摘要
利用掃描電鏡及電化學工作站研究了經不同處理后TC4鈦合金的微弧氧化膜層微觀形貌和電偶電流密度。結果表明:高溫氧化未使微弧氧化膜層表面形貌發生明顯改變;TC4鈦合金與鋼接觸時極易發生電偶腐蝕,不能直接接觸使用;對鈦合金進行微弧氧化處理后可降低電偶電流密度及電偶腐蝕敏感性;硅烷化封孔處理對微弧氧化膜層的電偶電流密度影響甚小;微弧氧化后進行高溫氧化及硅烷化封孔處理明顯降低TC4鈦合金的電偶電流密度。
關鍵詞: TC4鈦合金 ; 高溫氧化 ; 微弧氧化 ; 電偶電流
鈦合金具有重量輕、強度高、疲勞性能好、在高溫條件下具有一定的耐腐蝕性等特點[1],在航空、航天、船舶等領域有廣泛的應用[2]。但在海水和海洋大氣腐蝕環境中,由于鈦合金的電位較高,與異種金屬接觸使用時會發生電偶腐蝕。微弧氧化技術是解決該問題的有效措施,是提高鈦合金性能的一種有效的表面處理方法[3,4]。
微弧氧化是一種直接在有色金屬表面原位生長陶瓷層的新技術[5],通過微弧氧化獲得的薄膜不但具有附著力強和耐腐蝕性好的優點[6],而且還能夠大幅度地提高表面的硬度、耐磨性、電絕緣性等性能[7],能對基體起到很好的保護作用[8-10]。但微弧氧化涂層是在高壓作用下工件表面進行弧光放電,所得的氧化涂層中存在大量的放電通道,導致微弧氧化涂層中存在大量微米尺度的微孔。在腐蝕環境中,這些微孔的存在,不但為腐蝕介質滲入到基體提供了通道,而且加快了其侵蝕基體的速度[11,12]。因此,有必要對氧化涂層進一步處理,以隔絕基體和外界環境介質的接觸,增加其防腐性能。
本文采用微弧氧化、微弧氧化+高溫氧化、微弧氧化+硅烷化封孔、微弧氧化+高溫氧化+硅烷化封孔等幾種處理方法對TC4鈦合金表面微弧氧化膜層進行處理,考察不同表面處理工藝條件對TC4鈦合金微弧氧化膜層及電偶電流的影響。
1 實驗方法
實驗材料采用湖南湘投金天鈦金屬股份有限公生產的2.5 mm規格TC4鈦合金板材,其主要化學成分 (質量分數,%) 為:Al 6.47、V 4.2、 Fe 0.22、C 0.01、O 0.16、Ti余量。取120 mm×25 mm×2.5 mm的TC4鈦合金板材,對其微弧氧化處理后進行高溫氧化及封孔處理,具體工藝為:1#試樣表面經微弧氧化處理、2#試樣表面經微弧氧化+高溫氧化處理、3#試樣表面微弧氧化+硅烷化封孔處理、4#試樣表面經微弧氧化+高溫氧化+硅烷化封孔處理。微弧氧化采用正恒流電脈沖控制方式,電解液溫度控制在20~35 ℃。微弧氧化膜層的高溫氧化溫度為450 ℃,高溫氧化氛圍為空氣。封孔處理采用硅烷偶聯劑水解溶液。實驗后采用FEI Quanta-200型環境掃描電鏡 (SEM) 觀察微弧氧化膜層的微觀形貌,并采用PAR2273電化學工作站測量TC4鈦合金與925鋼耦合的電偶電流密度。
2 結果與分析
2.1 表面處理工藝對微弧氧化膜層微觀形貌的影響
不同工藝條件下的微弧氧化膜層的表面微觀形貌見圖1。由圖可知,TC4鈦合金微弧氧化處理后,膜層表面呈現多孔形態,膜層表現出“火山狀”的微孔形貌特征。膜層表面多微孔的形貌特征取決于微弧氧化機制中微放電作用的本質[13],孔洞大小不一及分布不均勻是由于在微弧氧化過程中產生了比較強烈的弧光放電。這種多孔形態導致氧化膜層的最外層晶粒稍粗大,組織比較疏松。
圖1 高溫氧化前后的微弧氧化膜層微觀形貌
經微弧氧化和高溫氧化處理后的2#試樣與微弧氧化后的1#試樣相比,表面形貌沒有發生明顯改變,焙燒后的形貌相對更清晰一些。且表面氧化物相互連接、覆蓋和重熔,孔洞分布著塊狀的氧化物,膜層較為致密。但在膜層表面產生了開裂,且開裂位置多經過微弧氧化膜表面的微孔缺陷處。這主要是由于在熱處理過程中,微弧氧化膜與基體的熱膨脹系數不同導致的[14],在高溫氧化過程中產生的熱應力作用下,不斷形成位錯,位錯遇到膜層表面微孔缺陷受阻,隨著位錯不斷的積累,在表面微孔缺陷處形成裂紋源,當熱應力聚集達到一定程度時,微弧氧化膜層產生開裂[15]。
2.2 表面處理工藝對微弧氧化膜層硅烷化封孔效果的影響
經過微弧氧化處理以及微弧氧化+高溫氧化處理后的試樣均經3次硅烷化處理的3#和4#試樣的表面微觀形貌如圖2所示。由圖2可知,表面經微弧氧化處理后直接進行硅烷化處理的3#試樣,微弧氧化膜的表面存在一層灰色的膜,微孔缺陷得到一定程度的封閉;這是由于TC4鈦合金表面氧化物顆粒的疏松結構,為硅烷水解溶液向內部沉積提供了有利通道。但由于沉積的硅烷膜較薄且分布不均,微弧氧化膜的表面仍然存在一定的微孔缺陷。而微弧氧化+高溫氧化處理后再經硅烷化處理后的4#試樣,微弧氧化膜層的表面獲得一層厚且較為均勻的灰色膜,不存在微孔缺陷。經微弧氧化+大氣高溫氧化處理后的微弧氧化膜層,在微弧氧化膜層的多孔結構以及界面處氧化物顆粒的疏松結構[16]的共同作用下,使得微弧氧化膜層經硅烷化處理后在表面獲得更厚、更均勻的硅烷沉積膜。
圖2 高溫氧化前后微弧氧化膜層封孔后微觀形貌
通過以上對比可知,高溫氧化處理對微弧氧化膜層的后續硅烷化封孔產生了積極的作用,使微弧氧化膜層表面沉積了一層較厚的硅烷膜,全部封閉了微弧氧化膜層的微孔。
2.3 表面處理工藝對微弧氧化膜層電偶電流的影響
經過不同表面處理后的TC4鈦合金與925鋼耦合后測定其電偶電流。表面未經處理的TC4鈦合金試樣與925鋼耦合后,平均腐蝕電流密度為1.27 μA/cm2,電偶腐蝕敏感性為C級,屬于不允許接觸使用。
將TC4鈦合金表面經微弧氧化處理后再與925鋼耦合時,使電偶腐蝕電流從1.27 μA/cm2降到0.19 μA/cm2,其電偶腐蝕敏感性從C級降低到A級,抗電偶腐蝕性優良,按標準屬于可以使用范圍。進一步將經微弧氧化后的TC4鈦合金經硅烷化封孔處理后,其電偶電流密度僅降低到0.18 μA/cm2,說明進一步的封孔處理對降低電偶腐蝕的作用較小。而將經微弧氧化后的TC4鈦合金先經過高溫氧化處理后再進行硅烷化封孔處理,與925鋼耦合后其平均電偶電流降低至0.04 μA/cm2,較微弧氧化及微弧氧化+硅烷化封孔處理的試樣降低了一個數量級、較未經表面處理的試樣降低了兩個數量級,說明微弧氧化+高溫氧化+硅烷化封孔處理后在表面形成的更厚、更均勻的硅烷沉積膜能顯著降低平均電偶電流密度,顯著地提高了鈦合金抗腐蝕性能。
TC4鈦合金-925鋼的電偶電流-時間曲線如圖3所示。未經微弧氧化處理的TC4鈦合金與925鋼接觸后,隨著時間的延長,電偶電流逐漸下降,約50000 s后趨于穩定;經表面處理后的TC4鈦合金,在接觸后較短時間內,電偶電流迅速下降并趨于穩定。其中,微弧氧化后進行高溫氧化并硅烷化封孔的試樣,在與925鋼接觸后,約2000 s后電偶電流趨于穩定,用時最短。產生這種現象的原因在于,鈦合金微弧氧化后在表面有一層穩定性好的氧化膜,可以有效降低電偶電流;微弧氧化后進行硅烷化封孔處理使表面微弧氧化膜層的一些孔洞被較薄的硅烷膜覆蓋,進一步降低了電偶電流;微弧氧化后進行高溫氧化并硅烷化封孔處理后,表面由于有較厚、較均勻的硅烷沉積膜的阻擋作用,大幅度降低了電偶電流。
圖3 不同處理工藝條件下TC4鈦合金-鋼電偶電流-時間曲線
3 結論
(1) 高溫氧化未使微弧氧化膜層表面形貌發生明顯改變,但對微弧氧化膜層的后續硅烷化封孔處理產生積極的影響,能將微弧氧化膜層中的孔洞及微裂紋全部封閉。
(2) 對TC4鈦合金表面進行處理能降低TC4鈦合金和925鋼耦合時的電偶電流密度,可以大幅度降低TC4鈦合金和925鋼接觸腐蝕的敏感性。為避免TC4鈦合金和925鋼在腐蝕介質下發生電偶腐蝕,微弧氧化+高溫氧化+硅烷化封孔處理是有效的防護措施。
參考文獻
1 Xie N S, Wu L Z. Effect factor and its application of micro-arc oxidation technique on titanium alloy surface [J]. Hot Work. Technol., 2011, 40: 130
1 解念鎖, 武立志. 鈦合金表面微弧氧化的影響因素及其應用 [J]. 熱加工工藝, 2011, 40(12): 130
2 Jin H X, Wei K X, Li J M, et al. Research development of titanium alloy in aerospace industry [J]. Chin. J. Nonferrous Met., 2015, 25: 280
2 金和喜, 魏克湘, 李建明等. 航空用鈦合金研究進展 [J]. 中國有色金屬學報, 2015, 25: 280
3 Yerokhin A L, Leyland A, Matthews A. Kinetic aspects of aluminium titanate layer formation on titanium alloys by plasma electrolytic oxidation [J]. Appl. Surf. Sci., 2002, 200: 172
4 Xin X J, Xue J F. Corrosion, Protection and Engineering Application of Titanium [M]. Hefei: Anhui Science and Technology Press, 1988: 65
4 辛湘杰, 薛峻峰. 鈦的腐蝕、防護及工程應用 [M]. 合肥: 安徽科學技術出版社, 1988: 65
5 Tu Z M, Li N, Zhu Y M. Application and Technology on Surface Treatment of Titanium and Titanium Alloys [M]. Beijing: National Defense Industry Press, 2010: 127
5 屠振密, 李寧, 朱永明. 鈦及鈦合金表面處理技術和應用 [M]. 北京: 國防工業出版社, 2010: 127
6 Wang Q L, Xu L L, Ge S R. Investigation on structure of microarc oxidation ceramic layer on titanium alloy [J]. China Surf. Eng., 2007, 20(5): 11
6 王慶良, 徐伶俐, 葛世榮. 鈦合金微弧氧化陶瓷層的結構研究 [J]. 中國表面工程, 2007, 20(5): 11
7 Shi S R. Study on sealing treatments of micro arc oxidation coatings on Al alloy 6061 [D]. Harbin: Harbin Engineering University, 2013
7 石世瑞. 6061鋁合金微弧氧化涂層封孔處理技術研究 [D]. 哈爾濱: 哈爾濱工程大學, 2013
8 Wang C J, Jiang B L, Liu M, et al. Corrosion characterization of micro-arc oxidization composite electrophoretic coating on AZ31B magnesium alloy [J]. J. Alloy. Compd., 2015, 621: 53
9 Cui X J, Yang R S, Liu C H, et al. Structure and corrosion resistance of modified micro-arc oxidation coating on AZ31B magnesium alloy [J]. Trans. Nonferrous Met. Soc. China, 2016, 26: 814
10 Wang P, Wu T, Peng H, et al. Effect of NaAlO2 concentrations on the properties of micro-arc oxidization coatings on pure titanium [J]. Mater. Lett., 2016, 170: 171
11 Xia S J, Yue R, Rateick Jr R G, et al. Electrochemical studies of AC/DC anodized Mg alloy in NaCl solution [J]. J. Electrochem. Soc., 2004, 151: B179
12 Duan H P, Du K Q, Yan C W, et al. Electrochemical corrosion behavior of composite coatings of sealed MAO film on magnesium alloy AZ91D [J]. Electrochim. Acta, 2006, 51: 2898
13 Rudnev V S, Lukiyanchuk I V, Kon'shin V V, et al. Anodic-spark deposition of P- and W (Mo)-containing coatings onto aluminum and titanium alloys [J]. Russ. J. Appl. Chem., 2002, 75: 1082
14 Luo Z Z. Study on silanization of anodized film on Al alloy [D]. Harbin: Harbin Engineering University, 2016: 34
14 羅兆柱. 鋁合金陽極氧化膜硅烷改性的研究 [D]. 哈爾濱: 哈爾濱工程大學, 2016: 34
15 Evans H E, Lobb R C. Conditions for the initiation of oxide-scale cracking and spallation [J]. Corros. Sci., 1984, 24: 209
16 Xiang W Y, Jiang H T, Tian S W. High temperature oxidation behavior of titanium and titanium alloys [J]. Metallic Funct. Mater., 2020, 27(3): 33
16 向午淵, 江海濤, 田世偉. 鈦及鈦合金高溫氧化行為研究 [J]. 金屬功能材料, 2020, 27(3): 33
免責聲明:本網站所轉載的文字、圖片與視頻資料版權歸原創作者所有,如果涉及侵權,請第一時間聯系本網刪除。
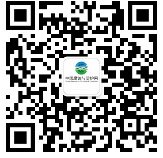
官方微信
《中國腐蝕與防護網電子期刊》征訂啟事
- 投稿聯系:編輯部
- 電話:010-62316606-806
- 郵箱:fsfhzy666@163.com
- 中國腐蝕與防護網官方QQ群:140808414