截至目前,國內外石油、天然氣、輸水礦漿等長輸管線一般都采用碳鋼鋼管,但是碳鋼易發生腐蝕,這不僅會造成巨大的資源浪費,還會給管線運營帶來安全風險。
1953年,美國將環氧樹脂涂敷于鋼管內壁,這是世界上最早將涂層應用于輸送管線的案例。之后,日本及一些歐洲國家也陸續開發了多種防腐蝕涂層和技術,鋼管的防腐蝕技術得到了很好的發展。
20世紀80年代中期,曼內斯曼公司和巴斯夫化學工業公司共同推出擠壓聚烯烴三層結構防腐蝕涂層,并逐步推廣應用至今。
20世紀70年代,我國開始在部分城市管道上應用環氧煤瀝青涂層,80年代才開始引進環氧樹脂涂料技術并逐步推廣使用。
碳鋼的防腐蝕研究和施工技術從環氧煤焦油、環氧瀝青、液態環氧樹脂等逐漸發展為現在的熔結環氧樹脂涂層、多層環氧涂層、三層聚乙烯涂層、三層聚丙烯涂層、五層聚丙烯涂層、七層聚丙烯涂層等等。目前,國內外大型輸油輸氣管線如西氣東輸長輸管線、陜京天然氣管線、中俄天然氣管線等,均采用環氧涂層。
不管是單、多層環氧體系的涂層,還是三層聚乙烯涂層、聚丙烯涂層,起到防腐蝕作用的都是與鋼管基材直接作用的由熔結環氧粉末形成的涂層,即熔結環氧涂層。
1 熔結環氧涂層
熔結環氧涂料的主要成分為含有環氧基和羥基的酚醛環氧樹脂或酚醛改性環氧樹脂,以及胺類、酚類或醇類固化劑,它是一種通過混合、擠出、研磨得到的無揮發性有機物的固體粉末,能夠以空氣為載體進行輸送和分散。將熔結環氧涂料施涂于已預熱的金屬基材表面,經熔化、流平、固化后會形成一道或多道均勻、致密的涂層,因此它也是一種熱固性材料。熔結環氧涂層是環氧樹脂和固化劑吸熱發生加成反應后,形成的均勻致密、且連續穩定的涂層。
熔結環氧涂層的涂裝工藝流程為:光管表面預清→光管中頻預熱→光管噴砂除銹→光管內吹掃→表面處理→中頻加熱→環氧涂料噴涂→涂層管冷卻→管端預留處理→包裝出廠。
對金屬基材進行表面處理主要是去除基材表面的污染物,同時使表面呈粗糙狀態,有助于涂層的附著。常用的表面處理工藝有化學預處理和機械預處理。其中,化學預處理包括溶劑清洗、磷酸化學預處理、鉻酸鹽處理等,機械預處理包括噴砂除銹、沖洗清理等。涂料噴涂前,對基材進行表面處理保證其達到良好的表面狀態,達到除銹等級Sa2.5級以上,表面錨紋深度70 μm左右,表面灰塵度不超過1級的水平。
環氧涂料經過流化床充分流化,再通過專用噴槍,采用高壓靜電噴涂的方式噴涂至提前預熱(預熱溫度為190~230 ℃)的基材表面,此時的基材已經過前文所述表面處理。環氧粉末粒子附著在基材表面,熔融結合固化后形成連續致密且有一定厚度的涂層。
2 鋼質基材的腐蝕機理
金屬腐蝕指金屬與環境發生反應出現退化的現象,金屬發生電化學腐蝕必須滿足四要素,即整個腐蝕過程有陰極、陽極、反應回路以及電解液。從微觀來看,在金屬內部,電流從陰極流向陽極,在電解液中,電流從陽極流向陰極,形成了閉合回路,金屬作為陽極流出電子,發生腐蝕。綜上,抑制任一環節都可以使腐蝕減緩或趨于停止。
由上可見,隔絕金屬材料與水和空氣接觸,避免金屬表面形成陰極、陽極、反應回路和電解液,可有效防止腐蝕或者延緩腐蝕,這也是防腐蝕涂層的主要防護機理。因此,涂層和基材之間的有效結合是涂層具有防腐蝕性能的關鍵,故涂層與基材的附著力是評價涂層防腐蝕性能的重要指標。
3 熔結環氧涂層附著力的評價方法
01 熱特性分析
熱特性分析是評價熔結環氧涂層附著力的基本方法之一,主要目的是評價環氧粉末材料涂裝后是否有效固化,若固化不完全將直接導致涂層附著力變差。
熱特性分析是通過涂層的吸熱特性分析其玻璃化轉變溫度的變化值(ΔTg)或固化度(C,又稱為固化百分率)。通常來說,材料不可能百分百固化,一般當玻璃化轉變溫度的變化值不超過5 ℃或固化度不小于95%時,即可認為涂層已經固化完全。表1是不同標準中關于涂層的熱特性要求。可以看出,各標準的取樣方法以及升溫降溫程序基本一樣。GB/T 23257-2017、CSA Z245.20-2014以及ISO 21809-2-2014標準中關于ΔTg的要求基本一致,但這些標準都沒有對涂層固化度提出要求,在AS/NAZ 3862:2002標準中,除了對ΔTg提出了更加嚴格的要求外,對涂層固化百分率也提出了相應要求。
表1 各種標準中關于涂層熱特性的要求
取同種粉末材料,分別于150 ℃和210 ℃下將其涂敷于基材表面(每個條件取3塊平行試樣),固化3 min后冷卻,環氧涂層干膜厚度均為200~300 μm,分別進行熱特性分析和環境暴露試驗,熱特性分析方法參照AS/NAZ 3862:2002標準,環境暴露試驗是將試樣置于大氣環境中,每隔7天觀察涂層腐蝕情況,結果如表2所示。
表2 不同涂敷溫度下制得涂層的熱分析結果和環境暴露試驗結果
由表2可見:滿足固化要求的涂層,其附著力的保持時間越長,防腐蝕性能越好。
02 熱水煮浸泡
熱水煮浸泡法也是評價環氧涂層附著力的重要方法之一,一般試驗周期為24小時,試驗溫度為75 ℃或98 ℃,表3為不同標準中關于涂層熱水煮浸泡法的具體要求。
表3 不同標準中關于涂層熱水煮浸泡法的要求
矩型法(試樣尺寸30 mm×15 mm)的具體評價標準為:
1級-涂層明顯不能被撬剝;
2級-被撬離的涂層小于等于50%;
3級-被撬離的涂層大于50%但有明顯的抗撬剝性;
4級-涂層很容易被撬剝成條狀或大塊碎屑;
5級-涂層成一整片被剝離。
V型法(試樣尺寸20 mm×20 mm)的具體評價標準為:
1級-在“V”形劃線的任意點上涂層沒有明顯的剝離,表面錨紋上完全附著涂層;
2級-涂層比較困難地出現小的碎屑狀剝落,表面錨紋上附著涂層;
3級-涂層在刀尖撬剝的地方有碎屑狀剝落,但面積范圍不太大,表面錨紋上附著部分涂層;
4級-涂層成塊狀剝落,有很小的抗剝離性;
5級-在“V”形劃線區域鋼管表面涂層完全脫落。
國家標準、加拿大標準及國際標準中均規定熱水煮浸泡法的溫度為75 ℃,且均采用矩形方法評價,3級或4級均可視為合格。但澳大利亞標準則要求環氧涂層耐98 ℃的水,接近沸水浸泡,且評價采用V型方法,3級就視為不合格,評價標準更加嚴格。
熱浸泡試驗主要考察涂層在服役過程中的耐水滲透能力,耐水滲透是一個長期過程,一般隨著溫度升高,水分子運動越劇烈,擴散滲透能力越強,水浸泡時間越長,滲透能力也越強。進一步說,水浸泡時間越長,對涂層的耐水滲透能力的評估結果越穩定全面,因此,在很多項目的設計或涂層施工技術規范中,增加了28天或更長時間的水煮,浸泡溫度不變,評價標準也不變。這是因為管線一旦服役,涂層耐水滲透就不會停止。
另外,在線或者現場對涂層附著力進行評價時,可以直接采用矩形法或V型法,不需要進行水煮試驗,以方便快速對涂層進行初步評價。
03 陰極剝離法
陰極剝離也是評價環氧涂層附著力的重要方法之一,用來檢驗涂層的附著力性能及其在陰極保護系統中抗陰極剝離的能力,各標準中關于陰極剝離試驗的具體試驗方法及評價要求見表4。
表4 各標準中關于陰極剝離試驗的具體試驗方法及評價要求
管線在服役過程中,周圍環境等都可能會為雜散電流或腐蝕電池的形成提供條件,管線鋪設完成后大都采用陰極保護措施,這就需要涂層具有良好的抗陰極剝離性能。因此各標準中的試驗方法都是模擬陰極保護過程,以觀察和評價涂層的附著力和抗陰極剝離性能。
通常要求采用短期和長期的試驗以完整評價涂層的這項性能,短期試驗的電壓高于長期試驗,但某些標準中則采用控制電流來進行試驗。但附著力的好壞最終都是根據距離中心漏點邊緣的剝離寬度來評價的。根據具體的項目要求,試驗溫度等條件也可以依次改變。
筆者曾經完成的項目,要求環氧涂層厚度300 μm時,在98 ℃,48 h,1.5 V電壓后涂層陰極剝離寬度最大值不超過3 mm,以及在98 ℃,28 d,1.5 V電壓后的涂層陰極剝離寬度平均不超過7 mm,這是非常嚴格的要求,對涂層材料以及施工技術等都是很大的挑戰。
綜上所述,陰極剝離性能可以作為熔結環氧涂層的主要評價指標,評價涂層附著力的主要方法之一。
04 拉拔法
拉拔法也是評價環氧涂層附著力的常用方法之一,主要通過機械拉脫的方法,評價涂層和基材之間能夠承受多少兆帕的強度,以及涂層是否有內聚破壞現象。
現在,多采用蘑菇頭方法,參照GB/T 5210或者ISO 4624以及ASTM D4541等標準要求,在實際評價過程中,除了試驗設備顯示的拉脫強度讀數值外,還應當評價拉脫后涂層的狀態,包括涂層與基材分開、涂層與涂層分開、涂層與膠分開以及分開程度。
熔結環氧涂層與基材具有很好的附著力才能使熔結環氧涂層對基材起到防腐蝕作用。附著力評價方法包括熱差分析法、熱水煮、陰極剝離法和拉拔法等。那為什么熔結環氧材料能在碳鋼表面良好附著呢?
4 熔結環氧涂層附著力的影響因素
01基材表面結構
附著氧化皮或銹蝕的金屬基材表面在進行防腐蝕涂層施工前需預處理,其目的主要有二:一是去除基材表面的銹蝕或其他附著物,二是形成粗糙的表面輪廓。基材表面經過噴砂除銹后,通過除銹等級標準評價基材表面銹蝕或附著物的去除質量,完全去除表面銹蝕和附著物即為Sa3級或SSPC SP5級金屬。通過錨紋深度檢測標準評價基材表面粗糙度,包括縱向錨紋深度指標和橫向峰數指標,傳統復印膠帶不能檢測峰數指標,各標準或行業規范一般只側重于錨紋深度指標,峰數指標很難實際測量。
表5是基于某電子測量儀測得的采用不同表面預處理方式處理后基材表面的錨紋深度和峰數,可以看出,同樣的錨紋深度情況下,峰數值越高,基材表面輪廓越粗糙。即單位長度上不規則峰越多,單位面積上與涂層的附著面積越大,涂層的附著力越高。
表5 不同表面預處理方式處理后基材表面的情況
02 涂層和基材界面的表面能/次表面能
熔結環氧粉末在金屬基材上的應用,最終體現于固體-固體界面,即環氧涂層固體界面與金屬基材固體界面,主要指標是表面能和次表面能。
表面能是指產生(或擴張)單位表面積所需做的可逆功。粉末熔融附著于基材的過程中,粉末熔融,且由固態轉變為熔融狀態,金屬基材的表面能遠遠高于環氧樹脂材料,理論上,熔融狀態的環氧粉末在膠化過程中,能夠充分潤濕基材。金屬基材表面的附著物清理得越干凈,其表面能越高,環氧粉末的熔融浸潤越徹底,涂層的附著力越高。
比表面通常用來表述物質分散的程度,即單位體積(或質量)固體所具有的表面積。這也印證了上述,金屬基材表面經過預處理后,表面輪廓質量越高,即錨紋深度越深,峰密度越大,基材的比表面越大,涂層的附著力越強。
03 材料的物理結構
熔結環氧樹脂材料的種類很多,本工作以雙酚A環氧樹脂為例分析其對附著力的影響。
根據雙酚A環氧樹脂分子通式:
其中的環氧基和羥基具有高極性和活性和極強的反應性,這使固化物具有優良的黏接力和內聚力,這為環氧材料在金屬表面形成化學鍵提供了可能,也有助于增強環氧材料固化后的附著力。同時,因為醚鍵和羥基等高極性基團的存在,環氧材料的浸潤性和黏附能力得到提高,粗糙表面的潤濕和浸潤能力進一步增強。
04 基材顯微組織的影響
長輸管線一般多采用X45~X70級鋼管,以西氣東輸管線用X70鋼為例,其顯微組織為針狀鐵素體,它們彼此咬合,相互交錯分布,基體上分布著高密度纏結位錯,這些微觀因素賦予了針狀鐵素體鋼管優良的強韌性能。那么,是否可以認為這種不規則的內部組織結構有利于環氧樹脂粉末涂層的附著呢?
關于這一點,筆者以碳鋼鋼管和不銹鋼光管為例進行研究,結果表明:碳鋼鋼管表面組織不規則排列,彼此咬合,高密度纏結位錯;不銹鋼鋼管表面組織排列明顯有差別,較碳鋼基材組織纏結位錯程度輕,相比于不銹鋼管碳鋼鋼管更有利于涂層的附著。
前期實踐經驗表明:普通熔結環氧粉末材料并不能應用于不銹鋼管或雙相不銹鋼管表面,但是改性環氧粉末能夠很好地附著在雙相不銹鋼管表面。即能在碳鋼鋼管上良好應用的的熔結環氧粉末材料不能應用于不銹鋼基材上,這與基材的顯微組織有關,顯微組織觀察結果也印證了這一觀點。
05 涂層+基材整體微觀結構的影響
熔結環氧粉末在預熱的基材上吸熱,熔融、膠化、交聯、固化形成一層高分子涂層,即防腐蝕涂層。
熔結環氧粉末在與基材結合的過程中,官能團如羧基具有極強的反應性,具有明顯的電負性,非常容易與基材表面形成極性鍵。同時一般基材的預熱溫度為220~230 ℃,材料與基材接觸的部位更有利于化學鍵合,粉末在固化過程中與基材接觸界面形成化學鍵,更有利于熔結環氧樹脂材料與基材的附著力的提高。
由圖1可見:涂層與金屬基材的結合面緊密無氣孔,附著良好,兩層間緊密附著無疏松多孔、縫隙、氣泡等存在,涂層與基材結合緊密。
(a)200×
(b)500×
圖1 涂層和基材結合處微觀形貌
如果極性鍵和化學鍵存在,說明熔結環氧樹脂與金屬基材之間形成了分子與分子的結合,具有范德華力,這也是熔結環氧粉末涂層的附著力普遍高于液態環氧樹脂涂層的重要原因。
結論
(1) 熔結環氧粉末材料應用于金屬碳鋼基材上,有優良附著力和防金屬碳鋼基材腐蝕的性能;
(2) 熔結環氧粉末材料本身的結構有助于在金屬碳鋼基材上良好附著。
免責聲明:本網站所轉載的文字、圖片與視頻資料版權歸原創作者所有,如果涉及侵權,請第一時間聯系本網刪除。
相關文章
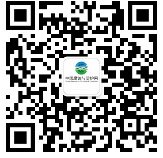
官方微信
《腐蝕與防護網電子期刊》征訂啟事
- 投稿聯系:編輯部
- 電話:010-62316606-806
- 郵箱:fsfhzy666@163.com
- 腐蝕與防護網官方QQ群:140808414
點擊排行
PPT新聞
“海洋金屬”——鈦合金在艦船的
點擊數:8148
腐蝕與“海上絲綢之路”
點擊數:6486