1 序言
錐齒輪是工業中非常重要的機械零件,主要特點是可以承受較大的負荷,工作平穩,噪聲和振動小,廣泛用于汽車主減速器上,在傳遞功率和運動過程中起著至關重要的作用。引起齒輪失效主要與工作條件有關,主要包括應力狀況、載荷、溫度及環境等。齒輪失效的主要因素包括設計、材料、加工、安裝、環境和使用等方面。
齒輪斷口分析是判斷齒輪斷裂形式和斷裂機理的重要技術手段,斷口形貌可真實地記錄裂紋的起因、擴展和斷裂的過程,因此它不僅是研究斷裂過程微觀機制的基礎,同時也是分析斷裂原因的可靠依據。由于齒輪表面殘余應力對齒輪疲勞壽命有重要影響,因此殘余應力檢測分析已成為新興的失效分析檢測手段。
2 斷裂失效齒輪背景調查
失效齒輪為某普通牽引車型中橋的齒輪副從動輪兩齒斷裂,主動輪完好。該車試用8個月,行駛里程為100573km,零件三包期限為18個月,發生故障時仍在三包期內,其相關件橋殼完好,與齒輪副 無干涉,主動輪、從動輪螺紋及裝配螺母完好,無松動潛在相關影響。齒輪使用的材料為22CrMoH鋼(日本牌號SCM822),該材料具有較高經濟性和適合的力學性能,多用于中型汽車后橋主動齒輪、從動齒輪。重載滲碳齒輪熱處理一般技術要求為:1/2齒高處有效硬化層深度1.7~2.1mm,表面硬度58~63HRC,心部硬度33~45HRC,馬氏體級別1~4級,殘留奧氏體1~4級,碳化物1~2級,心部組織1~4級,表層非馬氏體厚度≤0.02mm,晶粒度高于6級。
滲碳淬火從動齒輪生產工藝過程如下:圓鋼下料→鍛造→等溫正火→粗車→精車→鉆孔、攻螺紋→銑齒→倒棱→清洗→熱處理(滲碳、壓淬、低溫回火)→拋丸清理→車內孔→研齒配對→包裝入庫。失效齒輪結構如圖1所示。
3 失效分析設備
在失效分析過程中,常用設備儀器主要有金相顯微鏡、直讀光譜儀、維氏硬度計、洛氏硬度計、 掃描電子顯微鏡(SEM)、X射線應力分析儀及電解拋光儀等。
4 斷口宏觀形貌分析
當金屬零件所受的應力大于材料的臨界強度時,零件通常會產生斷裂,并在斷裂處形成斷口。斷口分析是各種失效分析手段中最主要的分析方式,斷裂的位置通常處于零件結構或材料組織最 脆弱的地方。
斷口的出現除了與材料的成分、組織及零件的結構相關,還與零件斷裂時所受力情況及 外界使用環境相關。由于斷面內包括了試樣斷裂失效整個過程的大量信息,所以通過對斷口的形態觀察,分析其所記錄的相關數據,就能研究斷裂的性質、原因、形式,以及所受應力狀態等諸多信息。斷口就是打開的裂紋,包含了從裂紋的產生到最后發生斷裂的整個過程,而其他裂紋可能是伴隨著斷口產生的,通常并不包括斷裂剛開始時的信息。進行宏觀斷口分析的目的是確定裂紋源區、擴展區和最終斷裂區,查明斷裂生產的機理,是完成失效分析的基礎。
通過宏觀斷口觀察(見圖2),主動輪完好,從動輪有1#、2#兩個齒出現斷齒,其中1#齒可見明顯光亮輝紋,為典型接觸疲勞斷裂形式。相鄰斷齒無明顯疲勞斷裂特征,呈深灰色沖擊韌性斷口。同一構件系統中出現兩種性質不同斷裂特征,在這種情況下應先確定首個斷裂部位。基本原則為既有疲勞斷裂又有沖擊韌性斷裂,一般疲勞斷裂發生在前,由此分析得出1#齒先斷裂,2#齒是被1#齒碎片打斷的。進一步對1#齒進行宏觀觀察,發現1#齒斷口處既有疲勞斷裂特征也有韌性斷裂特征。當兩者同時存在時,裂紋源區存在于疲勞裂紋一側。宏觀粗視分析結論為1#齒凹面近齒根處齒面次表層最先出現顯微裂紋,隨著疲勞應力的增加,在表面滲碳層先出現壓碎(壓潰),裂紋進一步向心部擴展,到交界剪切唇處失穩斷裂,而斷裂的碎片將2#齒打斷。下面將對1#齒的裂紋源區、剪切唇和心部韌性斷裂進行微觀形貌分析。
5 斷口微觀形貌分析
對斷口進行掃描電鏡顯微觀察,圖3所示為斷口齒輪疲勞源區SEM形貌,
圖4所示為疲勞擴展區SEM形貌,
圖5所示為瞬斷區SEM形貌。
斷口裂紋源位于齒輪凹面中下部,裂紋擴展過程還產生其他的次生微裂紋,在變載荷應力作用下,齒輪凹面中部接觸區咬合面近齒根的表層處首先產生顯微裂紋,出現齒面壓潰剝落。接著裂紋呈人字花樣往心部擴展,最終在剪切唇處斷裂,心部瞬斷區可見明顯韌窩準解理形貌特征。裂紋兩側,未見明顯夾雜物及第二相缺陷。斷裂性質確定為接觸疲勞裂紋。
1)斷口裂紋源位于齒輪凹面中下部,裂紋擴展過程還產生其他次生微裂紋。
2)裂紋源微觀形貌為接觸疲勞特征,心部微觀形貌為韌窩加解理特征。
6 理化分析
(1)化學成分分析檢測齒輪所選用材料的化學成分是否滿足圖樣技術要求,采用Q8直讀光譜儀檢測其化學成分,結果見表1。
從表1可看出,齒輪材料化學成分符合GB/T5216—2014《保證淬透性結構鋼》要求。
(2)有效硬化層深度有效硬化層深度是滲碳齒輪的重要技術指標。若有效硬化層過淺,齒輪的耐磨性不足;若有效硬化層過深,會加劇硬化層坍塌剝落速度。本失效件測定了主減速器從動錐齒輪的硬度層深和梯度,按GB/T9450—2005《鋼件滲碳淬火硬化層深度的測定和校核》進行測定和計算,550HV1硬度的有效硬化層深度為2.18mm,硬化層略超深。
(3)晶粒度按GB/T6394—2017《金屬平均晶粒度測定方法》中的比較法,與標準系列評級圖進行對比,用比較法一般存在一定的偏差(±0.5級),本次分析試樣晶粒度為7.0級,符合細晶粒標準要求(晶粒度細于6級)。
(4)非金屬夾雜物在從動錐齒輪上取金相試樣,按GB/T10561—2005《鋼中非金屬夾雜物含量的測定標準評級圖顯微檢驗法》規定進行夾雜物評定,材料中個別視場的夾雜物、硫化物和均勻性略有超標。
(5)金相組織在主減速器從動錐齒輪上取金相樣,金相組織按QC/T262—1999《汽車滲碳齒輪金相檢驗》進行評定,馬氏體4級(見圖6),
殘留奧氏體3級(見圖7),
碳化物1級,心部3級(見圖 8)。
從圖6~圖8可看出,馬氏體、殘留奧氏體、碳化物和心部游離鐵素體均滿足金相組織要求。按GB/T6394—2017進行評定,晶粒度為7.5級,合格。表面硬度61HRC、心部硬度39.5HRC符合圖樣技術要求。另外,在整個齒面上均存在不同程度的內氧化現象,齒面內氧化深度為0.02mm,齒根處內氧化(非馬氏體組織)深度最大為0.025mm(見圖9)。
從橫截面觀察齒面裂紋,發現微裂紋起源于表面的內氧化。整個齒面上均存在內氧化現象,這相當于齒面上存在較多的“刀口”,在較大的齒面接觸工作應力作用下,齒面迅速在內氧化的“刀口”處形成微裂紋,并向脆性滲碳層內部發展和延伸。非馬氏體組織是由內氧化的貧合金化元素導致而形成。一旦形成此類組織,其后果是降低最表面硬度(一般指≤0.05mm處的硬度)、耐磨性及疲勞極限,且由晶粒邊界或氧化物的應力集中區域萌生細微裂紋并向更深的地方延伸。
7 殘余應力檢測分析
殘余應力檢測設備參數見表2。
失效件從動齒(未強化噴丸)和經表面強化噴丸樣件殘余應力對比見表3。
齒輪強化噴丸是提高齒面接觸疲勞強度的有效途徑之一。由于噴丸強化提高了表面壓應力而顯著改善其疲勞性能,因此對于承受高周波疲勞載荷的工件更為有效。噴丸強化形成的殘余壓應力可抵消部分外加載荷。噴丸時小尺寸球形鋼丸擊打工件表面而形成壓應力,每一彈丸的沖擊都會使金屬產生一定的塑性變形,最終因表面不能完全回復而形成了永久的壓應力狀態。作為一種表面強化工藝,噴丸能在表面形成殘余壓應力,相當于材料抗拉強度極限的55%~60%,而工件表面恰是容易萌生裂紋的地方。對于滲碳淬火齒輪,所形成的壓應力可達1177~1725MPa,可大大改善疲勞性能。壓應力層深度是噴丸強度(或噴丸能量)的函數,隨著彈丸尺寸或彈丸速度的增加而增加。從殘余應力測試對比驗證數據看,經過表面強化工藝,齒根部表面殘余壓應力由824MPa提高到1252MPa,接觸疲勞性能得到大幅提升。
8 結論
通過齒輪斷口分析、理化分析、金相組織及殘余應力分析,得出重載滲碳齒輪失效的原因如下。
1)裂紋源位于齒輪凹面中下部表面,失效斷裂形式為接觸疲勞斷裂。
2)齒面及齒根上存在的內氧化,弱化了晶界,降低了齒輪接觸疲勞強度。
3)從動齒輪材料純凈度和均勻性略有超標,熱處理壓淬后齒輪變形不一致,與主動齒輪工作嚙合時 由于受力偏載而產生應力集中,加速了齒輪斷裂。
9 建議和措施
1)齒輪在滲碳淬火及回火后,因為存在內氧化軟層,所以在噴丸強化處理時易產生應力集中,成為疲勞裂紋源的起點。建議在保證材料淬透性的前提下選用低Si材料,盡量控制Cr、Mn、Ti、V等合金元素含量,滲碳原料氣(甲醇或天然氣)采用凈化處理,減少氧化性組分,如水、硫等雜質的含量,減輕熱處理后產品的內氧化程度。
2)強化噴丸可提高齒輪的彎曲疲勞強度和接觸疲勞強度,是改善齒輪抗咬合能力、提高齒輪使用壽命的重要途徑。
3)從材料源頭控制夾雜物的純凈度和偏析,配合實施壓淬工藝減小熱處理變形,提高接觸區一致性,改善工況。
免責聲明:本網站所轉載的文字、圖片與視頻資料版權歸原創作者所有,如果涉及侵權,請第一時間聯系本網刪除。
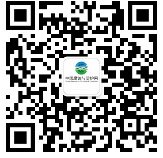
官方微信
《腐蝕與防護網電子期刊》征訂啟事
- 投稿聯系:編輯部
- 電話:010-62316606-806
- 郵箱:fsfhzy666@163.com
- 腐蝕與防護網官方QQ群:140808414