0 引言
燃氣輪機作為一種動力裝置,廣泛應用于艦船推進、汽車機械、航空航天等領域,其動力來源通常是由葉片從高溫高壓氣體中獲取能量,再將其轉化為機械功。渦輪葉片是燃氣輪機中的重要部件,一般由抗高溫氧化、腐蝕能力良好的鎳基高溫合金制成,作為目前承溫能力最高的單晶高溫合金其承溫能力已接近合金承受溫度的理論極限[1-2]。然而隨著對發動機推重比和進口溫度需求的迅速增加,在工作環境中燃氣溫度將超過鎳基高溫合金的熔點250 ℃以上,導致材料更快地產生熱疲勞和降解[3-5],因此,人們研究發明了熱障涂層(Thermal Barrier Coatings,簡 稱 TBCs)用 以保護基體免受高溫燃氣損傷。
熱障涂層是通過一定工藝將耐高溫陶瓷材料涂覆在基體上的保護層,它的發展始于 20 世紀 50年代,美國國家航空航天局率先提出了熱障涂層的概念,并將 CaO-ZrO2/NiCr 應用于火箭飛機的噴氣管[6]。隨著熱障涂層的不斷發展,目前用于航空普遍使用的是 6%~8% 氧化釔穩定氧化鋯[7-8]。目前,配合使用熱障涂層與內部冷卻技術,可以使合金表面溫度降低 100~300℃,使燃氣輪機能夠在遠遠高于高溫合金熔點的環境中工作[9]。因此,利用該技術來改善渦輪葉片的基體環境是切實可行的。然而,熱障涂層服役環境惡劣,在外物作用、內部生長應力、相變引起的體積膨脹等多方面因素的交叉作用下,極易萌生裂紋,隨著服役時長的增加,裂紋也將進一步延伸、擴展,引發剝落并導致最終失效。近年來,國內外學者對熱障涂層進行了大量研究及改良,包括制備方法、材料成分、涂層結構等多個方向,此外,為保障航空發動機的質量,節約熱端部件的高昂成本,熱障涂層的再制造技術,包括涂層裂紋修復以及涂層清洗后再制造也成為了實現航空領域穩定發展的關鍵。然而截止目前,熱障涂層領域仍存在很多問題,尤其是涂層失效,大大影響了航空發動機的使用安全性。
本文從熱障涂層的沖蝕、氧化以及熱腐蝕三個方面介紹了熱障涂層的失效機理,旨在為先進熱障涂層的制造提供更多理論基礎和設計思路,綜述目前應對涂層失效的措施,并對熱障涂層的研究和應用前景進行了展望。
1 熱障涂層簡介
熱障涂層通常選用雙層結構[10-12],這是熱障涂層目前應用最廣的結構形式并在航空發動機渦輪葉片上得到了實際應用,如圖 1 所示。
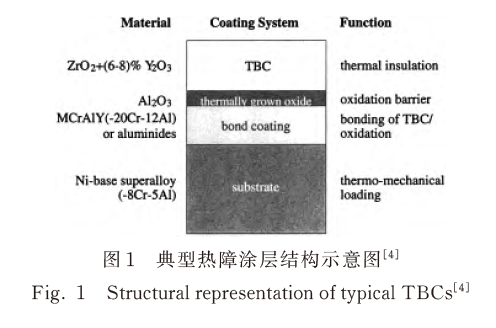
熱障涂層的頂部為陶瓷層,應具備的功能有耐蝕、隔 熱以及較高的抗熱震性。 通常為YSZ(6%~8%)制成的厚度約300μm 的陶瓷層,熔點較高(約2700℃),熱導率較低(致密材料在1000 ℃下的熱導系數約為 2.3 W·m-1·K-1)[13-16]。
陶瓷層和基體之間存在一層厚度為75~150μm 的粘結層(Bond Coat),目前使用最廣的粘結層材料為 MCrAlY,M 為金屬 Fe,Ni,Co 或者他們之間的組合[17-20]。Ni+Co 是最常用的組合,Ni+Co基能使基體在具備一定緩和應力能力的同時兼具一定的抗氧化和腐蝕性能。Cr、Ni 可起到固溶強化作用,此外,Al 元素在高溫下生成Al2O3,可提供抗氧化性能,Cr 元素可在 Al 氧化后形成氧化物Cr2O3,起到隔絕基體的效果,并提供一定的抗熱腐蝕能力,促進 Al2O3 的生成。微量元素Y 的含量很低,一般小于 1%,能夠細化晶粒,提高 Al2O3 與基體間結合力,改善涂層的抗熱震性[21. 22]。
粘結層 MCrAlY 中主要相組成為 γ(Ni+Co)固溶體和 β-NiAl金屬間化合物雙相,渦輪葉片工作環境下,溫度超過 700 ℃,可能導致粘結層氧化,并在粘結層和陶瓷層間生成厚度為1~10 μm 的熱生長 層(Thermally Grown Oxide,簡 稱 TGO),粘結層內 Al 含量減少,β-NiAl轉變為 γ ′(Ni3Al)相。當 涂 層 中 β 相 消 失 時 ,粘結 層 的 抗 氧 化 性降低[23-25]。
2 熱障涂層的失效行為
從很大程度上來說,熱障涂層的壽命可以決定整個高溫零部件的壽命,而熱障涂層的失效剝落是熱障涂層在航空燃氣渦輪發動機中的最大問題,需要以嚴格的標準頻繁檢查來確保安全,極大地限制了熱障涂層的應用。對其失效機理的研究是為了更有針對性地解決失效原因,提高熱障涂層服役壽命,因此通過認識涂層失效的機理并完善其成分結構是先進熱障涂層研究中的重要一環。
2.1 沖蝕及外物損傷
燃氣輪機涂層表面的物理損傷通常有兩種情況,第一種情況源于燃燒形成的碳顆?;蛘甙l動機基體磨損形成的粒子[26],夾雜在氣流由于慣性力的作用撞擊涂層表面,形成沖蝕,如圖 2 所示。第二種情況是由于燃氣輪機外界氣流中夾雜著雜質或者顆粒[27],如高空中的冰塊、砂礫、火山灰等,在慣性力作用下會對整個渦輪葉片造成碰撞,如圖3 所示。沖蝕和外物損傷都主要發生在陶瓷層的頂部,可能導致涂層內部柱狀晶變形和開裂,甚至熱障涂層局部厚度減少,在葉片表面的陶瓷層上產生刻痕或者形變。將造成系統的平衡性以及葉片的氣流特性略微降低和退化,當葉片處于旋轉或 葉 片 通 過 頻 率 狀 態 下 時 ,易 造 成 疲 勞 失效[28-29]。有些外物撞擊后,產生的殘余應力可能致使裂紋擴展到粘結層/金屬基體界面,隨后裂紋沿著界面橫向擴張,使粘結層和陶瓷層部分從基體上剝落,進一步造成涂層的失效。沖蝕的作用深度通常與作用粒子的質量、粒徑和速度有關,此外,陶瓷層硬度、彈性模量等力學性能也將會影響作用層深度[26-32]。
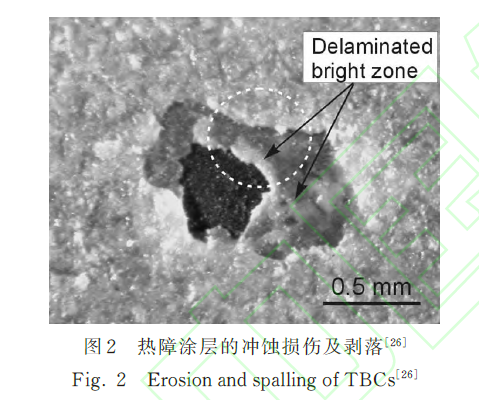
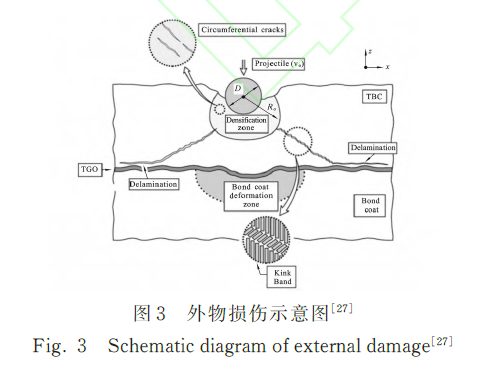
2.2 燒結及氧化行為
通過各種手段沉積后涂層的表層不可避免地存在氣孔和裂紋,在 高溫服役環境 下(大于 1200 ℃),可能會發生燒結反應,使涂層致密化以及熱導率上升。并且由于基體與陶瓷層間的熱膨脹系數不匹配,燒結會造成額外應力。當處于逐漸升高的溫度下時(約為1200~1400 ℃),頂部陶瓷層沿厚度方向將有明顯的線性收縮,在自由表面附近燒結效應更加顯著[33]。此外,氧在二氧化鋯基的陶瓷層中具有較高的離子擴散率,所以粘結層可能會被氧化,形成TGO。TGO 的氧離子擴散率較低,但鋁元素與氧元素的親合力較強,有向外擴散的趨勢,當鋁元素的擴散速度小于其反應生成α-Al2O3 相的速度時,Cr 及Ni 元素也將相繼被氧化為 Cr2O3、NiO、Ni2Cr2O4 等氧化物,使 TGO 厚度增加,如圖 4 所示。大量研究表明[34-37],熱生長氧化物內部存在兩類應力,即由于氧化物和金屬基體間熱膨脹系數差異導致的熱失配應力和氧化膜生長產生的生長應力。Li M H 等[38]通過觀察,認為粘結層發生嚴重氧化時,氧化層生長較快,粘結層與TGO 界面不規則,不規則的界面將會產生應力集中,并會加速面外應力的累積,從而導致粘結層與 TGO 間界面的開裂。A. Rabiei 等[37]利用短裂紋斷裂韌性和測量的缺陷波長等材料屬性預測TBC 中的 TGO 臨界厚度,認為 TGO 存在一個厚度約為 5 μm 的臨界值,低于此臨界值時 TGO 不會影響到涂層,高于臨界值時,裂紋形態和分層面都發生了明顯的變化,并且會出現明顯裂縫,如圖5所示。
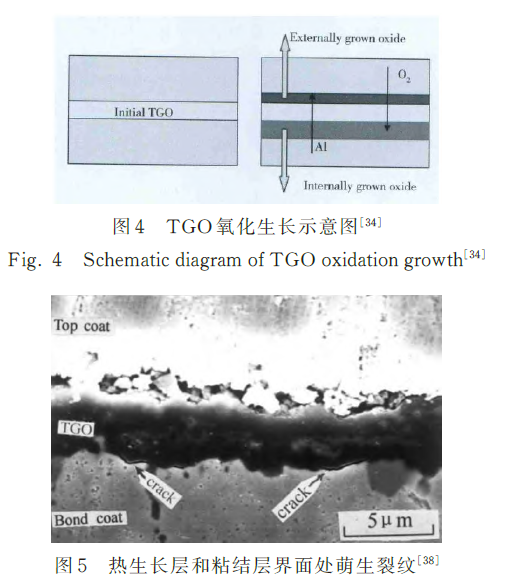
2.3 腐蝕行為
2.3.1 熱障涂層在海洋環境下的腐蝕行為
在海洋高濕、高鹽霧環境下,體系中存在的大量NaCl,將沿著熱障涂層表面的孔隙、裂紋通道持續侵入 MCrAlY 粘結層以及基體,在高溫條件下會加速粘結層的氧化從而使熱生長層的厚度增加,增大其開裂傾向。即便處于常溫條件下,鹽霧侵入也會使表層氧化鋯晶體擠壓變形,產生裂紋的擴展[39-40]。燃料中的含硫物質也是造成燃氣輪機腐蝕的一大成因。在 650~750 ℃ 的溫度范圍內,會發生低溫熱腐蝕。由于SO3 分壓偏高,導致金屬氧化物酸性熔解,在 Ni-Cr、Co-Cr、Co-Cr-Al 和 Ni-Cr-Al 合金中形成Na2SO4 和NiSO4 或CoSO4的低熔點混合物,造成點蝕。當處于 850~950 ℃ 較高的溫度下,一般會通過形成金屬硫化物來提高熔融硫酸鹽中Na2O的活性,進而對熱生長層產生堿性溶劑腐蝕[41]。當船用燃氣輪機接觸到工業或森林火災污染的空氣,以及自身燃料中就會產生腐蝕鹽類,如V2O5、Na2SO4。這些腐蝕鹽類產生以下反應[42-43]。

陶瓷涂層中ZrO2通常以不穩定的四方相(t‘)存在,經式(1)和(2)反應失去穩定組元 Y2O3 后,ZrO2 易于在 1 220 ℃以下發生相變,轉換為單斜相(m),當 ZrO2從四方相轉化為單斜相時,會伴隨著4. 6% 的體積增大[13],這樣的體積變化帶來的相變應力將會引起裂紋甚至是涂層的剝落。周長海等[44]在 900 ℃下向等離子噴涂 Y2O2-ZrO2熱障涂層中添加 V2O5 與 Na2SO4 混合鹽,其表面由粗糙,有部分未熔顆粒,且存在微裂紋的層片狀涂層轉變成為塊狀、細棒狀的 YVO4,從而影響了 Y2O3 的穩定作用,如圖 6 所示。
2.3.2 熱障涂層在航空領域的腐蝕行為
相對于海洋環境下的燃氣輪機而言,航空發動機使用更為為純凈的燃料,含硫量較低,硫化比例少。但仍可能在飛行過程中沉積上其他鹽類。
火山活動會使空氣中夾雜鈣鎂鋁硅等元素的鹽類(CaO-MgO-SiO2-Al2O3簡稱CMAS)[45-46]。 CMAS 的熔點較低,在 1 190~1 260 ℃間。當其沉積在燃氣輪機部件的熱障涂層上時,可能會在高溫燃氣的作用下受熱熔化,潤濕陶瓷層并滲透進入 TBCs。一方面可能導致不穩定的四方相 t’溶解為單斜相 m 和立方相 c,產生相變應力;另一方面CMAS 滲透進涂層填充孔隙會導致楊氏模量的增加以及應變容限的降低,在高溫下陶瓷層與粘結層以及鎳基高溫合金的熱膨脹系數不匹配產生的熱應力將會導致涂層失效[47-48]。A.K.Rai 等[47]認為,改變材料結構形貌比改變材料化學性質更加重要,并提出了表層致密化以及將電子束氣相沉積制得的柱狀結構涂層修改為羽狀結構。L.Steinberg 等[46] 制 備 了 不 同 組 分 的火 山 灰 和CMAS,在室溫環境中,羽狀結構抗外物沖蝕速率明顯優于普通涂層,然而在高溫條件下一旦預制的火山灰和 CMAS 滲透進涂層內部后,羽狀結構涂層和普通涂層的受沖蝕速率分別達到 5.06~5.95 g/kg 和 2.72~3.24 g/kg,即羽狀結構涂層與腐蝕鹽類作用區域的增加反而會加劇外物對涂層的侵蝕。
3 熱障涂層的修復與再制造研究
熱障涂層自問世以來,就有大量學者從結構或成分方面對其進行改善,并取得了一定的成果。ChangF 等[49]利用激光在熱障涂層表面制備了釘扎結構,經實驗證明釘扎結構有助于減輕沉積層的殘余應力,并且有助于提高TBC在熱循環中的應變耐受性。Liu H 等[50]使用離子鍍膜技術在熱障涂層表面制備了Pt 層,在 1250 ℃的CMAS 環境下進行腐蝕,在 2 h 以內Pt 層以下涂層保留了結構完整性。徐振華等[51]制備了新型 La(2Zr0. 7Ce0. 3)2O7熱障涂層,經 1089 h 恒溫氧化后陶瓷層氧化增重低于 8YSZ 涂層。
盡管上述熱障涂層的改性在某些方面優于傳統的6%~8%TBCs,但始終存在一些問題,如制備工藝復雜,保護周期短或者界面結合較差等。無法避免在長期處于服役環境的情況下出現裂紋甚至剝落,因此目前為止涂層的修復仍是延長服役壽命的關鍵?,F階段涂層的修復方法通??煞譃閮深?,其一是在制造階段加入自修復材料,使涂層在高溫氧化環境下自發完成修復過程;另一種是在涂層出現裂紋或剝落時,對其進行填充,當出現較大程度的相變或者不可修復的破損時,可將其除去后再使用等離子噴涂(APS)或電子束物理氣象沉 積(EB-PVD)等 方法進行熱障涂層的再制造。
3.1 自愈合涂層
自愈合涂層是指涂層在受到損傷后具備一定的自修復能力,自愈材料包括金屬、聚合物、陶瓷以及它們的復合材料,這些復合材料在受到機械,裂紋擴展后產生自修復機制。損傷自修復的先決條件是產生移動相,通過移動相填充裂紋,修復材料機械性能。
早在 20 世紀 70 年代就有關于自修復材料的報道。F. F. Lange[52]將 SiC 材料熱震后發現裂紋,隨后進行 1400 ℃恒溫氧化,在 10 h 后發現裂紋區域被藍色SiO2薄膜所填充,自主完成了修復過程。這是由于SiC 在高溫下暴露一段時間后,將與進入的氧氣形成SiO2 反應,該反應通常發生在 720 ℃左右。形成的硅具有非晶態結構,處于半流體狀態,能沿著周圍的微裂紋和微孔隙流動。Al2O3 氧化物如果接近TGO 和ZrO2 氧化物,則形成固體復合化合物,如莫來石(3Al2O3·2SiO2)和 ZrSiO4。這個完整的過程被定義為一個自愈過程,其最終產物可作為額外的氧屏障限制其向粘結層的通量,并因此提高了系統的抗氧化性。具體反應如式(3)~式(5)所示。
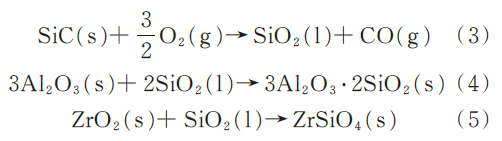
為了提高熱障涂層的熱循環壽命,K. Portilla-Zea 等[53]使用霧化器在 TBC 粘結層與陶瓷層間制備了一層SiC 纖維層,研究添加 SiC 對YSZ 熱障涂層的影響。在 1100 ℃下循環氧化后,保持 190 ℃恒溫加熱 80 min,隨后使用通用試驗機進行附著力測試,結果表明,與常規的 YSZ TBCs 相比,增加了SiC 層的TBCs 在循環氧化后能夠產生硅類化合物填充微裂紋,并且減少和延緩裂紋的延伸,具有更強的附著力。
研究人員還試圖開發新的涂層體系,將其整合至 TBC 自修復涂層中 。Ouyang T 等[54] 在GH4169 基體上制備了 YSZ/SAZ 涂 層(SAZ 由SiC、Al2O3 和YSZ 粉末噴霧干燥獲得),經 1 100 ℃等溫氧化 20 h 為一個循環,在 20 個循環后 YSZ/SAZ 熱障涂層的質量損失僅為YSZ 體系熱障涂層的 43. 66%。利用Al2O3 具有較低的氧擴散系數(1400 ℃時約為10-12 cm2/s),進而增強了 TBC 體系的抗氧化性。在過去幾十年內,有大量關于其他自修復涂層體系的文獻報道[55-58]。
MoSi2 作為近年來熱障涂層裂紋自修復的新興材料 ,具 有與 YSZ 相近的熱膨脹系 數(8. 5× 10-6 ℃),在 800 ℃以上,會首先氧化生成 Mo5Si3,然后再進一步氧化生成易于揮發的 MoO3。在熱障涂層的工作溫度下,與氧氣接觸并發生反應,生成的MoO3 將會揮發,剩余產物 SiO2體積相較反應前的 MoSi2 要大,導致 SiO2擴張,當涂層在熱循環過程中出現裂紋時,SiO2 可能由于體積膨脹進入周邊裂紋,從而實現裂縫填充。此外,SiO2 會與陶瓷層中的 ZrO2反應生成 ZrSiO(4鋯石),該過程造成體積收縮,使裂紋間隙減小。并且 ZrSiO4 與 ZrO2結合力較好,強度、硬度高,能夠對涂層的機械強度進行較好的修復。F. Nozahic 等[59]使用懸浮液等離子噴涂技術將 MoSi2 分散在 8YSZ 中,經火花等離子燒結制備復合材料。研究了該復合材料在 1 000~1 300 ℃溫度下的 10 h 循環氧化,在 MoSi 顆粒周圍和YSZ 基體晶界附近生成了SiO2 修復裂紋并與ZrO2基體生成ZrSiO4,恢復基體的機械性能,經自修復后的涂層中已無明顯裂紋。Z. Derelio‐glu 等[60]在使用 MoSi 顆粒作為裂紋愈合劑的基礎上在其中加入了硼合金組元,B 元素在使用溫度下能增加 SiO2的流動性,在 SEM 圖的觀察下,發現SiO2移動了 40 μm,促進了裂紋的填充,如圖 7 所示。此外,MoSiB 體系的涂層在抵抗 CMAS 腐蝕方面也被證明是切實有效的[61],熔融 CMAS 會與涂層作用形成CaMoO 和SiO ,相互作用的反應產物改變了CMAS 的組成,產生結晶,有效地固定了CMAS,并抑制了與 MoSiB 基涂層的進一步相互作用。此外,涂層中存在一些裂紋在高溫下會被周圍流動的硼硅酸鹽填充。
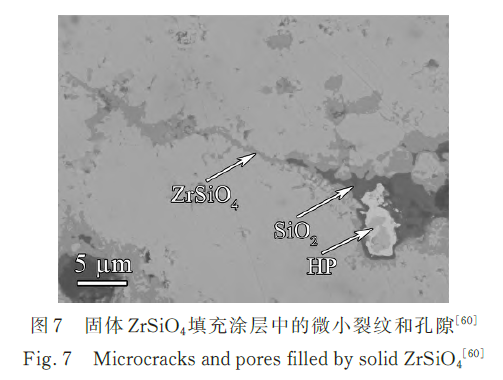
美國宇航局也發布了有關飛機發動機應用的高溫輕質自修復復合材料的研究成果[62]。研究了不同添加劑對CrMoSi-SiC 復合涂層的修復情況,在 1600 K 氧化 24 h 后,沒有任何添加劑的 CrMo‐ Si-SiC 試樣的劃痕和孔洞幾乎沒有變化。但是,添加 5wt. % CrB2 后待修復劃痕和孔洞有明顯閉合;在 CrMoSi 合金中加入 1wt. % Ge 作為固溶體對修復劃痕有效果顯著,但對孔的封閉影響較小;當CrMoSi 合金中Y 含量為 0. 1wt. %時,劃痕沒有得到明顯修復;添加 5wt. % ZrSiO4 對修復劃痕效果較好,但氧化皮呈層狀且易碎。
3.3 熱障涂層的再制造方法
航空發動機長期處于高溫高壓、強腐蝕性的惡劣環境下,當渦輪葉片或其他熱端部件長期服役后,熱障涂層易出現裂紋、剝落等破損,會導致防護作用逐漸降低甚至失效。由于航空發動機關鍵零部件制造工藝復雜,生產周期較長,直接更換新部件將造成資源的大量損失。而對缺陷部位進行修復或再制造,能夠大幅節約生產成本。因此,燃氣輪機葉片熱障涂層的修復及再制造是一項關鍵的航空技術,經濟效益好,材料利用率高,具有廣闊的工程應用前景。
3.2.1缺陷涂層的修復方法
液體注入等離子體噴涂是一種具有潛力的涂層修復方式,工作原理是通過輸送馬達抽出溶液,在載氣的作用下,經過霧化噴嘴,進入等離子體中,在熱等離子體中發生物理、化學反應后,沉積到金屬基體上,噴霧的前驅液滴以液態形式沖擊基體,形成涂層。Rousseau 等[63]使用了低功率等離子體反應 器(LowPower Plasma Reactor,簡 稱LPPR)用于修復局部損壞的 TBC。將硝酸鹽ZrO(NO3)2 和 Y(NO3)2 前驅體溶液以低功率(240 W)噴入Ar/O2 等離子體放電并轉化為氧化物涂層,修復受損試樣上的部分裂紋和孔隙,所得涂層的顯微結構為層狀,具有較高的微米和納米孔隙度。如圖8所示。對受損EB-PVD 涂層,LPPR 涂層也在柱狀間隙(圖 8 白色箭頭)及分層裂紋(圖 8 黃色箭頭)中展現出了較強的滲透性,與此同時,由于粘結層中的鋁元素和等離子放電過程中的氧化劑的交互作用,有約3μm 的新熱生長層生成,這種小尺寸的熱生長層可以為整個涂層系統提供一定的化學和機械相容性。
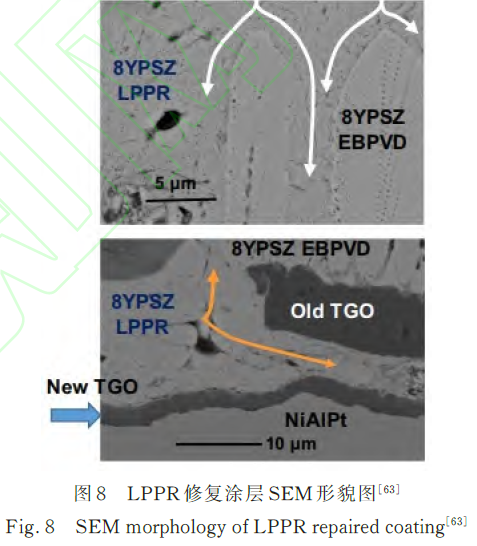
溶膠凝膠法通常用作涂層的制備,且其成本低廉、操作簡單,相較其它涂層制備工藝較為靈活,因此可應用于涂層的修復,使用浸漬法可在熱障涂層裂紋處填充溶膠-凝膠涂層,涂層質量與溶膠中YSZ 粉末質量分數、熱處理溫度、浸涂次數等有關[64]。然而浸涂過程的方向性會導致裂紋的不均勻不對稱填充,此外,浸涂次數的把控也將大大影響涂層的成型狀態,浸涂次數較少會有明顯的凝固裂紋,過多則會導致后續沉積效率的降低以及涂層附著力的減弱。因此要得到廣泛應用還有待于進一步研究。
3.2.2 失效熱障涂層的再制造方法
當熱障涂層在服役過程中厚度低于臨界尺寸或產生不可修復的破損時,難以修復原有涂層,需要去除并重新涂覆新的涂層。新涂層與原有涂層的制造工藝相同,可使用等離子噴涂、電子束物理氣象沉積以及化學氣相沉積等多種沉積方法進行新涂層的制造,因此,熱障涂層再制造的重點和難點在于完全去除原有涂層的同時不損傷基體。
早期應用于熱障涂層陶瓷面層的去除方法有噴砂法、高壓水射流法以及鹵氣反應法等,噴砂法去除陶瓷涂層效率高,成本低,但可控性較差,容易對粘結層甚至基體材料造成損傷。高壓水射流去除法通過保持渦流脈沖水射流噴嘴與渦輪工作葉片靶距,將噴嘴沿著渦輪工作葉片的軸向方向逐行往復運動,逐層剝離當前表面的陶瓷層,操作工序簡單,無有害物質排放以及環境污染問題,但可控性差,易損傷粘結層和基體。鹵氣反應法是將熱障涂層和含氟粉末混合加熱至980~1050℃,持續弱化涂層和基體間的結合,使涂層自發地與基體分離,但設備昂貴,易對涂層及基體均造成損傷。
目前,國內外應用較多的熱障涂層去除方法是熔融堿法,熔融堿法的原理是利用金屬粘結層與陶瓷層之間的熱生長氧化層(主 要成分為 α-Al2O3)容易被堿性溶液腐蝕的原理松動涂層。宮聲凱等[65]使用了 KOH 與NaOH 混合溶液,將涂層置于含有上述溶液的坩堝中反應 3~20 min,再將處理后的熱障涂層試件進行表面濕吹砂處理,去除部分粘結層。在掃描電鏡下觀察到陶瓷層已被完全去除,且在電鏡分辨精度范圍內沒有發現鉀和鈉離子的存在,證明對基體和粘結層是安全的。該方法對設備要求低、工藝簡單,并且對試樣損害較小。
由于激光技術的進步,激光清洗也逐漸進入了人們的視線,被廣泛用于文物、微電子線路板等材料的清洗,是一種新型表面清潔技術。與噴砂法等傳統的清潔方法相比,激光清洗具有可控性好、無機械接觸、基底損傷小、材料適應性廣等優點,且清洗廢料為固體粉末,易于回收,是一種綠色清潔的清洗方式[66]。工作原理如圖 9 所示[67]。激光直接作用于涂層表面,可通過編程并在遠程控制下破壞雜質和基底之間的作用力,隨著激光作用時間的增加,待清洗物與基材之間熱膨脹系數的差異將在界面處產生壓力,清洗物發生屈曲、失穩,從基材表面衍生裂紋,出現機械斷裂、振動破碎等現象,最終以噴射的方式從基材表面清除或剝離。清洗閾值與待清洗物的顆粒大小、物化性質以及基體材料有關[67-68]。
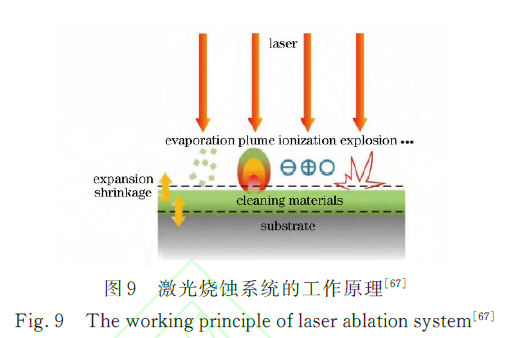
目前,國內外已有科研機構開展了關于激光清洗去除航空發動機零部件表層雜質的理論和試驗研究。Zhu 等人采用脈沖固態激光清洗裝置對波音系列飛機上的BMS10-11底漆進行清洗[69]。不同激光能量密度清洗下的飛機表面宏觀形貌如圖 10 所示。研究表明,隨著激光能量密度的增大,表面漆料的清洗也更加徹底,激光能量密度達到5J/cm2 時,清洗效最好,且不會降低飛機蒙皮及鉚釘孔間的摩擦磨損性能。而當進一步增大能量密度后,將對零部件表面鋁層造成損傷。
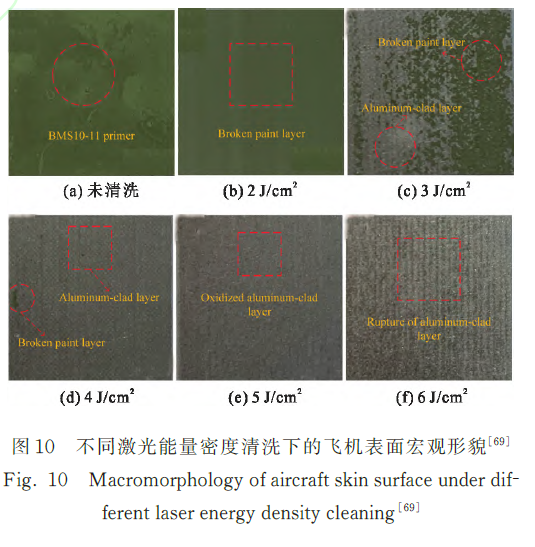
曼徹斯特大學Marimuthu[70]等基于有限元法模擬分析了激光清洗航空發動機零部件熱障涂層過程中的瞬態溫度場、殘余熱應力以及材料去除率,并研究了積分通量對涂層和基體燒蝕速率的影響,得 出 TiN、CrTiAlN、WC值,其驗證性實驗與有限元模擬的結果具有良好的一致性。
4 結語
大量的研究和實踐證明了熱障涂層是保障燃氣輪機高溫部件有效運作的關鍵技術。隨著燃氣輪機進口溫度以及推重比需求的增加,對熱障涂層也提出了更高的要求,未來熱障涂層的發展主要有以下幾個方面。
(1)熱障涂層表面裂紋及界面脫粘缺陷的無損檢測。通過對涂層顯微組織形變大小、裂紋形成與擴展位置、外物損傷程度進行準確的預測與評估,判斷涂層的破壞程度,從而界定其失效與否,并及時對產生的磨損、磨蝕現象甚至開始裂紋擴展的涂層進行修復,進而避免陶瓷面層的大面積剝落,顯著提升熱障涂層的可靠性。
(2)新型熱障涂層多因素失效評估及成分、結構優化。稀土氧化物摻雜氧化鋯、稀土鋯酸鹽等新型熱障涂層雖已有較多的探索研究,但對其測試分析多數只滿足單一環境的使用需求,然而涂層投入實際生產應滿足外物磨損、高溫氧化、熱腐蝕等多元環境的使用需求。此外,粘結層中 Al、Cr、Ni 等元素擴散形成的氧化物熱生長層也是引發裂紋和分層的重要成因,而目前對于熱障涂層的改性研究主要集中在陶瓷層,因此,需要對粘結層成分優化,探索替換 Al、Cr、Ni 等元素且抗氧化性能較優的粘結層材料。與此同時,相較于傳統雙層涂層結構,成分分布的梯度化能顯著地減少或消除涂層內部界面,緩解涂層內部應力,故開發成本低廉,工藝簡單的梯度熱障涂層制備方法也將成為未來熱障涂層開發探索的方向。
(3)熱障涂層自愈合修復新理論及再制造新技術。自愈合材料對涂層的填充具有顯著效果,但目前自愈合修復主要針對涂層尺寸修復,對于相變及應力緩解研究較少,因此,應對這一問題進行綜合研究,探索自愈合修復新理論。此外,對于現階段熱障涂層的研究,需正視其失效問題,基于現有再制造工藝,開發再制造新技術,為熱端部件在航空航天領域的實際使用中提供更可靠的保障。
免責聲明:本網站所轉載的文字、圖片與視頻資料版權歸原創作者所有,如果涉及侵權,請第一時間聯系本網刪除。
相關文章
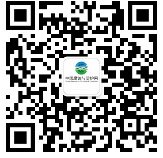
官方微信
《中國腐蝕與防護網電子期刊》征訂啟事
- 投稿聯系:編輯部
- 電話:010-62316606-806
- 郵箱:fsfhzy666@163.com
- 中國腐蝕與防護網官方QQ群:140808414
點擊排行
PPT新聞
“海洋金屬”——鈦合金在艦船的
點擊數:7130
腐蝕與“海上絲綢之路”
點擊數:5741