經過多年大規模滾動式開采,合水油田地層壓力虧空,無法滿足油田開采需求。為了及時彌補地層壓力,實現油田高產穩產,近年來陸續進行了注水處理,注水井占比高達29%,增產效果顯著。
然而,隨著原油含水率增加,地面生產設施腐蝕環境惡化,管線及設備頻繁出現了結垢與腐蝕問題。這不僅會導致管線或設備因腐蝕失效而停產,造成嚴重的經濟損失,更會引發油氣泄漏,造成環境污染甚至人員傷害事故。
以某采出水處理站為例,盡管站內除油沉降罐采用玻璃鋼涂層進行防護,但在服役一段時間后內壁玻璃鋼涂層發生脫落,內部布水管線腐蝕結垢嚴重,上部分水管甚至因結垢而堵塞,如下圖所示。
圖1 除油沉降罐內構件的腐蝕結垢情況
圖2 除油沉降罐內布水管線腐蝕結垢情況
由圖2可見:管線內壁靠近金屬基體表面附著了多層硬質結垢物,且和基體金屬結合緊密。清除垢層后,未在金屬基體表面發現明顯的局部腐蝕,但從管線截面環向壁厚來看,該管線環向壁厚分布不均,7點鐘位置存在明顯減薄,說明在長期服役過程中管線發生了嚴重的腐蝕減薄。這不僅縮短了設備的運行周期,還可能給設備的安全生產帶來隱患。
因此,中國石油天然氣股份有限公司長慶油田分公司第十二采油廠和安科工程技術研究院(北京)有限公司的技術人員通過一系列分析手段,對腐蝕結垢原因進行了深入剖析,并探討了有效防止或減輕水處理系統腐蝕結垢的配套措施,以期為油田正常生產提供理論支撐。
水質分析
采用瑞士萬通881離子色譜、島津UV-2600紫外可見分光光度儀及化學滴定法測試水樣中Na+、K+、Ca2+、Mg2+、Sr+、Ba2+、Fe2+等陽離子與Cl-、SO42-、HCO3-等陰離子的含量。由分析結果可知:前端處理站1和2采出水中含有較多Sr2+、Ba2+與SO42-、HCO3-,混合后Ba2+、SO42-、HCO3-含量大幅下降,說明介質混合后形成了BaSO4與BaCO3結垢物。
利用HD1000溶解氧測試儀,對水處理站內主要生產節點位置水質中的溶解氧含量進行了測試;參照標準SY/T 5329-1994《碎屑巖油藏注水水質推薦指標及分析方法》,采用細菌測試瓶,利用絕跡稀釋法進行細菌含量測試。由測試結果可知:生產介質水相中溶解氧含量為1.00~1.53mg/L,細菌含量較少,僅檢測出了9個/mL腐生菌(TGB);未檢測到硫酸鹽還原菌(SRB)與鐵細菌(IB),這可能是因為除油沉降罐中添加了殺菌劑,導致注入水及后續的產出系統中細菌含量較低。
綜上可知,來自于不同層位的生產介質混合后會發生結垢,結垢物的沉積會導致垢下腐蝕。此外,較高含量的溶解氧勢必會導致地面生產管線及設備發生氧腐蝕,存在較高的氧腐蝕風險。
腐蝕產物分析
借助X′Pert PRO粉末X射線衍射儀對布水管線中沉積的結垢物進行物相分析。由分析結果可見:除油沉降罐內主要的結垢物為BaSO4、BaCO3,還含有少量SrSO4。
利用TESCAN VEGA3掃描電子顯微鏡與配套的能譜儀對布水管線內壁腐蝕產物的微觀形貌與化學成分進行表征。由分析結果可見:布水管線內壁結垢物結構緊密,存在分層現象,主要元素為Fe、Ba、O、S,推測結垢物中主要成分為BaSO4與鐵氧化物。機械清除垢層后,管道內壁表面主要元素為Fe、O。
由此可知,布水管線內主要的堵塞物為BaSO4、BaCO3結垢物與鐵氧化物,導致除油沉降罐及內構件腐蝕的主要原因為垢下腐蝕與氧腐蝕。
腐蝕結垢原因
由上述測試可知,來自于不同前端處理站的采出水礦化度高,溶解氧含量也較高,具有較強的腐蝕性,會發生電化學腐蝕,形成FeOOH、Fe2O3、Fe3O4等鐵氧化物。
同時,由于采出水中含有成垢離子,如Ba2+、Sr2+、SO42-與HCO3-等,含不同成垢離子的采出液混合后,成垢離子相互補充,很快達到BaSO4與BaCO3的溶度積,形成過飽和溶液。
當過飽和度較高時,成垢離子對會聚集形成較大的粒子,溶液中開始出現一些不易溶解的、體積較大的BaSO4與BaCO3固體成核粒子,即所謂的晶核。所形成的BaSO4與BaCO3晶核會吸附在凹凸不平的管道表面,并以其為中心,在過飽和度的驅動下不斷長大,成為肉眼可見的晶體。
由于水處理系統是比較復雜的多相體系,含有較多的懸浮物、腐蝕產物等雜質且管道表面較粗糙,為垢的生長提供了足夠的相界面和雜質。
因此,析出的BaSO4與BaCO3會以懸浮物、腐蝕產物等為載體,快速形核,并吸附在除油沉降罐等設備內部附件表面生長。在晶核形核與吸附、長大的循環作用下,除油沉降罐等設備內部附件表面形成結垢層。結垢物一旦在金屬管線或設備表面形成,由于其疏松程度與分布情況不同,導致采出水介質在金屬表面的流動和介質擴散受到限制,造成結垢致密區域金屬表面介質化學成分與其他區域有很大差別,兩者之間形成電位差,發生微電偶腐蝕,促進局部區域腐蝕加速,形成局部腐蝕坑。
一旦局部腐蝕坑形成,受垢層掩蔽效應的影響,腐蝕坑內反應形成的Fe2+富集。為保證電位平衡,外部溶液中離子半徑較小的Cl-會通過垢層擴散至蝕坑內部,形成FeCl2。FeCl2易發生水解,形成H+,導致局部酸化,pH下降。H+的增加會促進腐蝕坑內金屬的活性溶解,加速腐蝕。腐蝕進一步會產生更多的Fe2+,導致腐蝕坑內富集更多的Fe2+,促使更多的Cl-遷入,引起pH降低,即通常所說的“酸化自催化作用”。在酸化自催化作用下,腐蝕坑會不斷發展、長大,直至管線與設備發生腐蝕穿孔。
由此可知,導致采出水處理站原油沉降罐腐蝕主要是由于具有較高結垢傾向的高礦化采出水與高濃度溶解氧的存在。
腐蝕防治措施
針對水處理系統的腐蝕問題,結合現場生產情況,可通過添加適宜的藥劑進行腐蝕防治。根據油田在用藥劑的性能評價結果,選取了SW-188阻垢劑、KEW-227緩蝕劑、HZG-30殺菌劑與Na2SO3除氧劑作為處理藥劑,通過加藥罐連續向除油沉降罐中加注藥劑,各藥劑加入量如下:140mg/L SW-188、60mg/L KEW-227、30mg/L HZG-30殺菌劑,30mg/L Na2SO3。
針對該加藥方案,在除油沉降罐內安裝掛環進行加藥效果的現場評價試驗,試驗周期30天。
(a)加藥前 (b)加藥后
圖5 加藥前后試樣的宏觀腐蝕形貌
由圖5可見:加藥前,試樣表面大部分區域附著有結垢物,內外表面均有連片大腐蝕坑、腐蝕嚴重,均勻腐蝕速率為1.01mm/a;加藥后掛環試樣表面結垢物減少,腐蝕坑面積減少,均勻腐蝕速率大幅降低,降至0.15mm/a。
由此可知,通過連續加藥,可有效控制除油沉降罐內構件及后續水處理設備、工藝管線的腐蝕結垢進程,從而降低水處理系統因腐蝕結垢導致的停產、維修頻次,保障油氣生產的安全、穩定運行。
結論
(1) 合水油田采出水腐蝕性強,水質略偏酸性(pH為6.5~7.0),礦化度高,含有較多的Ba2+、Sr2+、SO42-與HCO3-等成垢離子,存在較高的結垢風險與氧腐蝕風險。
(2) 導致采出水處理站除油沉降罐發生腐蝕的主要原因為高礦化采出水與高濃度溶解氧的存在,導致除油罐內壁與分水管等內附件發生垢下腐蝕與氧腐蝕。
(3) 向水處理系統中的除油沉降罐管內連續加注阻垢劑、緩蝕劑、除氧劑及殺菌劑,可有效緩解水處理系統設備及管線的腐蝕結垢,降低因腐蝕結垢導致的停產、維修頻次,保障油氣生產的安全。
免責聲明:本網站所轉載的文字、圖片與視頻資料版權歸原創作者所有,如果涉及侵權,請第一時間聯系本網刪除。
相關文章
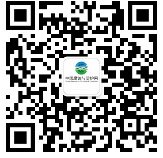
官方微信
《中國腐蝕與防護網電子期刊》征訂啟事
- 投稿聯系:編輯部
- 電話:010-62316606-806
- 郵箱:fsfhzy666@163.com
- 中國腐蝕與防護網官方QQ群:140808414
點擊排行
PPT新聞
“海洋金屬”——鈦合金在艦船的
點擊數:7607
腐蝕與“海上絲綢之路”
點擊數:6107