2013年,中航工業副總工程師、殲-15總設計師孫聰在接受新華社專訪時透露,國內鈦合金和M100鋼的3D打印技術已廣泛用于新機的設計試制過程。殲-15的主承力部分,包括整個前起落架,即是采用國產3D打印機和高強度鈦合金粉末制造而成。
殲-15艦載機
實際上,采用3D打印制造飛機起落架,并不是一項簡單的事情,尤其是對于大型民機來說,這與起落架的功能和性能要求密切相關。本期我們就來聊一下飛機起落架的材料構成和3D打印制造技術。
▌飛機起落架的制造材料和傳統制造特點
無論起飛還是降落,起落架都是支撐飛機的唯一部件,尤其是在飛機降落階段,其承載的載荷不僅來自機身重量,還有飛機垂直方向的巨大沖力。因此,起落架的材料強度必須十分優異。此外,由于復雜的受力情況,起落架材料還必須具有超韌性、抗疲勞和和耐腐蝕的性能。
現代大型客機多采用支柱套筒式起落架,由外筒和活塞桿套接起來的緩沖支柱組成,機輪直接連接在支柱下端,支柱上端固定在飛機機體骨架上
傳統上,起落架的主要承力構件均采用大型整體鍛件進行制造。材料多選用低合金鋼、鈦或鋁的合金,如波音787起落架主支柱外筒采用300M鋼鍛件,緩沖支柱活塞桿是鈦合金整體鍛件,這種整體的結構取代拼焊結構,能夠有效提高壽命。在材料性能方面,300M鋼的抗拉強度很高,達到1860Mpa,其橫向塑性、斷裂韌性和抗疲勞性也都很高,是大型飛機起落架的主導應用材料。鈦合金因重量輕、強度高也被廣泛用于起落架主承力構件上。
起落架鋼材料多采用真空感應加真空自耗重熔,材料冶煉成本高,因此材料價格較高。而起落架外筒及活塞桿為筒狀構件,采用傳統鍛造+機加的制造方法,筒內實心部分需要采用深鏜切削加工去除,易造成材料浪費,且加工難度大,制造周期長;特別是面對當前飛機型號的快速試制時,采用鍛造工藝制造起落架將面臨原材料尺寸規格限制、不利于快速響應等諸多技術問題。另外,當前的加工方法也限制了部件結構設計,從而使強度重量比無法得到有效改善。因此在滿足材料性能的前提下,如何節約成本和簡化工藝成了一個亟需解決的問題。
▌國內外飛機起落架3D打印制造技術
國內外采用激光直接沉積進行飛機起落架的制造研究自多年前已經開始,現在看來這種技術是可行的。航空工業沈陽飛機設計研究所高級工程師崔燦指出,激光直接沉積成形對于飛機起落架制造具有‘變革性’意義,它能突破規格限制、減少原材料浪費、縮短加工制造周期,在未來飛機起落架快速試制方面具有較為明顯的技術優勢及應用前景。
激光熔化沉積過程
采用金屬3D打印制造飛機起落架最大的質疑在于能否達到傳統鍛件的性能。該研究所目前已突破 A-100 鋼激光直接沉積增材制造成形工藝、性能質量控制等關鍵技術,已有效解決飛機型號研制中存在的復雜構型超規格結構試制技術瓶頸,實現起落架外筒及活塞桿等大型關鍵承力構件的無模敏捷快速試制。目前由該單位試制的起落架零件已在飛機上實現領先試用,力學性能基本達到材料鍛件水平。
A-100鋼激光直接沉積成形飛機起落架
國內北京航空航天大學擁有目前國內最大的金屬3D打印機,其外部尺寸達12米長,可為中國商用飛機、軍機項目制造大型復雜部件,包括鈦機身骨架及高強鋼起落架。2006年,北航已采用激光能量沉積技術為某型號飛機起落架生產關鍵零部件,至2014年已經受2000多個起落的實際飛行。如果沒有該技術,此型號飛機的驗證可能要推遲兩年。2008年,北航獲得300M鋼的激光成形技術專利。實際上沈陽飛機設計研究所制造的飛機起落架也有北航的身影,其采用激光直接沉積的飛機起落架A-100鋼,抗疲勞強度比鍛件高20%。
激光直接沉積A-100鋼最終熱處理后的主要技術指標
國外方面,今年6月加拿大金屬3D打印研究機構 Burloak Technologies與法國賽峰集團簽署了備忘錄,兩家公司計劃采用DED技術制造飛機起落架系統部件。9月12日,賽峰集團與Norsk Titanium也簽訂了采用快速等離子沉積技術制造飛機起落架的諒解備忘錄。從這樣密集的行動看來,賽峰決心將3D打印技術應用于起落架的制造進程中。而無論所謂的DED、快速等離子沉積還是激光直接沉積,實則都是金屬3D打印基于噴粉或送絲的重要形式,也表現出此類工藝在大型金屬部件直接制造方面的優勢。
Norsk等離子體沉積過程
Norsk Titanium是一家專注于鈦合金快速等離子沉積技術的挪威公司,它獲得的歐洲8級安全認證預示著其產品不存在問題,可以投入驗證,從而得到了美國國防部、美國宇航局、歐洲宇航局和許多其他航天機構的承認。目前它為波音787設計和制造的4個零部件均已獲得航空認證。賽峰集團增材制造總工程師介紹,兩家公司的合作已經取得了重要的里程碑。
Norsk生產世界第一個FAA認證的3D打印結構鈦組件
除此之外,采用SLM技術也可為起落架制造零件。近日,利勃海爾航空航天公司宣布已開始為空客3D打印用于批量生產A350 XWB的前起落架支架。
利勃海爾開發的前起落架傳感器支架
通常為了保證飛行安全,即使是由傳統制造方式制造的起落架液壓零部件也需要經過1200萬個測試周期,3D打印的起落架零件也同樣需要經歷這樣一段測試周期之后,才能夠進行飛行測試。
相對于傳統的鍛造+機加的制造技術,3D打印無疑帶來了“變革性”的變化。即便圍繞著它有一些與鍛件相比性能差異的疑慮,但數據正在說明一切。隨著相關技術的不斷完善,該技術必將越來越多地應用于飛機起落架等重要承力結構件的生產和試制。
END
免責聲明:本網站所轉載的文字、圖片與視頻資料版權歸原創作者所有,如果涉及侵權,請第一時間聯系本網刪除。
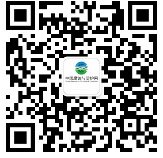
官方微信
《中國腐蝕與防護網電子期刊》征訂啟事
- 投稿聯系:編輯部
- 電話:010-62313558-806
- 郵箱:fsfhzy666@163.com
- 中國腐蝕與防護網官方QQ群:140808414