引言
目前,高超聲速飛行器已成為各個軍事大國不惜重金、傾力開發的重要突防手段。高超聲速飛行器再入大氣層返回地面,以及某些高超聲速飛行器在大氣層中加速、巡航時,都要經歷馬赫數5 以上的超高聲速飛行。當進行高超聲速飛行時,飛行器的表面產生強烈的氣動加熱,導致某些部位表面溫度甚至高達2 000 ℃ 以上。其加熱負荷主要包括兩部分: 一部分來自飛行器前面高能激波層的輻射加熱,另一部分是對流加熱。對流加熱又包括高溫氣體的對流加熱和氣體表面催化重組的反應熱。防熱系統是發展高超聲速飛行器的重點技術之一。
1 高超聲速飛行器防熱設計的特點及種類
高超聲速飛行器的防熱結構需根據不同的受熱部位、熱環境、暴露時間以及具體執行的任務來進行針對性設計。目前,超高聲速飛行器的防熱結構可分為燒蝕型、非燒蝕型以及復合型三類。
1. 1 燒蝕型防熱結構
燒蝕型防熱結構主要利用材料在升華、熔化和碳化時的相變熱及化學反應熱,帶走大量的熱量,其中應用最為廣泛的是碳化吸熱。一般而言,暴露時間在半小時內,表面溫度1 370 ℃以上的超高聲速飛行可以考慮使用燒蝕型防熱結構。特別是在高熱流密度( 10 MW/m2以上) 及一次性使用系統中燒蝕防熱材料仍將占據主要地位。
1. 2 非燒蝕型防熱結構
非燒蝕型防熱結構一般都是可重復使用的防熱結構,其對防熱材料的一般要求是: 1) 耐高溫; 2)抗熱震性好; 3) 性能穩定,可靠性高; 4) 表面特性要求: 高輻射率,低表面催化,必要時做表面防水處理; 5) 低熱膨脹系數; 6) 導熱系數低; 7) 質量輕; 8) 低成本。
非燒蝕型防熱結構主要包括熱沉型結構、熱結構以及被動絕熱結構三大類:
1) 熱沉型結構一般具有較高的熱容量,可以在短時間內吸收較多熱量,將其升溫限制在可控范圍內。如果表面溫度低于530 ℃,暴露時間在半小時內,就可以考慮采用熱沉型防熱結構。
2) 熱結構是指采用的結構材料在高溫下仍然能保持足夠的強度,熱結構特別適用于像操縱面一類的輕負載構件。用于熱結構的材料有兩類: a) 金屬基復合材料( MMCs) : 鈦-鋁合金等耐高溫鈦基復合材料( TMC) 都是候選的MMCs 材料,如表面溫度在500 ℃以下,暴露時間不超過1. 5 h,可以適用鈦金屬熱結構系統。這類材料在高溫下( 650 ~816 ℃) 仍然具有很好的強度及抗蠕變性能。不過,鈦-鋁合金在高溫下易于氧化,表面需要采用低催化性、高輻射率的防氧化涂層。在X-38 項目中采用了金屬/陶瓷基復合材料( CMC) 方向舵設計方案;b) 陶瓷基復合材料: 基于高溫強度及抗高溫蠕變性能,C /SiC、SiC /SiC、帶涂層C /C、C /C-SiC( Si 熔融滲透C /C 復合材料) 以及超高溫陶瓷材料( UHTCs)都是候選CMC 材料。例如,在X-43 項目中采用Haynes 230 合金與C /C 機翼前緣集成設計方案。此外,采用非平衡編織的高導熱炭纖維復合材料有利于結構散熱,也能避免高熱點,提升其在高溫環境的使用溫度。
3) 絕熱結構的熱防護系統一般可用于表面溫度在530 ~ 1 370 ℃ 的區間內,暴露時間在1 h 左右。目前主要包括托架支承防熱結構( 帶表面防護層的絕熱結構) 以及剛性絕熱瓦及柔性絕熱氈結構。
在具體設計過程中,上述三種結構可以組合使用,以滿足實際應用要求。對于一些長時間、高熱流密度的場合,還需采用“疏、堵”相結合的模式,用高導熱材料削減其熱流峰值,同時與主動防熱系統結合使用,如對流冷卻技術、膜冷卻技術、相變蒸發冷卻技術以及熱管技術等。目前,典型吸氣式超聲速飛行器設計采用的非燒蝕防熱方案通常是將熱結構、絕熱制品以及主動冷卻集成為一體,可承受的表面溫度在1 600 ~ 2 000 ℃左右,暴露時間在1. 5 h 左右。
1. 3 復合型防熱結構
復合型防熱結構主要指用燒蝕類有機材料填充的輕質陶瓷材料,如SIRCA 等,既具有較好的輕質隔熱性能,同時又具有燒蝕、相變性能。此外,復合型防熱結構也可以是上述兩種防熱結構的組合,在某些關鍵部位,燒蝕型防熱結構可用于作為其外層非燒蝕型防熱層的強化防熱措施。
2 絕熱型防熱結構
2. 1 托架支承防熱結構
托架支承防熱結構主要可分為兩類,一類是鎧裝防熱結構,另一類是CMC 集成防熱結構。其主要結構是外面采用耐高溫面板,提供足夠的抗沖刷及沖擊強度; 其底層可以使用包裹絕熱層結構,必要時,面層與襯板之間可以使用加筋增強,中間絕熱層可提供最佳的隔熱效果。相比較而言,托架支承結構對絕熱層的強度要求較低,絕熱材料的選擇余地較大,可以使用單一絕熱材料,也可以選用復合絕熱材料。托架支承防熱結構主要特點是將外層面板的氣動壓力負荷傳遞到下層的機身結構上,同時通過采取有效降低熱橋效應的措施,阻止外層的熱負荷向內層傳遞。整體結構不僅具有防熱功能,同時也具有一定的承重功能以及抵抗氣動噪聲及振動負荷。
2. 1. 1 鎧裝防熱結構
鎧裝防熱結構具有更好的韌性及抗沖擊性能,更能耐空間飛行碎片的沖擊。為了提高防熱結構的比強度及抗變形能力,面板材料一般采用金屬蜂窩體結構。其下層絕熱層采用包裹的低容重陶瓷纖維氈,如Saffil 氧化鋁纖維氈,也可以是多屏絕熱氈,或者氣凝膠氈。目前,氧化物彌散增強超級合金面板的最高使用溫度最高可達1 250 ℃。
美國早期的水星號飛船以及雙子座號飛船均是采用這樣的熱防護結構。另外,20 世紀90 年代,美國X-33 無人空天飛機模型機的機身底部也采用由Inconel 617 和鈦復合蜂窩面板與絕熱材料制成的金屬防熱結構。
2. 1. 2 CMC 陶瓷防熱結構
CMC 陶瓷防熱結構采用高溫陶瓷材料作為面板,絕熱材料一般采用氧化鋁纖維氈、多屏絕熱氈、氣凝膠氈的復合絕熱縫氈,還可以是填充氣凝膠的多孔陶瓷等。目前,CMC 結構集成防熱結構已成為歐洲航天局自主開發的主要候選防熱系統方案。該系統將防熱材料與承重構件組合成結構化集成系統,不僅質量相對較輕,并且在綜合性能及維護方面也具有優勢。
2. 2 剛性絕熱瓦及絕熱氈結構
帶有表面涂料的剛性絕熱瓦及絕熱氈結構,自身承擔著氣動負載及一定的抗沖擊能力,同時又具有較好的高溫絕熱性能,典型的絕熱結構如航天飛機的熱防護系統。
3 航天飛機防熱技術
航天飛機在再入大氣層時,速度可以高達馬赫數25,目前航天飛機防熱系統是唯一經過長期驗證的可重復使用防熱技術,盡管美國載人航天飛機項目已經終止,但是它為今后更先進高超聲速飛行器的開發提供了寶貴的遺產。根據熱負荷特點,航天飛機上部,一般可使用低溫絕熱制品( LRSI,溫度一般< 649 ℃) ; 底部迎風面一般采用剛性高溫絕熱瓦( HRSI) ,最高使用溫度可達1 260 ℃; 鼻錐及迎風翼部位一般采用碳陶類超高溫絕熱制品,最高使用溫度可達1 650 ℃。經過三十多年的發展,航天飛機防熱結構大致經歷了三、四代的更新升級。代際之間的防熱材料不一定都是完全的替代,有的可能僅僅是局部的替代。表1 為航天飛機三、四代防熱結構采用的主要材料。
航天飛機防熱系統一般采用以下三種形式的制品:
1) 剛性制品,通常以剛性絕熱瓦的形式來使用;2) 仿形制品,以柔性的形式制造,在其被保護的剛性結構表面上定型,最后可固化成剛性絕熱制品;3) 柔性制品,制造與使用都是以柔性的形式,如柔性縫制絕熱氈。
3. 1 剛性絕熱瓦
剛性絕熱瓦的概念最早是由Lockheed ( LMSC)公司在20 世紀60 年代初提出的,本來考慮用于阿波羅探月項目,最后阿波羅探月項目并未采用這一防熱方案。1962 年,LMSC 開發了第一塊石英纖維剛性絕熱瓦LI-1500,盡管當時Rockwell 公司也發明了莫來石纖維剛性絕熱瓦,但后者容重較重,性能穩定性也不及前者,最后LMSC 勝出,并從1972年開始建立生產線,1977 年開始規模化定型生產兩種剛性絕熱瓦: LI-900 及LI-2200,厚度范圍:25. 4 ~ 127 mm,大小一般為152. 4 mm × 152. 4 mm,表面涂有一層0. 425 mm 厚的RCG 高溫輻射涂料。表2 為專為航天飛機開發的主要剛性絕熱瓦制品及其組分特點和匹配的涂料。
RCG 高溫輻射涂料滲透性較差,一般僅用作涂料來使用,而TUFI 高溫輻射涂料與HETC 高溫輻射涂料不僅可用作高溫輻射涂料,還可以用作多孔絕熱瓦的表面處理劑,可以滲透到絕熱瓦內部6 mm以上,從而起到對剛性絕熱瓦的增強、增韌作用。
剛性絕熱瓦安裝時底部需要用漿料涂層對絕熱瓦底部進行局部致密化,以便防止絕熱瓦在底部基材結合處的根部斷裂。此外,剛性絕熱瓦具有脆性,不能直接安裝在航天飛機的金屬框架結構上,為此,在剛性絕熱瓦與航天飛機機身結構之間增加一層Nomex 芳綸應變隔離塊SIP( 容重194 kg /m3,使用前需進行熱穩定處理) ,一方面起到限制振動的傳遞,另一方面可以緩沖航天飛機內部結構與絕熱瓦之間不同的熱膨脹系數。SIP 與剛性絕熱瓦之間采用RTV 硅橡膠粘接,并在真空包壓力下加壓固化。
剛性瓦塊與剛性瓦塊之間要留有一定的膨脹縫( 0. 7 ~ 5 mm) ,主要用來解決剛性瓦與機身輕質合金結構的熱膨脹不同步的問題。膨脹縫的底部也采用經防水處理19 mm 寬的條狀Nomex 芳綸針刺氈固定在機身結構上,飛行器在再入大氣層時,高溫高壓的等離子體包圍著高溫絕熱瓦,為了避免高溫等離子體滲透到膨脹縫下面的背襯Nomex 芳綸氈,對芳綸氈造成破壞,需要在膨脹縫內插入陶瓷纖維復合盤根封墊。
3. 2 柔性絕熱氈
柔性絕熱氈中僅有兩種有機絕熱氈,分別是FRSI 芳綸針刺氈及PBI 氈。其它均為陶瓷纖維類柔性絕熱氈。主要柔性絕熱氈及其組成特點以及匹配涂料見表3。
盡管柔性絕熱縫氈耐用性能并不比剛性絕熱瓦好,但是柔性絕熱縫氈的制造及安裝效率高,重量及制造成本也較低,因此,在航天飛機上部背風面得到了大面積的應用。剛性絕熱瓦與柔性絕熱氈絕熱性能的比較見圖1 。柔性絕熱縫氈的主要缺點是表面厚度均勻性較差,而且表面粗糙,這樣一方面在高速飛行時織物表面纖維之間摩擦加劇,引起表面織物的加速損害,另一方面高速飛行時也會產生不可接受的氣動邊界效應。因此,無法用于航天飛機迎風面的底部絕熱。
20 世紀80 年代,由Ames 開發了升級型柔性絕熱氈TABI。TABI 柔性絕熱氈包含有骨架結構及填充層兩部分,骨架結構是由Nextel 440 二氧化硅硼鋁纖維或者Nicalon 的SiC 纖維編織而成的三向織物,三向織物骨架內形成的四邊形或者三角形截面槽溝,需要用形狀匹配的石英氈條填充。采用Nextel 440 編織布需要外涂高輻射率涂料,而Nicalon的SiC 纖維編織布本身具有較高的輻射率,不需外涂涂料,這樣其表面比原來的絕熱縫氈更為平整,具有更好的氣動表面。不過SiC 纖維在溫度高于1 370 ℃時,將出現易脆性。TABI 具有很好的抗氣動噪聲能力。柔性絕熱氈一般采用室溫RTV 硅橡膠粘接到機身。
3. 3 CRI 仿形氈
CRI 仿形氈的性能介于剛性絕熱瓦與柔性絕熱氈之間。以柔性的形式制造,在其被保護的剛性結構表面上定型,最后可固化成剛性制品。CRI 仿形氈的使用溫度范圍可以達到980 ~ 1 093 ℃。其絕熱芯材可以硬化以獲得更平整的表面,而且其尺寸精度也比一般的柔性絕熱氈要高。控制有縫線與無縫線產生的表面高度差在± 0. 38 mm 之間。
表4 為剛性絕熱瓦與絕熱氈采用的涂料及其特性。
3. 4 增強碳陶高溫制品( RCC)
RCC 最早是在20 世紀60 年代早期由LVT 公司在Dyna-Soar 項目中首先開發的。RCC 一般適用于鼻錐部及翼前緣等局部超高溫部位,使用溫度可達1 600 ℃以上。RCC 的制造工藝分原坯工序以及抗氧化工序兩部分。原坯工序主要采用交聯型酚醛樹脂浸漬石墨化的粘膠纖維布,然后將浸漬的石墨布進行層壓固化,對固化后的層壓板進行高溫熱解,將酚醛樹脂轉化成碳陶制品,再用糠醇真空浸漬,然后再次熱解,經多次上述浸漬-固化-高溫熱解工藝,致密基材容重,增加強度,直至容重達到1 602 kg /m3左右。為了提高其高溫抗氧化性能,原坯還需采用包括以下三道工藝組成的抗氧化處理:
1) 通過擴散涂層工藝在其外表面形成一層SiC 來提高其抗氧化能力; 2) 用正硅酸乙酯浸漬并固化,形成一層SiO2涂層,進一步減少裸露的炭; 3) 用帶有SiC 粉末的水玻璃涂覆密封表面的裂紋與孔隙( 0. 51 mm 厚) 。這種炭-炭增強制品具有很低的熱膨脹系數,能夠有效抵抗熱應力及熱震環境。用PAN 纖維布代替粘膠纖維布可在纖維方向獲得強度更高的RCC,這樣的RCC 也可稱之為ACC。
3. 5 航天飛機防熱系統的主要不足
在哥倫比亞航天飛機由于熱防護層失效發生重大災難后,引發了人們對航天飛機防熱系統安全性及可靠性方面更多的反思與討論。每架航天飛機有2 ~ 3 萬片的絕熱瓦,每一次檢查、更換、維修以及表面的防水處理,都需要投入大量的人力、物力與財力,以及消耗大量的時間,同時每次返回大氣層前還需要對絕熱結構做詳細的檢查,稍有不慎,就會釀成機毀人亡的重大事故。因此,傳統航天飛機的防熱系統確實對航天飛機的可靠性及安全性存在一定的隱患風險。除了需要對其高溫熱防護材料進行更新換代外,近幾年還提出了強化型熱防護系統的概念。例如,德國高性能宇航結構系統公司( HPS) 提出的再入大氣航天器安全改進熱防護系統( SAFIT) ,對航天飛行器重要結構部位,如靠近前錐體或者機翼前緣的部位等增加一層二級熱防護層,該熱防護層主要由燒蝕材料或者可瓷化聚合物組成,萬一遇到一級熱防護系統失效,溫度超過規定要求,二級熱防護系統自動激活,以保護航天器再入大氣層余下行程的安全。由于二級熱防護層在一級保護層的內部,通常情況下都無需維護,可以重復使用。盡管二級熱防護層會增加一定的質量,但是航天器的安全性得到了有效的提升,同時也節約了重復使用航天器的檢修成本。典型防熱系統( TPS) 盡管只占航天飛機總質量約10%,但是防熱系統關系到整個航天飛機的安全。
4 升級版航天飛行器防熱材料
4. 1 抗氧化碳陶基輕質絕熱制品
在上一代航天飛機的防熱系統中,增強碳陶制品存在著很多缺陷,如容重大, 一般要達到1 600 kg /m3 ; 制造工藝繁瑣、復雜、耗時,僅僅原坯工藝階段就需要近20 多道的工序,因此,RCC增強碳陶基高溫絕熱制品的成本很高,供貨周期長達12 個月之久。近些年,NASA 新開發出了替代RCC 制品的熱點新材料———抗氧化碳陶基輕質絕熱制品( ROCCI) ,該產品已經多次在X-37B 高超聲速飛行器上得到成功的驗證,并在2011 年獲得NASA 政府年度發明獎。ROCCI 制品具有以下特點: 1) 抗高溫,使用溫度高達1 650 ℃。即使溫度失控超過2 000 ℃,ROCCI 仍然能通過其內部炭的燒蝕來繼續提供一定時間的防熱功能; 2) 抗高溫氧化性能好; 3) 密度輕,典型密度僅為400 kg /m3 左右,并且通過改變工藝參數,可以獲得不同密度的制品; 4) 模塊化設計,便于維修更換; 5) 制造成本低,僅為RCC 制造成本的1%,并且維護成本也較低; 6) 熱膨脹系數低,抗熱震性好,并且具有很好的尺寸穩定性; 7) 與增韌、增強的高溫輻射涂層有良好的匹配性。例如,最新開發的HETC 高溫輻射表面處理劑與其有很好的相容性; 8) 生產周期大大縮短,供貨周期僅為1 個月左右。
4. 2 ROCCI 制品生產工藝及特性
ROCCI 制品采用的C-C 原料氈的典型特性為:
230 kg /m3 的容重,83 %體積的孔隙率以及99. 9 %質量的碳含量,碳纖維的平均直徑為8 μm。目前,ROCCI 采用的標準生產工藝可以簡單歸納為三步法:
1) 浸漬: 硅氧烷凝膠浸漬多孔碳纖維增強氈塊;2) 干燥: 將浸漬有硅氧烷凝膠的多孔碳纖維增強氈塊干燥;3) 高溫熱解。
將干燥后的多孔碳纖維增強浸漬氈塊置于1 000 ~ 1 500 ℃的高溫下進行高溫熱解,熱解一般在惰性氣體中進行。通過熱解工藝,可以將原來的-Si-O-C-鍵轉化成在高溫中更穩定的-Si-C-Si-鍵。這樣,經過高溫熱解處理的多孔碳纖維增強氈塊實際變成了表面覆蓋有SiC 層的碳纖維以及SiC 晶須組成的復合制品。此外,通過延長熱解時間與提高熱解溫度可以進一步提高SiC 的轉化率,得到密度更輕的絕熱制品。通過重復多次的三步法工藝,還可以進一步增加多孔碳纖維增強氈塊中SiC 的轉化率,提高了其高溫抗氧化能力。這種創新工藝也為碳纖維抗高溫氧化性能的改善提供了一種很好的思路。圖2 為標準三步法工藝制成的ROCCI 制品的SEM 圖,圖3 為在惰性氣體Ar 中,1 500 ℃ 高溫下,經長時間( 24 h) 處理得到的ROCCI 制品的SEM。兩者對比可以發現,經長時間高溫下處理,SiC 轉化率明顯提高,同時內部還生長出了很多SiC晶須。圖4 為ROCCI 制品在含氧13% 的Ar 中的TGA 失重曲線,可以用來衡量制品抗氧化能力。
在具體應用時,ROCCI 可與剛性絕熱瓦( 如AETB、BRI 瓦) 組成TUFROC 抗氧化高溫絕熱組件,以便于裝配在航天器的鼻錐及迎風翼部位。此外,采用HETC 表面處理劑增強、增韌的ROCCI 制品外表面還可以涂上改性RCG 涂料,進一步提升其高溫抗氧化能力。剛性絕熱瓦基材與ROCCI 制品可以同時用機械方式以及RCG 結合劑整合成TUFROC 組合體,其中1. 2 mm 厚的RCG 不僅起到粘接的作用,而且在ROCCI 與剛性絕熱瓦之間形成緩解溫度梯度的過渡層。
4. 3 新一代航天飛行器
美國在2011 年停止載人航天飛機項目后,并沒有中止航天飛行器升級換代的研發工作,其中采用與航天飛機熱防護結構相似的代表性升級版航天飛行器主要有兩種,X-37B 無人航天飛行器及追夢者載人航天飛行器。
目前,由波音公司負責開發的X-37B 是2004年由NASA 轉讓給美國國防預先研究計劃局( DARPA),目前由美國空軍快速反應能力辦公室管理。
X-37B 防熱系統基本上沿用航天飛機防熱系統的理念,采用了升級版的航天飛機防熱系統。為了滿足軍事用途,其防熱系統要求比航天飛機的防水、防沖涮性能更好,適應氣候條件的能力更強。X-37B無人航天飛行器上部背風面大面積采用CRI 仿形氈,代替AFRSI 柔性絕熱氈。一方面可以優化航天飛機的氣動阻力,提高負荷能力; 另一方面可以提高安裝效率,便于更換維修,降低使用成本。X-37B的底部迎風面采用硅基剛性絕熱瓦,并且普遍采用TUFI 增強、增韌處理,顯著提高了剛性絕熱瓦的使用壽命。鼻錐及迎風翼等超高溫部位采用Ames 的WLE 防熱結構: BRI-20 絕熱瓦基材+ ROCCI 頂帽+ HETC 表面處理涂層組成的TUFROC 抗氧化高溫絕熱組件。
美國Sierra Nevada Corporation( SNC) 也開發了縮小版的追夢者載人航天飛行器,其防熱系統方案是飛行器底部采用TUFI 增強、增韌處理的AETB-17 剛性絕熱瓦,上部采用AETB 白色剛性絕熱瓦以及FRSI 柔性絕熱氈,鼻錐及迎風翼等超高溫部位采用TUFROC 抗氧化高溫絕熱組件。
5 輕質絕熱瓦的改性
5. 1 改性剛性絕熱瓦
改性剛性絕熱瓦是采用氧化鋁溶膠改性絕熱瓦( ASMI) ,通過對絕熱瓦表面成分的改性,可以有效抑制方石英析晶,降低加熱收縮率,提高使用溫度。圖5 為改性前后AETB 絕熱瓦在不同溫度下的方石英析出量。其采用溶膠-凝膠法的改性工藝為:
采用醇鹽工藝將88% SiO2 + 12% B2O3制成硼酸硅溶膠,該溶膠由部分水解的正硅酸乙酯與硼酸三甲酯的乙醇溶液組成,然后將該溶膠與氧化鋁溶膠配合使用,對剛性絕熱瓦進行改性處理。具體浸漬工藝如下: 首先將輕質多孔絕熱瓦外表面用復合溶膠浸漬滲透至約6 mm 厚,然后在70 ℃下進行干燥,并在500 ℃下燒結1 h。整個工藝可以多次重復直到獲得所希望的成分含量。
5. 2 輕質燒蝕型剛性絕熱瓦
20 世紀90 年代,Ames 通過在孔隙率高達90%以上的剛性絕熱瓦填充有機硅樹脂,開發了輕質燒蝕型剛性絕熱瓦( SIRCA) ,賦予了輕質剛性絕熱瓦新的生命力。SIRCA 的特點介于剛性絕熱瓦與燒蝕型制品之間。與剛性絕熱瓦相比,其承受的熱流密度明顯提高,可承受最大熱流密度可達2 000 kW/m2,例如,由有機硅樹脂填充FRCI-12剛性絕熱瓦獲得的SIRCA-15F, 容重約為264 kg /m3,其承受的熱流密度達1 000 kW/m2。與傳統燒蝕型防熱材料相比,SIRCA 具有以下優點:
1) 在高溫下,自身具有很好的結構穩定性,無需另加增強結構,如蜂窩增強結構;2) 采用多功能、梯度化的聚合物浸漬,以優化燒蝕性與絕熱性之間的平衡;3) 坯料生產成本較低,更為靈活,可實現計算機輔助制造。
該防熱結構已成功用于火星探路者以及火星開拓者兩個項目上,同時也被設計選用為X-34 低成本航天飛行器的鼻錐尖端以及機翼前緣的防熱結構。圖6 為剛性絕熱瓦與其對應的燒蝕型剛性絕熱瓦以及其它燒蝕型制品的導熱系數的比較。SIRCA的機加工性能好,無需進行后處理、熱處理以及額外的涂層處理,是今后低成本航天飛行器防熱結構的重要候選材料。
5. 3 氣凝膠改性剛性絕熱瓦
由于剛性絕熱瓦孔隙率很高,達到90% ~96%,削弱了其絕熱性能,因此,可以采用氣凝膠填充或者紅外遮蔽劑來處理,以提高其絕熱性能。
例如,多孔剛性絕熱瓦中的纖維用紅外輻射遮蔽涂層包裹處理來提高其隔熱性能。波音公司Andrea OBarney 用硅鋁氣凝膠填充高溫多孔纖維絕熱瓦,以提高其絕熱性能。NASA Ames 研究中心SusanWhite 通過用氣凝膠浸漬AETB-8 多孔絕熱瓦,制成的復合絕熱制品既可用于低溫絕熱,又可以用于高溫絕熱,有望用于航天飛行器推進劑超低溫儲存的一體化絕熱結構。圖7 為浸漬氣凝膠AETB-8 與非浸漬AETB-8 在真空及大氣壓下的導熱系數比較。然而,也有報道用硅鋁氣凝膠浸漬AETB-12 會惡化其加熱收縮率,因此,氣凝膠的填充要避開其高溫面。
6 超高溫防熱結構
某些超聲速飛行器,如吸氣式高超聲速飛行器,需要水平起飛,在大氣層中加速、巡航,而且必須在低海拔的大氣中吸取空氣作為發動機的氧化劑。此外,這類高超聲速飛行器的體積與形狀對升阻比的影響極大,為了獲得更高的升/阻比,需要有一個薄而纖細的低厚弦比外形結構。因此,吸氣式高超聲速飛行器所有系統必須高度集成,需要承受更高的氣動壓力。另外,吸氣式高超聲速飛行器上面攜帶的液氫燃料罐超低溫儲存于- 253 ℃,而飛行器的外表溫度達到1 093 ~ 1 650 ℃。因此,其防熱結構要在有限的空間里克服巨大的溫度梯度。
為了減輕高超聲速飛行器鼻錐處氣動加熱的強度,一般需要對其鼻錐進行適當的鈍化處理,但是對于典型的吸氣式超聲速飛行器,尖銳的鼻錐處產生的激波有利于最大化流進發動機的空氣流量。因此,其尖端前緣將承受更高的熱負荷,其溫度可達2 000 ℃以上。為了避免熱結構溫度梯度太大,其尖端前緣一般使用導熱性能良好的纖維增強碳陶復合材料或高溫復合陶瓷材料作為熱結構材料,以減緩熱結構的局部超高溫熱點。
能夠在2 000 ℃以上氧化氛圍中使用的超高溫陶瓷材料( UHTCs) 并不多,目前研究最多的是碳系化合物和硼系化合物,但它們的抗氧化性能相對較差,材料的本質脆性使其斷裂韌性較低,且加工難度較大。碳陶復合材料在高溫環境下自身的抗氧化性能和耐燒蝕性能較差,因此,國內外研究學者將碳陶復合材料的改性研究作為該材料體系的研究重點,通常采用難熔碳化物,如SiC、HfC、TaC、NbC、ZrC 等涂層來提高其抗氧化能力,但是由于性能匹配問題,涂層系統在1 700 ℃以上的使用效果并不理想,同時碳陶復合材料制作工藝比較復雜,成本較高也限制了其應用。目前研發的主要硼系UHTCs材料有二硼化鉿以及二硼化鋯陶瓷,其成分內添加有適量的SiC 助劑用于降低陶瓷的燒結溫度及改善抗氧化性。此外,二硼化物導熱性良好,以此降低尖端極值溫度,緩解溫度梯度,由于這些超高溫陶瓷材料非常脆,因此,目前正在研究多種添加劑,如SiC、碳納米管、銥涂層以及TaSi2 來增韌,增強以及改善抗熱應力能力。也有研發人員采用擠出法制造纖維增強ZrB2-SiC 陶瓷制品,以改善其抗熱震性。此外,UHTCs 在高溫下與氧原子重新結合的催化效率以及熱輻射率也是UHTCs 的重要性能指標。
除了開發新型UHTCs 材料,開發合適的冷卻方案也是目前的重要任務。例如,將一些金屬管埋在CMC 的機翼前緣中,通過泵入冷卻劑來帶走熱量;又如,將吸熱型碳氫燃料流過帶有催化金屬陶瓷涂層的系列熱交換器,將燃料進行高溫裂解的同時生成了燃燒性能良好的高純小分子燃料; 再如采用半被動隔熱概念,利用熱管將工作流體將熱量從高溫區帶走,回流到飛行器面積較大的區域,通過熱輻射將熱量驅離飛行器。盡管采用主動冷卻系統會增加系統的成本、復雜性以及重量和體積,但對于高熱負荷的區域是必須的。
此外,碳納米管復合材料也將為未來航天飛行器的防熱設計帶來全新的革命性變化。碳納米管材料的楊氏模量超過1012 Pa,抗張強度達2 × 1011 Pa,雖然其質量只有鋼材六分之一,強度卻比鋼材高上百倍。沿納米管軸向的導熱系數高達3 000 W/m·K; 而垂直于軸向的導熱系數只有0. 25 W/m·K,基本上成為了絕熱體,而且碳納米管材料的導電性能也非常獨特,可以制成導電體、半導體及絕緣體,并具有壓電特性。這些優異的性能特點都為今后碳納米管基復合材料在高超聲速飛行器中的應用提供了巨大的想象空間。
7 結束
語目前,熱防護系統,特別是超高溫防熱結構仍然是開發高超聲速飛行器的重點技術之一。隨著新型航天材料的技術進步,高超聲速飛行器的熱防護系統也將會有不斷的更新升級換代,特別是新型碳納米管復合材料有望成為未來高超聲速飛行器防熱系統的首選材料之一。
另外,伴隨著高超聲速飛行器熱防護材料與技術的發展,也將帶動其它工業領域的高溫絕熱材料以及超高溫結構材料的技術升級。例如,美國利用其成熟的剛性絕熱瓦以及柔性高溫絕熱毯制造技術,開發了各種一體化高溫絕熱結構材料,即便是在當今,其高溫剛性纖維絕熱制品以及高溫纖維織物,無論在品種上,還是在品質上仍然是出類拔萃的。可以期待我國高超聲速飛行器熱防護材料與技術的開發同樣也必將有力推動我國工業高溫絕熱材料以及超高溫結構材料的發展。
更多關于材料方面、材料腐蝕控制、材料科普等方面的國內外最新動態,我們網站會不斷更新。希望大家一直關注中國腐蝕與防護網http://www.ecorr.org
責任編輯:王元
《中國腐蝕與防護網電子期刊》征訂啟事
投稿聯系:編輯部
電話:010-62313558-806
郵箱:fsfhzy666@163.com
中國腐蝕與防護網官方 QQ群:140808414
免責聲明:本網站所轉載的文字、圖片與視頻資料版權歸原創作者所有,如果涉及侵權,請第一時間聯系本網刪除。
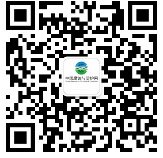
官方微信
《中國腐蝕與防護網電子期刊》征訂啟事
- 投稿聯系:編輯部
- 電話:010-62313558-806
- 郵箱:fsfhzy666@163.com
- 中國腐蝕與防護網官方QQ群:140808414