鋁合金結構外型美觀、耐腐蝕性強,具有廣泛的應用前景。然而,關于鋁合金結構在高腐蝕性環境下的行為尚無系統研究,限制了其在復雜惡劣環境下的應用。
隨著材料科學和結構工程的不斷發展,鋁合金逐漸成為一種常用的建筑材料,已較廣泛地應用在空間網格結構、人行天橋、門式剛架中。鋁合金材料的自重約為鋼材的三分之一,強度和低碳鋼相近,具有良好的耐腐蝕性能,是一種性能良好的綠色建筑材料。
金屬結構在使用過程中,受到服役環境的影響,會出現各種各樣的損傷,其中腐蝕是較為常見的一種損傷形式。金屬腐蝕現象普遍存在于國民經濟建設的各個領域,危害極其嚴重,會造成重大的經濟損失,甚至導致安全事故。
眾所周知,鋁是一種非常活潑的金屬,其表面能自然形成一層致密的氧化膜,這使得鋁材料在普通大氣環境下表現出優良的耐腐蝕性;并且還可以在工廠對成型構件進行表面處理,進一步提高其耐腐蝕性。因此,作為一種在腐蝕性環境中性價比較高的選擇,鋁合金結構具有較好的耐久性,能顯著降低結構服役期間的維護費用。
近年來,隨著鋁合金建筑結構的不斷發展和應用,針對鋁合金結構在極端惡劣大氣環境中的耐久性研究需求日益凸顯。
鋁合金大氣腐蝕特點
鋁合金具有優良的耐腐蝕性能,但并不意味著完全不會出現腐蝕現象。飛機常用鋁合金材料制造,充分利用了鋁合金輕質高強的特點,然而在高鹽高濕環境介質的作用下卻又具有相當的腐蝕敏感性。例如1981年,臺灣民航客機B-737遭遇空難,之后查明是該機經常運輸海鮮,機身下部鋁合金結構多處發生嚴重的晶間腐蝕、剝蝕,導致出現裂紋和孔洞,在空中增壓時引發爆破解體。
從腐蝕的外觀形貌來看,金屬的腐蝕可分為均勻腐蝕和局部腐蝕。對于鋁合金來說,其表面存在的氧化膜具有良好的保護性,故均勻腐蝕現象非常輕微,甚至不會出現。然而,在某些極端條件下,則可能出現局部腐蝕現象,并會造成一定的危害。鋁合金在海洋大氣環境下的局部腐蝕主要包括點蝕、電偶腐蝕、縫隙腐蝕、剝落腐蝕、晶間腐蝕和應力腐蝕等。
現有的研究證明,在鹵素離子含量高的潮濕大氣環境中,空氣中的鹵素離子(如氯離子)會侵蝕鋁合金材料表面的氧化膜,破壞防護層,形成腐蝕坑。尤其是在沿海、多雨、潮濕、高溫和工業污染較為嚴重的地區,應特別注意鋁合金材料的腐蝕,避免出現嚴重的安全事故和經濟損失。此外,在實際施工過程中,構件不可避免地會出現碰撞、劃擦和磨損,這些都會破壞鋁合金構件表面的氧化膜,降低其耐腐蝕性。另外,鋁合金結構在服役過程中,受到的外荷載也可能使其表面的氧化膜開裂,從而降低其耐腐蝕性。
鋁和鋁合金的耐腐蝕性能主要取決于其表面鈍化膜的性質及其在各種環境中的穩定性。腐蝕現象的影響因素非常復雜,受到氣候條件、空氣中污染物濃度和材料本身性質等各種因素的影響,而且各因素之間還有耦合效應。這也造成了鋁合金的各種腐蝕破壞形式之間存在一定的關聯,比如點蝕會逐步發展為晶間腐蝕和剝落腐蝕,而各種局部腐蝕又會成為應力腐蝕的裂紋源。
鋁合金腐蝕試驗研究現狀
現有的關于鋁合金腐蝕的研究,基本都集中在材料科學中。通過各種電化學測量技術,評定鋁合金的耐腐蝕性能。但是對于鋁合金腐蝕后力學性能的相關研究非常少。另外,值得注意的是,鋁合金牌號繁多,從1×××系至9×××系,各種各樣的合金成分對鋁合金本身的耐腐蝕性能影響很大。例如,常用的高強鋁合金2×××系鋁合金(以銅為主要合金元素)和7×××系鋁合金(以鋅為主要合金元素)的強度較高,但是其耐腐蝕性較差;3×××系鋁合金(以錳為主要合金元素)、5×××系鋁合金(以鎂為主要合金元素)和6×××鋁合金(以鎂和硅為主要合金元素)則具有更好的耐腐蝕性能,屬于中等強度鋁合金。
通常來說,鋁合金橋梁中建議使用5×××系和6×××系鋁合金,原因在于其強度和耐腐蝕性能更加適合工程應用。我國《鋁合金結構設計規范》(GB 50427—2007)中也規定,鋁合金結構型材宜采用5×××系和6×××系鋁合金,板材宜采用3×××系和5×××系鋁合金。建筑結構用鋁合金牌號的選用充分考慮了材料的強度和耐久性要求。
腐蝕試驗是探究金屬大氣腐蝕規律的有效手段。目前金屬腐蝕試驗研究一般通過室外大氣暴露試驗和室內模擬加速試驗來進行。衡量金屬腐蝕程度的指標包括年失重率或年增重率,孔蝕坑的深度、面積和密度分布,以及腐蝕后力學性能損失量等。觀察腐蝕形貌和腐蝕產物時,可以使用掃描電子顯微鏡、原子力顯微鏡、激光掃描共聚焦顯微鏡等。另外也可以采用電化學工作站、掃描開爾文探針技術等電化學測量手段來研究金屬腐蝕。
1 室外大氣暴露腐蝕試驗研究現狀
室外大氣暴露試驗是將所研究的金屬材料或試件放置在實際使用環境下進行暴露試驗,是最直接的研究方法。鋁合金耐候性的研究由來已久。對于均勻腐蝕的金屬來說,如鐵、鋅等,腐蝕失重率或平均損失厚度是具有相當可信度的衡量腐蝕程度的指標;但是對于鋁合金這類具有明顯局部腐蝕特征的金屬,這兩種指標并不能完全反映腐蝕程度。因此,采用蝕坑深度和分布密度及剩余力學性能可更好地反映腐蝕損傷程度。表1給出了部分文獻中的室外暴露腐蝕試驗數據。可以看出鋁合金耐大氣腐蝕性能良好,蝕坑深度基本處于微米級別。下文將對表1給出的部分文獻中的試驗數據進行闡述。
01 短期室外大氣暴露腐蝕試驗
通過短期的室外暴露試驗能夠探究鋁合金的初期大氣腐蝕行為。HERN NDEZ等在西班牙特內里費島進行了大氣暴露試驗。該試驗并未說明采用了何種牌號鋁合金,根據其合金成分推測為5×××鋁合金,半年后試件表面出現了點蝕現象,即使是在最嚴酷的腐蝕環境下,蝕坑平均深度不超過60μm。
國內王沙沙等在青島對6061-T651鋁合金進行了海洋-工業大氣環境下的室外暴露試驗。一年后,其屈服強度和抗拉強度降低幅值均在5%以內;之后又進行了6061-T6鋁合金與30CrMnSiNi2A結構鋼電偶連接件的室外暴露試驗,證明了異種金屬接觸會顯著降低鋁合金的耐腐蝕性,且空氣中硫化物會促進沿晶腐蝕的發展。
ELOLA等也在西班牙的5個試驗點對A1050鋁合金進行了長達4年的大氣暴露試驗。最終發現,在海洋-工業大氣環境下,鋁合金的腐蝕情況最嚴重;而在大陸性氣候的鄉村地區,鋁合金的腐蝕情況最輕微。隨時間延長,腐蝕坑密度遵循線性增長規律,而腐蝕坑平均深度和最大深度遵循雙對數規律。
SURNAM等在毛里求斯島上對A1050鋁合金進行了為期1.5年的暴露試驗,得到最大腐蝕深度約為50μm;并采用冪指函數擬合了最大蝕坑深度增長曲線。
02 中、長期室外大氣暴露腐蝕試驗
短期鋁合金室外暴露腐蝕試驗證明了其腐蝕具有點分布的特征,且鋁合金在大氣中暴露一段時間后的腐蝕速率會迅速降低。鑒于鋁合金在大氣中腐蝕速率低、發展慢,而且國際上普遍認為材料自然腐蝕數據需要8~10年以上才有真正的應用價值,所以中、長期的腐蝕試驗是必需的,這對于認識鋁合金結構在整個壽命周期內的承載性能變化具有重要的參考意義。
早在20世紀20年代,美國Alcoa實驗室進行了相當廣泛的鑄造鋁合金和變形鋁合金的暴露試驗,大約有25000個試件。從20世紀四五十年代,法國和意大利也相繼開展了鋁和鋁合金的大氣暴露試驗。我國起步較晚,從20世紀80年代才開始進行相關的試驗。
GHALI給出了6061-T鋁合金在海洋大氣環境(巴拿馬)下的中、長期腐蝕情況,暴露試驗持續了16年,測得每年平均腐蝕深度為17.3μm。
FUENTE等通過試驗發現,在工業或海洋大氣中,鋁合金的腐蝕情況最嚴重,暴露16年后觀察到大約100μm深的腐蝕坑;根據該試驗所用合金成分,推斷為1×××系鋁合金。以上兩類試驗都證明了鋁合金具有較好的長期耐腐蝕性能。
鋁及鋁合金在不同環境下的腐蝕敏感性差異很大,在我國不同自然環境下的腐蝕率相差6~15倍,而相對易腐蝕環境為海洋大氣、濕潤工業環境、工業污染環境。鄭棄非等對10種鋁合金在我國7個典型大氣試驗站進行了10年暴露試驗。得出結論:影響鋁合金中、長期腐蝕的環境因素中,污染物因素是主要的,氣候因素是次要的;其中,空氣中SO2含量的影響最為顯著。大量研究均表明,鋁合金大氣腐蝕最敏感的環境是海洋和工業大氣環境。
鋁合金在腐蝕發展過程中腐蝕速率的變化基本遵循“先快后慢”的特點。WALTON等進行了各種Alcoa變形鋁合金和鑄造鋁合金的長期大氣耐候性試驗。結果表明,鋁合金在大氣中暴露1~2年后,腐蝕速率迅速衰減,表現出“自停止”的現象。即使是耐腐蝕性較差的鋁合金,在嚴酷海洋大氣環境下,腐蝕坑深度每年增長小于50μm;在普通大氣環境下,每年增長小于25μm。
文邦偉等在萬寧試驗站進行了10年的大氣暴露試驗,研究了純鋁、防銹鋁、鍛鋁和硬鋁的耐腐蝕性,1年平均腐蝕深度約為0.2~0.45μm/a,10年后的年平均腐蝕深度為0.08~0.25μm/a,表明腐蝕速率隨時間迅速減緩。
文邦偉等和林德源均指出鋁合金的腐蝕產物會堆積在金屬表面,具有一定的防腐作用。
03 腐蝕規律模型
通過對試驗數據的總結分析,學者們試圖建立各種數學模型來描述鋁和鋁合金在不同大氣環境下的腐蝕行為。
最常見的腐蝕模型為冪指函數模型,AZIZ等提出采用冪指函數來表達蝕坑深度增長規律。冪指函數增長規律的表達式為:
式中:C為腐蝕程度;t為暴露腐蝕時間;k為與材料和環境相關的參數。
其中,指數n在SURNAM等試驗模型(S模型)中約為0.2,而在Godard模型(G模型)中則為1/3。相比于G模型,S模型能更好地代表毛里求斯大氣環境下的鋁合金最大腐蝕深度增長規律,從中可以得出:針對不同的大氣環境和材料屬性,k和n均應通過大量試驗數據確定,以得到符合當地氣候條件的腐蝕深度增長規律。
MELCHERS調查了大量鋁合金腐蝕試驗數據,認為相比冪指函數模型,雙峰函數模型更適用于描述蝕坑深度增長規律。
OTERO等根據腐蝕規律推斷蝕坑深度的增長遵循半對數曲線,且推測在100年后最大蝕坑深度不會超過第1年的5倍。
ELOLA等則根據試驗數據擬合了描述蝕坑深度發展規律的雙對數曲線。半對數函數模型和雙對數函數模型的表達式分別為:
式中:C為腐蝕程度;t為暴露腐蝕時間;a和b均為與腐蝕因素相關的擬合參數。
以上腐蝕模型的曲線如圖1所示。
圖1 腐蝕模型
鋁合金腐蝕發展的影響因素眾多,主要包括材料化學成分、材料微觀結構、暴露溫度、暴露時間、局部溶液條件和應力狀態等。此外,適用于短期腐蝕規律的模型未必適用于長期腐蝕。因此要建立統一且具有相當可信度的腐蝕模型是非常困難的。面對諸多的鋁合金類型和復雜的大氣環境,鋁合金的大氣腐蝕發展規律存在明顯的差別,必須通過足夠的現場試驗數據對腐蝕規律模型的參數進行校準。換句話說,對于特定的鋁合金牌號和大氣環境,需要對其腐蝕模型參數進行專門的校準,這就會耗費大量的時間和經濟成本。
2 室內模擬加速腐蝕試驗研究現狀
因室外腐蝕試驗周期長、耗費大,室內模擬加速腐蝕試驗成為研究海洋大氣腐蝕的主要手段。加速試驗必須滿足模擬性、重現性和加速性3個要求,直接影響到室內模擬試驗和室外暴露試驗的相關性。常見的室內模擬加速腐蝕試驗有鹽霧試驗、干濕周浸循環試驗等。表2給出了部分文獻中的室內模擬加速腐蝕試驗數據。
張琦對LC4和LY12兩種鋁合金均進行了間歇鹽霧和周期輪浸加速試驗,并與廣州和海南瓊海的現場試驗進行對比,發現采用pH=3.0的5%NaCl+0.5%(NH4)2SO2為溶液的間歇鹽霧試驗對于大氣暴露腐蝕具有較好的模擬性和加速性。
王潔采用干濕循環鹽霧試驗的方法對7075鋁合金(1mm厚)的腐蝕性能進行了研究,發現5個周期后鋁合金強度下降約20%~30%。強度衰減較大的原因有兩個:一是7075鋁合金本身的耐腐蝕性較差;二是該試驗中試件厚度太薄。鋁合金原始試件的厚度對其剩余力學性能存在較大的影響。在腐蝕深度相同的情況下,與較厚的鋁合金試件相比,較薄試件會表現出更明顯的強度降低。
由于鋁合金本身強度較低,故緊固件一般采用強度較高的其他金屬材料,如不銹鋼、碳素鋼等。在高濕、高鹽霧濃度的海洋環境下,異種金屬之間的接觸會導致電偶腐蝕。鋁合金的電位較低,通常作為陽極金屬而被加速腐蝕;不過,此類接觸一般會形成“大陽極-小陰極”的原電池,相對“小陽極-大陰極”來說較為安全。
MREMA等對常用的建筑用鋁合金6061-T6的耐腐蝕性能進行了詳細研究。首先通過連續中性鹽霧試驗研究安裝各種緊固件的鋁合金板的電偶腐蝕情況,預腐蝕時間為1000小時。結果表明,緊固件表面處理防腐性能從高到低依次為GEOMET鍍鋅涂層→絕緣襯套→鍍層墊圈(氯乙烯)→未表面處理。對于無保護層的鋁合金6061-T6(鋁板和緊固件均未表面處理),蝕坑最大深度為0.5mm。之后,繼續研究了在含氯環境中,埋置在水泥砂漿中的A6061-T6鋁合金板(9mm厚)的腐蝕行為,采用干濕循環加速腐蝕試驗方法,所有預腐蝕試件的強度幾乎無損。
最后,MREMA等在沖繩的宮古島進行室外暴露試驗,得出結論:1000小時連續鹽霧試驗大概對應于直接大氣暴露試驗的1~3年中的某個時間點。另外,若緊固件進行了GEOMET表面處理,大氣暴露3年后毫無腐蝕。
除鹽霧試驗外,干濕周浸循環和氙燈輻射試驗也是模擬海洋大氣環境的方式。楊浪等對去除氧化膜后的6061-T651鋁合金在模擬工業-海洋大氣環境下的腐蝕進行了研究。通過氙燈老化(59h)和周期浸潤(48h)試驗,經8個循環周期后,鋁合金出現點蝕和晶間腐蝕,其屈服強度和抗拉強度分別降低4.1%和5.6%,這表明試樣的腐蝕沒有對強度造成明顯影響。
馮馳等采用與楊浪等相同的試驗方法研究了不同表面處理下6061鋁合金和30CrMnSiA 結構鋼的電偶腐蝕。腐蝕8個周期后,采用環氧聚酰胺底漆和丙烯酸聚氨酯面漆的復合防護涂層的6061鋁合金強度和塑性損失較小,抗拉強度和斷后伸長率分別下降約6%和5%;而僅采用表面陽極氧化處理的6061鋁合金的抗拉強度和斷后伸長率分別下降了約24.2%和13.4%。該試驗中腐蝕溶液為具有強氧化性的酸性溶液,故大大加快了腐蝕速率,使得強度降低率約為1年青島海洋-工業大氣環境下的4倍;不過該試驗結果是否能夠重現長期暴露試驗中的腐蝕規律也未可知。
為探究加速腐蝕試驗方法的模擬性和加速性,劉明等對比分析了連續鹽霧、循環鹽霧、周期浸泡、周期降雨共四種模式的加速試驗,認為循環鹽霧試驗及周期降雨可較好地模擬瓊海大氣環境下2A12鋁合金的腐蝕規律。
郝美麗等認為通過鹽霧、干燥、濕熱、干燥、浸漬(NaHSO3溶液)的復合循環試驗可用于模擬LY12鋁合金在海南萬寧試驗站的大氣腐蝕行為。
韓德盛等設計了模擬海洋大氣腐蝕的“溶液浸泡-氣氛暴露”加速試驗,且與間歇鹽霧和周期浸泡進行對比,為進一步改進試驗方法提供了參考。因此,模擬加速腐蝕試驗方法需要針對具體的大氣環境進行特定的設計,以更好地重現腐蝕發展規律;但是目前該方面的研究尚無突破性的進展。
3 討論與小結
總的來說,腐蝕試驗是研究金屬腐蝕的主要途徑。室外大氣暴露試驗得到的結果數據真實可靠,最符合實際情況。短期室外大氣暴露試驗的周期較短,能較早地觀察到金屬腐蝕現象,但是只能反映腐蝕初期行為;長期室外大氣暴露試驗能得到更準確、更長時間內的金屬腐蝕行為規律,卻存在人力、物力耗費大和試驗周期長的缺點。從本文搜集的數據來看,試驗周期短則1~2年,長則20年;而過長的試驗周期必然會增加試驗過程中的不可控因素,造成試驗組織困難。
室內模擬加速腐蝕試驗能在實驗室條件下使用設備模擬腐蝕環境,加速腐蝕過程,預測真實大氣環境中的長期腐蝕行為,節約人力、物力,因此成為主要的腐蝕試驗手段。但是目前尚無任何加速試驗能夠準確地重現室外大氣暴露下的自然腐蝕情況。即便如此,室內模擬加速腐蝕試驗仍是研究腐蝕規律不可缺少的一種手段,具有重要意義。
在各種加速腐蝕試驗方法中,鹽霧試驗是模擬大氣腐蝕的最主要方法。不過,單一的連續鹽霧試驗對大氣暴露的模擬性并不好,而以干濕交替為基礎的加速腐蝕試驗則能更好地再現真實大氣環境,其結果更接近自然腐蝕情況。為探究多種腐蝕因素的影響,較準確地模擬金屬的腐蝕行為,學者們開始致力于研究多因子復合循環加速腐蝕試驗,如北京航空材料研究所研制的8因子加速試驗裝置,與自然暴露試驗相比具有良好的一致性。
總而言之,室外大氣暴露試驗仍需持續進行,以完善腐蝕數據庫。室內腐蝕試驗方法的研究方向應考慮多環境因子復合影響,有針對性地設計各類大氣環境下的室內加速腐蝕試驗。
既有鋁合金結構的腐蝕評價
腐蝕試驗能夠根據研究目的靈活設計,更準確地表現出鋁合金的腐蝕特性,但是時間和經濟成本很高。故通過對現有鋁合金結構進行腐蝕程度評定檢測,是一種有效的評價鋁合金結構耐久性的手段。
1 鋁合金結構腐蝕案例分析
相比于建筑結構,鋁合金應用于橋梁結構的歷史更為悠久。鋁合金最早用在橋梁上是在1933年建成的匹茲堡史密斯菲爾德街大橋(圖2),該橋使用鋁制橋面板替換重型鋼木橋面,橋梁自重的降低使橋梁的承載力得到顯著提高。2014-T6鋁制橋面板一直使用到1967年,然后被更耐腐蝕的6061-T6鋁合金橋面板所取代,該橋面板一直使用到1995年。
圖2 史密斯菲爾德街大橋
1983年,ALISON調查了7座鋁合金橋梁服役20~30年后的損傷情況。其中,除加拿大Arvida橋(圖3)外,其余6座橋梁均使用6061-T6和5083-H113鋁合金。通過目測方法調查發現:腐蝕情況很少,大部分結構基本無腐蝕,輕微點蝕也不影響結構的安全性能。因腐蝕損傷而需要維護的只有Arvida橋,該橋建于1950年,位于鄉村地區。由于冰雪季節長(4~5個月),因而附近道路上使用除冰鹽較多,服役環境惡劣。經檢查發現,樹葉、草和泥土進入了箱形柱并聚集在柱底造成排水孔堵塞,致使鋁合金墩柱底部出現剝落腐蝕;且在北部的底部水平橫梁上發現了一些小面積的剝落或分層(圖4a),支撐橋面的梁有微小腐蝕。最主要的腐蝕原因是采用了耐腐蝕性較差的2014-T6鋁合金,且未作任何防腐處理。后采用耐腐蝕性能更好的6061-T51鋁合金對橋墩進行修復(圖4b),并采用6061-T6和6061-T651鋁合金對橋梁橫撐和主梁進行替換。目前該結構已服役近70年,情況良好。
圖3 加拿大Arvida鋁合金橋
圖4 加拿大Arvida鋁合金橋橋墩修復前、后
20世紀60年代,位于紐約長島的兩座鋁合金橋建成通車。服役約20年后,鋁合金結構無腐蝕現象。但是該橋有一個潛在隱患,上部鋁合金結構和下部鋼支座之間直接接觸,在潮濕環境下易發生電偶腐蝕。在1996年的檢查中發現了這一現象,隨后對其進行了維修。
1956年,德國的Schwansbell鋁合金橋梁(圖5)建成,該橋采用AlMgSi1 F32鋁合金,即相當于現在的EN AW 6082-T6鋁合金。為驗證鋁合金橋梁在高腐蝕性工業大氣環境下的耐腐蝕性,該橋表面未作任何表面處理。約服役50年后,除結構表面呈現暗灰色外,各部件的承載力和使用功能均未受到影響,表現出優異的穩定性和耐久性(圖6)。
圖5 德國Schwansbell鋁合金橋
圖6 服役50年后Schwansbell鋁合金橋表面
1961年,日本現存時間最長的鋁合金橋——金慶橋建成(圖7)。該橋位于日本內陸,空氣中鹽分較少,但是環境潮濕,冬季會在道路上使用除冰鹽,所處環境較為惡劣。主體結構自建成后未進行過任何維修。服役56年后,在鋁合金制主梁、腹板、剪刀撐、橫梁以及這些構件的連接部位(焊接、鉚接部位)上出現大范圍細小的腐蝕坑,但腐蝕深度淺,對結構安全沒有影響。
圖7 日本金慶橋
2009年,上海崇明島建成一座鋁合金通信塔(圖8),該塔距海邊僅30m左右。筆者在2019年3月底觀察該通信塔的腐蝕問題,發現結構表面無明顯腐蝕痕跡,連接處也未發現腐蝕跡象,主體結構完好,表明鋁合金結構在近海地區仍表現出很強的耐腐蝕性能。
圖8 上海鋁合金通信塔
近百年的鋁合金結構發展史,充分證明了鋁合金結構在復雜嚴酷環境下良好的耐久性。鋁合金即使未作表面處理,其在海洋大氣環境下的耐腐蝕性也比經表面處理后的鋼材的耐腐蝕性更為優良。在海洋大氣環境中發生的輕微點蝕也基本不會影響結構整體承載力。
考慮到維修養護成本,嚴酷環境下鋁合金比鋼材更具性價比。但是,材料牌號的選取不當、異種金屬的接觸以及連接處縫隙密封不良等情況,均可能導致電偶腐蝕和縫隙腐蝕的發生,必須在設計和施工過程中予以避免。值得慶幸的是,電偶腐蝕通常不會出現在鄉村或非沿海地區的鋁合金結構中。
2 鋁合金結構大氣腐蝕現場檢測方法
開展鋁合金結構腐蝕情況的現場檢測,對于服役結構的安全性評價、檢修具有重要意義。因場地等條件限制,諸多實驗室檢測手段無法應用在現場檢測中,影響了鋁合金結構腐蝕現場檢測的精度和效率。目前鋁合金結構腐蝕檢測的主要項目有外觀檢查、腐蝕深度檢查、腐蝕產物分析和附著鹽分測量等;可采用的手段主要有目視檢測、渦流檢測、超聲檢測、滲透檢測、X射線檢測、電化學檢測等。
目前應用最廣泛、效率最高的就是目視檢測。該方法依賴于工程師的經驗和主觀判斷,無法量化腐蝕程度。本文所涉及的工程案例均采用了此方法來調查結構的腐蝕情況。目視檢測作為最基本的檢測方法,可快速地判斷服役結構的腐蝕外觀,為進一步的檢測提供指導。
因鋁合金獨特的材料性質,局部腐蝕或點蝕是最常見的腐蝕形式。故腐蝕深度是一項重要的檢測項目,可采用渦流檢測、超聲檢測、X射線檢測等方法。除此以外,附著鹽分測量、腐蝕產物分析也在以上工程案例中有所采用,可用來分析大氣腐蝕的起因和類型。
通過腐蝕圖像可分析腐蝕原因、判斷腐蝕類型,對于評定結構腐蝕程度具有重要意義。為此,部分學者開展了基于圖像處理技術的鋁合金腐蝕評價方法。該方法通過對腐蝕圖像進行提取、處理,得到二值圖像特征,最后可據此評定鋁合金的腐蝕等級,是一種應用前景廣闊的現場檢測手段。
3 討論與小結
因傳統觀念中認為鋁合金結構耐腐蝕性強,對于鋁合金結構的防腐和腐蝕評定未給予足夠的重視。然而,既有結構的腐蝕檢測表明,在高腐蝕性環境下,施工中操作不當會引起鋁合金結構的腐蝕,并引發結構安全問題,如加拿大Arvida鋁合金橋。因此,有必要發展鋁合金結構的大氣腐蝕現場檢測技術。
值得一提的是,航空航天領域中關于鋁合金腐蝕的研究更為廣泛和深入,對鋁合金建筑結構腐蝕檢測評定的相關研究具有重要的借鑒意義。但應注意,建筑用和航空用鋁合金結構的腐蝕之間存在巨大的差別,如服役環境、連接形式、材料種類、表面處理技術等。此外,有關鋁合金結構腐蝕等級評價的相關研究尚未見諸報端,需在大量腐蝕試驗和檢測調查的基礎上擴展相關研究。
結 論
(1) 鋁合金自身防腐性能優越,即使未作任何表面處理,其耐腐蝕性也比經表面處理后的鋼材的耐腐蝕性更為優良;但在極端大氣環境和施工操作不當的情況下,仍可能會產生危害結構安全性的腐蝕現象。
(2) 相對于鋁合金牌號的種類繁多,目前國內外對鋁合金的室外大氣暴露腐蝕試驗研究遠遠不足,有必要進行更長時間跨度和更多大氣環境下的腐蝕試驗,以完善腐蝕數據庫。
(3) 室內加速模擬腐蝕試驗方法并不能完全模擬真實環境下的鋁合金腐蝕情況,因此有必要改進和創新室內加速模擬腐蝕試驗方法,以期能夠盡可能地再現真實大氣環境中材料的腐蝕過程,更加準確地預測鋁合金的中、長期腐蝕行為。
(4) 影響鋁合金腐蝕的因素眾多且相互耦合,對腐蝕環境下多因素的鋁合金腐蝕模型的研究還有待進一步開展;電偶腐蝕和縫隙腐蝕造成的危害更為明顯,因此鋁合金連接件的耐腐蝕性能有待深入研究,以得到不同緊固件對鋁合金連接耐腐蝕性能造成的影響。
(5) 大量已建鋁合金結構的調查結果表明,鋁合金具有良好的耐腐蝕性能;但是,材料牌號選取不當、異種金屬的接觸以及連接處縫隙密封不良均可能造成鋁合金的腐蝕,進而影響結構的安全性。
(6) 鋁合金結構大氣腐蝕現場檢測技術和腐蝕評價標準尚未成熟,無法量化腐蝕程度對鋁合金結構服役壽命和承載力的影響。
免責聲明:本網站所轉載的文字、圖片與視頻資料版權歸原創作者所有,如果涉及侵權,請第一時間聯系本網刪除。
相關文章
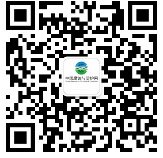
官方微信
《腐蝕與防護網電子期刊》征訂啟事
- 投稿聯系:編輯部
- 電話:010-62316606-806
- 郵箱:fsfhzy666@163.com
- 腐蝕與防護網官方QQ群:140808414
點擊排行
PPT新聞
“海洋金屬”——鈦合金在艦船的
點擊數:8237
腐蝕與“海上絲綢之路”
點擊數:6558