本文介紹了某石化公司煉油廠精制車的兩臺原料污水罐經檢測均發現存在嚴重的氫鼓包并伴有裂紋產生,通過對其檢測結果分析最終確定導致該類失效發生的原因是碳鋼材質處于濕硫化氫腐蝕環境下發生的氫鼓包,當鼓包內聚集的氫氣壓力超過了材質的承受極限,會使鼓包發生破裂產生裂紋。此外該罐使用雜質、夾層過多的 A3F 鋼、犧牲陽極塊的安裝位置不當、防腐涂層的破損脫落等因素也促成了失效的發生。
某石化公司煉油廠精制車間有兩臺原料污水罐,容積 3000m,其主要參數如下:材質:A3F;規格:φ18500×14406×5/6/7/8/9mm; 操作壓力為常壓,操作溫度常溫,內部介質為原料污水。
2012 年 10 月,我單位對該裝置位號為 G-2 的污水罐進行了全面檢驗,1金相、硬度測定等,通過檢驗,發現該罐存在嚴重的腐蝕問題——一帶板罐內壁存在 56 處鼓包并伴隨有裂紋發生。2014 年 9 月,我單位受委托對位號為 G-1 的污水罐進行了檢驗,主要采取的檢測手段為宏觀和測厚,發現的部分缺陷部位進行了表面滲透探傷。通過本次檢驗,發現該罐的一帶板內壁同樣存在局部鼓包并伴隨有裂紋缺陷的問題,且缺陷形貌與 G-2 非常相似。通過對該裝置在檢測過程中發現缺陷的兩臺原料污水罐進行比較,發現這兩臺儲罐的規格、材質、工況和介質都相同,缺陷形貌也基本一致,因此可以初步判斷導致這兩臺罐發生失效的機理相同。鑒于這一缺陷系重復發生于同一裝置同種工況的同類設備中,對車間的安全生產帶來了很大的安全隱患,因此在本文中,我們將對該類設備失效原因進行分析討論,找出導致失效發生的主要影響因素,為車間防止類似腐蝕失效再次發生提供解決方案。
一、檢驗情況
1.宏觀檢驗
對 G-1 進行宏觀檢驗,發現該罐罐壁的一帶板和三帶板上安裝的陽極塊固定支架普遍發生斷裂的問題。在罐壁一帶板安裝的陽極塊下部發現有14 處存在局部鼓包的問題,且多數鼓包處上部伴隨有肉眼可見的裂紋,見圖1,裂紋既有橫向裂紋也有縱向裂紋,且多數裂紋存在不規則十字交叉。
圖1 G-1罐內壁某處氫鼓包伴有裂紋圖示
2.滲透檢測
對鼓包及其周圍部位進行滲透檢測,發現鼓包處基本都伴隨有裂紋產生,裂紋的具體形貌見圖 2 所示。對鼓包部位進行打磨削平,發現在一定的厚度范圍內裂紋的長度越來越長,有時會有新的裂紋出現。從滲透檢測的結果分析,可知鼓包處的材質已經發生了明顯的裂化。
圖2 罐內壁某處鼓包處滲透檢測結果圖示
3.壁厚檢測
對鼓包部位進行壁厚檢定,鼓包處所測壁厚范圍在 4.3mm~6.5mm 之間,其附近未發生鼓包的所測壁厚均在 9.2mm 以上,鼓包部位僅有正常壁厚一般左右,且鼓包內外未見明顯的局部腐蝕,分析鼓包部位由于發生分層導致所測壁厚減小。
4.金相組織分析
對原料污水罐 G-2 母材和裂紋處分別選取一點進行金相組織分析,圖 3是母材處的金相組織,該部位的金相組織為鐵素體 + 珠光體組織。圖 4 是某條裂紋處的金相組織,其為鐵素體+ 珠光體,并伴隨有沿晶裂紋。
圖3 G-2罐內壁母材處的金相組織圖
圖4 G-2罐內壁某處裂紋處的金相組織圖
5.硬度測試
對 G-2 罐的母材和鼓包處進行了硬度檢測,母材的硬度值范圍在147 ~ 155HB 之間,而發生鼓包部位的硬度值范圍在 120 ~ 125HB 之間。分析硬度檢測的結果,發現鼓包處的硬度值低于母材部位的硬度值。
二、腐蝕發生原因
1. 工作介質原因
污水罐的內部介質為原料污水,其介質組成比較復雜,介質中主要含有原油、硫化物、無機鹽、有機酸等多種腐蝕組分。其中硫化物又分無機硫化物和有機硫化物。無機硫化物主要是硫化氫,易溶于水呈酸性,具有很強的腐蝕性。無機硫化物主要有硫醚、二硫醚化碳等,也具有一定的腐蝕性。由于污水罐的操作溫度為常溫,處于濕硫化氫腐蝕的敏感溫度范圍,容易造成濕硫化氫腐蝕。碳鋼和低合金鋼在濕硫化氫環境中發生氫鼓包和氫致應力腐蝕的案例非常普遍。
2. 電化學因素
分析本文中 2 臺原料污水罐氫鼓包發生的位置,發現所有氫鼓包均發生在罐壁一帶板的陽極塊正下方。綜合分析該罐的介質、溫度等工藝參數,可知該罐內部為濕硫化氫環境。其腐蝕機理為,H 2 S 在水中發生電離,電離公式為:
H 2 S → 2H + +S 2-
電離后,使得原料污水罐的介質呈酸性,會對罐壁產生腐蝕作用。為了防止罐壁發生腐蝕,對該罐實施了涂層防護和犧牲陽極陰極保護的防腐策略。陽極塊選用 Zn 塊,罐壁為陰極,構成了一個原電池。
在陽極發生陽極反應:
Zn-2e → Zn 2+
在安裝陽極塊的周圍,發生陰極反應:
2H + +2e → 2H
隨著電化學反應的持續進行,會在陽極附近產生大量的 H 原子,聚集在罐壁表面的氫原子,被罐壁吸附,會向鋼板中滲透,遇到夾層、夾雜物等顯微缺陷,就會聚集結合成氫分子。由于氫分子體積大,不能在金屬內部擴散,于是就在缺陷處不斷聚集,使缺陷內部的氫氣壓力不斷增加,當壓力超過金屬的屈服強度時,就會使金屬產生局部塑性變形,最終導致金屬表面凸起而形成氫鼓包。隨著電化學反應的持續進行,氫鼓包內氫氣壓力不斷增加,會使鼓包不斷擴大,最終使表面發生扯裂。
3. 材質的因素
碳鋼和低合金鋼因鋼板軋制問題,容易在板厚的中部產生夾層、夾雜物偏析聚集帶等顯微缺陷,當使用含有此類材質缺陷的設備在使用過程中如果發生滲氫,會便于氫氣在顯微缺陷處不斷聚集,導致氫鼓包的發生。本文中的兩臺罐的材質均是A3F沸騰鋼,該種鋼的純凈度不夠,鋼內夾雜物多。
4.腐蝕原因初步分析
首先,在普通酸性條件下,鋼的表面的氫原子會形成分子氫氣,并且,假如它們是以很慢的腐蝕速率產生的,那么它們會被無害地耗散掉。但是,當存在硫化物垢膜時,硫化物會成為負催化劑,對反應有促進作用。結果,原子氫滲透進入鋼材,并在晶體結構中聚集起來,從而影響鋼的機械特性。其它化合物,如硫化物、氫氰酸、磷,被叫做重組抑制劑或者催化劑毒物,它們阻礙原子氫轉化成分子氫。存在催化劑毒物時,原子氫的表面濃度升高,相應地增加了擴散進入鋼材的氫的總量。其次,分析鼓包發生的位置,發現本次發現的所有鼓包均發生在罐壁 1 帶板陽極塊的正下方。這是因為該處是電化學反應的活躍區域,陽極塊作為原電池的陽極隨著電化學反應的不斷進行不斷消耗,陽極塊附近的罐壁作為陰極附近發生陰極反應,產生大量的氫原子并在陽極塊附近聚集,致使陽極塊的附近的氫原子濃度遠高于其它部位。再次,檢查發現本文中兩個罐的陽極塊的安裝位置過于靠近罐壁,不符合相關標準中陽極塊與罐壁的安裝距離不小于 50mm 的規定,陽極塊與罐壁的距離過近也加劇了氫原子滲入罐壁的過程。此外,觀察發現罐壁靠下部的幾帶板的防腐涂層發生嚴重的脫落破損,由于缺少了防腐涂層這一層保護,使得產生的氫原子更容易滲透入罐壁的過程。
本次檢驗過程中,罐底板及罐壁安裝有陽極塊的下部及其它位置未檢出有鼓包存,尤其是罐壁 2 帶板及 3帶板也均裝有陽極塊, 但未發現有鼓包存在。針對該問題,我們將在今后的工作中展開進一步的研究討論。
三、結論
本文從多角度對某煉油廠精制車間的兩臺原料污水罐出現的嚴重氫鼓包并伴隨有裂紋性缺陷這一問題進行了分析,初步確定導致該類失效發生的原因是罐壁材質處于濕硫化氫腐蝕環境下產生的氫原子不斷滲入材質并聚集形成氫氣,隨著電化學反應的持續進行,在雜質、夾層處聚集的氫氣壓力不斷增加,會產生氫鼓包,當壓力超過了材質的承受極限,會使鼓包發生破裂產生裂紋。此外,使用雜質、夾層過多的 A3F 鋼、陽極塊的安裝位置不當、防腐涂層的破損脫落等一系列因素更加劇了上述過程的發生。
在今后工作中,針對本文兩臺儲罐發生的問題繼續跟蹤研究,主要從防腐涂層種類的選擇、陽極塊的種類、安裝的布局和位置參數等方面進一步驗證和優化,并在下一次檢驗過程中重點關注其它位置是否存在不同程度的鼓包問題,通過相關工作的開展,力求找到導致本文問題發生的根本原因。
● 作者簡介
魏盛斌,男,1963 年 3 月出生,1984 年 7 月畢業于重慶大學工程物理專業,本科學歷,于 1984 年 7月分配到烏魯木齊化工總廠監測中心工作至今,先后從事理化檢驗、鍋爐、壓力容器、壓力管道的現場檢驗工作和設備管理。1991 年被聘為理化檢驗工程師,2002 年被烏石化總廠聘為監測中心高級工程師,2005 年任監測中心副總工程師兼任容檢科科長,2009 年 4 月任烏石化公司監測中心副主任,2010 年 7 月任烏石化公司設備檢驗檢測院副院長。
近年來,主持參與多項烏石化公司的科技公關項目,獲得烏石化公司科技進步二等獎 2 項,技術改進項目二等獎 4 項,發表科技論文 5 篇。
免責聲明:本網站所轉載的文字、圖片與視頻資料版權歸原創作者所有,如果涉及侵權,請第一時間聯系本網刪除。
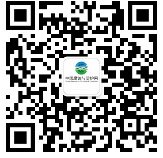
官方微信
《腐蝕與防護網電子期刊》征訂啟事
- 投稿聯系:編輯部
- 電話:010-62316606-806
- 郵箱:fsfhzy666@163.com
- 腐蝕與防護網官方QQ群:140808414