陶化工藝有時又稱鋯鹽鈍化工藝、納米陶瓷工藝等,是指以鋯/鈦等金屬的氧化物在材料表面沉積,以獲得類似陶瓷表面的金屬氧化物涂層。近年來,陶化工藝作為最有希望代替傳統高污染磷化鈍化及鉻酸鹽鈍化的技術之一獲得了快速發展,已開始在金屬表面處理中廣泛應用。目前,某些商用陶化技術耐蝕性已基本達到六價鉻鈍化水平。
鈦/鋯基陶化工藝目前仍處于快速發展階段,種類多種多樣,與六價鉻鈍化工藝不同,尚未有通用的最優配方。因此,不同工作中針對不同種類鈍化劑所提出的成膜機理也往往差別很大。按照原料鈦/鋯化合物種類,可以大體將其分為水解縮合及絡合離解兩大體系。
水解縮合主要用于解釋鈦酸異丙酯,鈦酸正丁酯,硫酸氧鈦,碳酸鋯銨,乙酰丙酮鋯等可水解的有機鈦/鋯化合物前驅體成膜過程。絡合物離解沉淀一般用于解釋氟鋯酸/氟鈦酸體系成膜過程。
目前,金屬陶化工藝的具體實施方法主要有浸泡法、噴淋法、電泳沉積法、涂覆 (輥涂或刷涂) 法等幾種,實際實施方法則主要取決于應用領域。按照施加處理液后是否需要水洗,又可分為水洗后干燥及直接干燥兩大類。其中,用于浸泡及電泳沉積的陶化液一般需水洗除去多余的未沉淀離子,而用于刷涂法的陶化液一般不可水洗直接干燥,不過也有例外。
1 金屬陶化劑配方研究進展
單獨使用鈦/鋯化合物作為成膜主劑,所得膜層往往為疏松多孔的網狀結構[10],難以提供理想的耐蝕性。因此,實際配方研究中一般需將鈦/鋯基化合物與一種或多種輔助成膜組分共同使用。其中,最常見的輔助成膜劑為具備封孔作用的各類硅烷偶聯劑,另外還有具有緩蝕或自修復作用的金屬離子,植酸、單寧酸等有機緩蝕劑,水溶性聚合物或聚合物水性乳液等。此外,近期也有少量陶化主劑本身的優化研究的報道。
1.1 鈦/鋯-硅烷體系復合
由于硅烷偶聯劑進行硅烷成膜的工藝具有無毒、污染小、適用性廣泛等眾多優點,將硅烷偶聯劑用于金屬表面處理已成為相關領域的一個主要研究熱點。通常認為,硅烷偶聯劑的成膜作用是依靠硅烷與金屬氧化層表面的羥基脫水連接,生成Me-O-Si鍵橋固定在材料表面,同時硅烷偶聯劑本身相互交聯形成主要為硅-氧結構的膜層。
Voevodin等提出,以四丙氧基鋯 (TPOZ) 和縮水甘油氧基丙基三甲氧基硅烷 (GPTMS) 配合,可在鋁合金表面獲得具備良好性能的溶膠-凝膠復合涂層,有望在航空工業中取代傳統的六價鉻涂層。由于鈦、鋯化合物陶化膜的性能與硅烷成膜特性具有互補性,將這兩類成膜劑共同使用形成有機-無機復合膜的工作已有不少報道,有部分種類已開始在實際生產中應用。文獻[13]報道的鍍鋅板用輥涂鈍化液配方為γ-縮水甘油醚氧丙基三甲氧基硅烷0.2%~2.0%、聚乙烯醇0.0~1.0%、碳酸鋯銨0.1%~3.0%、余量為水,適合輥涂后干燥使用,所得鈍化鍍鋅板中性鹽霧實驗144h無白銹,與含鉻彩色鈍化性能相當。文獻報道了一種以含氨基的硅烷偶聯劑預聚物及鈦/鋯化合物作為主要成膜材料的鈍化液配方,另外還含有游離氟離子、選自Mg、Zn、Ca、Al、Ga、In、Cu、Fe、Mn、Ni、Co、Ce、Sr、Sn及稀土元素的至少一種金屬元素、含氧酸氧化劑、以及表面活性劑。該鈍化液可浸漬或輥涂成膜,涂層附著力和耐蝕性良好,且具有優異的儲存穩定性。
文獻公開了一種雙組分陶化-硅烷復合轉化膜,A組份包含成膜主鹽、氧化性成膜促進劑、緩沖劑及表面活性劑,涂覆干燥后形成0.5~1 μm厚的底層無機化學轉化膜;之后使用包含水、硅酸鹽、硅烷、硅溶膠、鈦酸酯、鋯酸酯、水性樹脂及助劑的B組份形成2~3 μm厚的頂層有機封閉膜。該轉化劑可采用刷涂,輥涂,噴淋等方式施加,可用于船體等大尺寸金屬構件防腐,膜層具備優良的耐蝕性和抗玷污性,中性鹽霧試驗可達336 h以上不變色。王寧濤等采用電鏡及電化學方法對鈦鹽-硅烷兩步法復合鈍化膜的表面形貌及性能進行了研究,認為復合鈍化層耐蝕性主要來自其厚度導致的阻隔效果,硅烷膜層對鈦鹽鈍化層起到封孔作用。
1.2 具備緩蝕性能的金屬離子添加劑
為改進陶化涂層的耐蝕性能,與傳統的磷化技術相似,向陶化液中添加具有緩蝕性能的金屬化合物的工作已有報道。Moutarlier等采用溶膠-凝膠法,以四丙氧基鋯及硅烷為前驅體在鋁合金表面制備了鋯-硅烷鈍化層,并采用電化學方法測試了不同種類的金屬離子添加劑對該涂層耐蝕性的影響。結果表明,六價鉻離子可以有效提升涂層的長期耐蝕性能;三價鈰鹽由于其高水溶性會從涂層中迅速流失,因而對涂層耐蝕性沒有明顯幫助;六價鉬鹽及七價錳鹽的添加則導致涂層中生成高可溶性的結晶,對涂層結構造成破壞,因此反而導致涂層耐蝕性能的下降。已有研究中將鉬鹽及鈰鹽使用載體固定,以阻止其快速釋放,維持緩蝕作用并避免破壞涂層結構。Montemor等以ZrO2納米顆粒作為載體;Dias等以沸石作為載體分別實現了鉬離子的引入;Yasakau等以鉬酸鈰晶體納米線一次向鋯-硅烷涂層中引入鈰及鉬兩種元素,并以電化學方法證實了涂層耐蝕性能得到顯著提升。
單獨使用釩鹽可在金屬表面形成鈍化層,且具有一定的自修復能力,但其耐蝕性相對較差[21,22]。Zhong等[23]以H2ZrF6與NaVO3為主劑,并加入NaNO3及硼砂配制成鈍化液,以浸泡法制得釩-鋯氧化物復合結構為主的鈍化膜。其耐蝕性及附著力良好,且涂層劃傷后其中所含的V5+可與水反應生成釩鹽水合物VO(OH)3(H2O)2阻塞斷口,因此具有一定的自修復能力。專利[24]公開的鋁合金釩-鋯鈍化劑配方為:氟鋯酸 (質量濃度40%~50%) 30 g、偏釩酸鉀10 g、氟化鈉2 g、硝酸鈣12 g、檸檬酸40 g、雙氧水20 g、去離子水900 g,使用時稀釋10倍,浸泡-水洗工藝。成品在腐蝕環境 (pH值為3的3.5%NaCl溶液,質量分數) 中浸泡2 h后,在3.5%NaCl溶液中表面電阻率從1.622×105 Ωcm2上升至3.198×105 Ωcm2,說明其具有一定的自修復能力。
1.3 鈦/鋯-有機緩蝕劑復合
單寧酸和植酸等有機緩蝕劑可與金屬離子配位,形成配合物吸附在金屬表面,所得膜層均勻致密,但膜層極薄且與基體間附著力較差,無法提供足夠的耐蝕性能。與鋯/鈦基陶化劑共用時,有機緩蝕劑的存在對膜層致密度及耐蝕性能可起到一定的改善作用。
杜文朝等對有機緩蝕劑的研究表明,在鋯鹽鈍化液中加入0.75 g/L鞣酸后,轉化膜的自腐蝕電流密度由1.088×10-6 A/cm2降低至3.817×10-7 A/cm2。其經過正交試驗得出的最佳配方為鞣酸1.00 g/L、K2ZrF6 0.75 g/L、NaF 1.25 g/L、MgSO4 1.0 g/L、Ti(OBu)4 0.08 g/L,處理溫度為室溫,時間10 min;以該鈍化劑處理后,材料的自腐蝕電位由4.7×10-6 A/cm2降至9.7×10-8 A/cm2,表明鈍化層具備一定的耐腐蝕性能。Yi等以H2TiF6 2.0~3.0 g/L、H2ZrF6 1.5~2.5 g/L、NaF 2.0~3.0 g/L、單寧酸2.0~3.0 g/L在鋁合金表面制備了具有均勻明顯金色外觀的復合鈍化層,彌補了陶化膜層無顏色導致實際生產時難以判斷成膜完整性,客戶接受程度低的缺陷。專利[27]公開了一種雙組分鈦/鋯-有機緩蝕劑復合鈍化劑,A組分包含氟鋯酸、氟鈦酸、氫氟酸、植酸、單寧酸等成膜物質,B組分為助劑,使用時稀釋后混合,采取噴淋或槽浸循環攪拌,在常溫條件下可對Fe、Zn、Al等多種金屬材質進行陶化處理,所得膜層各項性能指標滿足陶化膜質量要求。
1.4 鈦/鋯-樹脂復合
高聚物樹脂因其本身具備的特殊性能,通常是一種優良的成膜材料,將樹脂溶解在有機溶劑中制成的防銹油漆已經得到了極其廣泛的應用。樹脂防銹層具有特別優良的潤滑性、致密性及與油漆的相容性,但單獨使用薄層樹脂作鈍化膜時,其機械性能及附著力不夠理想,導致耐蝕性能不佳。與鋯/鈦基陶化劑共用時,樹脂可以明顯提高膜層的耐蝕性能,但需選用與無機組分相容性較好的樹脂種類。
專利報道了一種鈦/鋯鹽-樹脂無鉻涂層劑,其含有100 mg/kg Zr元素濃度的氟鋯酸及100 mg/kg水溶性含氨基樹脂,以及氧化性含氧酸或還原性有機酸等促進劑,并用氫氧化鈉調節pH值至4。該涂層劑適用常溫浸漬-水洗工藝,可在冷軋鋼、鍍鋅鋼及鋁合金等金屬表面獲得性能良好的涂層。文獻報道了一種鋯/鈦-樹脂復合鈍化液,其組成 (質量分數) 為:氟鋯/鈦酸鉀、氟鋯/鈦酸鈉、氟鋯/鈦酸等鈦鋯化合物12~16份,氫氟酸、氟化鈉、氟化鉀、氟化銨等氟化物3~4份,丙烯酸和馬來酸酐的共聚物、丙烯酸衣康酸的共聚物、聚丙烯酸、聚丙烯酸鈉等水性高分子樹脂3~5份,二氯氧化鋯 (鈦) 1~3份,甲酸、乙酸、馬來酸等小分子有機酸3~4份,非離子表面活性劑0.1~0.5份,水65~75份。該陶化液具有穩定性好,成膜均勻,附著力強等優點,適合常溫噴淋和浸泡處理,且成本較低。Niknahad等[30]的研究表明,加入聚丙烯酸及聚丙烯酰胺可對氟鋯酸型鋁合金鋯鹽鈍化膜的耐蝕性產生明顯的增強作用,但仍不及傳統含六價鉻磷化工藝;傅里葉變換紅外光譜 (FT-IR) 及掃描電鏡 (SEM) 表征表明,聚丙烯酸分子中的羧基可以與氧化鋁表面的鋁離子及聚丙烯酰胺分子中所含的氨基間建立靜電相互作用,部分填充鈦鹽轉化膜的孔隙,從而提升膜層的耐蝕性。
1.5 多組分復合
在金屬鈍化領域中,僅靠一種成膜材料形成的鈍化層常常在耐蝕性,附著力,長期穩定性等某一兩個方面存在缺陷,從而影響實際應用。因此,在近期的配方研究,特別是一些相關企業的研究中,鈦/鋯基陶化常常與磷化、硅烷化、聚合物體系等鈍化工藝共同使用,以獲得可與鉻酸鹽系涂層相比擬的、具有實際使用價值的復合涂層。目前,此類研究大多以專利形式發表,一些在本領域具有技術優勢的國外企業已公開了大量的相關專利文獻。近幾年來,國內以專利等形式公開的類似配方也逐漸增多。
文獻報道了一個適用于連續線原位干燥的典型無鉻鈍化液配方,其優選包含有一種或兩種反應性硅烷偶聯劑,0.1%~5%的金屬離子,0.1%~10%的氟鈦酸,氟鋯酸或氟硅酸等氟化物,以及水性樹脂乳液。文獻報道的連續線輥涂法耐指紋鈍化液配方為:硅烷偶聯劑改性硅溶膠3%~10%,水性樹脂乳液40%~70%,部分甲醚化的改性氨基樹脂2%~15%,多異氰酸酯乳液2%~10%,選自氟鈦酸銨、碳酸鋯銨或氟鋯酸銨中的一種無機鹽1%~5%,水性聚乙烯蠟漿1%~6%,附著力促進劑1%~9%,流平劑0.1%~0.5%,余量為水。文獻報道的鍍鋅鋼輥涂鈍化劑配方為:10%~20%的含氨基硅烷偶聯劑、25%~50%的含烷氧基硅烷偶聯劑、0.1%~5%的氟鈦酸、氟鋯酸或氟硅酸等氟化物、0.01%~0.5%的含磷化合物、以及30%~60%的水性聚氨酯乳液。專利中報道了一種含有鉬的含氧陰離子以及一種具有特定分子結構 (類似氨甲基羥基改性聚苯乙烯結構) 的聚合物螯合劑的無鉻鈍化液配方,配方中另外還包含1%~3%的磷酸,0.1%~5%的選自氟鈦酸、氟鋯酸、氟硅酸或氟鉿酸的六氟化物酸,0.4%~1.2%的鋅離子和/或錳離子等金屬離子,以及15%~50%的水溶性樹脂或水性樹脂乳液。徐麗萍等[35]以硅烷偶聯劑、磷酸鹽、氟鈦酸鹽為成膜劑,鉬酸鈉和釩酸銨作緩蝕劑,以輥涂法制備了無機-有機硅烷復合鈍化膜,其耐蝕性能接近鉻酸鹽鈍化膜。
另外,有許多復合鈍化劑配方中均將氟鋯酸等陶化試劑作為輔助成膜組分使用,已難以歸屬于陶化工藝范疇,在此不再贅述。
1.6 陶化劑優化研究
文獻提出,在生產中,鋯基鈍化液中常含作為添加劑添加或來自水或被涂布的金屬工件中的Cu及Cu離子,其沉積在預處理涂層后會對性能產生負面影響。實驗表明,向鈍化液中加入含多羧基或膦酸官能團的Cu離子螯合劑后,鋯基預處理液的二次涂漆附著力及儲存期限有明顯提高。文獻[37]提出,在陶化涂層的電沉積涂裝過程中,如果使鍺化合物、錫化合物和/或銅化合物與鈦/鋯化合物同時析出形成復合膜,可以大幅改善電沉積涂裝的泳透性,并獲得具有更高的耐腐蝕性及涂料密合性的膜層。其報道的典型配方包含0.5 mmol/L GeF4、0.1 mmol/L H2TiF6、0.5 mmol/L H2ZrF6、2 mmol/L Al(NO3)3、1 mmol/L Zn(NO3)2,補加HF至F總量10 mmol/L,并以氨水調節pH值至3.7。該鈍化液適用于浸漬后水洗或電泳后水洗工藝,經鈍化處理后,材料橫切后腐蝕寬度由4~5 mm降低至1.9 mm,具有更佳的耐腐蝕性能。
文獻提出,鈦/鋯基鈍化液中的F元素與Zr元素摩爾比控制在F∶Zr=6以上,并同時加入Cu2+源及選自Ca、Mg、Al、B、Fe、Mn、W的一種或多種金屬離子源作為“F離子抑制劑”,可得到性能最佳的鈍化層。其典型配方包含H2ZrF6、(NH4)HF2、Cu(NO3)23H2O及Fe(NO3)39H2O。文獻[39]則提出,將鋯-硅烷系鈍化液中的F元素與Zr元素摩爾比控制在F∶Zr=3~6之間時,所得的鈍化層將主要以Zr(OH)4的形式沉積,因此含有較少的ZrF6-n(OH)n沉淀,與常規配方制備的鈍化層相比,其耐蝕性及二次涂漆附著力有明顯提升。
專利報道了一種不含磷酸鹽和氟化合物的硅烷/陶化浸漬鈍化液配方,包含納米二氧化硅顆粒和/或硅烷偶聯劑、金屬離子、水溶性樹脂、水溶性鈦化合物和/或鋯化合物、以及用于穩定鈦/鋯化合物的含數個羥基、氨基或膦酸基的有機化合物,該有機化合物可以替代氟鋯酸/氟鈦酸的部分作用,在儲存條件下穩定Ti/Zr離子,接觸到鋼板表面pH值升高之后又可使Ti/Zr元素析出沉積。該配方從源頭上徹底消除了含氟污染物的產生,從而更為環保,并節省了處理氟化合物所需大型廢水處理設備的建造費用。
2 陶化過程工藝和機理研究進展
2.1 陶化膜組成及顯微結構研究
目前,金屬鈍化領域的研究主要由相關企業開展,研究成果多以配方專利形式公開,存在著“重應用輕理論”的現象。陶化工藝雖已有數十年歷史,但目前對其成膜過程及膜層結構的系統研究仍不是很充分,尤其是多種鈍化組分共同使用時復合膜的形成過程與膜層結構仍有不清楚之處。
Cerezo等以加入少量銅化合物的氟鋯酸溶液作為鈍化劑 (漢高公司提供) ,采用浸泡工藝分別在6014鋁合金、冷軋鋼及熱浸鍍鋅鋼表面制備了鋯基鈍化膜。AES分析顯示熱浸鍍鋅鋼表面所形成的鈍化膜層最厚,冷軋鋼鈍化膜其次,6014鋁合金鈍化膜最薄;X射線光電子能譜 (XPS) 分析表明,大部分Zr元素在鈍化膜中以ZrO2的形式存在,且鈍化液與金屬基底反應產生的化合物如Al2O3、ZnO、FeOOH、FeF3、ZnF2和AlF3,與ZrO2相比含量較少;FE-AES Cu圖顯示,沉積在冷軋鋼和熱浸鍍鋅鋼上的涂層中,Cu均勻分布在表面上;而6014鋁合金中的Cu元素出現島嶼狀聚集,表明銅的沉積受到局部金屬氧化物/氫氧化物溶解和金屬底物的影響。Saarimaa等使用ToF-SIMS及XPS等方法對鍍鋅鋼表面的輥涂鈦鹽鈍化層進行了分析,結果表明,鈦鹽鈍化層主要依靠阻隔作用提升耐蝕性,其耐蝕性與表面均勻性正相關;與含鉻涂層相比,鈦鹽涂層均勻性受鍍鋅鋼基板表面清潔度影響較大。Mohanmadloo等研究了氟鋯酸鈍化劑 (漢高公司商品Bonderite NT-1) 在冷軋鋼表面的成膜過程和膜層顯微組織。電鏡觀察表明,鈍化層由50 nm結節和直徑100~500 nm的較大簇組成,可分為由基體金屬和鋯氧化物組成的下層和由鋯氧化物及氟化物組成的上層兩部分;電化學分析表明,樣品經表面處理后腐蝕電位升高,且處理浴溫度的升高 (由20 ℃上升至40 ℃) 導致鈍化層出現大量微裂紋,并導致腐蝕電流密度增加和極化電阻降低;處理浴pH影響涂層表面形態,對鈍化層抗腐蝕性能影響較小。
2.2 陶化過程工藝參數研究
與含鉻鈍化技術不同,鈦/鋯鹽陶化技術所用原料多種多樣,成膜機理也有主要依靠絡合物離解及主要依靠水解縮合兩大類,且常常加入其它輔助成膜組分以獲得實用程度的耐蝕性能,因此,不同配方所需的工藝參數往往差異很大。目前,鈦/鋯鹽陶化工藝優化研究均針對特定配方開展,其具體工藝參數無法推廣至整個陶化技術領域,但鈍化層形貌及性能與工藝參數的相關性分析具備一定的參考價值。
Mohammadloo等對氟鋯酸體系鈍化劑的研究表明,在浴液溫度20~30 ℃、浸泡時間60~120 s、pH值為4、酸濃度4%時可獲得性能最佳的鈍化層。楊進采用電化學方法研究了鋼鐵表面氟鋯酸體系鈍化液的成膜過程后提出,按照開路電位及EIS等效電阻變化可將成膜過程分為基體酸蝕活化、膜快速生長、膜減速生長、膜動態穩定以及膜溶解等五個階段;在成膜溫度為35 ℃、成膜時間為5 min的條件下,當主成膜劑鋯濃度為160 mg/L、pH值為4.0時,能夠在鋼鐵表面獲得耐蝕性最佳的氧化鋯轉化膜。
Zhu等以四氯化鈦為鈦源,配合氟硅酸和硝酸對鍍鋅鋼進行了鈍化處理,并研究了不同工藝條件下鈍化膜產生白銹時間的區別,結果顯示:pH值2.5~3.5之間時鈦鹽可以有效沉積;鈍化膜性能隨浸泡時間增大而改善,時間達到250s時最佳,隨后快速下降;浸泡溫度50 ℃時,鈍化膜性能最佳。Tsai等研究了三氯化鈦、氟硼酸鈉及硝酸鈉組成的鈦鹽鈍化浴在鍍鋅鋼板表面的成膜特性:EIS測試顯示材料浸泡200,300和500 s后所形成的涂層電阻分別為0.5,22.8和0.7 kΩ;SEM觀察表明,浸泡時間過短時所形成的涂層不夠完整,浸泡時間過長時所形成的涂層包含大量微裂紋。
Sako等以5%碳酸鋯銨水溶液作為鋯源,研究了固化溫度對輥涂鋯鹽涂層結構及性能的影響。結果表明,在80 ℃下固化時,涂層在中性鹽霧試驗中的耐腐蝕性優異,并隨固化溫度的升高而降低;固化溫度升高至160 ℃以上后,涂層性能變差。DSC測試表明,涂層固化時,在115 ℃和155 ℃有顯著的吸熱峰,115 ℃時鋯原子失去與其配位的水分子;155 ℃時鋯氧化物羥基間的氫鍵出現縮合脫水,造成涂層體積收縮,導致涂層表面上裂縫的發展。
Feng等研究了工藝參數對鋁合金表面浸泡法TPOZ/GPTMS復合鈍化膜層形貌及涂層耐蝕性能的影響,并分析了不同狀態下膜層上裂紋產生過程的差異。實驗結果表明,GPTMS與TPOZ的摩爾比對成膜過程有明顯影響,GPTMS組分的增加會減少膜層干燥時的收縮和交聯,并導致膜層開裂傾向的降低,但同時會使涂層阻隔能力降低;基體抽提速度的增加會導致涂層厚度增大,可提高涂層的耐蝕性,但更易引發裂紋及第二相缺陷;提高烘烤溫度有助于減少涂層開裂傾向并提高涂層耐蝕性,在GPTMS/TPOZ摩爾比為2.7,抽提速度180 mm/min,烘烤溫度110 ℃的工藝條件下可制得約1 μm厚、耐蝕性能良好的光滑無裂紋厚涂層。Álvarez等以TPOZ及GPTMS復合鈍化劑分別對經脫脂處理,物理拋光及化學刻蝕 (酸蝕) 處理后的鋁合金材料進行了鈍化處理。中性鹽霧測試表明,表面經物理拋光后所制備的鈍化膜耐蝕性能最差,而經脫脂處理的表面鈍化層盡管在最初3 d較早出現點蝕,但在長期測試中表現出比酸蝕后的粗糙表面更佳的耐蝕性能,表明鋁合金表面氧化層參與鋯硅烷鈍化層成膜過程,并對鈍化膜的最終性能有積極影響。
3 總結與展望
隨著環保壓力的日益增大,工業界迫切需要一種高污染的磷酸鹽/六價鉻鈍化工藝的環保型替代方案。在這一推動力的作用下,鈦/鋯鹽陶化工藝得到了飛速發展。最近數年來,以氟鋯酸/氟鈦酸體系為基礎的陶化劑已在多家企業中實現了工業化生產,并在家電板用鍍鋅鋼等高附加值產品生產中基本替代了六價鉻鈍化工藝;溶膠-凝膠法工藝也已基本達到實用化水平,并正在進入大規模產業化階段,已在一些企業中開始使用,正在實現對傳統磷化浴工藝的替代。
盡管很多陶化涂層耐蝕性能已接近或超過磷酸鹽/六價鉻涂層,但在工藝穩定性及成本控制方面仍未達到傳統工藝水平,并常需使用氟鋯酸/氟鈦酸等具有較高毒性及環境危害性的原料。因此,目前的多組分復合陶化體系在配方優化方面仍有大量工作需要完成。
可以預期,隨著這一領域的研究逐漸深入,人們對陶化成膜及膜層失效過程的理解將更加透徹。未來,陶化工藝將在現有基礎上進一步朝著功能化、差異化的方向發展,如光固化涂層,自修復涂層,自清潔涂層等新型功能涂層也將進入實用化階段。
免責聲明:本網站所轉載的文字、圖片與視頻資料版權歸原創作者所有,如果涉及侵權,請第一時間聯系本網刪除。
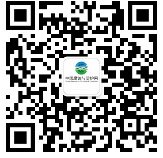
官方微信
《中國腐蝕與防護網電子期刊》征訂啟事
- 投稿聯系:編輯部
- 電話:010-62313558-806
- 郵箱:fsfhzy666@163.com
- 中國腐蝕與防護網官方QQ群:140808414