案例1:核電疏水閥蒸汽管線泄漏原因分析與預防(服役環(huán)境考慮不周)
1. 事故背景
某核電站近幾年接連發(fā)生常規(guī)島X機組疏水閥蒸汽管線泄漏事故,泄漏發(fā)生于相同機組的不同管線,出現(xiàn)泄漏的時間有長有短,泄漏位置均與焊縫有關,有焊縫與直管交界處,有焊縫與彎管交界處,也有焊縫區(qū)域,在靠近焊縫彎管內(nèi)表面的氣蝕坑中也發(fā)現(xiàn)了裂紋。
2. 失效部位
管線開裂泄漏情況見圖1a)。宏觀分析時發(fā)現(xiàn)焊接部位鋼管內(nèi)壁的顏色不同,焊縫一邊顏色較亮,呈銀灰色,而另一邊覆蓋著褐色氧化腐蝕產(chǎn)物,見圖1b);焊接下塌比較明顯,焊縫上存在蜂窩狀孔洞,而另一側焊縫未見此特征,見圖1c);焊縫與母材交界處存在孔洞以及起源于孔洞的微裂紋,見圖1d)。
圖1 泄漏管線宏微觀形貌
3. 失效分析
采用有限元對管線的實際工況進行數(shù)字模擬,并經(jīng)過現(xiàn)場勘查、事故調(diào)查、現(xiàn)場取樣和全面的理化分析及綜合分析,最后得出管線發(fā)生泄漏失效的原因如下:管線內(nèi)高溫水流經(jīng)彎管或焊接下塌處時,產(chǎn)生了局部負壓區(qū),高溫水流經(jīng)過這些區(qū)域時因壓力突然下降,瞬間氣化變?yōu)闅馀荩瑲馀荼〞r產(chǎn)生巨大的爆破應力,發(fā)生空泡腐蝕,同時也引起管線振動,當其頻率與管線固有頻率成整數(shù)倍時,管線還發(fā)生共振,振動幅度加大,導致管線在焊縫這個“薄弱環(huán)節(jié)”部位發(fā)生了腐蝕疲勞開裂,裂紋穿透整個管壁后,管線發(fā)生泄漏。
4. 改進措施
針對該次失效分析的結論,提出了三個預防措施:
① 提高焊接質(zhì)量,控制焊接下塌尺寸,減少空泡腐蝕發(fā)生的可能;
② 增加管線支撐架或改變管線規(guī)格,以改變管線固有頻率,防止發(fā)生共振;
③ 在管線上安裝減震設施實時監(jiān)測,依據(jù)監(jiān)測結果及時采取糾正措施,避免管線產(chǎn)生共振。
5. 整改后
核電機組根據(jù)該失效分析報告的結論和提出的預防措施,結合機組的實際情況,加強了焊接質(zhì)量控制,并將管線的壁厚由3mm改為5mm,改變了系統(tǒng)的固有頻率。經(jīng)過一年多的實際運行,未再發(fā)生管線泄漏事故。
案例2:裝卸料機料倉Ferguson齒輪隨動滾輪頂絲斷裂失效分析與預防(安裝不合理)
1. 事故背景
斷裂的頂絲服役于核電燃料裝卸料機料倉Ferguson齒輪隨動滾輪,該頂絲表面采取了“發(fā)黑”處理,安裝使用不到兩年,在設備維護和保養(yǎng)時發(fā)現(xiàn)斷裂,見圖2a)。
圖2 斷裂頂絲宏觀形貌及有限元模擬結果
2. 事故調(diào)查與分析
經(jīng)事故調(diào)查,在不同的設備上共發(fā)現(xiàn)有10多個頂絲斷裂,其裝配情況和斷裂位置基本相同。該頂絲在設備上的安裝服役示意圖見圖2b),正常情況下,頂絲依靠其頭部的圓錐體頂住滾輪螺紋部分的鍵槽部位,起定位和預防滾輪轉(zhuǎn)動的作用。頂絲擰進去的深度大約為16mm,露在外面大約為8mm,頂絲總長度為25.4mm。頂絲擰緊后再在露出部分緊固一個螺母,其目的是防止頂絲松動脫落。
經(jīng)調(diào)查,安裝螺母時沒有對扭矩作要求,原則上擰緊即可。在使用過程中,頂絲和滾輪會一起反復浸入齒輪箱中的潤滑油中。
按照實際頂絲的形狀、尺寸,以及裝配情況進行幾何建模和網(wǎng)格劃分,然后采用Ansys軟件對頂絲的受力情況進行模擬分析,分析結果如下:
①假設安裝時沒有螺母,最大拉應力出現(xiàn)在錐部第一扣螺紋處,見圖2c);
②實際裝配情況下,即頂絲外部有螺母時,最大拉應力出現(xiàn)在螺母與滾輪架接合處,見圖2d),該最大受力位置與實際斷裂位置相吻合。
3. 失效分析
根據(jù)頂絲的理化檢驗結果和斷口形貌分析結果判斷,該頂絲斷裂性質(zhì)為氫致延遲斷裂。
該頂絲的實際使用特點類似于螺栓,其硬度測試結果為476~482HV0.5,參考GB/T 3098.1-2010《緊固件機械性能螺栓、螺釘和螺柱》,該硬度已經(jīng)超出了12.9級螺栓的維氏硬度范圍385~435HV10。螺栓的強度等級越高,其對氫脆型斷裂就越敏感。
由受力分析結果可知,頂絲未加裝螺母時,服役過程中靠近錐部第一扣螺紋側面承受最大拉應力,但該部位頂絲的中心部位承受壓應力,見圖2c);若安裝扭矩較大時,靠近錐部的螺牙可能會發(fā)生斷裂,但頂絲整體不會發(fā)生斷裂。
加裝螺母后,頂絲受力特點與螺栓相似,服役過程中承受恒定拉應力,有限元分析結果表明最大拉應力出現(xiàn)在螺母與滾輪架接合處,見圖2d),該最大受力位置與頂絲實際斷裂位置相吻合。
4. 改進措施
針對該次失效分析的結論,提出了以下兩個預防措施:
① 不加裝螺母,改用其他方法來預防頂絲滑脫;
② 降低頂絲的硬度(相當于降低螺栓的強度等級),安裝時增加扭矩要求。
對于使用方來說,建議①比較容易實施,可從根本上解決問題;建議②涉及的實際硬度和扭矩都是未知數(shù),需要進一步驗證,實施起來相對比較困難。
5. 整改后
后來用戶從實際設備的整體考慮,將該頂絲材料改為304不銹鋼(實際上是降低了螺栓強度等級),經(jīng)過兩年多的實際運行,未再出現(xiàn)類似的斷裂事故。
案例3:地鐵列車減震總成中心銷失效分析與預防(優(yōu)化設計)
1. 事故背景與失效件宏觀形貌
地鐵列車減震總成上的中心銷在列車運行21a(年)后發(fā)生了斷裂,斷裂位置見圖3a),斷口形貌見圖3b)。中心銷材料為34CrNiMo6鋼,圖紙技術要求抗拉強度為800~1080MPa,已斷裂部分的螺母高度經(jīng)測量為57mm,斷裂的螺紋端長度為90mm。
圖3 斷裂中心銷宏觀形貌及示意圖
經(jīng)實際稱重,斷裂部分的總質(zhì)量為2.965kg,見圖3c);斷裂位于螺紋根部的過渡圓角處,該部位外圓尺寸為?46mm,過渡圓角半徑為R2.5mm,見圖3d),螺紋部分公稱直徑為56mm。
圖3e)為中心銷實際裝配情況,可以看到正常服役時,斷裂的螺紋部分位于列車底部,處于懸空狀態(tài),見橢圓形標識。列車靜止時,斷裂部位只受到螺紋部分和螺帽的重力作用。
2. 理化檢驗
由理化檢驗結果可知:斷裂中心銷的化學成分和拉伸性能符合技術要求;實際晶粒度等級為9.5~10級,夾雜物評定結果為A2.0,A1.0e,B0,C0,D0.5,橫向低倍和縱向低倍檢驗均未見明顯異常,斷裂源處、斷口處的顯微組織與遠離斷口處基體的一致,均為回火索氏體+少量鐵素體,斷口上可觀察到少量夾雜物;斷口宏觀分析和掃描電鏡(SEM)微觀分析均表明該中心銷斷裂性質(zhì)為疲勞斷裂,疲勞源位于螺紋端與銷桿的過渡圓角處,該部位存在周向分布的機械加工刀痕,過渡圓角半徑經(jīng)測量符合技術要求,疲勞斷裂源相對分布,為雙向彎曲疲勞斷裂。
3. 現(xiàn)場勘查
現(xiàn)場勘查時發(fā)現(xiàn),正常裝配情況下,螺紋部分處于懸空狀態(tài),但列車在啟動或剎車時會產(chǎn)生加速度,懸空的螺紋部分會受到慣性力的作用,力的大小遵循牛頓第二定律,即F=ma(F為作用力,m為質(zhì)量,a為加速度),該力的大小與斷裂部分的質(zhì)量以及加速度均成正比。懸空的螺紋部分類似于一個懸臂梁結構,螺紋端與銷桿過渡圓角處承受最大的彎矩和彎曲應力。過渡圓角處外圓直徑為46mm,螺紋外徑為56mm,可見斷裂處尺寸相對較小,R2.5mm處會產(chǎn)生應力集中,該部位的周向加工刀痕還會增加應力集中的程度,因而該部位容易萌生疲勞裂紋,成為疲勞裂紋源。
4. 失效原因
該中心銷斷裂失效分析的結論為:
① 斷裂的中心銷材料質(zhì)量檢驗結果符合相關技術要求;
② 中心銷斷裂性質(zhì)為雙向彎曲疲勞斷裂,列車在啟動或剎車時產(chǎn)生的加速度導致懸空的螺紋部分產(chǎn)生慣性力,該力的大小遵循牛頓第二定律,過渡圓角處較小的尺寸以及該部位的周向加工刀痕均會增加該處應力集中的程度,使該處容易萌生疲勞裂紋。
5. 改進措施
根據(jù)該失效分析結論和現(xiàn)場勘查情況,提出的預防措施如下:
①增大過渡圓角處的外圓尺寸?值和過渡圓角半徑R值;
③ 提高過渡圓角位置的表面加工質(zhì)量,減輕螺母的質(zhì)量。
6. 整改后
由于中心銷的原設計壽命為30a,斷裂時已經(jīng)服役了21a,考慮到減震總成的整體設計和結構,設計方同意將原來的R2.5mm提高到R5mm,用墊片解決了螺紋根部的緊固問題。各種理論計算結果表明:改進后的中心銷其疲勞壽命有了較大幅度的提高,完全可以達到30a的使用壽命。
免責聲明:本網(wǎng)站所轉(zhuǎn)載的文字、圖片與視頻資料版權歸原創(chuàng)作者所有,如果涉及侵權,請第一時間聯(lián)系本網(wǎng)刪除。
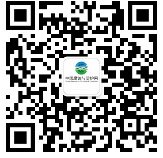
官方微信
《腐蝕與防護網(wǎng)電子期刊》征訂啟事
- 投稿聯(lián)系:編輯部
- 電話:010-62316606-806
- 郵箱:fsfhzy666@163.com
- 腐蝕與防護網(wǎng)官方QQ群:140808414