復合材料具有輕質、高比強度、高比剛度及1有效實現結構減重,提高飛行性能、安全性和可靠性,并有可能使得復合材料結構全壽命成本低于傳統的金屬結構,同時復合材料的廣泛應用還可進一步推進隱身和智能直升機結構設計技術的發展。因此,近幾十年來,幾乎直升機的所有結構都開展了復合材料的應用研究,并大部分得到了應用推廣。
直升機復合材料應用特點
直升機與固定翼飛機相比,最顯著的不同是有一、兩個或更多的旋翼,利用旋翼旋轉所提供及傳動系統所傳遞的升力、前進力和操縱力,直升機能有效的完成垂直起落、空中懸停和前飛、側飛、回轉飛行及貼地飛行,以及當發動機停車時可自轉下滑安全著陸。旋翼及傳統系統作為直升機所獨有的兩大動部件,因其動力響應產生高周疲勞( HCF )環境;同時直升機因地空地循環所誘發也存在低周疲勞( LCF )環境;對于部分利用懸停效應承擔搜索救援及外載運輸等起重任務的直升機,其附加疲勞環境為重復周期疲勞( RCF );選用具備優良抗疲勞特性的復合材料將是直升機追求高減重效益的最有效途徑。
直升機與固定翼飛機相比,其飛行高度一般在6 000 m以下,甚至在超低空15~30 m之間,飛行速度約在300 km/h,是一種中低空、低速飛行器。與高空高速固定翼飛機所不同,其主要應用環境為濕/熱、干/寒、沙塵/雨淋、海水等惡劣環境條件,為滿足在上述不同區域、不同氣候條件下的苛刻使用要求,具備優良的耐候性、耐蝕性的復合材料將是直升機環境適應性設計的必然選擇。
因直升機與固定翼飛機上述不同的飛行原理和使用環境,使直升機結構設計要求,除一般航空器設計的剛度、強度、質量、空氣動力、工藝性和使用維護性外,還有其特殊要求。例如旋翼系統對氣動彈性、疲勞壽命、振動、可靠性等設計要求尤為關注;突出的振動問題使直升機結構設計在很大程度上是結構動力學設計問題,直升機結構設計中必須設法降低強迫振動的振幅和避免出現動穩定性問題;軍用直升機還應滿足防彈、耐墜性等要求。
直升機結構通常分為以旋翼系統為代表的動部件結構和機體結構兩大類。這兩類結構設計有明顯的不同,旋翼系統動部件更加突出直升機專有技術。旋翼系統動部件設計以疲勞強度和調頻設計為主,率先選用復合材料正是看中復合材料優異的疲勞和剛度可剪裁特性,樹脂基復合材料模壓成型有利于旋翼槳葉采用先進翼型、沿翼展多翼型先進氣動布局和采用繞襯套纏繞接頭等,球柔性旋翼連接件采用的鋁基復合材料具有高的比剛度、比強度、低密度和韌性好等優異的力學性能,尤其具有極好的抗疲勞特性。與鈦合金結構件相比質量分數減輕30%,與鋁合金結構件相比壽命提高50% 。復合材料在旋翼槳轂上的應用不僅使槳轂明顯減重,更重要的是研制出了星型柔性槳轂、纖維/彈性軸承槳轂、無軸承槳轂等新型槳轂。
直升機機體結構采用復合材料,一方面著眼于結構減重,另一方面著眼于改進和創新結構設計及制造工藝,如涵道大垂尾結構、駕駛艙管梁骨架結構、耐墜吸能結構和大型整體壁板、夾層結構尾梁等。
與固定翼飛機相比,直升機在復合材料應用技術特點上有一定區別,主要表現在:
1結構形式不同。直升機與固定翼飛機有顯著區別,旋翼是直升機特有的結構,旋翼系統及傳動系統不僅動部件多,受力方式也不同;機身存在較多薄壁復雜曲面,大量采用蜂窩夾層結構。
2材料體系不同。直升機采用環氧樹脂預浸料,增強材料以織物為主,包括碳纖維/玻璃纖維/芳綸等織物,而固定翼飛機主要采用雙馬樹脂碳纖維單向帶預浸料;直升機旋翼連接件基于疲勞及減重的考慮,采用了鋁基復合材料。
3性能要求不同。由于結構形式和使用環境的區別,直升機復合材料在材料選用和環境適應性要求上與固定飛機存在差異,使得固定翼飛機所獲取的設計性能數據不能直接應用到直升機上;且對于旋翼系統等直升機特有的動部件,還要求復合材料具有優異的高周疲勞特性。國內直升機復合材料應用情況1960年代,國內即開展了碳纖維復合材料研究,直9型機就大量采用了環氧基碳纖維、高強玻璃纖維及芳綸的復合材料,主要用于主槳葉、涵道大垂尾、平尾、側端板、座艙罩等結構部件。
1990年代,國內在開展直升機研制初期即開始確定大量采用先進復合材料的技術方案,主要涉及到了各個型號旋翼系統的動部件(槳葉、槳轂、主減機箱),機身結構的座艙骨架、尾梁、垂尾、平尾等主受力結構。
進入21世紀后,碳纖維及高強玻璃纖維環氧基復合材料等此類戰略性材料基本已實現國內自我保障,解決了關鍵材料受制于人的困境,并掌握了包括復合材料研制、結構設計、制造、檢測、試驗、數據分析以及項目管理在內的系統的工程化驗證技術和管理方法,實現了碳纖維等關鍵材料的工程化生產和大批量供應。通過建立國產復合材料標準體系,對直升機復合材料從原材料控制到結構設計、工藝制造、無損檢測以及試驗驗證等各方面進行了統一規范,直接推動了國產復合材料在國內直升機上的大面積應用。
目前,國內在研和在役直升機均大量采用復合材料,主要應用部位有旋翼槳葉中的大梁、蒙皮、墊布、后緣條等,機體結構中的機身下構件蒙皮、座艙、動力艙整流罩、短翼、尾梁蒙皮、壁板、尾斜梁、尾段整流罩、儀表板、遮光罩等。其中,槳轂部分零件采用了金屬基復合材料,武裝直升機座艙采用了陶瓷復合防彈裝甲。
國內直升機復合材料應用存在的問題
直升機上推廣使用復合材料是一項能大幅度改善性能、降低生產成本、縮短生產周期和收益頗豐的適用技術。從設計的角度來考慮,目前主要要研究復合材料結構的力學問題,其中包括復合材料結構耐久性、抗墜毀性、定壽方法、接觸應力、彈擊損傷等;復合材料機身結構設計問題,包括設計準則、鋪層設計、破壞形式、損傷容限試驗、防斷裂方法、連接方法、疲勞強度、修補方法、工藝成型及質量控制等;復合材料旋翼結構設計研究,包括設計準則、選材、旋翼槳葉及槳轂結構型式及剖面形狀、槳葉及槳轂鋪層構造及剛度設計、測試及工藝等。
由于復合材料具有各向異性和性能可設計性的特點,設計人員以根據直升機結構的特點選用適當的組分材料和調整增強材料的方向使設計的直升機結構性能大幅得到改善,同時實現降低結構質量、減少生產成本、縮短生產周期的目的。
從國內直升機復合材料的應用與發展現狀來看,制約復合材料在國內直升機上的應用也在性能、重量和價格這3 個方面。
性能方面
目前國內先進直升機樹脂基復合材料用量很大,但由于其耐溫性能、濕/熱性能和斷裂韌性等幾個關鍵指標的限制,影響了其在某些特殊工況要求部位的推廣應用。
新一代損傷容限型、高抗疲勞性能的鋁基復合材料在應用上獲得了很好的減重效果,并有利于降低制造和維護成本。目前國內外正在進行這些鋁基復合材料的擴大應用和材料改進研究工作。
陶瓷復合防彈裝甲已在國內軍用直升機上成熟應用,但陶瓷材料脆性大,彈擊后容易破碎,抗多發彈能力較差。針對未來武裝直升機高生存力的要求,對開發出防護性和韌性好的陶瓷復合材料提出了需求。
質量方面
直升機大量應用薄壁結構,其復合材料面板厚度為0.3~1.0 mm,而目前直升機上普遍應用的織物預浸料單層厚度約為0.2~0.3 mm,復合材料的方向可設計性和厚度可設計性受到限制,明顯犧牲結構質量,制約了復合材料在直升機結構上的減重優勢。
價格方面
直升機復合材料成本主要包含原材料成本、制造成本和使用維護成本,制造成本大約占復合材料制件總成本的80%。熱壓罐法成型是目前國內直升機復合材料制件最主要的成型工藝方法,但其設備成本高,生產周期長,能源消耗大,故其生產成本高。為降低制造成本,國外已在開發低成本成型方法和先進的自動化工藝與設備,提升復合材料整體化、模塊化設計和制造水平上開展了大量的研究工作,在這些方面國內還有較大差距。
直升機復合材料發展趨勢
未來復合材料在直升機發展中的地位將更加重要,直升機在繼續選用成熟應用的復合材料的同時,應考慮開發性能更優異、且更適合直升機設計與制造要求的先進復合材料,采用更多先進的制造工藝和技術,擴大復合材料在直升機上的使用范圍。未來直升機復合材料總體發展方向是高性能化、結構-功能一體化、設計-制造一體化、智能化及低成本化協調發展,其發展趨勢展望如下:
1 高性能化
原材料技術是先進復合材料應用的基礎與前提,直升機復合材料的高性能化發展是未來的趨勢之一。樹脂基復合材料將在發展高強高模增強纖維的同時,提升樹脂基體的韌性、濕熱性能及環境適應性能力;金屬基復合材料著重于提升損傷容限及抗疲勞性能;陶瓷復合防彈裝甲材料應在提升綜合防護性能的同時進一步減輕質量。
2 結構-功能一體化
直升機的服役環境對防雷擊性能提出了要求,同時軍用直升機由于戰場特殊環境,還應具有隱身(視覺、紅外、雷達和聲學)、防彈、電磁屏蔽、耐墜性等功能。未來先進直升機復合材料應至少具備兩種或更多功能,有效實現復合材料結構承載-功能(隱身、防彈、防雷擊、電磁屏蔽、耐墜性等)一體化發展將是一大趨勢。
3 設計-制造一體化
發展以DFM(Design for Manufacture)為核心的設計-制造一體化技術,其實質是隨計算機和制造技術的進步,采用全新的設計理念和手段,發展數字化、自動化的設計技術,將設計和制造進一步融為一體,從而加快產品研發進度,提高質量。實現直升機復合材料制造過程數字化與飛機結構設計數字化趨向相適應,減少試驗次數,縮短研制周期,節約研發資金,降低廢品率及提高生產效率。
4 智能化
智能化是直升機復合材料結構設計亟需關注的研究方向。開發直升機復合材料自感知、自診斷、自修復和自適應智能化技術,可以實現直升機復合材料結構噪聲抑制、振動控制、主動變形和性能監測與損傷自修復。
5 低成本化
直升機復合材料全壽命周期的低成本化是未來的發展趨勢,包括材料低成本化、設計低成本化、制造低成本化和維護低成本化4 個方面。核心是發展低成本制造技術,其主要有:發展以自動鋪帶(ATL)和纖維自動鋪放(AFP)為核心的自動化制造技術;發展以共固化/共膠接為核心的大面積整體成型技術;發展以樹脂傳遞模塑成型技術為核心的低成本制造技術;發展非熱壓罐成型技術等。
結束語
隨著近幾十年的不斷發展,復合材料在直升機上的應用已發展到主承力結構并實現大范圍成熟應用,也推動了直升機技術的進步。國內直升機復合材料通過國內直升機型號需求的牽引和推動,目前已經基本實現國產化,形成了我國直升機復合材料研發及生產體系,技術水平在不斷提高,并有了較全面的發展和廣泛的應用,但是與國外發達國家相比,在材料、設計、工藝等方面仍有差距。未來國內直升機技術發展將追求高效能、長壽命、高可靠和低成本,對其材料與結構的綜合要求越來越高,對高性能復合材料、先進設計技術和制造工藝需求迫切。為此,國內今后應在解決目前發展中存在的復合材料性能穩定性問題的同時,大力發展高性能復合材料、結構功一體化復合材料和智能復合材料;重視發展自動化制造、大面積整體成型和低成本制造技術,提升復合材料工藝制造水平,降低制造成本;還應重點關注復合材料整體化和模塊化設計技術,發展復合材料設計-制造一體化技術,進一步提升復合材料的應用技術水平。
更多關于材料方面、材料腐蝕控制、材料科普等方面的國內外最新動態,我們網站會不斷更新。希望大家一直關注中國腐蝕與防護網http://www.ecorr.org
免責聲明:本網站所轉載的文字、圖片與視頻資料版權歸原創作者所有,如果涉及侵權,請第一時間聯系本網刪除。
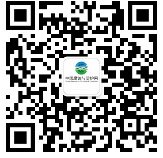
官方微信
《中國腐蝕與防護網電子期刊》征訂啟事
- 投稿聯系:編輯部
- 電話:010-62316606-806
- 郵箱:fsfhzy666@163.com
- 中國腐蝕與防護網官方QQ群:140808414