近年來隨著原油中硫、有機酸及各種重金屬含量的增加,延遲焦化裝置設備、管線腐蝕問題日益嚴重。加熱爐作為延遲焦化裝置的核心設備,其防腐問題也成為企業關注的焦點。
本文通過對延遲焦化裝置存在的高溫硫腐蝕和氧化腐蝕等反應機理進行分析,并結合延遲焦化裝置的原料性質和主要操作參數,提出延遲焦化裝置加熱爐防腐問題的對策。供企業參考借鑒。
01 腐蝕原因
1 加熱爐爐管高溫氧化、硫化腐蝕
加熱爐是焦化裝置的核心設備,其發生腐蝕的主要形態為高溫硫腐蝕。爐管材質為Cr9Mo,入口溫度為285~310℃,出口溫度為490~496℃,入口壓力3.25MPa,出口壓力0.10MPa。由于加熱爐燃氣(油)中含有微量的雜質硫及硫化氫,加熱爐爐管將受到高溫氧化、高溫硫化腐蝕兩個不同方式的腐蝕。
硫含量:硫含量越高,腐蝕越重。金屬表面很難形成連續、完整的硫化物保護層,此時的硫化腐蝕受金屬與環境界面化學反應所控制,高溫硫化腐蝕速度與含硫量呈直線關系,幾乎不存在臨界硫含量。
氧含量:氧含量越高,氧化腐蝕越重,但氧含量超過一定的值后,氧化速度漸趨穩定。
2 加熱爐爐管損壞形式
1、爐管鼓包、開裂失效
在熱強度較高的部位,由于氧化腐蝕、硫化腐蝕及滲碳腐蝕的共同腐蝕作用下,爐管壁厚減薄而造成爐管鼓包,甚至開裂。
2、爐管壁厚減薄嚴重失效
因爐管嚴重結焦,導致管壁溫度偏高,加速了氧化及腐蝕,使爐管壁厚減薄嚴重而失效。
02 對策
1 控制原料鹽含量
為了降低延遲焦化裝置原料中的鹽含量,車間根據生產實際情況,與相關部門協調,加強對原料鹽含量的監控,加強原油“一脫三注”的工藝管理,嚴格控制減壓渣油中的硫含量、鹽含量在車間要求的指標范圍之內。
2 設備選材
材料的選擇關乎裝置能否長周期的運行,對延遲焦化裝置而言,需將不耐硫腐蝕的碳鋼材質更換為ASTM A335 P9或更高的新型材料,以減輕因腐蝕對設備的傷害。
3 防腐措施
嚴格工藝操作,禁止設備超溫超壓,盡量減少波動。
延遲焦化裝置高溫重油部位以材質防腐為主,低溫輕油部位則要依靠選材、工藝防腐措施以及其他手段聯合進行防腐控制。
總之,延遲焦化裝置在加工處理高硫稠油時,所使用的管線、設備應選取防腐性較高的材質為宜。同時日常工作中應加強加熱爐、各設備及管線防腐的管理和監控,將企業各項防腐制度落到生產實處,確保各項防腐措施工作有效的開展。
免責聲明:本網站所轉載的文字、圖片與視頻資料版權歸原創作者所有,如果涉及侵權,請第一時間聯系本網刪除。
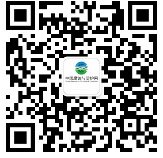
官方微信
《中國腐蝕與防護網電子期刊》征訂啟事
- 投稿聯系:編輯部
- 電話:010-62316606-806
- 郵箱:fsfhzy666@163.com
- 中國腐蝕與防護網官方QQ群:140808414