引言
鍍層技術是提高鋼鐵耐腐蝕性能的有效途徑之一。與傳統的純Zn鍍層、Galfan鍍層以及Galvalume鍍層相比,Zn-Al-Mg合金鍍層具有更優異的切口保護性能和耐大氣腐蝕性能,被廣泛用于汽車、建筑、交通等領域。
從20世紀80年代開始,Zn-Al-Mg合金鍍層在日本得到廣泛應用,合金鍍層中的Al含量范圍為6%-11%(質量分數),Mg含量范圍為0.5%-3.0%。
進入二十一世紀后,歐洲各鋼鐵企業為了滿足汽車生產的需要,開發了Al含量較低的Zn-Al-Mg合金鍍層鋼板,Al和Mg的含量范圍為1%-3%。
大量研究認為,Zn-Al-Mg合金鍍層中的Mg在大氣腐蝕條件下會阻礙多孔碳酸鋅和氧化鋅的形成,并且在陽極形成鎂的堿式碳酸鹽和堿式氯化物,具有更低的離子遷移率,因此具有更加優異的耐腐蝕性能。
本研究選擇較低鋁含量的Zn-Al-Mg合金為研究對象,分別采用爐冷、空冷和水冷的凝固方式獲得鑄造樣品,觀察了不同凝固方式下的合金顯微組織,并采用電化學實驗對其耐蝕性進行評價。
1.試驗方法
1.1合金的制備
采用電阻爐熔煉Zn-Al-Mg合金。合金原料采用純Zn錠(99.995%Zn,質量分數)、純Al錠(99.6%Al,質量分數)和Zn-Mg中間合金(Zn-11%Mg,質量分數),目標成分為Zn-1%Al-1%Mg(質量分數)。使用電子天平稱量母合金質量,精確到0.01g。合金的熔煉步驟如下:
1將烘干的純Zn和純Al原料放入石墨坩堝中,然后將石墨坩堝放在電阻爐中升溫至500℃,升溫速率為10℃/min,保溫2h;
2待坩堝中的合金全部熔化后,將烘干的Zn-Mg中間合金加入石墨坩堝中,并用石墨罩將Zn-Mg中間合金壓到熔體液面以下,促使中間合金熔化,并且避免鎂在空氣中氧化損失;
3將爐溫升高到550℃,保溫至合金全部熔化;
4用石墨棒緩慢攪拌坩堝中熔化的合金,促使合金成分均勻;
5將電阻爐溫度降低到420℃,降溫速率為10℃/min,然后保溫2h,使石墨坩堝中的合金溫度及成分均勻。將均勻化的合金熔體分批倒入干燥的石墨鑄型中,石墨鑄型內腔尺寸為Φ30mm×5mm,壁厚為3mm。為實現爐冷、空冷和水冷的凝固方式,將石墨鑄型分別放置在加熱爐中、空氣中以及20℃的水浴中。
待石墨鑄型冷卻到室溫,從石墨鑄型中取出樣品,將樣品表層1mm厚的氧化層除去,然后切割成分析樣品。其中,用于掃描電鏡(SEM)觀察的樣品為Φ10mm×1mm的圓片,用于電化學分析的樣品為Φ20mm×1mm的圓片。用電感耦合等離子體原子發射光譜(ICP-AES)方法分析合金樣品的成分,取樣位置為樣品中心。Zn-Al-Mg合金的實際成分為Zn-1.32%Al-1.10%Mg(質量分數)。
1.2分析方法
采用S-3400N型SEM觀察Zn-Al-Mg合金的微觀組織,加速電壓為15kV,并采用SEM附帶的能譜儀(EDS)測定微觀組織的化學成分。
采用PARSTAT 2273電化學工作站進行電化學實驗,實驗介質為含有3.5%(質量分數)NaCl的去離子水溶液,電解質溫度為(30±2)℃。
實驗采用三電極系統,輔助電極為鉑電極網,尺寸為10mm×10 mm;參比電極為飽和甘汞電極(SCE);工作電極為合金樣品,尺寸為10mm×10mm。測量極化曲線時的電位掃描速率為1mV/s,掃描范圍為-1.25—0.75V(vs SCE)。電化學阻抗(EIS)測量時交流信號的幅值為10mV,測量頻率范圍為105-10-2Hz。
實驗前將合金樣品表面用砂紙打磨并拋光,然后在無水乙醇中進行超聲波清洗,除去表面的灰塵、油污等。
2.實驗結果
2.1凝固方式對Zn-Al-Mg合金組織的影響
圖1 以不同冷卻方式得到的Zn-Al-Mg合金的微觀組織及共晶組織放大圖
圖1為Zn-Al-Mg合金以不同凝固方式冷卻到室溫的微觀組織。3種凝固方式得到的Zn-Al-Mg合金的微觀組織均由大塊的初始凝固(簡稱初晶)組織以及共晶組織構成,共晶組織分布在初晶組織之間。在爐冷凝固條件下,大塊初晶組織中有少量析出物。在水冷、空冷和爐冷條件下,共晶組織的形貌分別為層片狀、層片+顆粒狀和顆粒狀。
采用圖像分析的方法測量了不同凝固條件下初晶晶粒所占的比例,同時采用劃線法測量了初晶組織的尺寸,圖像分析采用Image J軟件,結果如圖2所示。
圖2 不同凝固方式下Zn-Al-Mg合金中初晶晶粒尺寸及其比例
可見,在水冷、空冷和爐冷的凝固條件下,Zn-Al-Mg合金的初晶組織尺寸依次增大,初晶組織的平均尺寸從10µm增大到20µm。而隨著凝固速率的降低,合金中的初晶組織所占比例不斷增加。在水冷、空冷和爐冷的凝固條件下,初晶組織所占比例分別為82.3%、88.7%和88.9%。
采用EDS分析圖1中不同位置的合金元素含量,結果如表1所示。
表1 Zn-Al-Mg合金中不同位置的元素含量
可見,初晶組織為富Zn相,其中固溶有少量Al。隨著凝固速率的降低,初晶中的Al含量逐漸降低。在水冷、空冷、爐冷的凝固方式下,初晶組織中的Al含量分別為7.8%(原子分數)、4.1%和2.4%。
根據EDS結果,共晶組織中包含有3種不同的相:富Zn相、Al-Zn相以及Mg-Zn相。共晶組織中富Zn相與初晶組織中富Zn相的合金元素種類和含量相近,固溶有少量的Al,而且隨著凝固速率的降低,固溶Al含量減少。
共晶組織中Al-Zn相的成分范圍較寬,在水冷凝固條件下,Al-Zn相中含有54.0%的Zn;在空冷凝固條件下,Al-Zn相中含有49.6%的Zn;而在爐冷凝固條件下,Al-Zn相中的Zn含量下降到20.6%。
凝固方式對共晶組織中Mg-Zn相的元素含量影響較小,在3種凝固方式下,Mg-Zn相中的Mg與Zn的原子比均接近1:2,這表明該相可能為有序中間化合物MgZn2。
2.2凝固方式對Zn-Al-Mg合金耐蝕性的影響
Zn-Al-Mg合金的極化曲線如圖3所示,采用Tafel區外推法得到電化學參數見表2。
圖3 不同凝固方式的Zn-Al-Mg合金的極化曲線
表2 不同凝固方式的Zn-Al-Mg合金的電化學參數
可見,不同凝固方式的Zn-Al-Mg合金的腐蝕電位(Ecorr)略有差異。水冷凝固的Zn-Al-Mg合金的腐蝕電位最高,空冷凝固的其次,而爐冷凝固的Zn-Al-Mg合金的最低。
不同凝固方式得到的Zn-Al-Mg合金的腐蝕電流密度(Icorr)有明顯差異,在水冷、爐冷和空冷條件下,Zn-Al-Mg合金的腐蝕電流密度分別為5.5,4.1和2.1µA·cm-2,即隨著凝固速率的增大,自腐蝕電流密度增大。
根據Faraday定律,對于相同成分的合金,自腐蝕電流密度與腐蝕速率成正比。因此推測,隨著凝固速率的增大,腐蝕速率增大,耐蝕性下降。
Zn-Al-Mg合金的EIS測試結果見圖4,等效電路見圖5。
圖4 Zn-Al-Mg合金的Nyquist圖和Bode相位圖
圖5 Zn-Al-Mg合金EIS的擬合等效電路
其中,Rs為溶液電阻(Ω·cm2),R1為電雙層的電荷轉移電阻(Ω·cm2),Q1是與電雙層有關的常相位角元件(CPE),R2是與Zn-Al-Mg合金表面有關的電阻(Ω·cm2),Q2是與Zn-Al-Mg合金表面有關的常相位角元件(CPE)。
等效電路的擬合參數見表3。
表3 等效電路的擬合參數
可見,不同凝固方式得到的Zn-Al-Mg合金的EIS具有相似的相位關系,可以用相同的等效電路進行表征。
溶液電阻Rs與凝固速率沒有明顯相關性,不同凝固速率下得到的Rs數值范圍為16.3~18.5Ω·cm2。而隨著凝固速率的提高,與Zn-Al-Mg合金表面有關的電阻R2有所提高,在水冷、空冷、爐冷的凝固方式下,R2分別為193,357和417Ω·cm2。
這表明,隨著凝固速率的降低,該Zn-Al-Mg合金的耐蝕性有所提高。
3.結論
1不同凝固條件下的Zn-1%Al-1%Mg合金均由初晶組織和共晶組織構成;隨著凝固速率的降低,合金中的初晶組織所占的比例和尺寸增大。
1Zn-1%Al-1%Mg合金中的共晶組織由富Zn相、Al-Zn相和Mg-Zn相組成,其中Mg-Zn相為MgZn2中間化合物。
3隨著凝固速率的下降,Zn-Al-Mg合金的自腐蝕電流有所減小,電化學阻抗譜中與合金表面相關的電阻有所增大,表明合金的耐蝕性提高。
更多關于材料方面、材料腐蝕控制、材料科普等方面的國內外最新動態,我們網站會不斷更新。希望大家一直關注中國腐蝕與防護網http://www.ecorr.org
責任編輯:韓鑫
《中國腐蝕與防護網電子期刊》征訂啟事
投稿聯系:編輯部
電話:010-62313558-806
郵箱:fsfhzy666@163.com
中國腐蝕與防護網官方 QQ群:140808414
免責聲明:本網站所轉載的文字、圖片與視頻資料版權歸原創作者所有,如果涉及侵權,請第一時間聯系本網刪除。
-
標簽: Zn-Al-Mg合金, 凝固組織, 耐腐蝕性
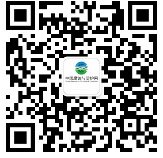
官方微信
《中國腐蝕與防護網電子期刊》征訂啟事
- 投稿聯系:編輯部
- 電話:010-62313558-806
- 郵箱:fsfhzy666@163.com
- 中國腐蝕與防護網官方QQ群:140808414