化聚乙烯涂料底漆附著力有明顯的提高。
所以說,該涂料適用于化工大氣的環境中。設備表面、金屬框架表面防腐蝕采用該材料,解決了常規涂料難以解決的防腐問題。
總之,對于已使用多年的儲罐進行防腐涂裝,只要選用適合儲油罐使用的防腐涂料,制定合理的涂裝方法,嚴格執行預先制定的施工方案施工,就可以獲得較好的防腐涂裝的施工質量。
免責聲明:本網站所轉載的文字、圖片與視頻資料版權歸原創作者所有,如果涉及侵權,請第一時間聯系本網刪除。
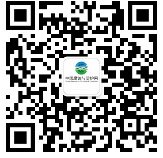
官方微信
《中國腐蝕與防護網電子期刊》征訂啟事
- 投稿聯系:編輯部
- 電話:010-62316606-806
- 郵箱:fsfhzy666@163.com
- 中國腐蝕與防護網官方QQ群:140808414