飛機起落架是飛機最重要的結構件之一,其性能與飛機的飛行安全密切相關。統計顯示,70%以上的航空事故都是由起飛和降落過程中起落架的失效引起。因此,隨著飛機安全性和舒適性要求的提高,對飛機起落架材料的綜合性能要求也越來越高。進入21世紀后,當海洋資源再度成為世界關注的焦點之時,海洋的國家戰略地位也空前提高,因而要求飛機需要長期或頻繁服役于海洋環境。因此,經常暴露于海洋環境的飛機起落架將面臨更為苛刻的服役環境。而目前已經工業化應用的飛機起落架材料多為高強度低合金鋼,如300M、AerMet100等,其強韌性可以達到設計要求,但是耐蝕性能較差,難以滿足飛機起落架在海洋環境中對耐蝕性能的要求,因此通常采用表面涂層來改善其耐蝕性能。
為了解決傳統高強鋼只能依靠表面涂層改善耐蝕性能這一現狀,新型高強度不銹鋼材料應運而生。本文首先簡述了當前使用的飛機起落架材料的發展歷程及研究現狀,然后通過對比分析不同起落架材料的性能優勢,討論了飛機起落架材料未來的發展方向及趨勢,并重點介紹了中國科學院金屬研究所在飛機起落架用高強度不銹鋼方面取得的最新進展。
1 飛機起落架用材料的應用現狀
飛機的發展初期,起落架主承力構件主要采用4130、30XГCA等1.2 GPa強度級別的高強鋼制造。隨著超高強度鋼技術的進步以及飛機設計指標的不斷提高,采用了更高強度級別(1.5~1.7 GPa)的超高強度鋼,如4340、4330M等。目前,隨著材料技術和制造技術的發展,強度級別在1.9 GPa的300M鋼以其優越的強韌性能成為軍民兩用飛機起落架的首選材料,是目前超高強度鋼中強度最高和應用最為成功的鋼種。
但是300M鋼的斷裂韌性較低。為了進一步提高飛機起落架材料的韌性以滿足航空工業發展的需要,美國Carptenter技術公司于20世紀90年代初推出新鋼種AerMet100,其斷裂韌性能夠達到115 MPa·m1/2,并已經成功用于F/A-18和F-22飛機起落架。
低合金超高強度鋼的力學性能能夠滿足飛機起落架的設計需求,但其最大的不足就是耐蝕性能很差,只能通過表面涂層改善其耐蝕性能,進而避免起落架材料因腐蝕而失效。但是,表面涂層不僅會造成環境污染問題,增加飛機運行過程中的維護費用,而且涂層脫落是飛機運行過程中的最大問題,給飛機的運行安全帶來極大的隱患。
在如今競爭激烈的商業氛圍中,更多的制造商開始關注產品的運行成本而非最初的生產成本,因此對結構材料的強度級別提出了更高的要求。同時,考慮到環境污染這一重大問題,表面噴涂等工藝有被削減的趨勢,如歐盟正在考慮取消Cd的電鍍工藝。由此可見,開發出300M、AISI4340及AerMet100等高強度低合金鋼的替代材料勢在必行。
進入21世紀后,為了解決飛機起落架因表面涂層失效造成的安全隱患和環境問題,1.9 GPa強度級別馬氏體時效不銹鋼的研究開發成為一個新的發展方向。上世紀末,美國國防部啟動了戰略環境研究與發展計劃(SERDP),其中在污染防治項目中,提出了設計一種新型的馬氏體時效不銹鋼來替代傳統的飛機起落架材料AerMet100。2006年開發出Ferrium S53馬氏體時效不銹鋼,其理論抗拉強度達到1.9 GPa。北京航空材料研究院也開發出了一種高強度不銹鋼材料S280[10],其具有比300M和AerMet100更好的耐蝕性能,在鹽霧環境中的腐蝕速率比300M低2個數量級,比AerMet100低1個數量級,同時具有優異的力學性能(強度、斷裂韌性和疲勞性能),有望替代AerMet100、300M鋼用作飛機起落架材料。幾種飛機起落架用高強度鋼的化學成分和力學性能如表1所示。
2 馬氏體時效不銹鋼的研究現狀及存在的問題
馬氏體時效不銹鋼是以無碳/超低碳Fe-Cr-Ni馬氏體組織為基體,利用馬氏體相變強化、固溶強化以及析出強化的協同作用獲得高強度的超高強度不銹鋼。與利用碳化物強化的高強度鋼不同,馬氏體時效不銹鋼的超高強度得益于時效過程中析出的高密度、納米尺度的金屬間化合物。馬氏體時效不銹鋼能夠兼顧高強度、高韌性以及優異的耐蝕性能(尤其是耐晶間腐蝕性能),已廣泛應用于航空航天、海洋開發等高科技領域。對于在腐蝕環境下服役的承力構件,馬氏體時效不銹鋼有望發揮其獨特的性能優勢。
表2所示為幾種典型的馬氏體時效不銹鋼的化學成分和相關性能。目前我國應用最廣的馬氏體時效不銹鋼是17-4 PH和15-5 PH,這類不銹鋼通過沉淀硬化獲得較高的強韌性以及優異的耐蝕性,廣泛應用于航空航天、軍工產品及重要機械部件,多用于受力較大和環境介質有一定腐蝕性的場合。但是,當強度指標要求更高時(如1.5 GPa以上),該類不銹鋼的應用受到了限制。與17-4 PH等典型的沉淀硬化不銹鋼相比,Custom 465等材料具有更高的強度級別,不但可以提高部件的服役壽命,而且延長了設備的維護周期,降低了設備的運行成本,目前已經應用于石油開采設備的軸類件、醫療器件、航空發動機以及武器裝備等領域。
通過對比現役飛機起落架材料及常用馬氏體時效不銹鋼的綜合性能發現,飛機起落架材料的發展主要面臨以下3個問題。(1) 對于目前常用的具有優異耐蝕性能的高強鋼,其強度級別普遍偏低,不能滿足飛機起落架材料的強度設計指標要求;而當強度級別達到起落架設計要求時,高強鋼的斷裂韌性或耐蝕性又偏低,如表2中的Custom 475。因此,如何實現飛機起落架材料在達到強韌性設計要求的同時,還具備優異的耐蝕性能,是起落架材料面臨的最為關鍵的問題。(2) 作為新型起落架材料的馬氏體時效不銹鋼的研究多集中在析出相的形貌觀察、析出相的演化機制和時效處理對力學性能的影響等方面,但對馬氏體時效不銹鋼耐蝕性能的研究很少。因此,對影響馬氏體時效不銹鋼耐蝕性能的主要因素尚不清楚,進而制約了該類材料的應用和發展。(3) 飛機起落架材料中的重要合金元素對力學性能的影響機制尚不清楚。對于新型高強度馬氏體時效不銹鋼,如S53、S280及Custom 475,均有一個顯著特征,即均提高了合金元素Co的含量,如表1和2所示。因此,不應忽視馬氏體時效不銹鋼中Co對其力學性能的影響研究。然而,馬氏體時效不銹鋼的合金體系比較復雜,合金元素之間的相互作用及其對微觀組織和性能的影響尚不清楚,特別是對于Co在馬氏體時效不銹鋼中的作用機制(即所謂“Co效應”)仍不是非常清楚,包括Co對強化相析出的作用機制及其對耐蝕性能的影響規律等。
3 新型馬氏體時效不銹鋼中的“Co效應”研究
自1960年第一個含Co馬氏體時效不銹鋼Pyromet X-12問世以來,人們便開始探索馬氏體時效不銹鋼中Co的作用機制,主要集中在Co對馬氏體時效不銹鋼力學性能的影響。目前一致認為,Co在馬氏體時效不銹鋼中一般處于均勻分布狀態,在時效過程中,Co會通過協同作用改變析出相的分布特征,進而提高馬氏體時效不銹鋼的強度。但已提出的關于Co的協同作用機制仍存在爭議,尚未得到一致認可。Co的強化機制一直是一個研究熱點,然而,Co對馬氏體時效不銹鋼耐蝕性能影響的研究卻鮮有報道,這可能是起初人們對馬氏體時效不銹鋼耐蝕性能的關注和重視程度不夠所造成的。
針對上述問題,中國科學院金屬研究所的研究人員以Fe-Cr-Ni-Co-Mo-Ti系馬氏體時效不銹鋼為研究對象,系統研究了該馬氏體時效不銹鋼中的“Co效應”與耐蝕性能和力學性能的關系,并從原子尺度探究了“Co效應”的基本原理,并在以上研究的基礎上開發出一種新型馬氏體時效不銹鋼,有望在新一代飛機起落架上得到應用。
3.1 Co對馬氏體時效不銹鋼耐蝕性能的影響
Tian等設計并制備了3種不同Co含量(0、5%、13%,質量分數)的馬氏體時效不銹鋼,其化學成分如表3所示。可以看出,除了Co元素以外,其它合金元素含量均處于同一數量水平上。
圖1所示為不同Co含量的馬氏體時效不銹鋼的固溶態(1050 ℃固溶處理1 h+液氮深冷處理8 h)和時效態(1050 ℃固溶處理1 h+液氮深冷處理8 h+500 ℃時效處理12 h)樣品在3.5%NaCl溶液中浸泡480 h前后的表面宏觀形貌。可以看出,0Co和5Co馬氏體時效不銹鋼在固溶態和時效態下均具有優異的耐蝕性能,經過480 h浸泡實驗后的表面依然光亮。不同的是,13Co馬氏體時效不銹鋼固溶態樣品表現出優異的耐蝕性能,浸泡實驗后表面依然光亮,但是時效態樣品經過浸泡后腐蝕嚴重,表面出現明顯的腐蝕痕跡。
浸泡實驗結果表明,雖然13Co馬氏體時效不銹鋼中的Cr含量達到13%,但是其時效態樣品的耐蝕性能很差。為了探究其耐蝕性能惡化的原因,利用三維原子探針(3DAP)分析技術表征了不同Co含量馬氏體時效不銹鋼時效不同時間后樣品中的Cr原子分布,如圖2[30]所示。可以看出,在固溶態樣品中,Cr原子均勻分布;0Co樣品時效100 h后Cr原子依然處于均勻分布狀態,5Co和13Co樣品時效100 h后Cr原子則出現了比較明顯的分布不均勻現象,即出現了Cr的調幅分解。值得注意的是,13Co樣品時效0.5 h后,Cr原子即出現了明顯的調幅分解現象,說明Co對Cr原子的調幅分解行為具有明顯的促進作用。
浸泡實驗和3DAP分析結果表明,Co促進馬氏體時效不銹鋼在時效過程中發生Cr原子調幅分解,而Cr原子的調幅分解會惡化馬氏體時效不銹鋼的耐蝕性能。為此分別對不同Co含量的馬氏體時效不銹鋼在不同時效狀態下進行了循環動電位極化曲線測試和3DAP分析。通過擬合循環動電位極化曲線,測出樣品的腐蝕電流密度,在3DAP分析基礎上,利用最大相關性方法計算調幅分解幅度的大小,如圖3[30]所示。可以看出,隨著時效時間的延長,0Co樣品調幅分解幅度變化不大,相應的腐蝕電流密度的變化也不大。但隨著時效時間的延長,5Co樣品調幅分解幅度逐漸變大,腐蝕電流密度也逐漸增大,說明隨著時效時間的延長,耐蝕性能呈現降低的趨勢。對于13Co樣品,隨著時效時間的延長,調幅分解幅度和腐蝕電流密度都呈現增加的趨勢,與5Co樣品相比,13Co樣品的增加趨勢更加顯著,時效40 h后達到最大值。
以上實驗結果表明,Co會顯著促進馬氏體時效不銹鋼中Cr原子的調幅分解進程,Cr的調幅分解幅度的變化趨勢和腐蝕電流密度的變化趨勢一致,Cr發生調幅分解是影響馬氏體時效不銹鋼耐蝕性能的主要因素。
3.2 第一原理計算分析Co促進Cr調幅分解的原因
對不同Co含量馬氏體時效不銹鋼在500 ℃時效不同時間后Co原子分布進行分析。結果表明,隨著時效時間的延長,Co原子并沒有出現明顯的偏聚行為,即時效過程中Co原子更傾向于均勻分布在Fe基體中。最近鄰分析結果表明,3DAP得到的Co原子的分布曲線與隨機分布曲線高度吻合,進一步證明時效過程中Co一直處于均勻分布狀態。值得注意的是,Cr的調幅分解通常出現在高鉻鋼或者長時間時效的低鉻鋼中,而低鉻鋼在短時時效過程中Cr的調幅分解現象尚未見報道。上述研究的馬氏體時效不銹鋼中的Cr含量(13%)遠低于發生調幅分解的臨界含量(20%),13Co樣品時效初期即出現明顯的調幅分解現象,證實了Co對Cr調幅分解的促進作用。時效過程中Co一直均勻分布在基體中,那么Co為什么能夠促進Cr原子的調幅分解?
對于Fe-Cr合金中的調幅分解行為,最初進入人們的視野來自于不銹鋼中出現的由于Cr的調幅分解造成的“475 ℃脆性”現象。由于不銹鋼中通常會加入Mo、Ni、Cu等合金元素來改善其性能,也有關于合金元素對Cr調幅分解的影響規律的研究[34,36,38~40],但是研究結果都集中在對實驗現象的描述以及調幅分解對性能的影響規律,而合金元素對調幅分解的作用機制很少被提及。
為了從原子尺度揭示Co促進Cr原子調幅分解的作用機制,利用第一原理方法計算了Co對Fe-Cr合金體系能量變化的影響。如圖4所示,共建立了4個超胞模型,模型中考慮了Cr原子的2種分布狀態:第1種,如圖4a和c所示,Cr原子彼此處于相對遠離的位置,而且整體上處于均勻分布狀態,用來模擬Cr原子沒有發生調幅分解的臨界狀態;第2種,如圖4b和d[30]所示,Cr原子彼此處于最近鄰分布狀態,整體形成Cr原子團簇,用來模擬Cr原子發生調幅分解的臨界狀態。與此同時,考慮了不含Co原子(圖4a和b)和含Co原子(圖4c和d)的情形,用來對比Co對Cr原子調幅分解過程的影響。模型中阿拉伯數字標記的原子用來表示該位置的Fe原子會被Cr原子替代,便于描述不同體系的合金成分。
Fe-Cr-(Co)合金體系中,Cr原子的團簇形成能(ΔE)是根據ΔE=EC-ED計算所得,其中EC和ED分別表示Cr原子處于團簇和均勻分布狀態下合金體系的總自由能。因此,ΔE正值表示Cr原子傾向于均勻分布狀態,相反,ΔE負值表示Cr原子傾向于形成團簇。可以看出,當體系中Cr原子個數小于等于4時,ΔE是正值;而當Cr原子個數大于4時,ΔE開始變為負值。這說明鋼中的Cr含量較低時,Cr原子傾向處于均勻分布狀態;而當Cr含量較高時,Cr原子傾向形成團簇。Klaver等的研究表明,這是由于Fe-Cr合金中Cr含量對Cr原子的團簇形成能具有重要的影響。
為了定量分析Fe-Cr-(Co)合金中Cr原子均勻分布狀態與團簇狀態之間轉換的臨界Cr含量,圖5給出了隨著Cr含量的增加,Cr原子團簇形成能的變化規律。可以看出,對于Fe-Cr合金和Fe-Cr-Co合金,隨著Cr含量的增加,ΔE都呈現線性下降的趨勢,但是2種合金體系的團簇形成能為零所對應的臨界Cr含量不同,Fe-Cr合金的臨界Cr含量為x(Cr)=8.8% (原子分數),Fe-Cr-Co合金的臨界Cr含量為x(Cr)=7.3% (原子分數)。這說明Co的添加會增加Fe-Cr合金中Cr原子形成團簇的趨勢,降低了Cr原子形成團簇的臨界含量。這與Kaneko等的研究結果一致,即在Fe-Cr合金中添加Co,會擴大其不相混溶區,也會加大調幅分解產物富Fe相和富Cr相的成分差異。
為了更好地理解磁效應和體系(Cr均勻分布和Cr團簇)穩定性之間的關系,圖5[30]描繪了隨著Cr含量的增加,在Cr原子形成團簇和均勻分布2種狀態下,Fe原子的平均磁矩差 (Δμ?Fe)(Δμ?Fe) 的變化規律。可以看出,對于Fe-Cr和Fe-Cr-Co合金體系,當Cr含量由3.7% (原子分數)增加到16.7%時, Δμ?FeΔμ?Fe 分別由-0.033μB、-0.021μB線性增加到0.043μB、0.067μB (μB為Bohr磁子)。2種合金體系中 Δμ?FeΔμ?Fe 為零所對應的臨界Cr含量不同,Fe-Cr合金的臨界Cr含量為x(Cr)=9.7% (原子分數),而Fe-Cr-Co合金的臨界Cr含量為x(Cr)=7.6% (原子分數)。可以明顯看出, Δμ?FeΔμ?Fe 是正值(負值)表示Fe原子間更強(更弱)的鐵磁相互作用,相應地,會造成合金中Cr團簇具有更高(更低)的穩定性。
計算結果表明,Fe-Cr合金中Co的加入可以導致Fe原子磁矩增加約0.02μB。需要注意的是,增加的0.02μB占bcc結構Fe中Fe原子磁矩(2.20μB)的1%。考慮到bcc結構Fe中每個Fe原子的鐵磁相互作用能是0.47 eV,根據Heisenberg經典鐵磁相互作用模型,鐵磁相互作用能與 Δμ?FeΔμ?Fe 呈線性關系。因此,Fe原子的平均磁矩變化1%,會導致每個Fe原子有4.7 meV的能量變化。
計算中所建的超胞約含50個Fe原子,則總的能量變化為235 meV。如圖5[30]所示,由于Cr含量的不同,Fe-Cr和Fe-Cr-Co體系的團簇形成能之差為100~280 meV,與235 meV這一能量變化值處于一個數量級。以上結果進一步證明,Co的加入增加了Fe原子之間的鐵磁相互作用,提高了Fe-Cr合金中Cr團簇的穩定性,進而促進了Cr團簇的形成。
3.3 Co對馬氏體時效不銹鋼力學性能的影響
為研究Co對馬氏體時效不銹鋼力學性能的影響,設計并制備了3種不同Co含量(7%、10%、13%,質量分數)的馬氏體時效不銹鋼,其化學成分如表4所示。可以看出,除了Co元素以外,其它合金元素含量均處于同一數量級上。
圖6所示為不同Co含量馬氏體時效不銹鋼的顯微組織和原始奧氏體晶粒尺寸。所有樣品的熱處理工藝為:1050 ℃固溶處理1 h+液氮深冷處理8 h+520 ℃時效處理12 h。需要說明的是,時效處理只是為了更好地腐蝕出組織形貌和原始奧氏體晶界,并不是材料的峰時效工藝。從圖6a~c可以看出,3種不同Co含量的馬氏體時效不銹鋼均是典型的板條馬氏體組織,同時還存在有少量的殘余奧氏體(白色條狀)。
如圖6d~f所示,利用截距法測量了不同Co含量馬氏體時效不銹鋼的原始奧氏體晶粒尺寸,表明3種不同Co含量馬氏體時效不銹鋼的原始奧氏體晶粒尺寸差別不大,均為50 μm左右。上述3種不同Co含量的馬氏體時效不銹鋼的顯微組織和原始奧氏體晶粒尺寸均差別不大的原因是,由于Co是很弱的奧氏體形成元素,Co含量變化3%對馬氏體時效不銹鋼的相變過程影響很小,因此不會對最終的顯微組織和原始奧氏體晶粒尺寸產生明顯的影響。
對不同Co含量的馬氏體時效不銹鋼進行固溶處理,固溶處理工藝為:1050 ℃固溶處理1 h+液氮深冷處理8 h,得到不同Co含量馬氏體時效不銹鋼在520 ℃的時效硬化曲線,如圖7所示。可以看出,3種馬氏體時效不銹鋼的時效硬化曲線變化趨勢相似。在時效初期,硬度升高很快,時效0.5 h后的硬度即達到峰值的80%以上;之后隨著時效時間的延長,硬度繼續增加,但是增加速率大幅度降低。達到峰值硬度以后,隨著時效時間的延長,硬度開始緩慢降低。可以明顯看出,Co含量的增加可以提高馬氏體時效不銹鋼的硬度,在峰時效狀態下,7Co、10Co和13Co馬氏體時效不銹鋼的硬度分別為45.3、47.1和49.1 HRC,Co含量增加3%可以將峰時效態硬度提高2 HRC左右。
固溶態和峰時效態馬氏體時效不銹鋼的屈服強度如圖8所示。可以看出,在固溶態下,隨著Co含量的增加,馬氏體時效不銹鋼的屈服強度變化不大。而在峰時效態下,隨著Co含量的增加,馬氏體時效不銹鋼的屈服強度顯著升高。峰時效態馬氏體時效不銹鋼的強度主要由3部分組成:板條馬氏體基體強度、合金元素的固溶強化貢獻的強度和析出相的析出強化貢獻的強度。在固溶態下,隨著Co含量的增加,馬氏體時效不銹鋼的屈服強度變化不大,說明Co能夠增強析出相的析出強化作用,進而提高馬氏體時效不銹鋼峰時效態的屈服強度。
3.4 馬氏體時效不銹鋼中Co強化機制的初步探討
如前所述,Co可以顯著提高峰時效態馬氏體時效不銹鋼的強度,而且強度的提高并不是由于Co的固溶強化作用,而是由于Co會增強析出強化效應。為了深入研究Co對析出強化效應的作用機制,對峰時效態下不同Co含量馬氏體時效不銹鋼中的析出相進行了表征與分析。圖9為峰時效態下不同Co含量馬氏體時效不銹鋼的TEM像和電子衍射花樣,圖10為峰時效態7Co馬氏體時效不銹鋼中元素分布圖。可見,馬氏體時效不銹鋼中主要有2種析出強化相:一種是Ni3Ti相,尺寸較小,呈棒狀;另一種是R相,尺寸較大,呈球狀。眾所周知,影響析出強化效應的主要因素是析出相的尺寸和數量密度。既然Co的加入可以增強析出強化效應,一定是Co的加入改變了析出相的分布特征。因此對不同Co含量馬氏體時效不銹鋼在峰時效態下的析出相分布進行了定量分析。
需要注意的是,TEM和3DAP在表征析出相特征方面有不同的優缺點,TEM的優勢是分析面積較大,缺點是分辨率較低。如圖9所示,很多納米尺寸的Ni3Ti析出相在TEM下難以觀察到。而3DAP的優勢是分辨率高,可以精確表征納米尺寸的細小析出相(如Ni3Ti),缺點是有效分析體體積要小。如圖10所示,整個分析體積中也只能夠部分包含R相。考慮到馬氏體時效不銹鋼中2種析出相的特征和表征手段的特點,利用TEM統計R相的尺寸分布和數量密度。為了保證統計結果的可靠性,每種材料選取10個不同的視場,然后進行整合和統計分析。利用3DAP統計Ni3Ti的尺寸分布和數量密度,為了保證統計結果的可靠性,每種材料制備了3個針尖樣品(即3個分析體),然后進行整合和統計分析。
析出相的分布特征統計結果如表5所示。對于Ni3Ti,隨著Co含量的增加,析出相的最大等效半徑逐漸減小,分別為12.68 nm (7Co)、9.52 nm (10Co)和7.55 nm (13Co),析出相的等效半徑也逐漸減小,分別為7.15 nm (7Co)、6.33 nm (10Co)和4.83 nm (13Co),體密度逐漸增大,分別為7.56×1021 m-3 (7Co)、9.81×1021 m-3 (10Co)和17.60×1021 m-3 (13Co),析出相占基體的體積百分比則變化不大(4.69%~4.81%)。對于R相,隨著Co含量的增加,析出相的最大半徑逐漸減小,分別為22.38 nm (7Co)、20.72 nm (10Co)和18.72 nm (13Co),析出相的等效半徑也逐漸減小,分別為12.52 nm (7Co)、12.14 nm (10Co)和11.09 nm (13Co),析出相的面密度逐漸增大,分別為1.02×1014 m-2 (7Co)、1.18×1014 m-2 (10Co)和1.37×1014 m-2 (13Co),析出相占基體的面積百分比則變化不大(4.98%~5.48%)。也就是說,Co可以減小馬氏體時效不銹鋼中析出相的尺寸,增加析出相的數量密度,即Co含量增加后,峰時效態下馬氏體時效不銹鋼中的析出相會更加彌散地分布,能夠有效增強析出相的析出強化效應。
根據圖11所示的馬氏體時效不銹鋼中析出相的演化機制可知,在固溶態下,Ni、Ti、Mo均處于均勻分布狀態;在時效處理過程中,Ni和Ti最先脫溶形成Ni-Ti團簇,進而形成穩定的Ni3Ti晶核,即發生Ni3Ti的形核過程。Ni3Ti形核后,在時效過程中,R相會在Ni3Ti與基體的界面形成團簇,之后發生R相的形核過程。因此可以認為,Co對Ni3Ti形核過程產生影響的根本原因應該是Co可以改變析出相分布特征。
圖12所示為利用3DAP分析的不同Co含量馬氏體時效不銹鋼在520 ℃時效1 h后的Ni3Ti的分布特征。統計結果表明,7Co、10Co和13Co馬氏體時效不銹鋼中Ni3Ti的數量密度分別為20.0×1021、22.3×1021和33.6×1021 m-3。由此可見,Co能提高馬氏體時效不銹鋼中Ni3Ti在時效初期的形核率,這也可以很好地解釋為什么峰時效態下高Co含量馬氏體時效不銹鋼中Ni3Ti的數量密度更高。馬氏體時效不銹鋼中的Ni3Ti在時效過程中的演化過程為:過飽和固溶體→團簇化→形核→析出相→析出相的長大→析出相的粗化,因此可以認為Co可能是通過影響Ni和Ti的團簇化過程而影響Ni3Ti的形核率。
圖13[44]所示為利用3DAP分析的不同Co含量馬氏體時效不銹鋼在520 ℃時效0.5 h后的Co、Ni、Ti元素分布。可以看出,Co均勻分布在馬氏體時效不銹鋼基體中,不同Co含量馬氏體時效不銹鋼中Ni-Ti團簇的分布特征差異很大。前述的實驗結果確定了以35%(Ni+Ti)等濃度面勾勒析出相的形貌,即認為析出相中(Ni+Ti)的含量超過35%后便形成穩定的Ni3Ti相。而當時效0.5 h后,3種馬氏體時效不銹鋼中尚未存在35%(Ni+Ti)等濃度面,因此認為仍處于Ni和Ti的團簇化階段,尚未形成穩定的晶核。
利用團簇分析方法,對不同Co含量馬氏體時效不銹鋼在520 ℃時效0.5 h后的Ni-Ti團簇進行了統計分析,如圖14所示。統計結果表明,7Co馬氏體時效不銹鋼中的Ni-Ti團簇尺寸分布比較集中,而10Co和13Co馬氏體時效不銹鋼中的Ni-Ti團簇尺寸分布比較分散。7Co、10Co和13Co馬氏體時效不銹鋼中最大Ni-Ti團簇包含的原子個數分別為843、1357和1722,Ni-Ti團簇的數量密度分別為131.6×103、59.35×103和25.97×103 mm-3。也就是說,隨著Co含量的增加,Ni-Ti團簇的尺寸越大,數量密度越低,即Co會促進Ni-Ti團簇的聚合。
如圖15所示,在520 ℃時效0.5 h后的13Co馬氏體時效不銹鋼試樣中選取了一個Ni-Ti團簇,并對Ni-Ti團簇及其周圍的一維濃度分布進行了分析。可以看出,Ni-Ti團簇中心的Ni原子和Ti原子含量(原子分數)分別達到了61.5%和23.7%,而Fe原子和Co原子的含量分別為6.8%和2.5%,遠低于其在基體中的含量(基體中Fe原子為65%,Co原子為13%)。因此在團簇化過程中,Ni-Ti團簇中的Co原子和Fe原子會被排斥到基體中。
根據經典的形核理論,在析出相形核過程中,存在一個臨近晶核尺寸,只有超過臨近晶核尺寸的晶核才能穩定存在,并形成成分穩定的析出相。上述研究結果表明,Co能夠改變馬氏體時效不銹鋼在時效初期形成Ni-Ti團簇的分布特征;隨著Co含量的升高,Ni-Ti團簇的尺寸增大。由于Ni-Ti團簇的尺寸只有達到了臨界晶核尺寸后才會形成穩定的Ni3Ti晶核,因此Co是通過促進時效初期Ni-Ti團簇化過程來提高Ni3Ti的形核率。
3.5 第一原理計算分析Co促進Ni-Ti團簇形成的原因
為了從原子尺度揭示Co促進Ni-Ti團簇形成的作用機制,利用第一原理計算方法分析了Co對Fe-Ni-Ti合金體系能量變化的影響。圖16所示為建立的2個晶胞模型,分別表示了不含Co和含Co的2個合金模型,所有合金原子均處于均勻分布狀態。為了表征Co對Ni-Ti團簇形成的影響,建立了不同的Ni-Ti團簇構型,如圖17所示,利用如下公式計算Ni-Ti團簇形成能ΔE:
式中,E(NiNTi1)表示形成Ni-Ti團簇情況下整個體系的能量,N表示Ni-Ti團簇構型中Ti原子周圍處于第一近鄰位置的Ni原子的個數;E(Alloy)表示不形成Ni-Ti團簇情況下整個體系的能量。為了保證計算結果的可靠性,對Ni2Ti1團簇分別計算了2個構型的能量,對Ni4Ti1團簇分別計算了4個構型的能量。
圖18所示為含Co和不含Co 2種合金體系下Ni-Ti團簇形成能的計算結果。可以看出,對于2種合金體系而言,隨著N的增加,ΔE均逐漸降低,說明在bcc結構的Fe基體中形成Ni-Ti團簇是熱力學驅動的過程,Ni-Ti團簇的形成可以提高整個體系的穩定性。同時還發現,與不含Co的合金體系相比,含Co合金體系的團簇形成能更低,說明Co的加入提高了Ni-Ti團簇形成的熱力學驅動力。
為了進一步理解Co提高Ni-Ti團簇形成的熱力學驅動力的原因,利用下式計算了不同結構的二元合金的形成能Eform.:
式中,E(AmBn)表示二元合金AmBn的能量值(包含m個A原子和n個B原子),μ(A)表示A原子的化學勢,μ(B)表示B原子的化學勢。
對于二元合金而言,其結構穩定性主要取決于合金成分和溫度。在Fe-Co-Ni-Ti體系中有6種二元合金(Fe-Co、Fe-Ni、Fe-Ti、Co-Ni、Co-Ti、Ni-Ti)。對于這6種二元合金,研究表明,其最穩定的結構相分別為bcc結構的FeCo相、fcc結構的FeNi3相、fcc結構的Co3Ni相、hcp結構的Ni3Ti相、bcc結構的FeTi相[50]和bcc結構的CoTi相。
圖19所示為不同二元合金的形成能。可以看出,在6種二元合金中,hcp結構的Ni3Ti相的形成能(-0.538 eV/atom)最低,這也是在馬氏體時效不銹鋼的時效初期便形成了Ni-Ti團簇的原因。如表4所示,實驗用馬氏體時效不銹鋼中的Ni和Ti含量的比值約為Ni∶Ti=11∶1,遠遠高于3∶1。據此可以推斷,在時效過程中,所有的Ti原子會與Ni原子形成Ni-Ti團簇,不會有剩余的Ti原子與其它原子(如Co和Fe)結合形成其它類型的團簇。因此,即使bcc結構CoTi相的形成能(-0.457 eV/atom)和bcc結構FeTi相的形成能(-0.475 eV/atom)同樣很低,時效過程中也不會形成Co-Ti團簇和Fe-Ti團簇,這也是Co原子和Fe原子會被Ni-Ti團簇排斥到基體中的原因(如圖15所示)。
在時效過程中,Co一直處于均勻分布狀態。因此可以推斷,馬氏體時效不銹鋼中的Co原子會占據Fe原子的位置。從圖19可以看出,bcc結構FeTi相的形成能(-0.475 eV/atom)遠低于FeNi相的形成能(0.155 eV/atom),說明Fe-Ti的相互作用遠強于Fe-Ni。因此,從熱力學角度考慮,在時效過程中,Ti原子的聚集難于Ni原子。因此可以推斷,Ti原子的聚集是Ni-Ti團簇化的反應控制過程。同時還可以看出,bcc結構CoTi相的形成能(-0.457 eV/atom)略高于bcc結構FeTi相的形成能(-0.475 eV/atom),bcc結構CoNi相的形成能(0.185 eV/atom)略高于bcc結構FeNi相的形成能(0.155 eV/atom),說明Co-Ti (Co-Ni)的相互作用均弱于Fe-Ti (Fe-Ni)。因此,Co原子的加入可以降低Fe基體中Ni原子和Ti原子聚集所需的能量,即Co提高了Ni-Ti團簇形成的熱力學驅動力。
3.6 飛機起落架用新型馬氏體時效不銹鋼的開發
根據上述研究結果,Co在馬氏體時效不銹鋼中的作用具有兩面性。一方面,Co會促進Cr的調幅分解,因而惡化馬氏體時效不銹鋼的耐蝕性能。Ferrium S53和S280 2種材料中均含有較高的含量Co (14%,質量分數),因此,即使這2種材料中的Cr含量較高,其在鹽霧環境下依然會出現點蝕的現象。另一方面,Co會改變馬氏體時效不銹鋼中析出相的分布特征,增強析出相的析出強化效應,進而提高馬氏體時效不銹鋼的強度。在上述研究結果的指導下,并在前期自主開發的一種高Co含量Fe-Cr-Ni-Co-Mo-Ti馬氏體時效不銹鋼(原型鋼)的基礎上,中國科學院金屬研究所設計了一種新型高強高韌高耐蝕馬氏體時效不銹鋼(新型鋼),其化學成分設計如表6所示。
采用雙真空冶煉技術(真空熔煉+真空自耗)對經過合金成分優化后的新型鋼進行熔煉。對新型鋼進行均勻化處理(1200 ℃保溫24 h)后,鍛造成方坯,其峰時效態熱處理工藝為:1050 ℃固溶處理1 h+深冷處理8 h+480 ℃時效處理20 h。利用TEM觀察了新型鋼在2種不同熱處理狀態下的顯微組織,從圖20a和b可以看出,在固溶態下,新型鋼為典型的板條馬氏體組織,基體中有較高密度的位錯,高密度的位錯能夠為時效過程中強化相的析出提供有利的形核位置,促進析出相的彌散分布,進而增強析出強化效應。圖20c為峰時效態下新型鋼中的析出相形貌。可以看出,新型鋼中有2種不同類型的析出相:一種是尺寸比較大的球狀析出相,結合圖20d1和d2所示的高分辨電鏡像和圖21所示的3DAP分析結果,確定該相為R相;另一種則是尺寸比較小的棒狀析出相,結合20d3和d4[43]所示的高分辨電鏡像和圖21所示的3DAP分析結果,確定其為Ni3Ti相。
從圖21所示的3DAP結果中還可以看出,新型鋼中每種析出相均有2種不同的形貌,Ni3Ti相有尺寸較大的棒狀形貌(圖21c)和尺寸較小的球狀形貌(圖21e)。馬氏體時效不銹鋼的基體為bcc結構,而Ni3Ti相為hcp結構,在Ni3Ti的長大過程中會存在特定的擇優取向,以保證析出相與基體之間最低的界面能,這也是Ni3Ti相長大以后均為棒狀的原因所在。尺寸較小的球狀Ni3Ti相則是形核初期的Ni3Ti相,由于尚未長大而呈現出球狀形貌。R相有尺寸較大的球狀形貌(圖21b)和尺寸較小的片狀形貌(圖21d)。
為了對比分析新型鋼的耐蝕性能,選取了17-4 PH、15-5 PH、PH 13-8Mo和原型鋼為對比材料,對這5種馬氏體時效不銹鋼分別進行了峰時效熱處理,熱處理工藝分別為:1040 ℃固溶處理1 h+油冷+480 ℃時效處理4 h (17-4 PH);1040 ℃固溶處理1 h+油冷+480 ℃時效處理4 h (15-5 PH);925 ℃固溶處理1 h+油冷+535 ℃時效處理4 h (PH 13-8Mo);1050 ℃固溶處理1 h+深冷處理8 h+500 ℃時效處理12 h (原型鋼);1050 ℃ 固溶處理1 h+深冷處理8 h+480 ℃時效處理20 h (新型鋼)。
對這5種馬氏體時效不銹鋼的峰時效態試樣在3.5%NaCl溶液中進行了浸泡實驗。由圖22a可以看出,浸泡實驗前所有樣品的表面均十分光亮。浸泡144 h后,如圖22b所示,只有原型鋼表面出現了嚴重的腐蝕,說明原型鋼的耐蝕性能最差。其它4種馬氏體時效不銹鋼中,只有15-5 PH邊緣出現了輕微的腐蝕現象,而17-4 PH、PH 13-8Mo和新型鋼表面均沒有出現腐蝕現象,說明這3種馬氏體時效不銹鋼均具有優異的耐蝕性能。
選取原型鋼、新型鋼和15-5 PH為研究對象,利用光電子能譜(XPS)對這3種馬氏體時效不銹鋼經過浸泡實驗后的表面鈍化膜成分進行了分析。需要注意的是,原型鋼的耐蝕性能較差,表面已經出現嚴重的腐蝕現象。因此原型鋼表面應該是腐蝕產物,而不是鈍化膜,但為了敘述方便,在文中統稱為鈍化膜。圖23[53]所示為3種馬氏體時效不銹鋼表面鈍化膜成分隨濺射時間的變化曲線。可以看出,原型鋼表面的鈍化膜成分主要是Co的氧化物,厚度約為1.2 µm,而新型鋼和15-5 PH表面的鈍化膜成分主要是Cr的氧化物,厚度約為100 nm。眾所周知,不銹鋼之所以具有優異的耐蝕性能,是由于其表面能夠形成富Cr的鈍化膜,保護基體材料不受腐蝕介質的進一步侵蝕。XPS分析結果表明,新型鋼和15-5 PH表面上均可以形成富Cr的鈍化膜,這是新型鋼和15-5 PH具有優異耐蝕性能的根本原因,而原型鋼表面上無法形成完整的富Cr鈍化膜,導致原型鋼的耐蝕性能較差。
圖24所示為峰時效狀態下新型鋼和商用馬氏體時效不銹鋼的抗拉強度、斷裂韌性和耐蝕性能關系圖,商用馬氏體時效不銹鋼的力學性能來自文獻。與目前商用馬氏體時效不銹鋼相比,新型鋼的抗拉強度(1.9 GPa)明顯高于多數商用馬氏體時效不銹鋼,略低于Custom 475和Ferrium S53的抗拉強度。除了抗拉強度外,耐蝕性能和斷裂韌性是馬氏體時效不銹鋼的另2個關鍵性能。17-4 PH的腐蝕電流密度最小,耐蝕性能最優,這得益于17-4 PH中更高的Cr含量(17%)。新型鋼的腐蝕電流密度與15-5 PH接近,說明新型鋼的耐蝕性能與15-5 PH相當,且明顯優于Custom 465、Custom 475、Ferrium S53這3種強度級別較高的商用馬氏體時效不銹鋼。新型鋼的斷裂韌性(78 MPa·m1/2)明顯高于同強度級別的Custom 475,與Ferrium S53相當。
綜上所述,新型馬氏體時效不銹鋼的抗拉強度(1.9 GPa)、斷裂韌性(78 MPa·m1/2)和耐蝕性能(與15-5 PH相當)達到了新一代飛機起落架材料的綜合性能要求,有望替代傳統的低合金高強度鋼而得到應用。與目前常用的馬氏體時效不銹鋼相比,新型鋼的綜合性能表現出明顯的優勢,有望用于在腐蝕環境下服役的承力構件,具有廣闊的應用前景。
4 總結與展望
同時提高超高強度鋼的強韌性、損傷容限性能和耐久性對起落架設計的吸引力是毋庸置疑的。但是當海洋資源再度成為世界關注的焦點,海洋的國家戰略地位變得更為重要時,飛機特別是艦載機將在整個壽命期內服役于海洋環境下,即長期暴露于高溫、高濕、高鹽的嚴酷腐蝕環境中。因此,飛機起落架要求采用耐腐蝕性能更優的超高強度鋼來設計和制造。
目前飛機起落架多采用300M或AerMet100鋼制造,其缺點是耐蝕性能較差,必須通過表面涂層來提高其耐蝕性能。應用廣泛的具有優異耐蝕性能的高強度鋼是17-4 PH和15-5 PH等沉淀硬化不銹鋼,這類不銹鋼多用于受力較大和環境介質有一定腐蝕性的場合。但當強度要求更高時(如1.5 GPa以上),該類不銹鋼的應用也會受到限制。
為了解決涂層帶來的安全隱患和環境問題,并兼顧材料的高強度和高韌性,中國科學院金屬研究所的研究人員基于新的超高強度鋼強韌化理論和成分設計理念,研究了Fe-Cr-Ni-Co-Mo-Ti系馬氏體時效不銹鋼中的“Co效應”,發現一方面Co會惡化馬氏體時效不銹鋼的耐蝕性能,另一方面Co會提高馬氏體時效不銹鋼的強度。結合三維原子探針技術和第一原理計算,從原子尺度上揭示了“Co效應”的基本原理。在此研究基礎上,成功地開發了一種新型Fe-Cr-Ni-Co-Mo-Ti馬氏體時效不銹鋼,其表現出優異的綜合性能:抗拉強度為1.9 GPa,斷裂韌性達到78 MPa·m1/2,耐蝕性能與15-5 PH相當。盡管該新型鋼的應力腐蝕斷裂韌性還沒有報道,但是綜合考慮其綜合性能,已經達到了飛機起落架材料的基本要求,未來有望替代當前使用的低合金高強度鋼而成為下一代飛機或艦載機起落架的備選材料。
免責聲明:本網站所轉載的文字、圖片與視頻資料版權歸原創作者所有,如果涉及侵權,請第一時間聯系本網刪除。
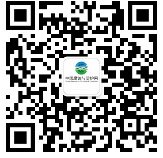
官方微信
《中國腐蝕與防護網電子期刊》征訂啟事
- 投稿聯系:編輯部
- 電話:010-62313558-806
- 郵箱:fsfhzy666@163.com
- 中國腐蝕與防護網官方QQ群:140808414