應力腐蝕開裂(SCC)是輕水堆核電站結構材料常見的環境損傷模式之一。研究發現[1,2,3],SCC是由敏感的材料結構、腐蝕性介質和應力共同加速作用下造成的一個裂紋由局部缺陷萌生到緩慢穩態擴展的過程,材料、水化學和應力是影響高溫高壓水環境中材料SCC的三個主要因素,而腐蝕是SCC發生的基本過程[4]。腐蝕產物膜(氧化膜)的結構和成分與SCC的萌生和擴展過程密切相關,研究氧化膜的結構與成分能夠揭示腐蝕的動力學過程和機制,從而為闡明SCC的機理提供基礎。在所有影響材料腐蝕行為的因素中,材料表面狀態是一個重要因素。目前關于表面狀態對奧氏體不銹鋼和鎳基合金在高溫高壓水環境中腐蝕行為的影響已進行了大量研究[5,6,7,8],發現了材料的機加工表面、打磨表面、機械拋光表面和電解拋光表面等具有不同的腐蝕行為。S.Cissé等報道了模擬壓水堆(PWR)一回路水環境(340℃,500h)和蒸汽環境(400℃,500h)中,打磨態304L不銹鋼表面形成的氧化膜比機械拋光態的薄[9]。關于電解拋光的研究,學者[6,7]主要從去除表面殘余應變層的角度解釋了電解拋光對不銹鋼和鎳基合金在高溫高壓水中腐蝕行為的影響。Ziemniak[6]認為高溫高壓水的溫度小于臨界溫度(374.15℃,22.1MPa)時,304不銹鋼電解拋光表面的腐蝕速率比機械拋光表面的低。盡管很多學者已經對電解拋光態鎳基合金在高溫高壓水中的氧化行為進行了研究,但是關于電解拋光工藝引起的表面成分改變對高溫高壓水環境中材料腐蝕行為的影響還鮮見報道。近期研究發現,電解拋光會提高600合金表面的鉻含量[8],在高溫高壓水中形成保護性較好的氧化膜,從而抑制腐蝕。由于電解拋光工藝可能造成材料表面的成分改變,進而影響材料的腐蝕行為,因而拋光工藝可能是影響材料腐蝕行為的重要因素。本工作在前期工作基礎上[8],針對不同電解拋光態600合金在壓水堆一回路水中的腐蝕行為進行研究,探討不同電解拋光工藝對材料腐蝕行為的影響及其機理。
1 試驗
1.1 試樣
試驗用材料為軋制退火態600合金。其化學成分(質量分數)為:wCr15.57%, wFe9.50%, wTi0.28%, wMn0.22%,wSi0.12%, wNb<0.05%,wC0.065%, wP0.007%, wS0.002 1%,余量為鎳。試樣尺寸為10mm×10mm×1mm,用SiC水砂紙將試樣表面逐級打磨至2000號,再用金剛石研磨膏拋光到0.5μm,最后采用兩種工藝對試樣進行電解拋光:(1)電解液成分(體積分數,下同)為15%硫酸+64%磷酸+21%水,電解溫度為70℃,電流密度為0.2A/cm2,拋光時間為30s(經此種工藝拋光的表面以下簡稱EPS-1);(2)電解液成分為30%硝酸+70%甲醇,電解溫度為0℃,電壓為3V,拋光時間為10s(經此工藝拋光的表面以下簡稱EPS-2)。電解拋光后,試樣依次在酒精-丙酮混合液和純水中超聲清洗,吹干后放入干燥皿中保存。
1.2 高溫高壓水腐蝕試驗
高溫高壓水腐蝕試驗在配有動態循環水回路、容積3L的316不銹鋼高壓釜中進行,試驗溫度為320℃,壓力為13MPa。試驗溶液模擬PWR一回路水溶液,含1000 mg/L B(以H3BO3加入)和2mg/L Li(以LiOH加入),室溫下溶液pH為6.398,325℃高溫下溶液pH約為7.25[10]。試驗前,向回路水罐中通高純氮氣去除水中的溶解氧,使水中溶解氧質量濃度<5mg/L。將試片置于高壓釜中,進行浸泡試驗,試驗時間分別為1,5,25,120,500h。
1.3 樣品分析
腐蝕試驗前,采用配有2keV氬離子濺射功能的ESCALAB 250型X射線光電子能譜(XPS)分析兩種電解拋光初始表面產物膜的成分和結構。腐蝕試驗后,采用XPS分析試樣表面腐蝕產物膜厚度方向的成分和結構,采用配有能譜分析系統(EDS)的FEI XL30型環境掃描電子顯微鏡(ESEM)觀察樣品表面的腐蝕產物形貌。XPS分析過程中采用Ar+對氧化膜進行濺射,據文獻[11]介紹,不同氧化物之間,比如尖晶石結構的Fe3O4和FeCr2O4濺射速率差異很小,參考標準Ta2O5樣品,濺射速率約為0.1nm/s。為保證XPS分析準確性,Ar+濺射區域直徑約2mm,而XPS分析區域直徑約0.5mm。鉻、鎳、鐵等元素的含量由元素峰面積乘以各元素的敏感性因子得出。采用XPSpeak4.1軟件進行分峰處理,以得到各元素價態及其所占百分比。采用C1s峰值285eV作為標準校正峰偏移。
2 結果與討論
2.1 產物膜的XPS
經不同電解工藝拋光后獲得的600合金初始表面元素隨濺射深度變化的XPS分析結果見圖1。由圖1可見,兩種電解拋光工藝都促使表層富鉻,EPS-1的Cr/(Ni+Fe)原子比大于EPS-2的,說明EPS-1富鉻程度高。從圖1(b)和圖1(c)可知,兩種工藝拋光后表面都形成了雙層結構的超薄產物膜,表層主要為氫氧化物,次表層主要為氧化物,這與文獻[12,13]一致。但兩種表面的產物膜成分與厚度存在差異。其中兩種產物膜表層的Cr(OH)3含量相近,EPS-1為32.1%(原子分數,下同),EPS-2為33.2%,但EPS-1中Ni(OH)2的含量大于EPS-2中的,分別為51.7%和36.5%。次表層氧化物的組成和成分也不同,其中EPS-1中的氧化物含量略高于EPS-2中的,由32.6%Cr2O3、7.5%NiO、3.8%Fe3O4或Fe2O3等組成,而EPS-2由24.5%Cr2O3、6.8%NiO組成。由氧化物含量的半峰高可以判斷,EPS-1的產物膜比EPS-2的厚,EPS-1約為5.6nm,而EPS-2約為2.1nm,如圖1(b)和(c)所示。需要注意,圖1所示產物膜中單質態金屬的存在可能是由于Ar+濺射的不均勻性以及XPS分析厚度超過產物膜厚度所致[14]。
圖1不同電解工藝拋光后600合金初始表面產物膜的XPS結果
Fig.1 XPS results of the films on the surface of alloy 600after different electropolishing processes:(a)depth profile of the atomic ratio of Cr/(Ni+Fe)for EPS-1and EPS-2;(b)and(c)composition depth profiles of Cr,Ni and Fe for EPS-1and EPS-2
2.2 腐蝕試驗
2.2.1 氧化膜形貌
兩種拋光工藝均能在試樣表面形成雙層結構的氧化膜,即連續致密的內層和由分散的顆粒狀或針狀氧化物組成的外層。試樣在晶界處存在凸起或溝壑,這是由于電解拋光工藝所致,并非腐蝕后形成的。由圖2(a)可見,試樣經過25h腐蝕試驗后,樣品表面形貌與原始形貌幾乎相同,只有極少的小顆粒形成;經120h腐蝕試驗后,EPS-1形成稀疏分布的小顆粒和針狀氧化物;經500h腐蝕試驗后,氧化膜外層的氧化物尺寸和密度都明顯增加,其中顆粒狀氧化物大小不均,小顆粒約幾百納米,大顆粒約5μm,針狀氧化物長度約3μm。由圖3可見,EPS-2具有相似的腐蝕行為,經500h腐蝕試驗后,EPS-2形成的顆粒狀氧化物分布密集,尺寸小,僅有幾百納米,針狀氧化物尺寸比EPS-1的小。
2.2.2 氧化膜厚度與成分
圖4中y軸代表鐵、鉻、鎳、氧四種元素的相對含量,其中,氧元素含量是氧元素占三種金屬元素和氧元素總和的原子比。由圖4和圖5可見,經不同拋光工藝拋光后,表面氧化膜具有不同的厚度(從氧的半峰高估計出氧化膜厚度)和化學成分。隨著腐蝕時間的延長,兩種氧化膜的厚度都增加,且EPS-1氧化膜的厚度比EPS-2的厚。腐蝕時間從1h延長到500h,EPS-1表面氧化膜的最高鉻含量分別為4 3.4%,34%,33.2%,35.7%,34.3%,而EPS-2表面氧化膜的最高鉻含量分別為47.5%,37.3%,42.7%,39.6%,31.2%。兩種表面中的鉻含量都在1h腐蝕試驗后達到最大,EPS-1中的最高鉻含量隨腐蝕時間的延長基本不變,而EPS-2則逐漸降低。氧化膜外層富含鎳和鐵,而內層富鉻,說明氧化膜外層可能是Ni-Fe氧化物,而內層可能是Ni-Cr-Fe氧化物。
圖2 EPS-1經不同時間腐蝕試驗后的表面形貌
Fig.2 Surface morphology of EPS-1after corrosion for different times
圖3 EPS-2經不同時間腐蝕試驗后的表面形貌
Fig.3 Surface morphology of EPS-2after corrosion for different times
圖4兩種電解拋光后600合金經不同時間腐蝕后形成產物膜厚度方向的XPS成分分析結果
Fig.4 XPS composition profiles of the oxide scale formed in EPS-1and EPS-2for different corrosion times
由圖6(a)和圖6(b)可見,在腐蝕前期,兩種氧化膜的表面主要會形成鉻的氧化物,這與文獻一致[15]。兩種表面膜的區別在于各組分的含量不同。對未濺射表面進行價態分析發現,EPS-1中的氫氧化物含量高于EPS-2的,尤其是Ni(OH)2的含量,EPS-1中的Ni(OH)2含量為23.4%,EPS-2中的為13.9%。而氧化物中的Cr3+含量基本相同,EPS-1中為14.1%,EPS-2中為13.7%。濺射15s后得到兩種表面膜的次表面,其氫氧化物含量明顯比未濺射表面的低,都小于10%。但EPS-1中的氫氧化物含量仍比EPS-2中的高,而氧化物中的Cr3+含量都明顯增加,但EPS-1中的低于EPS-2中的,分別為31.9%和40.1%,而Ni2+含量相差不大,分別為9.7%和6.1%。對于EPS-1,其氫氧化物中的Cr含量占25%,而EPS-2中約為13%。隨濺射時間增加,氫氧化物消失,剩下富鉻的氧化物。
圖5 EPS-1和EPS-2兩種氧化膜厚度隨腐蝕時間的變化曲線
Fig.5 Thickness of the oxide scales in EPS-1and EPS-2as a function of corrosion time
腐蝕500h后,兩種拋光表面形成的氧化膜價態分布不同,如圖6(c)和(d)所示,但都為兩層結構,即富鉻內層和由氫氧化物和氧化物組成的幾乎不含鉻的外層。EPS-1的內層氧化物中Cr3+的原子分數為47.7%,而EPS-2是58.1%,比EPS-1的高,這與圖4(i)和(j)中鉻元素占比較低相反。需要說明的是,在氧化膜中起保護作用的是Cr3+而不是Cr,因此Cr3+占比更能反映出氧化膜保護性的差異。另外,由于Ar+濺射過程是一個宏觀均勻過程,因此XPS數據同時包含內層氧化膜和外層顆粒的信息。在腐蝕初期,氧化物顆粒的尺寸和密度都很小,可以認為得到的都是內層氧化膜的信息。在腐蝕后期,外層氧化物的尺寸和密度都不可忽略,因此圖6是一個綜合了氧化膜內層和外層的分析結果。
2.3 討論
2.3.1 電解拋光初始產物膜
經不同電解拋光工藝形成的表面產物膜具有不同的成分和結構。研究表明[16,17],電解拋光形成產物膜的成分和結構不僅跟基體材料的性質有關,還跟電解拋光工藝有關。電解拋光可能會造成鐵、鎳的優先溶解,從而形成富鉻產物膜[8]。M.Datta[18]研究純鐵在磷酸-硫酸溶液中電解拋光時,發現向溶液中增加Fe3+會明顯改變表面產物膜結構,這是由于電解拋光過程中會在樣品表面形成一層鹽膜,改變電解拋光液成分會改變鹽膜的性質,從而改變表面氧化膜結構。因此,本工作中所采用的兩種拋光溶液在電解拋光過程中會形成兩種性質的鹽膜,影響電解拋光過程,從而形成兩種性質的表面,即EPS-1和EPS-2。電解拋光形成產物膜的具體結構,不同研究者有不同的表述[13,17,18]。Maurice[12]發現316不銹鋼電解拋光表面產物膜的組成復雜,這與電解拋光條件有關,并與本工作結果一致,即都是由氫氧化物和氧化物組成。如前文論述,EPS-1形成的產物膜比較厚,且氫氧化物尤是Ni(OH)2的含量高于EPS-2中的。
圖6兩種電解拋光后600合金經不同腐蝕時間后形成產物膜厚度方向的元素價態分布
Fig.6 Composition depth profiles of Ni,Cr and Fe ions in the oxide films in EPS-1(a,c)and EPS-2(b,d)after 1h(a,b)and 500h(c,d)exposure
2.3.2 高溫高壓水中的腐蝕行為
在高溫高壓水中,兩種電解拋光工藝產生的表面成分和結構不同的初始表面膜會轉變為成分和結構有差異的產物膜。首先,在高溫高壓水中,氫氧化物的存在,會使表面膜不夠致密,保護性差。氧化物在高溫高壓水中會發生溶解,其過程可能是先與水反應生成氫氧化物,然后通過氫氧化物溶于水中[19]。由于鎳的溶解速率比鉻的快[20],因此Ni(OH)2可能會在高溫高壓水中優先溶解,形成不致密的氧化膜。文獻[21]報道,由于Ni(OH)2的存在,600合金在一回路水環境中形成的氧化膜的保護性較差。另外,由于氧化膜中鉻的氧化物占主要部分,因此Cr(OH)3的溶解速率較慢。具體反應[19]如下:
也有文獻認為,在內表層氧化物晶界處形成的氫氧化鉻可能成為元素快速擴散的通道[7,19],增加了腐蝕速率。其次,氧化膜內層的鉻含量是影響高溫高壓水腐蝕的重要因素。Machet[15]研究了600合金在325℃時的短期腐蝕行為,認為原始表面存在的氫氧化物會發生脫羥基反應生成晶態氧化物,其化學反應如下:
文獻[20]認為,在高溫高壓水中,由于鎳、鐵等元素在氧化膜中的擴散速率比鉻的快,因此鎳、鐵等元素也有可能以離子形式溶解在水中,在氧化膜中留下空位,氧填補這些空位向內擴散,在界面處優先與鉻發生反應生成Cr2O3[21,22],形成富鉻氧化膜。也有文獻認為,基體氧化過程中,鉻優先于鎳、鐵與氧發生反應,在初始表面形成一層具有保護性的Cr2O3膜[19,20]。文獻[19]指出,在低溶解氧條件下,Cr2O3會穩定存在,并對基體起保護作用,而在高溶解氧條件下,Cr2O3不穩定,鉻會快速溶解,腐蝕速率加快。因此在DO<5mg/L條件下,Cr2O3的存在會對基體起到保護作用。
綜上可知,兩種電解拋光表面的初始膜中鉻含量和氫氧化物含量不同,尤其是Ni(OH)2含量不同,會導致在高溫高壓水中形成的氧化膜中鉻含量和氫氧化物含量不同,進而產生不同的高溫高壓水腐蝕行為。如圖1(b)和(c)、圖6(a)和(b)所示,EPS-1初始表面膜中鉻含量與EPS-2相近,但氫氧化物多,不夠致密。而EPS-2中氫氧化物尤其是Ni(OH)2含量少,在高溫高壓水中生成的氧化膜比EPS-1的致密,各元素在氧化膜中擴散速率較慢,可形成含鉻量高的氧化膜。經1h腐蝕試驗后EPS-1氧化膜中的最高鉻含量雖然從初始狀態的約35%增加到45%,但其中氧化物中的Cr3+含量基本不變(從32.6%到31.9%)。另一方面,EPS-2初始表面膜中鉻含量略低,氫氧化物少,經1h腐蝕試驗后最高鉻含量從約35%增加到約50%,其中氧化物中Cr3+含量從24.5%增加到40.1%,高于EPS-1,在隨后的高溫高壓水腐蝕中,表現出更好的保護性。
在高溫高壓水中,兩種電解拋光表面腐蝕行為類似,但腐蝕動力學有差異,EPS-1的腐蝕程度大于EPS-2的。腐蝕試驗后觀察到兩種電解拋光表面形成的氧化膜都呈雙層結構,這與文獻報道一致[5,6,7,8,9,23]。外層為富鐵、鎳大顆粒氧化物,內層為富鉻氧化物,并且尖晶石結構氧化物的化學組成具有非化學計量比的特點[11]。疏松的外層對基體沒有保護作用,內層可以阻止基體進一步被氧化,控制著基體的腐蝕速率。外層大顆粒氧化物的生長主要通過溶解/沉積機制而形成,氧化膜內層是由氧通過氧化膜向基體側擴散與基體金屬反應形成[7,11,15]。EPS-1與EPS-2形成的氧化膜主要差別在于內層。EPS-1氧化膜內層由于Cr3+含量低,保護性較差,具有較快擴散速率的鎳、鐵離子更容易通過氧化膜擴散到溶液中,再以沉積機制在氧化膜表面形成分散的顆粒狀、針狀氧化物,氧也更容易通過氧化膜擴散到氧化膜/基體界面,與金屬原子反應,使氧化膜內層向基體側生長。而EPS-2形成富鉻程度高的氧化膜,保護性好,各種離子在氧化膜中擴散速率相對較慢,形成較薄的氧化膜。從圖5中鉻價態分布上可以推斷,EPS-1形成的內層氧化膜可能是由氧化物和少量氫氧化物混合組成的,而EPS-2可能是由氧化物組成的。文獻[7,21]指出,氧化膜中的氫氧化物可能會提供離子快速擴散的通道從而導致腐蝕速率增加,因此EPS-2形成的氧化物致密性可能更好。
3 結論
(1)電解拋光工藝對鎳基600合金表面成分與結構有明顯影響,與EPS-2相比,EPS-1所采用的電解拋光工藝形成氫氧化物含量高且厚度大的產物膜。
(2)EPS-1與EPS-2初始表面成分與結構的不同會對高溫高壓水環境的腐蝕產生影響。氫氧化物含量高的EPS-1表面膜在高溫高壓水中轉變為致密性差、富鉻程度低的氧化膜,各離子在該氧化膜中擴散速率快,增加了氧化反應速率,形成較厚的氧化膜。
免責聲明:本網站所轉載的文字、圖片與視頻資料版權歸原創作者所有,如果涉及侵權,請第一時間聯系本網刪除。
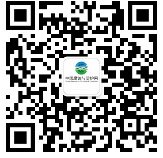
官方微信
《腐蝕與防護網電子期刊》征訂啟事
- 投稿聯系:編輯部
- 電話:010-62316606-806
- 郵箱:fsfhzy666@163.com
- 腐蝕與防護網官方QQ群:140808414