在壓水堆(PWR)核電廠中,蒸汽發(fā)生器(SG)的特殊結(jié)構(gòu)使得二回路系統(tǒng)腐蝕產(chǎn)物或金屬氧化物等雜質(zhì)極易在蒸汽發(fā)生器二次側(cè)發(fā)生沉積,尤其在管板、管束支撐板的縫隙處及換熱管表面,而雜質(zhì)的沉積會嚴(yán)重影響換熱管的傳熱效率和使用壽命[1]。腐蝕結(jié)垢問題已成為影響SG性能的一個重要問題。國際上通常采用全揮發(fā)處理法降低二回路設(shè)備材料的腐蝕,但是,隨著核電站運行時間的延長,難免有腐蝕產(chǎn)物進(jìn)入SG沉積結(jié)垢。為解決這一問題,美國電力研究院(EPRI)開發(fā)了向二回路冷卻劑中添加分散劑聚丙烯酸(PAA)的方法用于減緩腐蝕產(chǎn)物的沉積。研究表明,當(dāng)PAA的質(zhì)量濃度達(dá)到3~5μg/L時,鐵通過排污的去除率提高40%~70%,可以有效抑制腐蝕產(chǎn)物在蒸汽發(fā)生器內(nèi)的沉積。
SA-508Ⅲ和A106Gr.B鋼常用作壓水堆蒸汽發(fā)生器的管板、二次側(cè)筒體及給水管道等部件,這些部件與二次側(cè)的水化學(xué)環(huán)境直接接觸;水化學(xué)的改變與材料,尤其是低合金鋼、碳鋼的腐蝕密切相關(guān),因此有必要了解添加分散劑對材料腐蝕行為及其氧化膜的影響。本工作模擬了PWR二回路水質(zhì)環(huán)境,采用高溫高壓釜研究PAA對蒸汽發(fā)生器管板及筒體用材料A508III低合金鋼和給水管道材料A106Gr.B鋼腐蝕行為的影響,用掃描電鏡(SEM)、俄歇電子能譜分析對腐蝕氧化膜進(jìn)行了表征。
1 試驗
1.1 試樣及溶液
試驗材料為國產(chǎn)A508III低合金鋼和A106Gr.B碳鋼,其主要化學(xué)成分見表1。采用線切割將試樣割成20mm×15mm×2mm的試片,用SiC砂紙逐級打磨試片至鏡面光亮,用無水乙醇超聲清洗、干燥后稱量備用。
表1 試驗用金屬材料的要化學(xué)成分(質(zhì)量分?jǐn)?shù))
Tab.1 Main chemical composition of test materials(mass)
試驗溶液為模擬PWR二回路水溶液,pH為9.8(25℃),采用乙醇胺(ETA)+聯(lián)氨除氧(以下試驗溶液簡稱ETA溶液),溶液中含有20 mg/L ETA,溶解氧質(zhì)量濃度低于10μg/L。試驗溶液均用去離子水及分析純試劑配制而成。
1.2 試驗方法
靜態(tài)浸泡試驗依據(jù)GB10124-1988《金屬材料實驗室均勻腐蝕全浸試驗方法》進(jìn)行,采用容積為5L的高溫高壓釜。短期腐蝕試驗的溶液為未添加和添加2,5,10ug/L PAA的ETA溶液,試驗溫度為280℃,試驗時間為72h??疾?span lang="EN-US">PAA含量對A508III和A106Gr.B兩種材料腐蝕失重的影響。腐蝕相容性試驗也在高溫高壓釜中進(jìn)行,試驗溫度280℃,試驗壓力為6.5 MPa,試驗時間為2 000h,考察PAA與A508III和A106Gr.B兩種材料的相容性。將試樣置于高壓釜中,開始升溫至105℃,期間進(jìn)行除氧,之后向釜內(nèi)注入一定量的ETA和聯(lián)氨,然后逐漸升溫至目標(biāo)溫度后開始試驗,升溫過程大約4h。
腐蝕試驗結(jié)束后,取出試樣,干燥24h后稱量。之后對試樣進(jìn)行脫膜處理,脫膜方法參考文獻(xiàn)[2] :將樣品取出后放入盛有200mg/L K2Cr2O7溶液的燒杯中;再放入15%(質(zhì)量分?jǐn)?shù),下同)HCl+10%烏洛托品(六次甲基四胺)的脫膜液中脫膜。脫膜后依次放入盛有無水乙醇的兩個燒杯中,擦拭后冷風(fēng)吹干,放入干燥器中,24h后測量試樣的脫膜質(zhì)量。采用稱量的方式,利用腐蝕前與腐蝕試樣脫膜后的質(zhì)量差對比添加分散劑對材料腐蝕質(zhì)量損失及腐蝕速率的影響。
采用JSM-6400型掃描電鏡觀察A508III試樣經(jīng)2 000h相容性試驗后的表面形貌;采用日本ULVAC-PHI公司生產(chǎn)的PHI-700型納米掃描俄歇系統(tǒng)觀察腐蝕后A508III試樣表面氧化膜的俄歇電子能譜(AES)。
2 結(jié)果與討論
2.1 腐蝕失重
由圖1可見,在不添加PAA的ETA溶液中,A508III和A106Gr.B兩種試樣的腐蝕質(zhì)量損失分別為45.45mg/dm2和51.95mg/dm2。添加PAA后,試樣的腐蝕質(zhì)量損失增加,且隨PAA含量的增加,腐蝕質(zhì)量損失逐漸增大,說明在短時間(72h)內(nèi)添加PAA能加速碳鋼的腐蝕。這主要是由于PAA是弱酸,會在水溶液中電離出氫離子顯示弱酸性,PAA含量越大則酸性越強(qiáng),越有利于試樣發(fā)生腐蝕。浸泡液中鐵含量也是評估分散劑分散性能的一個重要指標(biāo)。用分光光度法檢測了試片經(jīng)含不同量PAA的ETA溶液浸泡72h后,溶液中的鐵離子含量(pH 9.8,280℃),見圖2。由圖2可見,隨著溶液中PAA含量的增加,鐵離子含量也隨之升高,說明PAA與試樣發(fā)生反應(yīng),使得試樣中的鐵及其氧化物溶解變成離子態(tài),利于鐵離子的釋放,與文獻(xiàn)報道一致[3] 。以上結(jié)果表明,隨著PAA含量升高,溶液pH下降,試樣腐蝕加重??紤]到腐蝕的問題,本工作后續(xù)試驗中PAA的加入量為5μg/L。
圖1試樣在含不同量PAA的ETA浸泡液中腐蝕72h后的質(zhì)量損失
Fig.1 Weight loss of samples after immersing in ETAsolution containing different contents of PAA for 72h
圖2 試驗溶液中鐵離子含量隨PAA含量的變化關(guān)系
Fig.2 Relationship between the content of Fe ion and the content of PAA in the test solution
由圖3(a)可見,試驗初期,A508-III試樣的腐蝕速率較高,添加PAA對試樣腐蝕速率的影響不大。隨著腐蝕時間的延長,A508-III試樣均勻腐蝕速率先快速減小,隨后逐漸變緩趨于穩(wěn)定。表明試樣表面形成的氧化膜具有一定的保護(hù)作用,阻礙了基體金屬的進(jìn)一步氧化。在腐蝕初期,氧化膜的保護(hù)作用不強(qiáng),但隨著腐蝕時間的延長,氧化膜厚度增加,其保護(hù)作用逐漸增大并趨于穩(wěn)定。根據(jù)腐蝕失重試驗結(jié)果,經(jīng)2 000h腐蝕試驗后,A508-III試樣在添加與未添加PAA分散劑的ETA溶液中的腐蝕質(zhì)量損失分別為178.1 mg/dm-2和227.0 mg/dm,腐蝕質(zhì)量損失大約減少21.58%,A508-III在兩種溶液中的腐蝕速率分別為0.1135mg/(dm2·h)和0.099mg/(dm2·h)。試驗結(jié)果表明,加入PAA對試樣起到一定的緩蝕作用,PAA與試樣有較好的相容性。腐蝕初期,無論PAA存在與否,腐蝕速率都較高;經(jīng)1 000h腐蝕試驗后,A508-III試樣在添加PAA的ETA溶液中的腐蝕速率有所降低,這表明PAA的分散作用是一個稍緩慢的過程。
圖3 A508-III試樣和A106Gr.B試樣在ETA溶液中有、無PAA條件下的腐蝕速率
Fig.3 Corrosion rates of A508-III(a)and A106Gr.B(b)samples in the ETA solution without and with PAA
由圖3(b)可見,在無PAA條件下,隨著腐蝕時間的延長,A106Gr.B試樣的腐蝕速率先快速減小,隨后逐漸變緩趨于穩(wěn)定。在ETA溶液中添加PAA后,試樣腐蝕速率逐漸隨時間的變化規(guī)律與未添加PAA時的基本一致,但腐蝕速率有所減小。根據(jù)腐蝕失重試驗結(jié)果,經(jīng)2 000h腐蝕試驗后,試樣在未添加和添加PAA的ETA溶液中的腐蝕失重分別為164.29mg/dm2和168.18mg/dm2,腐蝕速率分別為0.084mg/(dm2·h)和0.082mg/(dm2·h),約降低8%,可以認(rèn)為PAA與A106Gr.B材料具有較好的相容性。
2.2 腐蝕氧化膜
由圖4可見,在未添加PAA的ETA溶液中,經(jīng)2 000h腐蝕試驗后,試樣氧化膜表面的結(jié)構(gòu)較粗糙、顆粒物聚集明顯,這些顆粒物是尺寸為0.8~2.0μm的完好八面體結(jié)晶。在這些八面體顆粒物下面,有一層由結(jié)構(gòu)致密、尺寸更小(<0.2μm)的氧化物組成的氧化膜層。ETA溶液中加入PAA后,試樣氧化膜表面的大顆粒物數(shù)量明顯減少,分布更加均勻,這些顆粒物結(jié)晶度變差,形成形狀不規(guī)則、空隙較多的絮狀物,這表明PAA的存在改變了氧化物顆粒的生長過程。PAA在堿性條件下顯示負(fù)電性,極易與Fe2+、Fe3+等離子形成螯合物,這可能是導(dǎo)致氧化物顆粒形晶體結(jié)構(gòu)變化的主要原因[4]。
由圖5可見,經(jīng)2 000h高溫腐蝕試驗后,A508III試樣在兩種溶液形成的氧化膜的主要成分均為氧和鐵。在不含PAA的條件下,氧化膜在濺射40min后,開始出現(xiàn)鐵含量升高,氧含量下降趨勢;而添加PAA后,氧化膜在濺射25min后,氧含量逐漸下降,這表明添加PAA后的試樣氧化膜更薄,這主要是由于PAA的分散作用使得氧化物顆粒不易沉積在試樣表面[5]。
結(jié)合SEM和AES分析結(jié)果,認(rèn)為PAA分散劑抑制結(jié)垢的機(jī)理主要是由于PAA與氧化物顆粒間的靜電斥力作用和晶格畸變作用。PAA分散劑中加入冷卻劑后,因離子化產(chǎn)生的遷移性反粒子(H+)脫離高分子鏈區(qū)向水中擴(kuò)散,使分子鏈成為帶負(fù)電荷的聚離子(R-COO-),與表面帶正電荷的Fe2+、Fe3+等離子吸附形成聚離子。當(dāng)這種吸附不斷增加時,可使微粒帶上相同電荷,致使微粒間靜電斥力增加,聚結(jié)受阻,處于良好的分散狀態(tài),從而減少垢物的形成[6] 。另一方面,由于PAA吸附在氧化物晶核或微晶上占據(jù)一定的位置,阻礙和破壞了晶格的正常生長,還使得垢層中的晶體結(jié)構(gòu)發(fā)生很大的畸變,生成了一些不規(guī)則的非結(jié)晶顆粒,促使硬垢轉(zhuǎn)變?yōu)槭杷傻能浌?sup>[7] 。正是PAA的阻垢作用,試樣表面疏松的氧化膜逐漸脫離基體,使氧化膜更薄,分布更均勻,阻礙金屬基體與介質(zhì)離子的交換作用,使金屬基體表面各處離子含量及溶解氧含量一致,從而達(dá)到緩蝕的目的。
圖4 A508III試樣在280℃未添加和添加PAA的ETA在溶液中浸泡2 000h后的表面SEM形貌
Fig.4 SEM morphology of A508III samples after immersing in ETA solution without(a)and with(b)PAA at 280℃for 2 000h
圖5 A508III試樣在280℃未添加和添加PAA的ETA水溶液中浸泡2 000h后,表面氧化膜的AES圖譜
Fig.5 AES patterns of the surface oxide film of A508IIIsample after immersing in ETA solution without(a)and with(b)PAA at 280℃for 2 000h
3 結(jié)論
(1)PAA加入量為0~50μg/L時,試樣經(jīng)72h腐蝕試驗后的質(zhì)量損失隨PAA含量的增加而降低,試樣浸泡液中的鐵離子含量也逐漸升高,說明加入PAA能促進(jìn)鐵離子的釋放。
(2)經(jīng)2 000h的腐蝕試驗后,A508III試樣在ETA+PAA水化學(xué)環(huán)境中的腐蝕速率比其在未添加PAA的ETA水環(huán)境中的降低21.58%;A106Gr.B試樣在ETA+PAA水化學(xué)環(huán)境中的腐蝕速率比其在未添加PAA的ETA水環(huán)境中的降低8%。
(3)在加入PAA的ETA溶液中,試樣表面生成的氧化膜的氧化物顆粒結(jié)晶度下降,氧化膜厚度減薄。
(4)PAA通過靜電斥力和晶格畸變作用抑制腐蝕產(chǎn)物結(jié)垢。
免責(zé)聲明:本網(wǎng)站所轉(zhuǎn)載的文字、圖片與視頻資料版權(quán)歸原創(chuàng)作者所有,如果涉及侵權(quán),請第一時間聯(lián)系本網(wǎng)刪除。
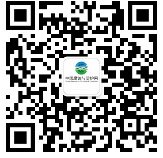
官方微信
《腐蝕與防護(hù)網(wǎng)電子期刊》征訂啟事
- 投稿聯(lián)系:編輯部
- 電話:010-62316606-806
- 郵箱:fsfhzy666@163.com
- 腐蝕與防護(hù)網(wǎng)官方QQ群:140808414