超高強度鋼冷噴涂鋁涂層性能研究
宇波,湯智慧、孫志華、張曉云、陸峰、劉光勛、王長亮、郭孟秋
北京航空材料研究院 北京 100095
個人介紹簡歷
宇波,男,遼寧沈陽人,1979年1月出生,1997年考入北京航空航天大學材料系攻讀本科學位,2001年于北航材料學院攻讀碩士學位,2004年4月畢業后到中國航空工業集團公司北京航空材料研究院第五研究室(金屬腐蝕與防護)參加工作。工作期間,主要從事金屬材料腐蝕性能研究與防護技術的研發及工程化應用工作,承擔了多項科研機型號課題研發工作,對于不銹鋼、高強度鋼、鋁合金、鈦合金等表面防護技術開展了深入的研究。作為第一作者在國內核心期刊及全國性會議發表論文5篇,作為主要申請人申請發明專利3份,獲得部級科技成果獎2項。
宇波
摘要:本研究采用冷噴涂技術在超高強度鋼表面制備純鋁涂層。研究分別采用掃描電鏡進行涂層微觀分析、采用EDS對噴涂粉末及涂層成分進行分析。涂層結合力采用彎曲法及劃格法進行評價,涂層耐蝕性采用中性鹽霧試驗進行考核,冷噴涂工藝對疲勞性能的影響進行對比評價,冷噴涂工藝的氫脆性能采用延遲拉伸試驗進行評價。研究結果顯示,冷噴涂鋁涂層微觀為層狀,涂層由純鋁構成,孔隙率小于1%,涂層與基體具有良好的結合力,噴涂試樣中性鹽霧試驗1000小時基體不腐蝕。疲勞試驗證明冷噴涂鋁工藝對基體抗疲勞性能有所提高,同時噴涂工藝對基體氫脆性能無影響。
關鍵詞:超高強度鋼;冷噴涂;鋁涂層;耐蝕性;疲勞;氫脆
1 前言
冷噴涂技術(CS),又稱為低溫氣動噴涂技術(CGDS),是近年來國內、外正廣泛開展研究的一門表面處理技術[1-2]。冷噴涂技術是將具有一定塑性的固態粒子通過高速氣流噴射到基體表面,固態粒子在與基體的撞擊作用下經過強烈的塑性變形而發生沉積形成涂層的方法。高速粒子的產生是利用高壓氣體通過縮放管產生超音速流動,將粉末粒子從軸向送入高速氣流中,粒子經加速后,在完全固態下撞擊基體[3-4]。
冷噴涂概念在上世紀80年代中期由俄羅斯氣動專家發現并提出,俄羅斯科學院西伯利亞分院理論及力學研究所在進行超音速風洞試驗時發現當粒子移動速度達到某一臨界值,粒子便可以沉積在目標材料的表面[5-6]。到了2000年后,冷噴涂技術逐漸成為表面工程的一個研究熱點。俄羅斯、美國、德國等國專家對該技術進行了廣泛的研究,已逐漸開始進行工業的應用。
由于冷噴涂采用低溫氣體對涂層粒子進行加速,因此冷噴涂技術具有許多優點。例如涂層適用范圍廣,能夠在在不同基體上噴涂金屬、合金、塑料等涂層;噴涂溫度低,涂層不易發生氧化及相變;涂層與基體結合緊密,孔隙率低;涂層與基體熱應力小,對基體殘余應力主要為壓應力……因此冷噴涂技術非常適用于對于表面處理技術要求較高的航空領域,以保證航空材料對于耐腐蝕、長壽命不斷增長的要求。本研究即對冷噴涂鋁技術進行研究,通過在超高強度300M鋼進行冷噴涂鋁涂層工藝,對冷噴涂鋁涂層的各項性能進行考核。
2 材料、試驗及結果
2.1 材料
試驗基體材料選用超高強度鋼300M鋼,其名義成分如表1。#p#分頁標題#e#
表1 300M鋼名義成分
C | Mn | Si | S | P | Cr | Ni | Mo | V | Cu | Fe |
0.38~0.43 | 0.6~0.9 | 1.45~1.8 | £0.01 | £0.01 | 0.7~0.95 | 1.65~2 | 0.3~0.5 | 0.05~0.1 | £0.35 | Other |
噴涂粉末采用鋁顆粒,顆粒粒度為300目,球形,粉末的顯微形貌如圖1,由北京礦冶研究院提供,粉末鋁含量達到98%以上。冷噴涂過程在北京航空材料研究院的冷噴涂設備上進行,其結構原理圖見圖2[7]。
圖1 噴涂鋁粉顯微形貌
圖2 冷噴涂設備結構圖
1-超音速噴嘴;2-氣體加熱裝置;3-送粉器;4-空壓機;5-氦氣源;6-噴涂室;
7-試樣架;8-控制裝置;9-粉末回收裝置
2.2 試驗和結果
2.2.1 涂層外觀與微觀
冷噴涂鋁涂層的微觀采用Quanta 600掃描電鏡進行觀測。由圖3可以看出,冷噴涂鋁涂層外觀為灰白色,涂層致密均勻。涂層在微觀形貌下較為平整、細致,涂層孔隙、夾雜物較少。涂層的表面存在橢球形顆粒,涂層內部為層狀結構,證明涂層在沉積過程中高速球形鋁粉在與基體碰撞過程中發生了強烈的塑性變形而成為扁平狀,在鋁粉的不斷沉積碰撞過程中,下層的鋁沉積層由于撞擊形成層狀結構,而表層的鋁粉由于未發生連續撞擊,其截面為橢圓形。
圖3 低溫氣動噴鋁宏、微觀形貌
2.2.2 涂層成分分析
使用能譜分析儀(EDS,Oxford INCAx-sight 6427)對冷噴涂鋁涂層的涂層成分進行了分析,如圖4.冷噴鋁涂層中鋁含量為97.78%(重量),說明冷噴涂工藝受到熱影響較小,金屬粉末被氧化的程度較低。
表2 鋁粉末與冷噴涂鋁涂層成分分析
鋁粉末 | 冷噴涂鋁涂層 | |
氧,% | 1.42 | 2.22 |
鋁,% | 98.58 | 97.7 |
2.2.3 涂層孔隙率
分別對冷噴涂涂層的表面及截面進行孔隙率的分析測量,測量結果如表3,涂層的截面形貌如圖5。從涂層的孔隙率結果可以看出,冷噴涂涂層具有非常小的孔隙率,說明在高速顆粒碰撞沉積過程中由于不斷地撞擊非常緊密的連接在一起,形成了致密的涂層,涂層的低孔隙率無疑會在使用過程中為涂層帶來優異的耐腐蝕性能。
表3 冷噴涂涂層表面、截面孔隙率
涂層 | 孔隙率平均值,% | |
表面 | 截面 | |
冷噴涂Al | 0.26 | 0.064 |
圖5冷噴涂鋁涂層截面形貌
2.2.4 涂層結合力
分別采用劃格法與彎曲法對涂層與基體的結合力進行考核,考核結果如圖6。從劃格法考核結果可以看出,劃線交叉處未發現涂層的開裂、起皮等現象,說明涂層與基體具有良好的結合力;采用彎曲法檢測,冷噴鋁涂層在彎曲后180°后未見裂紋,證明冷噴涂鋁涂層與基體具有較好結合力的同時,涂層具有較好的延展性能。
劃格法 彎曲法
圖6 冷噴涂鋁涂層與基體結合力檢驗
2.2.5 涂層耐蝕性
冷噴涂鋁涂層具有低氧化率、低孔隙率的特點,因此其應有較好的耐腐蝕性能。研究采用中性鹽霧試驗對冷噴涂鋁涂層的耐腐蝕性能進行考察,結果如表4。從考察結果可以看出,冷噴涂鋁涂層具有非常好的耐腐蝕效果,噴鋁試樣表面在500h左右開始出現鋁涂層的腐蝕,而鹽霧試驗進行1000h后仍未發生基體的腐蝕。
表 4 冷噴涂鋁涂層鹽霧腐蝕結果
涂層 | 測試時間/ h | ||||||||||||
95 | 184 | 280 | 351 | 446 | 518 | 614 | 690 | 780 | 849 | 930 | 960 | 1000 | |
冷噴涂Al | 發暗 | 白銹并擴展 |
鹽霧0h 鹽霧518h 鹽霧1000h
圖7 冷噴涂鋁涂層中性鹽霧檢驗
為了進一步研究冷噴涂鋁涂層的耐蝕性能,研究對冷噴涂鋁、高速火焰噴涂鋁涂層的電化學性能進行研究,通過極化曲線比較兩種涂層的耐蝕性能,結果如表5和圖8.冷噴涂鋁涂層的腐蝕電流大大低于高速火焰噴涂鋁涂層,而冷噴涂鋁涂層的腐蝕電位低于高速火焰噴涂鋁涂層。試驗結果說明冷噴涂鋁涂層相比高速火焰噴涂鋁涂層可以更好地保護基體材料,冷噴涂涂層的腐蝕速度更慢,耐蝕性能更好。
表5 極化曲線試驗結果
涂層種類 | 腐蝕電位, EC ,mv | 腐蝕電流,μA/cm2 |
高速火焰噴涂鋁涂層 | -0.752 | 6.01 |
冷噴涂鋁涂層 | -0.823 | 0.43 |
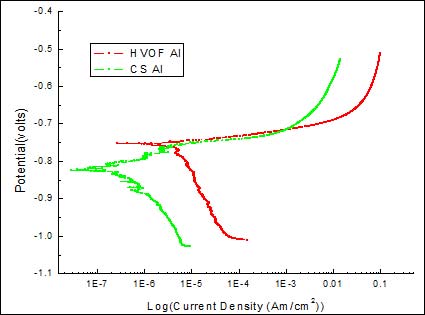
圖8 冷噴涂鋁涂層中性鹽霧檢驗
2.2.6 冷噴涂鋁涂層對疲勞、氫脆性能影響
采用300M鋼作為基體材料,考察冷噴涂鋁工藝對基體疲勞性能、氫脆性能影響,噴涂后試樣如圖9。疲勞試驗采取應力值為400MPa~600MPa的范圍內進行,應力比R=-1,疲勞試驗結果如表6。從試驗結果可以看出,在高應力狀態下,冷噴涂前后的基體疲勞性能基本一致,而當低應力狀態下(500MPa以下),冷噴涂對基體的疲勞性能甚至有提高作用。#p#分頁標題#e#
疲勞試棒 氫脆試棒
圖9 冷噴涂后的疲勞、氫脆試棒形貌
表6 300M基材及三種冷噴涂涂層疲勞測試結果
材料及涂層 | R | σmax/MPa | N/103 |
300M | -1 | 600 | 44 |
575 | 53 | ||
440 | 4130 | ||
420 | >10000 | ||
300M+冷噴涂Al涂層 | -1 | 600 | 27 |
560 | 52 | ||
500 | >10000 | ||
460 | >10000 |
冷噴涂鋁工藝對300M鋼氫脆敏感性測試結果見表7,采用持久拉伸的方法對冷噴涂鋁涂層的缺口拉伸試棒進行氫脆試驗,持久拉伸200h后氫脆試棒均未發生斷裂,證明300M鋼冷噴涂鋁的氫脆性能滿足要求。
表7 冷噴涂鋁涂層氫脆測試結果
涂層 | 試樣編號 | 切口直徑/ mm |
施加的恒定載荷/ N |
結果 |
冷噴涂 Al |
3 | 4.507 | 32893 | 200h內未發生斷裂 |
11 | 4.505 | 32864 | ||
19 | 4.500 | 32791 | ||
25 | 4.501 | 32806 |
3 結論
(1)300M鋼冷噴涂鋁涂層,涂層外觀均勻、平整,涂層為片層狀結構,孔隙率低于1%;
(2)冷噴涂鋁涂層成分主要由鋁構成,涂層與噴涂粉末的成分基本一致,噴涂過程鋁涂層基本沒有氧化;
(3)冷噴涂鋁涂層與基體具有良好的結合力,采用劃格法及彎曲法均滿足性能要求;
(4)冷噴涂鋁涂層具有良好的耐蝕性能,采用中性鹽霧試驗1000h未出現基體腐蝕,冷噴涂鋁涂層的耐蝕性能優于高速火焰噴涂鋁涂層;
(5)300M鋼冷噴涂鋁涂層不會降低基體材料的疲勞性能,同時冷噴涂工藝對基體氫脆性影響滿足要求。
參考文獻
[1]Papyin, Anatolii. Cold spray technology [J]. Advanced Materials & Processes,2001;159(9)
[2]Kreye H, Stoltenhoff T. Cold spraying -a study of process and coating characteristics[C].Proc.of 1st ITSC' 2000, 2000,419-422
[3]Zhao Aiwa, Wang Xiaofang, Wu Jie. Development of Cold Spray Technology and Its Industrial Applications [J]. Journal of Vibration Engineering.2004,17(S):651-653
[4]Wang Jiajie,Wang Zhiping,Huo Shubin. Characterization of copper layers produced by cold spraying [J].Transactions of the China Welding Institution, 2007,28(4):77-80
[5] Alkimov A P, Kosarev V F, Papyin, A N. A method of cold gas dynamic deposition [J]. Dokl. Akad. Nauk SSSR, 1990,315(5):1062-1065.
[6]D.Zhang, P.H. Shipway, D.G.McCartney. The Effect of Processing Variables on Deposition Characteristics of Aluminium by Cold Gas Dynamic Spraying [J]. China Surface Engineering, 2008,21(4):1-7
[7]Kosarev V F, Klinkov S V, Sova A A. Recently Patented Facilities and Applications in Cold Spray Engineering [J]. Recent Patents on Engineering 2007, 1(1):1-8
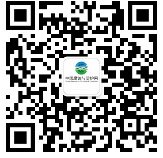
官方微信
《中國腐蝕與防護網電子期刊》征訂啟事
- 投稿聯系:編輯部
- 電話:010-62313558-806
- 郵箱:fsfhzy666@163.com
- 中國腐蝕與防護網官方QQ群:140808414