鎂合金具有比強度高、比剛度大、切削加工性好、生物相容性能優良和高度可回收等優點,在現代工業生產制造領域被稱為“21 世紀綠色工程材料”。為迎合制造業對環境保護的高度要求,諸多工業產品需進行自身輕量化,以減少能耗和有害物質排放,這使得鎂合金成為了工業制造業中的熱點。
然而,鎂的化學活性高,性質活潑,尤其在潮濕空氣、含硫氣氛和海洋大氣環境中,鎂及其合金表面極易被氧化形成疏松多孔的氧化膜,從而導致該表面的耐蝕性及耐磨性迅速降低變差,這在很大程度上阻礙了鎂合金在工農業領域中的廣泛應用。 因此, 如何實現鎂合金表面的改性處理研究來提高其耐蝕性受到科研人員的關注。
超疏水表面是近些年來逐漸興起并引起廣大學者關注的一種特殊潤濕狀態的表面, 它是指基底材料對水具有大于 150°的靜態接觸角,同時具有小于 10°滾動角的表面。自然生物界經億萬年的發展與進化,構造出許多此類表面,如廣泛存在的荷葉、水黽的腿、蜻蜓翅膀等,它們均具有超疏水性能。現有的研究報道表明,超疏水表面具有自清潔防污染特性,因其具有較低的表面自由能,能夠有效地改善基底材料的潤濕性, 調控材料的黏附力,使其在流體減阻、表面防護、防覆冰雪和功能材料等領域有廣泛的應用前景。因此,對鎂合金基底進行超疏水改性研究在加深鎂合金材料特性的認識, 擴展鎂合金材料作為功能材料的應用范圍, 提高鎂合金的材料使用性能等方面均有重要的指導和借鑒意義。
本文著重總結歸納目前鎂合金基底超疏水表面制備技術的研究進展, 并對鎂合金超疏水表面的發展進行了展望。
1鎂合金超疏水表面制備工藝
隨著人們對超疏水表面的研究發現, 超疏水表面具有自清潔特性源于其表面微細粗糙結構和低表面能物質的共同作用。 受此啟發, 對鎂合金基底超疏水表面的制備主要從構建特殊微細結構和低表面能物質修飾兩種途徑出發。 目前, 主要有微弧氧化、刻蝕、電沉積、水熱法和化學成膜等工藝,其中微弧氧化、刻蝕和電沉積技術借助特制的溶液或某些微粒來構建特定的表面微結構, 水熱法和化學成膜技術以制備具有低表面物質為主要目的, 或兩種工藝相結合來實現鎂合金超疏水表面的制備。
1.1 微弧氧化法
微弧氧化工藝是指借助電解液和相應的電參數,在輕金屬(如鎂鋁鈦等)及其合金試樣上利用微弧放電生成的高溫高熱來作用于金屬表面, 從而在該試樣表面生成一層陶瓷膜層 (也被稱為微弧氧化層) 。該膜層可有效改善鎂合金表面的耐磨、耐蝕和摩擦學等性能,已成為鎂合金改性研究的重要手段。
Hou 等采用微弧氧化工藝在 Mg-Li 合金基體表面制備出的膜層為超親水膜層, 之后再用包含低表面自由能含氟官能團的三嗪硫醇有機化合物鈉鹽單體 (ATP) 進行鍍膜, 制得了接觸角達 161°、滾動角為 3°的超疏水表面。研究表明,該表面具有良好的耐蝕性。李杰等對 MB8 鎂合金進行了微弧氧化處理并獲得超親水性的微米級粗糙結構,再利用環氧樹脂偶聯納米二氧化硅顆粒實現對微弧氧化層表面進行涂覆處理, 形成了具有微納二元結構的粗糙表面,最后利用 1H,1H,2H,2H-全氟葵烷基三氯硅烷改性修飾, 得到了具有超疏水性的復合膜層。該表面的靜態接觸角最大值為 161°,且該表面對不同 pH 值的水溶液均呈現出超疏水特性。 康志新等采用微弧氧化技術和有機鍍膜技術相結合的處理方法實現了對 Mg-Mn-Ce 鎂合金表面改性,獲得了超疏水復合膜層,接觸角達 173°,研究表明該表面的耐蝕性得到了明顯提高。Wang等 以微弧氧化為預處理構建微米級粗糙結構, 之后利用溶膠-凝膠和浸漬-提拉相結合的工藝得到經甲基疏水基團修飾的 SiO 2 膜層,構建出具有微納分級結構的表面,實現了 NZ30K 鎂合金表面的超疏水改性。在溶膠-凝膠工藝過程中,當 TEOS/乙醇摩爾比為 1/30 時,通過提高 MTES 添加量(MTES/TEOS 摩爾比) 可使 SiO 2 薄膜表面的靜態接觸角增大,當 MTES/TEOS 摩爾比為 1 時,其靜態接觸角可達 153°。 Liang 等在鎂合金表面利用微弧氧化技術構造微米級粗糙結構, 再利用化學修飾工藝構造出類似荷葉的微納分級表面結構, 該表面上液滴呈球形且易于滑動。
1.2 刻蝕法
刻蝕法是指利用溶液、 反應離子或其他手段來實現材料分離、去除的工藝統稱,其廣泛應用于微加工制造領域。 該工藝在超疏水表面制備領域已成功應用。目前主要有激光加工刻蝕、化學刻蝕、光刻、等離子刻蝕和其他機械刻蝕等。
張會臣課題組利用激光預處理在鎂合金表面構建微米級粗糙結構, 再通過自組裝技術制備低表面能物質,從而構造出鎂合金基超疏水表面。
Liu 等在鎂合金表面利用激光構造出微米級粗糙結構,再利用 AgNO 3 水溶液刻蝕該表面,從而構造出仿生的微納米分級粗糙結構, 最后通過 DTS(CH 3 (CH 2 ) 11 Si(OCH 3 ) 3 )修飾,制備出疏水性鎂合金表面。此表面雖未達到超疏水性,但通過仿生學制備得到的該表面具有良好的耐蝕性能。Jia 等利用刻蝕 (草酸溶液) 、 鍍銀 (電化學) 、 自組裝 (硬脂酸修飾)三步工藝處理后,在鎂合金 AZ31 表面制備出接觸角為 153°、滾動角為 4°的超疏水表面,且該表面置于液氮中長時間存放后, 其超疏水特性未發生明顯變化。 Takahiro 等對鎂合金試樣進行浸泡刻蝕, 使其生長出具有納米片層結構的二氧化鈰薄膜, 經三甲基硅烷鈦和氟硅烷混合溶液修飾后得到鎂合金超疏水表面, 經電化學極化曲線測試表明, 制備的超疏水膜層比鎂合金基底具有更好的抗蝕性。隨后,該課題組利用超純水在 120 ℃條件下浸泡處理鎂合金試樣, 使微納米片狀結構物在該試樣表面垂直生成, 經過十八烷基三甲氧基硅烷化學修飾后,該表面呈現超疏水性。電化學測試表明該試樣具有良好的耐蝕性,且該表面對純水、酸、堿和鹽的水溶液均呈現較高的疏水性能。
Feng 等用硫酸和 AgNO 3 水溶液處理 AZ91鎂合金表面,再用十二烷硫醇進行修飾,制備得到的超疏水表面呈現良好的耐蝕性。Yin 等利用化學刻蝕和低表面能物質修飾制備得到鎂合金基超疏水膜層,該表面在 150 ℃下持續加熱 1 h 依然具有超疏水性。張光明等采用刻蝕(硝酸溶液) 、鍍銀(電化學)和自組裝技術(硬脂酸修飾)改性處理,在 AZ91D 鎂合金表面上成功制備出了超疏水膜層。Wang 等首先將鎂合金試樣浸入 0.1 mol/L 的尿素溶液中,150 ℃保持 12 h,隨后用去離子水沖洗干燥,再浸入 1.0%的 FAS 乙醇溶液中 12 h,最后取出,在 100 ℃的烘箱中干燥 2 h,制備得到超疏水涂層。 Liu 等在 Mg-Li 合金表面通過稀鹽酸刻蝕合金表面,再經 FAS(CF 3 (CF 2 ) 7 CH 2 CH 2 Si(OCH 3 ) 3 )乙醇溶液的浸泡來實現低表面能的微納米表面結構, 達到超疏水性。Nitant 等利用稀硫酸和雙氧水溶液先后對 AZ31 鎂合金進行化學刻蝕處理, 使鎂合金試樣表面生成了具有花朵狀微結構物,研究表明該表面具有超疏水性,試樣表面的微結構物為氫氧化鎂,且該物質的出現提高了鎂合金試樣的耐蝕性能。
1.3 電沉積法
電沉積法是通過外加電流, 在一定的電解質和操作條件下從化合物水溶液或熔鹽中來獲取金屬或化合物的工藝, 該工藝近年來在材料學領域獲得了廣泛應用,目前已成功應用于制備超疏水表面。
Liu 等利用電沉積技術在鎂合金表面制備出具有菜花狀結構的鎳涂層,通過硬脂酸修飾后,得到接觸角高達 160°、滾動角低至 2°的超疏水表面,該表面在戶外環境中顯示出良好的耐久性,且在 3.5%的 NaCl 溶液中表現出優良的耐蝕性。Liu等利用含有硝酸鈰六水化合物和肉豆蔻酸的乙醇溶液, 在 Mg-Mn-Ce 合金表面電沉積制備出超疏水性表面。極化和電化學阻抗譜測試表明,該超疏水表面在 NaCl、 Na 2 SO 4 、 NaClO 3 和 NaNO 3 的水溶液中與鎂合金基底相比, 其耐蝕性均得到提高。 Tan等利用電沉積技術將鎳、 銅等金屬在鎂合金表面生成特殊微細粗糙結構, 再利用硬脂酸修飾制備得到超疏水表面。 通過調控硬脂酸在制備混合溶液中的比率,可以控制制備表面對水滴的滾動角從小于10°到接近 180°,該研究為制備超疏水表面粘附力的可調控提供了新方法。 黃艷萍等利用硫酸刻蝕和電沉積法相結合的工藝,在 AZ31 鎂合金試樣上制備出低粘附超疏水表面,電化學測試結果表明,與鎂合金基底相比,硫酸刻蝕-電沉積法制備的鎂合金超疏水表面的耐蝕性明顯提高。
Wang 等首先利用含 Ni 溶液化學反應在AZ91D 表面沉積一層 Ni 作為對合金的預處理,然后通過電沉積方法將含 Cu 的鹽溶液中的 Cu 沉積到經鎳處理過的合金表面, 從而構建出表面微納結構。最后利用月桂酸進行表面低能化處理,得到超疏水表面。超疏水的 AZ91D 試樣在不同腐蝕介質中均表現出優異的耐蝕性能。 Han 等通過稀鹽酸將鎂試樣浸蝕 2 min 以粗化鎂表面,再浸入 NiSO 4水溶液中, 通過化學反應使金屬 Ni 沉積在鎂表面,進一步構建出微/納米分級結構,最后在脂酸水溶液中浸泡 50 min, 使表面形成硬脂酸來降低表面自由能,此時接觸角增至 144.5°,接近超疏水表面。
Wang 等通過電沉積工藝在鎂合金表面沉積粗糙鋅層,再通過硬脂酸修飾,得到了靜態接觸角為154°、滾動角為 3°的超疏水表面,該表面呈現良好的耐蝕性。
She 等采用電沉積技術在 AZ91D 鎂合金表面獲得接觸角高達 167°的花狀復合微結構的Ni-Co 合金鍍層超疏水表面,研究表明,該表面可將鎂合金試樣在 3.5%NaCl 溶液中的腐蝕速率大大降低,呈現出良好的耐蝕性和自清潔性能。Liu 等利用一步工藝將 Mg-Mn-Ce 合金放置在含有硝酸鈰和肉豆蔻酸的乙醇溶液中, 制備出最大接觸角為 160°、滾動角小于 2°的超疏水表面,且最短沉積時間為 1 min,其耐蝕性大大提高。She 等利用電沉積制備出了接觸角可達 163°和滾動角僅為2°的鎂合金超疏水表面,該表面在 3.5%NaCl 溶液中呈現出耐蝕性明顯提高的性質。
1.4 水熱法
水熱法又稱為熱液法, 是指在密封的壓力容器中,以高溫高壓的水溶液作為反應介質,使待處理工件與溶液之間發生化學反應或重結晶, 從而獲得所需性能的工藝。 目前此工藝已成功用于制備超疏水膜層。
Gao 等在過氧化氫環境中進行快速水熱反應, 不使用任何模板和表面活性劑, 可以獲得 AZ31鎂合金超疏水表面,而經 FAS 修飾后其接觸角可以進一步提高。Wang 將經打磨處理的鎂合金試樣放入尿素水溶液中, 在 150 ℃的反應釜中加熱12 h,再用 FAS 進行修飾,在 100 ℃下加熱烘干,制得超疏水表面。
1.5化學轉化膜法
利用化學轉化膜來制備鎂合金超疏水表面是近年來發展起來的新工藝。 該工藝利用鎂合金試樣與處理液發生化學反應從而生成防護膜來提高鎂合金的耐蝕性,也被稱為化學氧化膜法。
Yang等利用化學轉化膜法在AZ91D鎂合金表面制備出具有自修復能力且在 3.5%NaCl 溶液中具有良好耐蝕性的錫酸鎂膜層。研究表明,在3.5%NaCl 溶液中的自修復機理是“溶解-再沉積”過程,其最佳修復時間為 4 h,對自修復后的錫酸鎂膜層進行硬脂酸修飾,制備得到具有耐腐蝕的超疏水表面。Zhao 等在 AZ91D 鎂合金表面制備一層經脂肪酸修飾的磷酸鹽轉化膜層,該膜層呈現接觸角大于 160°,滾動角為 2°且耐蝕性顯著提高。Takahiro 等通過化學轉化膜技術在 AZ31鎂合金表面生成具有納米結構的二氧化鈰膜層,再利用氟硅烷修飾制備得到超疏水表面, 該試樣在3.5%NaCl 溶液中進行電化學阻抗譜測試表明,該試樣的耐蝕性與鎂合金基底相比得到明顯提升。
2結語
1)鎂合金基底超疏水表面的制備過程中為達到降低材料表面自由能的目的,選用的試劑多為含氟有機試劑,在實驗過程中,往往會給人體及環境帶來危害,且造價高昂,如何開發并利用環境友好型、經濟性高且可操作性強的試劑是研究的方向之一。
2)鎂合金超疏水表面制備技術的開發研究目前多停留在實驗室階段, 開發出的超疏水表面往往存在力學性能差、易磨損的缺點,如何提高超疏水表面的可靠性和耐久性是未來研究方向之一。
3)如何定量評價鎂合金基底超疏水表面的耐久性及其影響因素, 鎂合金基底超疏水表面對具體工程實際應用的影響還需進一步研究。
更多關于材料方面、材料腐蝕控制、材料科普等方面的國內外最新動態,我們網站會不斷更新。希望大家一直關注中國腐蝕與防護網http://www.ecorr.org
責任編輯:邢云輝
投稿聯系:編輯部
電話:010-62313558-806
郵箱:fsfhzy666@163.com
中國腐蝕與防護網官方 QQ群:140808414
免責聲明:本網站所轉載的文字、圖片與視頻資料版權歸原創作者所有,如果涉及侵權,請第一時間聯系本網刪除。
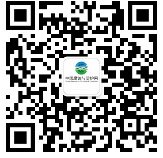
官方微信
《中國腐蝕與防護網電子期刊》征訂啟事
- 投稿聯系:編輯部
- 電話:010-62316606-806
- 郵箱:fsfhzy666@163.com
- 中國腐蝕與防護網官方QQ群:140808414