鎂鋰合金( magnesium-lithium alloy) 是在鎂基體中添加鋰元素,其比重介于1. 4 ~ 1. 6 之間,密度較一般鎂合金更低,在需要輕量化結構材料的交通、電子、醫療產品等領域展現出廣闊的應用前景。但由于鎂鋰合金的腐蝕電位較低、耐蝕性極差,使用前必須進行適當的表面改性處理。
與普通陽極氧化、化學轉化及電鍍等技術形成的陶瓷層性能相比,微弧氧化陶瓷層是在弧光放電條件下,由閥金屬表面原位生長而來,有著更高的耐磨性和耐蝕性。為了進一步提高微弧氧化陶瓷層的性能,有學者將高硬度碳化硅顆粒、納米氧化鋁等中性物質通過超聲作用,均勻分散在電解液中,制備出包覆相應添加劑的微弧氧化陶瓷層。由于高硬度顆粒包覆于陶瓷層之中,極大地提高了微弧氧化陶瓷層的耐磨性。實驗基于提高微弧氧化陶瓷層減摩性的目的,通過在電解液中加入石墨烯添加劑,以期制備出含碳的微弧氧化陶瓷層,進而改善其陶瓷層性能。
實驗結果表明,在超聲和攪拌的作用下,石墨烯添加劑均勻的分散到電解液之中,使得試樣表面起弧電壓降低30 V 左右、表面放電通道孔徑明顯減小、并且在17 μm 厚的微弧氧化陶瓷層中檢測到碳元素的梯度分布。隨后大量的研究工作表明,通過在電解液中加入石墨烯添加劑,制備出含碳的微弧氧化陶瓷層由于放電通道孔徑的減小,對其耐蝕性的提高有著明顯改善的作用。
本文主要研究了在石墨烯添加劑加入電解液前后,制備的微弧氧化陶瓷層在3. 5% NaCl 溶液中耐蝕性能的變化,以及含碳陶瓷層在兩種腐蝕條件下( “浸泡在不同濃度NaCl 溶液中3 h”和“在3. 5%NaCl 溶液浸泡不同時間”) 耐蝕性能,并分析了含碳陶瓷層對提高其耐腐蝕性能的機理。
1 試驗材料及方法
1. 1 材料與試劑
試驗材料為鎂鋰合金,試樣尺寸為20 mm ×30 mm × 3 mm,其成分為( 質量分數,%) : 5% Li、3. 5%Al、1% Zn、1. 2% Ce、1. 5% Mn、余量為Mg。石墨烯添加劑( 石墨烯分散液) 由北京碳世紀科技有限公司提供,其干粉顆粒度為325 目。微弧氧化前試樣需要經過砂紙打磨,去除機械加工時表面形成的氧化皮,并在拋光機上進行拋光,隨后在超聲清洗機中超聲10 min,最后使用熱風迅速吹干。將試樣與鎂絲的一端相連,連接處用高分子液體密封膠覆蓋,鎂絲的另一端固定在微弧氧化設備( 如圖1 所示) 正極支架上,試樣作為陽極,不銹鋼電解槽作為陰極。
實驗所用的電解液為硅酸鹽體系,其各組分含量分別為: 硅酸鈉( 10 g /L) ,氫氧化鉀( 5 g /L) 、十二烷基苯磺酸鈉( 3 g /L) 、石墨烯添加劑( 5 mL /L) 。采用WHD-60D 型單極性微弧氧化脈沖電源。輸出參數為: 電流2 A、占空比50%、頻率500 Hz、處理時間30 min。電解液溫度保持25 ℃、電解液pH 值為12。石墨烯添加劑的含量分別為0 mL /L 和5 mL /L。
1. 2 試驗檢測
采用SSX-550 型掃描電子顯微鏡觀察了陶瓷層截面形貌; 采用X 射線能譜儀對微區元素進行點掃描; 采用EPMA-1600 型電子探針對陶瓷層截面進行線掃描分析; 采用D8 FOCUS—X 射線衍射儀對陶瓷層物相組織進行檢測分析; 采用電化學工作站對陶瓷層的耐蝕性進行了檢測并討論。電化學實驗采用三電極體系,試樣為工作電極,飽和甘汞電極作為參比電極,鉑電極作為輔助電極。試樣表面裸露出面積為1 cm2,分別檢測在兩種腐蝕條件下,陶瓷層的耐蝕性能。采用CS360 型電化學工作站檢測試樣的動電位極化曲線,掃描電位( 相對開路電位) - 0. 1 ~ 0. 1 V,掃描速率為0. 5 mV/s。
2 結果與討論
2. 1 表面形貌及物相分析
圖2 為鎂鋰合金經微弧氧化處理后陶瓷層表面SEM 形貌照片。由圖2( a) 可以看出未加入石墨烯添加劑制備的試樣表面形貌如同火山噴發并堆積而成,陶瓷層表面微孔尺寸在1. 5 ~ 2. 5 μm 之間,孔徑尺寸變化大,分布不均勻且在放電微孔處有裂紋產生。而由圖2( b) 可以看出加入石墨烯添加劑( 5 mL /L)后制備的試樣表面微孔大小趨于均勻,尺寸在0. 5 μm 左右,孔徑尺寸變小且沒發現有裂紋產生。在恒流工作模式下,由于石墨烯添加劑的加入,使得起弧電壓降低30 V 左右,這樣單脈沖擊穿陶瓷層的能量降低,表現為試樣表面放電通道分布均勻,孔徑尺寸減小。
XRD 衍射圖譜如圖3 所示。由圖可知,鎂鋰合金基體主要有Li、Li3Mg7、Li3Mg17、LiAlSi4O10物相組成。未加入石墨烯添加劑制備的試樣表面Li3Mg7和Li3Mg17物相相對峰值較基體有所降低,且多出MgO、Mg2 SiO4以及SiO2 3 種物相。微弧放電過程中產生的熱能,可使微區的固態鎂瞬間發生熔融,Mg 原子通過放電通道向基體/陶瓷層界面處遷移,與吸附在界面處的O 原子結合形成MgO。而在高溫和堿性環境條件下,使得生成的SiO2和MgO 熔融并發生反應,最后在溶液的冷淬作用下,熔融氧化物轉變為MgO和Mg2 SiO4的混合物。與其相比,加入石墨烯添加劑后制備的試樣MgO 物相的相對峰值較高,并且又出現了新的Mg2 SiO4衍射峰,表明陶瓷層中MgO 和Mg2 SiO4物相含量在逐漸增多。說明石墨烯添加劑的加入在降低起弧電壓的同時,也促進了陶瓷層中MgO 和Mg2 SiO4物相含量的升高。
2. 2 截面形貌及線掃描分析
圖4( a) 和4( b) 分別為電解液中石墨烯添加劑含量為0 和5 mL /L 時,所制備的試樣經金相腐蝕后的截面SEM 照片。可以看出,鎂鋰合金基體的顯微組織由淺色長條狀的富鎂α 相固溶體和深色β 相固溶體組成。陶瓷層主要有疏松層( 1) 和致密層( 2)組成。兩者的疏松層厚度均約為8 μm,但圖4( b) 試樣疏松層中因微弧放電而產生的微孔尺寸明顯小于圖4( a) 試樣,這是由于石墨烯添加劑的加入,使得終止電壓降低,減小了單脈沖放電的能量,故而產生的微孔尺寸較小,這也與陶瓷層表面微孔尺寸的變化趨勢相同。而圖4( a) 試樣疏松層內部存在尺寸較大的微裂紋和顆粒,這是因為在疏松層形成過程中,由于表面微弧放電產生瞬間高溫燒結作用以及電解液的急速“冷淬”作用,使得陶瓷層外層產生較大過冷度,內應力來不及釋放,便造成疏松層內部生成大量微裂紋。此外,圖4( b) 試樣的致密層厚度約為10 μm,明顯厚于圖4( a) 試樣的厚度5 μm,并且,其致密層中并無發現明顯的微裂紋產生,這首先是由于電解液的“冷淬”作用對致密層的影響相對較小,其次是石墨烯添加劑的加入,降低了單脈沖微弧放電的能量,促進并保持了致密層的生長。
圖4( c) 為試樣陶瓷層截面線掃描( AB 線) 元素含量分析,其中0 ~ 8 μm 段,C 元素來自鑲嵌粉( 成分主要為有機物) ,故其含量較高。在8 ~ 25 μm 段( 陶瓷層) ,Si 和O 元素均有先上升后降低的趨勢,其主要來自參與氧化反應的電解液; Mg 元素含量逐漸升高,最終趨于基體Mg 元素的含量值; C 元素含量逐漸降低并趨近于零。微弧氧化反應一旦開始,將在放電通道內部產生瞬間高溫高壓,將基體熔融并噴射出的熔融物,在電解液“冷淬”作用下迅速凝固,并將部分石墨烯包覆在陶瓷層中,使得放電通道附近局部區域的陶瓷層厚度增加。此外,石墨烯在超聲分散的作用下彌散分布于電解質溶液中,由于其表面能較大,能夠吸附電解液中電子,而使本身帶上負電。在強電場作用下,其能夠隨電解液沿放電通道進入陶瓷層內部并參與到陶瓷層生成的反應之中。
2. 3 耐蝕性研究
圖5 為不同試樣在質量分數3. 5% 的氯化鈉溶液中浸泡3 h 測得的極化曲線,其計算結果如表1 所示。未加入石墨烯添加劑制備的試樣自腐蝕電位相比原始試樣提高0. 13 V,其腐蝕電流密度減小6 倍左右。加入石墨烯添加劑制備的試樣自腐蝕電位相比原始試樣提高0. 26 V,其腐蝕電流密度減小10 倍左右。其結果表明,通過在電解液中加入石墨烯添添加劑,在降低起弧電壓的同時,能夠降低單脈沖擊穿陶瓷層的能量,減小放電通道尺寸,使得腐蝕液離子滲入陶瓷層的阻力變大,進而明顯提高的陶瓷層耐蝕性。其次,放電結束之前,在熔融物從孔道噴出之后,彌散分布于電解液中的石墨烯隨電解液進入放電通道,并迅速凝固,對腐蝕液離子的滲入也起到一定的阻礙作用。
圖6 為加入石墨烯添加劑后制備的試樣在不同質量分數( 3. 5%、5%、7. 5%、10%) 的氯化鈉溶液中浸泡3 h 時間下測得的動電位極化曲線,其計算結果如表2 所示。由圖可知,隨著氯化鈉溶液濃度的升高,試樣自腐蝕電位由- 1. 61 V 降低到- 1. 63 V。
其腐蝕電流密度逐漸升高,當NaCl 溶液濃度10%時,腐蝕電流密度達到最大值8. 70 × 10 - 03 mA/cm2,其值增大了將近40 倍,明顯加快了試樣的腐蝕損壞。表明隨著Cl - 離子濃度的升高,Cl - 在陶瓷層中的滲透擴散速度加快,降低了陶瓷層的自腐蝕電位,加速了腐蝕介質對基體的腐蝕破壞。分數3. 5% 的氯化鈉溶液中,不同浸泡時間下測得的動電位極化曲線。其計算結果如表3 所示。由圖可知,隨著浸泡時間的延長,試樣的自腐蝕電位逐漸降低,由- 1. 56 V 降低到- 1. 63 V,自腐蝕電位降低了約0. 07 V。其腐蝕電流密度逐漸升高,由浸泡3 h 時的2. 28 × 10 - 04 mA/cm2,升高到浸泡96 h 時的2. 92 × 10 - 03 mA/cm2,提高了10 倍左右,明顯會加快腐蝕介質對基體腐蝕。年腐蝕速度也增大了近15 倍左右。
圖8 為加入石墨烯添加劑后制備的試樣在質量分數3. 5%的氯化鈉溶液中,浸泡不同時間后的表面形貌圖。表4 為能譜儀測得圖8( a) 、8( b) 、8( c) 中A、B、C 三處點元素含量。由圖8( a) 可以看出,在腐蝕初期,試樣表面看不到任何腐蝕附著物,但有幾條腐蝕裂紋產生。由8( a) 內嵌放大圖可以看出,腐蝕裂紋是由在放電微孔處開始萌生,并逐漸向四周擴展延伸。其中A 處元素含量以Mg、Si、O 為主,沒檢測到Cl 元素,說明腐蝕初期,主要產生腐蝕裂紋,并沒有產生腐蝕產物。隨著腐蝕時間延長至12 h,裂紋的數量和尺寸逐漸增大,使得疏松層開始發生脫落。由8( b) 內嵌放大圖看出,疏松層表面附著大量腐蝕產物。測得B 處含有大量Cl 元素,說明其為腐蝕產物。
疏松層和腐蝕產物的脫落,導致腐蝕液中的Cl - 離子滲入致密層的速度加快,使得腐蝕裂紋深度增加,逐漸延伸到致密層中。當腐蝕時間達到96 h 時,試樣表面塊狀腐蝕產物已經發生脫落。測得C 處Cl 元素含量為2. 00%,表明Cl - 已經滲入到基體表面,開始腐蝕基體。如圖8( c) 所示,疏松層已完全脫落,內部致密層也受到嚴重腐蝕。通過在電解液中加入石墨烯添加劑,在一定程度上改變了電解液的電導率、粘度等參數,這就降低了試樣表面起弧電壓,減少了單脈沖放電能量,并且微弧放電微區分布趨于均勻,使得生成的膜層致密層微孔尺寸較小,且無明顯微裂紋產生,對腐蝕液離子的滲入阻礙較大。此外,由于微弧放電瞬間高溫作用,微孔周圍電解液迅速蒸發,在對流傳質和擴散遷移的作用下,石墨烯添加劑一部分參與到膜層的生成反應之中,雖未改變膜層表面結晶相的類型,但改變了膜層表面個元素的相對含量; 另一部分伴隨電解液進入放電通道,隨著溫度的迅速降低,石墨烯添加劑便已顆粒物的形式存在于放電通道之中,對腐蝕介質離子的滲入起到明顯的阻礙作用,進而改善了微弧氧化膜層的耐蝕性能。
3 結論
1) 通過在微弧氧化電解液中加入石墨烯添加劑,降低了起弧電壓,并制備出含碳微弧氧化陶瓷層。其陶瓷層表面放電微孔尺寸僅為0. 5 μm 左右,相比不加入石墨烯添加劑制備的試樣的孔徑尺寸明顯降低;
2) 陶瓷層表面主要由Li3Mg7、Li3Mg17、Mg2 SiO4以及MgO 等物相組成,由于石墨烯添加劑的加入,促進了Mg2 SiO4以及MgO 等物相的形成,提高了其在陶瓷層中的含量;
3) 極化曲線計算結果表明,含碳陶瓷層明顯提高了其自腐蝕電位,降低了電流密度和腐蝕速度。而且,陶瓷層在高濃度的Cl - 離子溶液中腐蝕較快,隨著浸泡時間延長,Cl - 離子不斷深入到陶瓷層內部,造成了基體的腐蝕。
更多關于材料方面、材料腐蝕控制、材料科普等方面的國內外最新動態,我們網站會不斷更新。希望大家一直關注中國腐蝕與防護網http://www.ecorr.org
責任編輯:王元
《中國腐蝕與防護網電子期刊》征訂啟事
投稿聯系:編輯部
電話:010-62313558-806
郵箱:fsfhzy666@163.com
中國腐蝕與防護網官方 QQ群:140808414
免責聲明:本網站所轉載的文字、圖片與視頻資料版權歸原創作者所有,如果涉及侵權,請第一時間聯系本網刪除。
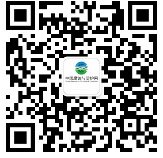
官方微信
《中國腐蝕與防護網電子期刊》征訂啟事
- 投稿聯系:編輯部
- 電話:010-62313558-806
- 郵箱:fsfhzy666@163.com
- 中國腐蝕與防護網官方QQ群:140808414