摘要
為滿足不斷攀升的兩機渦輪動力系統的快速發展,表面沖擊強化技術在渦輪轉子用高溫合金表面強化的應用及相應機制的研究受到了廣泛關注。然而,高溫合金表面硬化層在高溫服役環境下的回復、再結晶行為難以避免,由此引起的表面強韌化、抗疲勞效果的退化,成為制約表面沖擊強化技術在先進高溫合金關鍵部件深入應用的瓶頸。本文總結了近年來鎳基高溫合金表面沖擊強化機制及應用研究進展,分析了表面沖擊強化對鎳基高溫合金表面強韌性及抗疲勞的作用規律,探究了高溫合金表面沖擊硬化層在高溫及長期時效過程中的顯微組織、微結構演化及其對高溫穩定性的作用機理。以期為發展鎳基高溫合金表面沖擊強化、提高兩機渦輪轉子疲勞抗力提供基礎。
關鍵詞: 鎳基高溫合金; 表面強化處理; 抗疲勞制造; 硬化層; 組織和性能高溫穩定性
高溫合金具有優異的高溫強韌性、良好的抗氧化和抗熱腐蝕性能、顯著的抗蠕變與抗疲勞性能以及優良的組織結構高溫穩定性,被廣泛應用于航空航天、石油化工等領域關鍵熱端部件的制造[1~4]。其中渦輪動力系統關鍵熱端部件(渦輪盤、渦輪葉片等)被譽為渦輪發動機的心臟,需長時間在高溫、熱腐蝕環境服役。因此,提高渦輪轉子關鍵熱端部件用高溫合金的高溫性能,始終是渦輪動力系統能效躍升、服役安全的核心保障[5,6]。隨著高端航空發動機、重型燃氣輪機研制技術的飛速發展,高品質渦輪轉子用高溫合金,更需在長期高溫、疲勞環境下面臨“高溫強韌化”和“性能穩定性”的雙重考驗[7]。而強韌化設計與微結構熱力學往往相互制約[8~10],成為先進渦輪系統研發的瓶頸之一[11]。
近年來,高能噴丸(shot peening,SP)、表面高速機械擠壓(high-speed surface extrusion,HSE)、超聲表面滾壓(ultrasonic surface rolling process,USRP)和激光沖擊(laser shocking processing,LSP)等表面沖擊強化技術在兩機渦輪轉子抗疲勞制造領域的應用研究廣泛深入地展開,顯現出積極的效果和廣闊的前景[12~14]。表面沖擊強化通過在金屬表層引入可觀的塑性變形和殘余壓應力,誘導高密度位錯、孿晶等表面微結構的改變[15~17],從而獲得具有顯著綜合強化效果的梯度硬化層,有望成為高強金屬材料有效的表面抗疲勞制造技術[16~21]。
然而,表面沖擊強化在金屬表面獲得的高殘余壓應力硬化層[15],仍以垂直表面向內的沖擊形變強化為主[12,15,17]。硬化層在劇烈塑性變形(severe plastic deformation,SPD)時產生的高密度位錯、晶格畸變和亞穩界面,使表層獲得可觀殘余壓應力、顯著強化效果的同時,也在表面引入了缺陷密度梯度分布的微結構亞穩層[18]。而對高溫合金而言,600℃甚至以上的高溫條件下,硬化層中的亞穩微結構易發生回復和退化,導致殘余壓應力的松弛甚至消失。這直接影響高溫合金表面沖擊硬化層高溫強化作用的穩定性,也一直是制約表面強化技術在高溫合金渦輪轉子表面強韌化、抗疲勞制造中深入應用的瓶頸性問題[12,13],長期受到設計、制造和研究者的廣泛密切關注。
迄今為止,關于高溫合金表面沖擊強化的諸多實際應用和研究報道中,表面硬化層高密度亞結構的回復推遲、殘余壓應力可保留的機理尚不明確。本文歸納了鎳基高溫合金表面沖擊強化技術及應用的研究進展,在分析不同表面沖擊強化技術提升鎳基高溫合金表面強韌性及抗疲勞作用規律的基礎上,結合近年來本課題組的研究結果,探究了高溫合金表面硬化層在高溫下的顯微組織、微結構演化機理。分析高溫下維持表面強化作用的關鍵機制,展望鎳基高溫合金新型表面沖擊強化技術和抗疲勞調控機制的未來發展方向,以期為具有更高承溫能力的鎳基高溫合金關鍵渦輪轉子強韌化與抗疲勞制造提供思路和參考。
1 高溫合金的表面噴丸處理及噴丸強化
渦輪動力系統的高溫合金關鍵熱端部件,裝機前需經多道次復雜機械加工,構件表面完整性易被破壞,表面粗糙度增大。加之機械加工難以避免在表層引起殘余拉應力等,從而劣化了高溫合金的高溫疲勞性能[22]。尤其對于渦輪轉子,其在長期服役過程中的高溫抗疲勞性能,更是動力系統服役安全的關鍵[23,24]。因此,諸多金屬材料的表面強化技術在高溫合金轉子構件的抗疲勞制造領域倍受關注[23~25]。表面噴丸處理,作為便于實施、低成本和沖擊能量輸入可準確調控的表面處理技術,較早被用于高溫合金的表面強化[26,27]。噴丸處理采用硬質鋼丸、鑄鐵丸、陶瓷丸等轟擊工件表面,在表層引入殘余壓應力,可有效抵消機械加工的表面殘余拉應力,提高材料的抗疲勞能力[28~31]。噴丸處理對高溫合金構件的影響主要有:硬化層殘余應力分布狀態、表面形態和疲勞裂紋萌生阻力等[13,28]。
1.1 高溫合金噴丸處理后的表面應力狀態及分布
高溫合金表面噴丸強化的研究[29~31]表明,噴丸處理可明顯改變機械加工的殘留表面拉應力,在合金表面引入了較為理想的殘余壓應力層,這對高溫疲勞抗力要求很高的高溫合金渦輪轉子,無疑具有高的實用價值。鐘麗瓊等[28]的研究發現,對FGH97合金進行陶瓷彈丸90°噴射4 min處理后,次表層(距表面幾十微米)處獲得了較高的殘余壓應力,應力場深度可達280 μm左右。Wang等[30]對FGH96合金進行了車削、陶瓷噴丸和復合噴丸(高強鑄鐵彈丸和低強陶瓷彈丸)殘余壓應力場的對比研究,發現噴丸處理明顯增加了表層殘余壓應力,并且應力最高值、深度均隨噴丸強度的增加而增大(圖1[30])。在鑄造高溫合金、變形高溫合金的相關研究中也獲得了相似的效果。K4169鑄造高溫合金噴丸處理后表面殘余壓應力由258 MPa增加至1079 MPa,進而顯著提高了合金的疲勞壽命[32]。
免責聲明:本網站所轉載的文字、圖片與視頻資料版權歸原創作者所有,如果涉及侵權,請第一時間聯系本網刪除。
-
標簽: 鎳基高溫合金, 表面強化處理, 抗疲勞制造, 硬化層, 組織和性能高溫穩定性
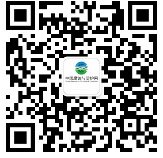
官方微信
《腐蝕與防護網電子期刊》征訂啟事
- 投稿聯系:編輯部
- 電話:010-62316606
- 郵箱:fsfhzy666@163.com
- 腐蝕與防護網官方QQ群:140808414