為配合GB/T20801-2020《壓力管道規范 工業管道》實施,主編應道宴老師在耄耋之年,寫了數篇文章,對實施過程中的重大疑難問題進行解讀。壓力管道人已經介紹了回顧與展望,壓力設備中介質危險性分類的跨世紀之爭!,關于工業管道標準與安全技術規程一系列問題最權威的解答!且看應道宴先生第一篇文章! 等3篇,本文與碳鋼管材使用過程中的眾多疑難問題解讀!應道宴老師GB20801-2020第3篇相關文章來了!為姊妹篇,考慮到GB/T20801-2020版不會再像2006版一樣出版實施指南,更為彌足珍貴,展示了一位老專家對行業技術進步的熱忱與期待。經與應老師溝通,獲得許可全文首發。本文行文為二簡字(讀者可自行搜相關歷史背景),不再一一轉化。
關于GB9711
GB/T9711—2017石油天然氣工業管綫輸送系統用鋼管(ISO 3183-2012,MOD)實際上是API 5L—2012 45th的中國版。“管綫用管”從名稱上看似乎是長輸管道專用的碳鋼鋼管,實際上在工業管道領域中有著廣泛的用途。二十余年前,筆者就在某大型乙烯裝置的合作設計中初次接觸到國外工程公司采用API 5L Gr.B(旡縫管和DSAW板焊管)替代了原設計的ASME A106 Gr.B和A671 CC60。隨著西氣東輸工程的開展,GB/T 9711管綫鋼管的生產和應用也越來越廣泛的進入壓力管道的各亇領域,對提高國內壓力管道用鋼管的質量、管理和設計選用、采購水平起到了巨大的推動作用。近十年來,筆者在多亇場合都講過:GB/T 9711是一本壓力管道用碳鋼鋼管的百科全書,它不但包括了各種鋼管的生產工藝,提供了從低強度到高強度碳鋼鋼管的多種質量等級,還示范、教育了壓力管道的業主和管道材料設計,施工人員,如何根據具體環境及工況條件,做好設計選材及采購工作。
GB/T 9711的內容十分繁雜,結合工業管道領域內的應用,筆者認為應從下列三亇方面來解讀:
(1)首先,管綫鋼管不僅包括了從X42(L290)~X120(L830)眾多高屈強比的高強度碳鋼,還包括了眾多工業管道及長輸管道工程中,輔助管道用的屈服強度僅為175、210、245MPa,其PSL2高于GB/T699優質碳素鋼08、10、20, 其PSL 1相當于GB/T700普通碳素結構鋼的Q195、Q215、Q235等低強度碳鋼。本文表8~表12中僅列入了GB/T 9711中L245、L390(X56)、L485(X70)三亇強度級別的牌號,其中L245的強度等級對應于工業管道中最常用的20號鋼; L390(X56)的抗拉強度490MPa相當于工業管道中大口徑板焊管及鍛件常用的16Mn和Q345; 而L485(X70)的屈服強度與壓力容器球罐用的低裂紋傾向的CF62鋼板基本一致。
(2)管道材料設計者應注意,GB/T 9711和GB/T21237-2018管線鋼管用寬厚鋼板包括了PSL1,PSL2,兩亇質量等級。其實除了標準正文中的兩亇質量等級外,在GB/T 9711-2017的附錄中還設置了多亇質量等級供用戶選用。如附錄G“抗延性斷裂擴展用的PSL2鋼管”要求的低溫沖擊韌性,比常規的PSL2,提高了接近一倍。GB/T 21237管線管用寬厚鋼板實際上就是按照附錄G的要求制訂抗延性斷裂擴展用,更高低溫沖擊韌性要求的大口徑板焊管用鋼板標準,相當于PSL3。又如附錄H“酸性服役條件PSL2鋼管的訂購”規定了抗濕硫化氫應力腐蝕破裂用碳鋼的化學成份,如含硫量和夾雜物形狀控制要求、硬度試驗、HIC試驗、SSC試驗以及相應的旡損檢驗和表面缺陷控制要求,均比常規的PSL2有大幅度的提高,相當于PSL4。
(3)用戶必須注意GB/T 9711中包含了多達十余種的碳鋼鋼管制管工藝,本文中僅就高頻電阻焊焊管、無縫管、雙面直縫埋弧焊板焊管三種制管工藝進行分析。關于螺旋焊焊管,由于工業管道領域缺少使用經驗,為此本文未列入分析闡述。
GB9711技術要求及質量控制指標
如前所述,由于GB/T 9711包含的鋼級、質量等級、制管方式十分繁雜,GB/T 9711-2017標準的編寫又沿用了ASME規范相互穿插引用,適用于鋼管生產者角度的美式標準編制方式。為此,筆者試圖從標準選用者的視角出發,用表格的形式,將用戶選用時關心的各項技術指標和質量控制要求,分別用列表、對比並列的方式列出,便于用戶有一亇清晰,全面的認識。
1. 化學成分,碳當量
表8所示為GB/T 9711-2017管綫鋼管和專用于管綫鋼DSAW板焊管的GB/T 21237-2018管線管用寬厚鋼板的化學成分,碳當量要求一覽表。從表8及其四亇注解中提供了許多有助于國內壓力管道行業認識和使用碳鋼鋼管標準的新摡念。
(1) GB/T 9711-2017管綫鋼管是典型的ASME/ASTM/API鋼級標準,而GB/T8163、5310等是國內傳統的鋼號標準。從表8和注1可見,GB/T 9711的化學成分范圍相比國內同等強度級別的碳鋼要寬得多,幾乎所有的化學組分均旡下限,鋼管制造商是根據用戶的產品規格、性能要求和鋼廠內控的專有程序來確定熔煉成分和軋制工藝的。而國內其他壓力管道用鋼管制造商並不需要內控標準,因為標準規定的化學成分上下限平均值以及雜質限量的50~30%基本上就是鋼廠的內控熔煉成分。
(2) GB/T 9711-2017管綫鋼管編制的直接目的是為用戶服務,供用戶選用;而GB/T8163、5310編制的直接目的是為鋼管制造商生產及質量控制服務,間接的用途才是供用戶選用。標準中除各種鋼級外,考慮到用戶的規格和性能的不同需求,標準中設置了各種質量等級和附錄的組合,就反映了用戶的不同需求。因此用戶在使用GB/T 9711時,需改變習慣使用GB/T8163、5310的習慣(僅注明鋼號及標準號), 除鋼級外,必須注明相應的質量等級號、制管形式(ERW、無縫、SAW)及相應交貨狀態標記和沖擊試驗溫度等附加要求。
(3)API5L等ASME/ASTM/API壓力設備用碳鋼標準通過表8注1的降碳升錳的措施有效地解決了美歐(中)之間關于高強度鋼和低溫用碳鋼的錳碳比、屈強比、可焊性(碳當量CE)的不同理念,給鋼廠和用戶提供了更大的選擇空間。
(4)突出了鈮、釩、鈦的微合金化對析出強化、細化晶粒、提高再結晶溫度(為控制軋制創造條件)、防止焊接過熱區晶粒長大的作用。標準一方面對鈮、釩、鈦含量及總量都只控制上限而且較低, 同時又不規定下限, 從L245到X80的鈮、釩、鈦成分限制基本一樣,為鋼廠內控專利技術留出很大空間。
(5)強度級別越高,鋼管的質量等級越高,管綫鋼的含碳量反而越低,顛覆了傳統發展高強度碳鋼的思路。這表明隨著管綫鋼的開發及其實踐應用走出了一條新路徑,筆者總結為下列幾點:
① 本文第三節 “碳鋼的低溫韌性”中已列出的純淨化,細晶粒,熱處理,錳碳比;
②微合金化,其含量都比傳統的低合金高強度鋼的鈮釩鈦的含量低了一亇數量級。含量雖然低,但其作用卻不容小覷。
③“控軋控冷”(在標準中稱為熱機械軋制)
管綫鋼管最大的亮點是焊管。焊管用的寬厚鋼板與鋼帶通常就在上述微合金化和細晶鎮靜鋼的基礎上,采用適當降低終軋溫度和/或兩相區軋制的控軋工藝,並輔以軋后控制冷卻的控軋控冷工藝, 進一步獲得針狀鐵素體或超低碳貝茵體組織、細化晶粒、提高屈服強度及韌性,省卻調質熱處理,降低成本。
④ 隨著上述效果的顯現,鋼的可焊性反而可在強度提高的同時卻不斷改善,而且修正了含碳量低于0.12條件下的碳當量公式,見表8注3所示。其中鈦、鈮的微合金釘扎作用,為大線能量埋弧自動焊的防止過熱區晶粒長大起到了關鍵作用。
(6)大量的研究和實踐表明,板材生產中的硫化錳片狀夾雜物是濕硫化氫酸性環境下產生HIC的根源所在,因此表8中專門列出了相應條件下的0.002%低硫要求,除此以外,通過加鈣控制硫化錳的形態也是另一個選項,為此表8注4也列入了相應規定。必須說明,HIC是板材在濕硫化氫酸性環境下所特有的腐蝕裂紋方式,其相應的低硫及HIC試驗要求,僅適用于鋼板(帶)及其焊管,而不應套用到旡縫鋼管、焊接材料、焊縫以及鑄鍛件。
表8. GB/T 9711-2017管綫鋼管和GB/T21237-2018管線管用寬厚鋼板化學成分,碳當量
注1.表8所列化學成分為熔煉分析和產品分析,其中有關碳、錳上限的規定分列二行,其下行的規定均遵循: 碳含量比規定最大碳含量每減少0.01% , 則允許錳含量比規定最大錳含量增加0.05% , 對于鋼級≥L245/B 但≤L360/X52 的鋼級, 最大錳含量為1.65%; 對于鋼級>L360 或 X52 但<L485 或 X70 的鋼級, 最大錳含量為 1.75% ; 對于鋼級 L485/X70 的鋼級, 最大錳含量為2.00% 。但對于GB/T9711附錄H酸性服役條件者,則錳含量比規定最大錳含量只允許增加0.20%。
注2.表8所列各鋼級的殘余元素含量的規定如下:
L245N/BN,PSL2, Cu≤0.50% ,Ni≤0.30% ,Cr≤0.30% , Mo≤0.15% 。
L390M/X56M,PSL2, Cu≤0.50% ,Ni≤0.50% ,Cr≤0.50% , Mo≤0.50% 。
L485M/X70M,PSL2, Cu≤0.50% ,Ni≤1.00%,Cr≤0.50% , Mo≤0.50% 。
注3.表8所列各鋼級(質量等級PSL2)均規定了碳當量的限制條件:
碳含量大于 0.12% 使用CEIIW , 碳含量小于等于0.12% 使用 CEpcm 。
CEIIW=C + Mn/6 + (Cr + Mo + V)/5 + (Ni+Cu)/15
CEPcm=C + Si/30 + Mn/20 + Cu/20 +Ni/60 +Cr/20 + Mo/15 +V/10 +5B
注4用于PSL2+附錄H酸性服役的管綫鋼的化學成分還應符合下列要求:
① A.ltotal ≤0.060%;N≤0.012% ;Al/N≥2:1(不適用鈦鎮靜鋼或鈦處理鋼) ;Cu≤0.35% ( 如果協議,Cu≤0.10%) ;Ni≤0.30% ;Cr≤0.30% ; Mo≤0.15% ;B≤0.0005% 。
② 在焊管有意 增 加 鈣 含 量 情 況 下, 除 另 有 協 議 外, 如果 S>0.001 5% 則 Ca/S≥1.5。SMLS 管 和 焊 管 Ca ≤0.006% 。
③ SMLS 管的最大硫含量可增至0.008% , 而且如果協議焊管可增至0.006% 。對于這些硫含量水平較高的焊管,可協議確定較低的 Ca/S。
2管綫鋼管的交貨狀態(熱處理)和焊后處理
配管材料設計者初次使用管線鋼管標準時都要被GB/T 9711表1及表3中的鋼管交貨狀態及其標記字母搞得眼花繚亂,不知所措。結合國內實際生產和使用情況,筆者總結了下列幾點建議,供使用者參考。
(1)鋼管的交貨狀態可歸納為無縫鋼管,焊管用板或帶卷以及焊后處理三類.
(2)GB/T 9711表1和表3中的交貨狀態品種繁多,而且出現了許多非傳統的熱處理狀態名詞,其實還是可歸納為∶熱軋(R),正火(N),控軋控冷(M, 熱機械軋制)和調質(Q, 淬火加回火)四種。在四種熱處理工藝中唯一的新工藝就是M--俗稱:控軋控冷,又稱熱機械軋制。
所謂“控軋”就是控制鋼板或鋼管的熱軋溫度、終軋溫度以及在軋制溫度范圍內的變形率,所謂“控冷”就是控制軋后的冷卻速度。因此控軋控冷不但要精心確定化學成份、坯料的加熱溫度、初軋溫度、終軋溫度以及在相應軋制溫度區域內的變形量以及軋后的冷卻速度,還必須具有嚴格並行之有效的質量管理制度,否則控軋控冷將成為一紙空文和營銷的噱頭。
通過微合金碳化物在奧氏體冷卻中沉淀析出強化、阻止晶粒長大(本質晶粒)、適當降低終軋溫度 (1050~1000℃)致使軋制過程中抑止形變奧氏體回復和再結晶進行、阻止再結晶晶粒長大、細化奧氏體相變晶粒 ,繼而進行低溫軋制或兩相區軋制以及快速冷卻,合金碳、氮化合物析出,形成晶粒度細于8級的鐵素體細晶粒。據文獻介紹,晶粒度由6級細化到10級,鋼的韌脆轉變溫度下降54 ℃、屈服強度提高85MPa;如晶粒度由6級細化到11級,鋼的韌脆轉變溫度下降74 ℃、屈服強度提高115MPa;
為了提高屈強比, 提高韌性,管綫鋼一般通過降碳升錳,防止珠光體形成,
X42~X56 標準規定 C≤0.24 實際控制C ≈0.12, 晶粒度≥7~8級;
X60~X65 標準規定 C≤0.12 實際控制C ≈0.09, 晶粒度≥7~9級;
X70~X80 標準規定 C≤0.12 實際控制C ≈0.06, 晶粒度≥7~10級。
控軋控冷用于板、帶生產稱為熱機械軋制;這也是DN400以上大口徑長輸管道和工業管道采用GB/T9711高屈強比鋼級DSAW鋼管的最大的亮點。因為板帶之類扁平鋼材的生產流程相比于管棒之類細長及中空鋼材更易達到控軋控冷的效果。
控軋控冷用于無縫鋼管在標準中稱為熱機械成型,此種工藝適用于少規格大批量的高鋼級DN600以下鋼管生產,估計在工業管道領域內的需求難以符合批量要求,而常用調質(Q)替代。
通過鋼管或鋼板控制終軋溫度在鋼材的正火溫度范圍,並軋后空冷,達到相當于正火的效果,在標準中又稱為正火軋制(板)或正火成型(無縫管)。此時,“控軋”又歸入正火(N)范疇。
(3) 焊后處理
管綫鋼管的用戶必須注意,在GB/T 9711的領域內,旡輪是一般可焊低碳鋼L245以及高屈強比管線鋼的焊接鋼管(厚度通常不大于25mm),包括高頻電阻焊和埋弧焊,焊接后是不作傳統意義上的焊后熱處理的。電阻焊焊縫僅是通過在線的焊縫區域局部加熱以消除淬硬組織(馬氏體)。而埋弧焊焊管則通過冷擴徑以達到定徑及消除部分焊接應力的雙重目的,見本文表9所示。同時還應注意到按GB/T 9711生產的鋼管,水壓試驗是必不可少的檢驗項目(不允許用無損檢測來替代水壓試驗),而且采用較高的試驗壓力,以驗證鋼管的整體完整性,部分降低焊接殘余應力並降低脆性斷裂風險, 見本文表10所示。
(4) GB/T 97116.2.1條規定:PSL1 鋼管的交貨狀態應由制造商選擇。因此鋼管制造廠除了X65以上的高鋼級鋼板可能采用熱機械軋制工藝(M)外,通常都是熱軋狀態交貨(R)。而高鋼級采用PSL 1的低質量等級, 本身就是一個悖論。而一般L245和L390(X56)的PSL 1鋼管,無輪是ERW鋼管、旡縫管還是直縫埋弧焊焊管, 與工業管道內常用的GB/T 3091的ERW鋼管,SAW鋼管以及GB/T 8163無縫管的技術要求和質量等級高度重合。因此,工業管道領域內選用GB/T9711 PSL 1鋼管的必要性與可能性不大。
(5) 綜上所述,工業管道領域內使用的主要集中在PSL 2。因此,
以L245為例 : 無縫管及焊管用板帶推薦正火態(N);
L 390(X56):正火N(旡縫管),控軋M(板帶,焊管):
L 485(X70):調質Q(無縫管):控軋M(板帶,焊管)。
表9 管綫鋼管、鋼板的交貨狀態(熱處理),晶粒度要求
注:用于PSL2 DSAW管的GB/T 21237-2018管綫鋼管用鋼板的A、B、C、D型粗系和細系非金屬夾雜物,按GB/T10561方法A,應不大于2.5級(輸油), 2級(輸氣);帶狀組織不大于3級(按GB/T 13299)。
表10 管綫鋼管水壓試驗要求
3. 管綫鋼管的質量等級
除本文表8所示的化學成分、碳當量以及表9所示的交貨狀態和晶粒度要求的差別外,從本文表11~表13可見,PSL 2鋼管在機械性能的穩定性,抗脆斷能力以及旡損檢驗要求等壓力設備用鋼最關心的材料性能的可靠性方面均有大幅度提高。因此,在GBT 9711管線鋼管各鋼級的適用溫度范圍內,PSL 2可符合工業管道GC1級碳鋼管道的要求。
4. 工業管道規范中管綫鋼管的適用溫度范圍
關于管線鋼管各鋼級的適用溫度范圍問題,筆者在編寫GB/T 20801.2-2020中的觀點是:
(1) L245及X42~X80的溫度下限,按照長輸管道行業的埋地地溫的需求限于-30℃,但由于其考慮防止脆性斷裂擴展的止裂需求,因此長輸管道行業的抗脆斷判據高于工業管道領域內的防脆斷判據。因此有可能進一步降至-46℃,但目前尚有待于工程實踐和試制證實。
(2) L245的使用溫度上限同20號鋼,而高屈強比管綫鋼在GB/T 20801-2020工業管道中使用溫度上限限于200的理由如下:
① 通過控軋控冷獲得高屈強比的管綫鋼,在300℃以上溫度,長期使用的低溫回火效應將使材料在快速控冷條件下獲得的高屈強比大幅度下降,因此不宜用于較高溫度。這個道理類同于調質高強鋼的使用溫度上限必須低于其回火溫度50~100℃以上。
② 其次,長輸管道領域內沒有高于200℃的需求,因些國際上未開展材料中溫機性的測試和統計研究工作。
③ 由于工業管道的碳鋼許用應力設計安全系數,按常溫抗拉強度三分之一確定,因此高屈強比鋼級的常溫許用應力足以維持到200℃。所以,ASME B31.3和GB/T 20801工業管道規范高屈強比鋼級的使用溫度上限暫定于200℃。
表11. GB/T9711-2017管綫鋼管、GB/T21237-2018鋼板機械性能
表12. PSL 2管綫鋼管、鋼板的沖擊軔性要求
注1.AKV試驗溫度為0 ℃(GB/T 9711)或-20℃ (GB/T 21237),用戶還可采用更低試驗溫度,如-30℃或更低, 但應在采購合同中提出並予規定。DWT落錘撕裂試驗按API RP5L3管綫鋼管落錘撕裂試驗方法。
注2.AKV單個試驗值不應小于規定最小平均(同一組的三個試樣) 吸收能的75%。
注3.同時具有足夠的 CVN 吸收能和剪切面積和是管體的一個基本特性, 該剪切面積足以保證在試驗溫度或高于試驗溫度時, 輸氣管線能避免脆性斷裂擴展, 并控制延性斷裂的擴展時有足夠延性斷口。
表13 管綫鋼管、鋼板的NDT要求
注: L12.5、L10、L5 分別表示對比試樣刻槽深度相對于厚度的百分比。
制造工藝
1. 高頻電阻焊焊管
高頻電阻焊焊管是帶鋼在焊管機組,經多道軋輥滾壓冷成型逐漸卷起,形成有開口間隙的圓形管坯,調整擠壓輥的壓下量,使焊縫間隙控制在1至3mm,并使焊口兩端齊平。利用50KHz~400KHz的高頻交流電的趨膚效應和鄰近效應,在管坯開口邊緣處形成一個電磁感應回路,產生強大而集中的熱效應,在很短的時間內使焊縫邊緣迅速加熱到焊接所需溫度, 經壓輥擠壓后,熔融狀態的金屬實現晶間壓接接合,快速冷卻后形成一條牢固的對接焊縫。因此, 帶卷的分條質量、同板差、軋輥機組的運行精度都對焊縫間隙及錯邊量產生很大影響。如間隙過大,則造成鄰近效應減少,渦流熱量不足,焊縫晶間接合不良而產生未熔合或開裂。如間隙過小則造成鄰近效應增大,焊接熱量過大,造成焊縫燒損或者焊縫經擠壓、滾壓后形成深坑,影響焊縫質量。
高頻直縫焊管的焊接速度可達數十米至一百余米/分。因此焊接電流、電壓及機組運行速度將直接影響到焊接質量的穩定性。ERW焊接為壓接方式,而不是熔融焊接,冷卻速度很快, 焊接熱影響區相對較小。焊縫的淬硬強度和韌性與母材不同。熔融金屬擠壓形成的內側焊接毛刺缺口效應及焊縫的淬硬組織是高頻直縫焊管質量可靠性的最大隱患。
因此,雖然GB/T 9711 ERW管在焊縫熱處理、母材質量等級以及焊縫旡損檢驗要求上,較GB/T 3091 Q235 ERW管有較大提高,但仍然難以完全消除筆者對電阻焊焊管質量穩定性以及內側焊道缺口效應的擔憂。為此,參照長輸管道行業的設計潛規,把GB/T 9711 PSL 1 ERW管的適用壓力放寬到4.0MPa;而GB/T 9711 PSL 2 ERW管,限制用于輸油之類液體管道。
由于工業管道規范對電阻焊規定了縱縫焊接質量系數,即使提高了無損檢測要求也不得大于0.85的規定,因此也限制了電阻焊焊管在劇烈循環工況和GC 1管道的使用。此外尚需提醒用戶的是,由于電阻焊焊管生產效率高,成本低,行業門檻低,采購時應對焊管廠能否嚴格執行管綫鋼管的質量管理模式進行考察和認證,以杜絕魚目混珠,假冒偽劣。
2.無縫鋼管
無縫鋼管是工業管道常用的制管型式。如前所述,GB/T 9711 PSL 1各種鋼級無縫鋼管的質量等級基本上處于GB/T 8163相同的水平。而GB/T 9711 PSL2各鋼級無縫鋼管的成分控制、熱處理、力學性能和抗脆斷能力、無損檢測、壓力試驗等環節,均有大幅度提高。因此,GB/T 9711 PSL2無縫管在相應適用溫度范圍內,可符合GC 1級管道的要求。而且X70、X80還是按照ASMEB31.3 K類管道(超高壓管道,許用應力為屈服強度的三分之二)可焊高強度碳鋼鋼管的不二選項。根據筆者的經驗,GB/T 9711 PSL2 L245和L390相對于GB/T 6479、9948、5310的20G和Q345,有更高的性價比和經濟價值。
3. 直縫埋弧焊焊管(板焊管)
如前所述,雙面直縫埋弧焊DSAW鋼管是GB/T 9711對長輸管道及工業管道領域貢獻的最大亮點, 彌補了工業管道行業缺乏大口徑高質量焊接鋼管的缺陷。ASME/ASTM 壓力設備用大口徑直縫雙面埋弧焊鋼管 A671、A672、A691的技術特征,筆者總結于下:
①容器級鋼板;②板厚負偏差0.3mm;③DN400以上直縫雙面電熔焊;④Class 22和Class21要求焊縫100% XT(UT);⑤Class 22和Class21要求焊后熱處理;⑥Class22鋼管應經水壓試驗,水壓試驗壓力為 60-50%屈服強度,但不大于19.0MPa。
GB/T 9711 PSL 2 DSAW管與ASME/ASTMA671的差別主要在于板厚負偏差及焊后熱處理方面。但這兩項差別並不影響管線鋼DSAW鋼管的質量等級。其中焊后熱處理一項, 由于GB/T 9711 PSL 2 DSAW管的壁厚不大于25mm、板材的微合金化減除了過熱區晶粒粗大的隱患、且輔以冷擴徑和水壓試驗對部分消除焊接應力的作用,因此綜合效果可等同于ASME/ASTM A671的焊后熱處理。至于板厚負偏差一項, 僅僅是A671提供給用戶和設計者的心靈雞湯, 因為板焊管的理論重量是按板厚正負偏差的中間值計算 ,而不是按名義厚度計算的, 因此在板厚正負偏差帶不變的前提下,無論負偏差大小, 用戶是沾不到任何便宜的。由此可知, GB/T 20801.2-2020對板焊管的各項要求,都是以GB/T 9711 PSL 2 DSAW管為模板編制的。
4. 對GB/T 37577-2019之我見
近日獲悉GB/T 37577-2019“低溫管道用大口徑焊接鋼管”批準並頒布實施。但筆者閱讀后大失所望。因為該標準中下列各項背離了低溫大口徑焊接鋼管的基本要求和材料焊接接頭目前可能達到的抗脆斷能力,對設計選用者產生許多誤導作用。
①“外徑114.3mm以上”?
筆者的觀點:外徑114.3mm直縫雙面焊,不可能﹗螺旋焊管,不允許!
②“焊管制造方式采用HFW或EFW”?
筆者的觀點: HFW,不允許! 螺旋焊管,不允許!單面焊EFW或單面焊雙面成型,不允許!
③ “厚度不大于75mm” ?
筆者的觀點: 75mm低溫管道尚無可預見需求,更何況在標準所示GB/T 3531的牌號中尚無30mm以上厚板大線能量自動或半自動電熔焊可達到母材抗脆斷能力的成熟焊接工藝;
④“標準推薦的焊后熱處理制度及其免除”
筆者的觀點: 為改善近縫區的抗脆斷能力恐怕不是傳統的回火制度所能勝任的。即使是表列的傳統回火制度亦需對保溫溫度及冷卻速度進行調整。否則對焊接熱影響區的抗脆斷能力可能是負面作用。
單面焊與雙面焊
1. 雙面焊與單面焊雙面成形
提起雙面埋弧焊,筆者不禁想起,多年來壓力設備焊接領域內盛行的:“單面焊雙面成形”或“采用氬弧焊打底”來替代並達到雙面焊效果的說法。雖說在焊接工藝評定或樣品或見證件,亦有可能顯示效果,但據筆者的經驗,除非采用設置可熔化墊環的單面焊工藝(ASME/AWS規范中經常提及,但該工藝國內從未采用),否則上述可達到雙面焊效果的單面焊工藝,在實際產品焊接中卻淪為自欺欺人或廠商的營銷噱頭。因此,筆者認為,所謂“雙面焊”必須在內外兩側均應有施焊焊道,至少應在內側采用不添加填充金屬的氣體保護焊蓋面掃一道,才能達到並符合“雙面焊”的效果。
2. 管道環縫對接的坡口加工
所以,按照該觀點,管道施工現場的環縫對接一方面只能外側單面施焊, 更何況管道環縫對接還存在著管端不圓度和壁厚偏差而導致的錯邊現象, 所以極難達到雙面焊要求。為了減少由此而加劇的環縫焊接質量問題,德國DIN 2559提供了一個很好的案例。即將鋼管對接兩端的內側,在管端坡口加工時, 預先都機加工到下式及圖4所示管端內孔機加工孔徑dp
dp=dO min – 2 tmin
式中:
dp 內孔機加工孔徑;
dOmin 鋼管最小外徑,即鋼管名義外徑扣除標準規定的最大外徑負偏差;兩側鋼管外徑負偏差不同時,取較大值; 對閥門、法蘭之類鑄鍛管道元件的對焊管端為機加工件者,取外徑負偏差為0;
tmin 鋼管最小壁厚,即鋼管名義厚度扣除標準規定的最大厚度負偏差;兩側鋼管厚度負偏差不同時,取較大值; 對閥門、法蘭之類鑄鍛管道元件的對焊管端為機加工件者, 取厚度負偏差為0。
圖4 管端內孔機加工孔徑dp
3. 高強度管線管帶來的不同鋼級的環縫對接問題
采用高強度管線管的管道系統中經常會遭遇不同強度等級的管道元件對焊連接問題。ASME B31.8“輸氣管道規范”、MSS SP44“大直徑管線法蘭”中對此作出了如下規定:
(1)對接接頭的最大允許厚度差: 大端厚度TD不大于小端厚度T的50%,即TD≯150% T。
如環縫外側齊平,內側錯邊時就采用圖5a所示結構,較厚側內壁削邊過渡, 削邊斜度不大于300,但也不小于140;
如環縫內側齊平,外側錯邊時就采用圖5b所示結構,較厚側外壁削邊過渡, 削邊斜度不大于300 ,但也不小于140;
(2) 焊接材料及焊接工藝按強度較高側材料進行;
(3) 當兩側管道元件鋼級相差懸殊, 導致較厚側厚度TD大于較薄側厚度T的50%時,就需要采用中間強度的過渡短節。如按長輸管道規范設計的管道系統中,L245鋼管或A105(RP0.2250MPa)法蘭或對焊端閥門 與X70(RP0.2485MPa)鋼管對接就需要采用X52或F52(RP0.2360MPa)短節過渡。如: 壁厚20mm X70(RP0.2485MPA) 鋼管,先與壁厚30mm X52或F52(RP0.2360) 過渡短節連接,然后壁厚30mmX52或F52(RP0.2360) 的過渡短節 再與壁厚40mm 的A105(RP0.2250MPa) 法蘭或對焊端閥門環縫對接。
圖5.不等厚環縫的坡口加工
免責聲明:本網站所轉載的文字、圖片與視頻資料版權歸原創作者所有,如果涉及侵權,請第一時間聯系本網刪除。
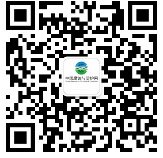
官方微信
《中國腐蝕與防護網電子期刊》征訂啟事
- 投稿聯系:編輯部
- 電話:010-62316606-806
- 郵箱:fsfhzy666@163.com
- 中國腐蝕與防護網官方QQ群:140808414