輕質原油劣質化,常減壓裝置面臨重大考驗
本文的常減壓裝置設計于1995年,于1997年建成投產。最初是為了輕質原油所設計的。然而,隨著近年來油田的深度開采及加工原油結構調整,輕質原油的密度、硫含量和酸值逐年上升,已接近于含硫含酸原油,給裝置安全生產帶來了重大隱患。
表1近年來玉門煉廠加工混合原油典型數據
裝置問題一一顯現,工藝改進勢在必行
1 塔頂腐蝕加劇
2012年以來常減壓裝置塔頂低溫部位出現多次空冷管束泄漏,主要是原油中的氯化物和硫化物受熱分解產生的HCl和H2S,在有冷凝水存在時形成酸性環境對設備造成腐蝕,為典型HCl-H2S-H2O腐蝕。
2 直餾柴油酸度超標
2012年起常減壓裝置加工出的直餾柴油酸度嚴重超標,不但具有較強的腐蝕性,而且當直餾柴油與催化裂化柴油調合時,柴油的顏色變深,安定性變差,給總廠柴油調和帶來很大難度。
3 加熱爐出口泄漏點增多
2013年常減壓裝置在高溫液相和氣相混合區域出現多次滲油,屬于典型的高溫部位環烷酸腐蝕。
4 減壓塔高溫部位均勻減薄加劇
2013年減壓塔高溫部位均勻減薄加劇,溫度基本在250℃-380℃之間,是由原油中所含的有機硫化物熱分解生成硫化氫而引起的均勻腐蝕,屬于典型的高溫硫腐蝕。
5 空氣預熱器出現內漏
表2 常壓裝置加熱爐熱效率監測數據(2013.6)
由表2可知,空氣預熱器內部出現泄漏。主要是由于在加工含硫原油時,瓦斯燃燒過程產生大量的SO2和SO3,在換熱冷凝時形成硫酸,產生了較嚴重的硫酸露點腐蝕。
積極探索,應對措施相應出爐
1 合理優化摻煉比例
常減壓蒸餾裝置摻煉的原油為混合原油,因此裝置根據自身的特點,選擇合適的加工工藝路線,優化原油調和比例,避免含硫高的原油與含酸高的原油混煉,以防止原油中的硫和酸產生的共同效應加劇對設備的腐蝕。
2 改進工藝防腐
采用超聲波破乳——電脫鹽技術代替原有的破乳劑脫鹽,有效降低了脫后原油鹽含量;同時根據原油性質優化了HY8110中和劑緩蝕劑配方來減緩腐蝕,即改進“一脫二注”防腐工藝。
表3、表4為采用“一脫二注”法后原油鹽含量及常壓塔頂冷凝水中鐵離子及氯離子的含量。
表3原油脫鹽前后鹽含量變化
表4 注入中和劑緩蝕劑和水后塔頂冷凝水參數指標及腐蝕速率
由表3和表4可以看出優化傳統的“一脫二注”法后所有的指標都比前一年同期有所改善。
3 設備材質升級
將空冷材質升級為09Cr2AlMoRe;對腐蝕嚴重的部分空冷升級為雙相不銹鋼2205。對于環烷酸腐蝕嚴重的爐出口轉油線升級為316L,對于減壓高溫渣油管線升級為Cr5Mo,以應對高溫硫腐蝕。
4 直餾柴油加注柴油脫酸劑
制定了常二線柴油加注復合脫酸劑方案,在柴油管線增加管道靜態混合器,增加混合強度,解決常壓直餾柴油酸度高的問題。
表5脫酸工藝改造前后柴油酸度變化
由表5以看出,改造后常二線柴油酸度明顯降低。
5 建議減壓高溫部位加注緩蝕劑
目前中石化已研制出了緩蝕性能優于美國同類產品的高效高溫緩蝕劑。經實驗證明:該緩蝕劑不僅可用于解決高溫環烷酸酸腐蝕問題,而且對高溫硫腐蝕也有很好的緩蝕作用。
實施對策,以觀后效如何
針對裝置存在的腐蝕類型和存在部位等18個點進行腐蝕在線監測改造,使用15個精密電阻探針和3個PH計系統涵蓋了常減壓裝置幾種腐蝕的典型部位,提供的數據能直觀的反應出某段時間及某段管線的腐蝕速率和腐蝕裕量,能客觀地反應溫度和PH值大小對腐蝕的影響,裝置重點腐蝕部位監測結果如表6。
表6 常減壓裝置重點部位腐蝕在線監測結果(2014.5.31)
由檢測結果可知通過技術改造,目前常減壓裝置重點部位腐蝕率均滿足HG/T20580-2011上給出的化工設備腐蝕速率范圍(0.13~0.25mm/a)腐蝕裕量充足,材質升級合理、防腐措施到位。
希望通過對本實際案例中出現的問題與具體解決措施的分析,能夠給有類似問題的同行們新的思路和啟迪。
更多關于材料方面、材料腐蝕控制、材料科普等等方面的國內外最新動態,我們網站會不斷更新。希望大家一直關注中國腐蝕與防護網http://www.ecorr.org 責任編輯:王元 《中國腐蝕與防護網電子期刊》征訂啟事
投稿聯系:編輯部
電話:010-62313558-806
郵箱:ecorr_org@163.com
中國腐蝕與防護網官方 QQ群:140808414
免責聲明:本網站所轉載的文字、圖片與視頻資料版權歸原創作者所有,如果涉及侵權,請第一時間聯系本網刪除。
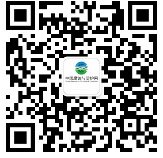
官方微信
《腐蝕與防護網電子期刊》征訂啟事
- 投稿聯系:編輯部
- 電話:010-62316606-806
- 郵箱:fsfhzy666@163.com
- 腐蝕與防護網官方QQ群:140808414