深海環境讓腐蝕防護面臨挑戰
為了進行深海水下生產系統合理的選材,需要對系統所處的深海環境因素的影響進行分析,而管道輸送介質的參量(H2S和CO2含量和分壓)以及環境參量(溫度,壓力,流速,微生物等)對管道腐蝕有很大影響,這些因素的不斷變化以及長期的累積作用,對管道的破壞作用是巨大的,因此必須先對系統所處的環境進行充分的考慮。
1.1CO2/H2S因素的影響
CO2和H2S是油氣管道內最常見,最有害的兩種腐蝕管道的物質。單純的潮濕的H2S主要導致材料的應力開裂,氫脆等破壞,而單純的CO2與水作用主要形成碳酸,在管道上形成析氫作用,可形成Fe3O4或者FeCO3兩種主要腐蝕產物,且兩種氣體隨著pH值的變化導致腐蝕更為嚴重。兩種氣體在管道腐蝕過程中存在競爭協同效應,CO2/H2S的分壓比決定了腐蝕過程中的控制因素,對管道均會產生嚴重破壞,所以對這兩種酸性氣體的監測和控制,有利于管道的長久使用。
1.2溫度和壓力的影響
現行的水下管道內油氣溫度80~90℃,最高可達100℃以上,高溫加劇了CO2/H2S腐蝕,氯離子腐蝕等。水下外部海水的壓力和管道內部的壓力對材料的選擇提出了要求,管道內部壓力增加,導致腐蝕氣體CO2/H2S分壓的增加,均會加劇管道的腐蝕。
1.3 氯化物的影響
原油經過脫水,殘留下無機鹽主要為氯化物,氯離子的含量可達近20000 mg/L,體系中氯離子的存在使鐵的腐蝕速度加快,增加了溶液的導電性,并使溶液中H+活度加大,同時以一定的反應級數直接參加了電極反應,對金屬的陽極溶解具有催化作用。
研究表明,氯離子不僅降低材料的腐蝕電位,而且對金屬材料的表面膜具有極強的穿透和侵蝕作用,使膜發生顯微開裂,形成孔蝕核。
1.4流速的影響
流速是輸油氣管道應該控制的一個參數,它是關于水下采油量和管材尺寸的函數。流速過低可能導致大量腐蝕垢的沉積,從而影響系統正常的運行;而流速過大可能導致管道的沖刷腐蝕,在變徑或變向部位,可能導致局部流速過大,并且當流速到達一定值時,形成湍流,導致沖擊和空泡氣蝕等,所以合理選擇流速也是管道保存的一個必要條件。
1.5微生物的影響
深海環境苛刻,高壓、低溫(或局部高溫)、低氧等,存在著種類繁多的微生物(如細菌、真菌、藻類和原生物等),它們附著于工程材料表面,形成生物膜,在生物膜內部,溶解氧、pH、有機物和無機物種類等都與外部環境不同,會造成微生物腐蝕,其中最主要的是由硫酸鹽還原菌(SRB) 引起的腐蝕。
SRB一般認為是厭氧細菌,溶解氧對SRB的生長會產生很大的影響,海水溶氧量范圍一般為0-9 mL/L。一些好氧微生物的代謝活動也給SRB營造了一個厭氧的環境,使SRB得以繁殖,從而加速管道腐蝕,目前,關于SRB腐蝕的機理有陰極去極化機理、濃差電池機理、局部電池機理、代謝產物機理、沉積物下的酸腐蝕機理、陽極區固定機理等。
選自《腐蝕與防護》第36卷 2015年第10期
作者:張雷,副研究員,博士,任職于北京科技大學
深海常見的腐蝕影響因素
深海通常指1000米以下的海洋,占到海洋總面積的3/4,而其中深海沉積物覆蓋了地球表層的50%以上。深海及深海沉積物中微生物的生存面臨高壓,低溫或高溫、黑暗及低營養水平等幾個主要極端環境,長期以來一直被認為是一片“荒蕪的生命沙漠”。然而,在深海極端環境條件下卻存在著一些絕大多數微生物所不能生長的高溫、低溫、高酸、高鹽或高壓等極端環境下生活的微生物。開展深海適冷菌、深海適熱菌、深海適壓菌等微生物附著條件下的材料腐蝕機制及其防護的研究具有更大的挑戰性和創新性。深海環境下生產設施不僅受到海水溫度,壓力,氯離子等影響,而且油、氣、水多相介質的輸送,特別是多相介質中含有H2S/CO2時,會進一步加劇了對管道的氫脆、孔蝕等。復雜的深海環境更加凸顯了水下設施選材及腐蝕控制的重要性。目前對生產系統進行腐蝕控制常用的方法是陰極保護或加注緩蝕劑。此外還可對影響生產設施的關鍵腐蝕因素,如H2S分壓,CO2分壓,溫度,氯離子含量等進行監測,從而預測材料的失效時間。
1.CO2/H2S因素的影響
隨著海洋工程開發步伐加快,深海工作站、油氣勘探等均向地質條件和物理環境更加復雜的區域發展,一些高H2S和CO2含量高含硫地質環境的區域已成為油氣勘探的重點,深海用高強度材料的需求量激增,而其失效壽命越來越受到關注。CO2和H2S是油氣管道內最常見,最有害的兩種腐蝕管道的物質。單純的潮濕的H2S主要導致材料的應力開裂,氫脆等破壞,而單純的CO2與水作用主要形成碳酸,在管道上形成析氫作用,可形成Fe3O4或者FeCO3兩種主要腐蝕產物,且兩種氣體隨著pH值的變化導致腐蝕更為嚴重。兩種氣體在管道腐蝕過程中存在競爭協同效應,CO2/H2S的分壓比決定了腐蝕過程中的控制因素,對管道均會產生嚴重破壞,所以對這兩種酸性氣體的監測和控制,有利于管道的長久使用。
國內外鉆井工程中腐蝕研究主要集中在CO2、H2S和CO2/H2S的腐蝕與防護方面,防腐蝕措施主要包括選材、控制鉆井液、防腐層、電化學保護等。這些防腐措施都有一定的缺陷。由于應力腐蝕破裂的威脅,許多深海探測用高強度材料不得不全部采用鈦合金以滿足要求,但由于資源和成本因素,不可能大量采用鈦合金。H2S 對金屬的腐蝕主要為硫化氫應力腐蝕(SSC)和氫誘導開裂(HIC),其破壞敏感度是隨H2S濃度增加而增加,在飽和濕H2S中達最大值。
2.陽光的影響
陽光通常不直接參與材料腐蝕過程,主要通過影響海生物的生長起作用。清澈干凈的海水中,用光敏設備可在200 m深度探測到陽光。由于吸收和散射引起衰減,20 m以下就沒有可利用的陽光了,也就是說,那些需要陽光才能生長的海生物在20 m以下不能生存。同時,沒有陽光也就是沒有紫外線,那么所有在陽光下不能使用的保護涂層和合成橡膠都可使用。
3.溫度和壓力的影響
溫度不僅會直接影響到材料的腐蝕行為,對其他影響腐蝕的因素也有一定的作用,如:溫度上升,氧的溶解度會降低,海生物活性增加,鈣質水垢更易沉積到金屬表面。溫度在海面下最初300 m時下降速度很快,再向下到1000 m溫度下降速度減小。低于這個深度溫度幾乎恒定在冰點上下幾度范圍內。在4000 m深水層,不同海洋的溫度分布趨于均勻,整個大洋的水溫差不過3℃左右。底層的水溫主要受南極底層水的影響,其性質極為均勻,約為0 ℃左右。
靜水壓力每下降100 m壓力增加1 MPa。這只是在海水溫度、鹽度和海水密度不變時成立。實際上在不同海域這些因素變化程度是不同的。如果需要知道某處的確切壓力,必須實際測量或根據溫度和鹽度梯度的詳細數據計算。
4.含氧量的影響
海水溶氧量范圍一般為0-9mL/L。通常表層海水含氧量為飽和或接近飽和;300~1000 m深度海水含氧量相對較低;1000 m以下海水含氧量增加,一直到海底達到相對較高的水平。中間含氧量相對較低的范圍稱為最小含氧區,這可歸因于從海面下沉的腐爛微生物消耗了氧氣。北太平洋的最小含氧區是世界上最大的無氧水體。1000m以上含氧量最高為0.25 L。在一些海溝或其他區域,海底海水幾乎不含氧而成為還原環境。一些深海區域由于可以得到含氧豐富的海流的補充,例如南極溶化的富含氧的冷水,其含氧量可以達到表層海水的水平。
5.洋流速度
通常海洋深層和近海底的洋流要比表面洋流緩慢。根據美海軍測試表明,百慕大附近350 m深洋流速度為50-60 m/s。深海洋流中浮球的不確定漂移表明洋流的方向和速度也是變化較大的。
6.海生物污損
試驗表明嚴重海生物污損范圍為從海而到180 m深處。180~1200 m為輕度,1200m以下被認為非常輕微。除上述基本的海水腐蝕因素外,有可能對腐蝕造成影響的其他因素是靜態水壓、沉降速度、海底沉降物的性質以及厭氧菌產生的硫化氫等。
深海的腐蝕因素眾多,如溫度、壓力、pH值、化學成分、流速、氯化物、生物環境等等,這些參數都會對材料的腐蝕產生影響。
參考文獻:郭為民,李文軍,陳光章。材料深海環境腐蝕試驗。裝備環境工程,2006.
深海環境應當如何選材
水下生產設施包括大量的部件,根據部件的腐蝕形式,材料適用性和經濟性綜合考慮,對主要部件選材方法進行如下分析:
1 井口和采油樹的選材
井口和采油樹主要用于原油的生產,海水和處理后的海水,大量的化學物質的注入口以及進行氣舉作業。在原油的生產與傳輸過程中起到一個關鍵性的作用。主要包括采油樹的主體結構和聯接部件,井口罩,密封部件,套管掛,油管掛,閥門和阻氣門,大量的墊片等。受到傳輸介質高流速的沖刷作用,而且傳輸介質中可能含有砂,對井口和采油樹存在大量的侵蝕作用。另一方面,井口和采油樹存在大量小部件,如果不能正確的選材可能導致整體的失效。所以,對于井口和采油樹整體而言,所有零件推薦選擇較耐蝕材料。
(1)采油樹主體和聯接部件
采油樹和聯接器可以選擇以下材料:①低合金鋼,AISI4130和8630,內部覆蓋著625合金;②ASTMA182F22(21/4%Cr,1%Mo鋼,內部覆蓋著625合金);③AISI410(13%Cr不銹鋼);④ASTMA182F6NM(13%Cr4%Ni不銹鋼);⑤雙相不銹鋼。
對于上述提供的材料,焊接部位覆蓋耐蝕的625合金的低合金鋼,在海下表現出較低的風險,低合金鋼推薦采用為ASTMA182F22,耐蝕合金推薦采用A182F6NM。
(2)井口罩和密封部件
這些部件相對于采油樹的主體部分較薄,可以采用AISI4130或8630來制造。在潤濕和密封部位,可以在表面覆蓋625合金。
(3)套管掛
套管掛通常采用AISI4130,4140或8630來制造,并且在正常的操作環境下,不能接觸生產的流體。
(4)油管掛
油管掛應采用高強度的CRA材料來制造,根據工況要求,可以采用以下材料:① 覆蓋625合金的AISI4130,8630或者ASTMA182F22;② ASTMA182 F6NM;③22%或25% Cr雙相不銹鋼;④ 718合金
(5)閥門和阻氣閥
閥門和阻氣閥可以通常采用下列兩種方法來制造:①覆蓋625合金的AISI 4130,8630或者ASTMA182F22;②ASTMA182F6NM。
(6)墊片
在水下的油氣管道的墊片可以采用:①316不銹鋼;②退火態的825和625合金。如果墊片應用在環形槽上,建議采用退火態的625合金或6%Mo的不銹鋼。對于處理過的海水注入系統,退火態的625合金是可以滿足要求的,而對于未經處理的海水則需要對材料的耐開裂能力和接觸腐蝕進行充分考慮。
2 匯管的選材
水下匯管是一個高風險的部件,主要用于存儲生產的流體,包括油,氣和產生的水,注入處理和未處理的以及產生的水,注入存儲用的氣并提高生產效率。功能的缺失,對導致油氣的泄露。對于匯管的材料選擇和裝配在ISO13628-15中已經詳細的介紹,此處對其他方面進行補充:比如說ERW/HFI 管道一般不會推薦到集合管的選材中,由于它可用的厚度可能不能夠滿足設計的要求,這在ISO13628-15標準中并未提到。
由于水下匯管設計的復雜性,存在大量的分支,閥門,死角,普通碳鋼加緩蝕劑可能達不到目的,并且無法對其腐蝕情況進行監測,可以首選具有一定強度和斷裂韌性的耐蝕合金。如果管道的服役時間小于10年,可以選用具有一定耐蝕能力的碳鋼。選擇耐蝕合金時主要考慮:雙相和超級雙相不銹鋼;管道內部覆蓋一層625合金。
3 閥門的選材
在水下生產設備中存在大量的閥門,包括采油樹的主閥門,匯管和流線管道處閥門,液壓控制系統的閥門等。而在相關的標準中,對閥門的選擇進行了規定,包括:APISpecs6A,17D,14A和RP14B;ISO10423,13628-4,13628-6,13628-8和14723以及ISO15156/NACEMR0175。
而對于閥門的選擇主要應考慮幾個主要因素:溫度和壓力范圍、在閥門主體和局部位置流體的腐蝕性和侵蝕破壞、固體潛在的磨損(覆蓋耐磨的或者光滑的表面)、固體潛在的沖擊作用,比如在材質較脆的閥門處的壓裂支撐劑的作用、不同材料之間的電偶腐蝕的影響、在法蘭和密封面處的縫隙腐蝕、移動部件的耐劃傷性能、對于分金屬材料而言,爆發性的解壓,耐溫度和化學物質的能力、材料的陰極保護的影響、材料有效涂層的影響、材料的經濟性問題等
總體而言,對于金屬材料包括碳鋼和低合金鋼,不銹鋼(奧氏體,馬氏體,沉淀強化鋼等),鎳基合金,鈹銅合金等的選擇需考慮特定實際環境,通常在管道潤濕部位覆蓋鎳基合金來抵抗碳鋼和低合金鋼的內腐蝕。非金屬材料主要用于密封部位,在使用時也進行鍍層保護,如鈷合金,碳化鎢及化學鍍鎳等,來提高密封性,耐劃傷,耐腐蝕和侵蝕能力。
金屬材料的承壓邊界根據設計和生產標準進行選擇,在ISO14723中只是列舉了一部分可用材料的壓力-溫度等級。因此,在采油樹,匯管及流線管道閥門選擇時常常不相同,對以上典型材料的要求可以根據標準ISO14723和NORSOKStandardM-630來選擇。
水下生產設備還有大量的部件,包括流線管道,冒口,法蘭,墊片,密封材料等,其選材的方法步驟與上述三種關鍵部位選材原則相似,在對使用環境了解的情況下,根據大量現行的標準進行選材,控制好腐蝕裕量,考慮經濟性,從而組合成一套適合服役環境下的水下生產系統。(作者:張雷)
深海水下設施腐蝕控制的推薦做法
設備在服役之后,除了控制好環境因素,采用對關鍵位置(例如:井口),關鍵因素(CO2分壓,H2S分壓,氯離子含量等)進行長效的監控,還需采用適合的材料腐蝕的控制方法。
1 陰極保護法
常見的陰極保護法包括犧牲陽極和外加電流陰極保護。
一個良好的陰極保護系統可以有效抑制碳鋼和低合金鋼的均勻腐蝕,接觸面的縫隙腐蝕,異金屬的電偶腐蝕,奧氏體不銹鋼氯化物應力腐蝕開裂,不銹鋼的點蝕和細菌腐蝕等。
現行的深海生產管路的陰極保護系統主要根據DNV RP-B401或NACE RP0176,而碳鋼和低合金鋼的海底管道系統主要依據ISO 15589-2來設計。對于生產設備由不同種材料組裝而成,在海水中耐蝕能力較差,所以必須采用陰極保護對系統進行保護處理。
深海中的環境隨著深度,位置,季節有很大的不同,對陰極保護電流的影響很明顯。針對此種情況,主要通過提高初始的電流密度來對不銹鋼進行極化。
保護與被保護材料之間還需要考慮如下:零件的設計盡量簡單,避免復雜的結構導致無法確保陰極保護的均勻性;確保被選擇的材料具有最優的熱處理工藝和微觀組織結構,及應用時確定材料與犧牲陽極之間的穩定的反應等,詳細的設計方案還應參照 NACE Report 7L192。
在海水中,電位相對于Ag/AgCl體系更負的情況下,容易導致氫脆和開裂。為了最大程度上減小水下設備氫脆開裂的風險,低壓陰極保護法采用二極管對電壓進行控制,或者選擇低壓陽極材料,比如Al-0.1% Ga合金、碳鋼等,而如何對不同體型的部件有效的控制,還需進一步實驗驗證。
傳統使用的陽極材料是鋁-鋅-銦體系的合金,但是傳統的合金比例可能在深海設備中或者在熱操作的環境中不太適用。最優的合金成分,首先對設備所處的環境進行了解后,通過相同環境下的模擬實驗來確定。
2 保護涂層
涂層保護效果的好壞,首先取決于被保護設備表面的情況,良好的表面對涂層的粘附力和效果至關重要。所以在設計涂層之前,根據ISO 8501-3中的做法,對設備表面進行處理,包括油,灰塵,可溶鹽,油脂等。
對于深海設備涂層的選擇,首先要考慮如下問題:
(1)在有涂層的構件上,陰極保護的效果(即與陰極保護的兼容性問題
(2)操作溫度
(3)操作深度
(4)海底環境
此外,還需要考慮基體材料和涂層的附著問題,涂層設計年限,日常維護等問題。而對于管線接頭,緊固件等特殊位置的涂層,參考ISO相關標準和實驗室的模擬實驗來進行涂層的設計。
3 加注緩蝕劑
緩蝕劑的加入,可以在管道內表面形成保護膜從而達到保護的目的,具體的緩蝕劑種類、加入量、緩蝕效果與經濟性還需根據具體的工況環境、材料等進行分析后確定。加注緩蝕劑的一個問題是要清楚流線的走向,另一問題就是加強管道中緩蝕劑量的實時監測。(張雷)
模擬深海環境高強度船體鋼陰極保護準則研究
在海洋環境中,通常采用陰極保護和涂層來抑制鋼材的腐蝕。然而,陰極保護電位過負會造成鋼材“過保護”,導致陰極過量析氫,提高鋼材的氫致開裂敏感性,此外,鋼材的強度越高,其氫脆敏感性也越高。
1、試驗材料與步驟
試驗材料為800MPa級別高強度低合金船體用鋼。
慢應變速率試驗(SSRT)采用棒狀拉伸試樣,工作段尺寸為,表面粗糙度為R0.8。用砂紙將試樣標距段打磨至平滑,用無水乙醇、丙酮擦洗并烘干。試驗采用SSRT/Constant Load/Low Cycle Fatigue恒應變速率高壓釜腐蝕實驗機。高壓釜內海水壓力為4.5MPa,溫度為(10±2)℃,通入高純N2控制溶液中溶解氧含量為4.0(±0.5) mg/L,以模擬低溫、低氧的深海條件。選定應變速率為1.89×10-7s-1(3.4×10-4mm/min)進行試驗。
試驗結束后立即取出試樣用蒸餾水、乙醇清洗斷口,冷風吹干,測量斷后伸長率和斷面收縮率;用XL-30環境掃描電鏡(SEM)觀察斷口的微觀形貌。
電化學試驗用試樣尺寸為10mm×10mm×2mm,工作面積為1cm2。其余部分用環氧膩子進行涂封。參比電極為銀/氯化銀參比電極(Ag/AgCl),輔助電極為鉑電極,文中電位若無特征,均相對于銀/氯化銀參比電極。掃描電位范圍-0.80V~0.20V(vs.Ecorr),掃描速率為20mV/min。
失重試驗用試樣尺寸為100mm×30mm×2mm,將試樣清洗、干燥后稱量,然后浸泡在高壓釜中,施加-0.75,-0.80,-0.85V恒電位進行陰極極化,周期為15d。試驗后清洗腐蝕產物并稱量,計算試樣的腐蝕速率。
2、結果與討論
2.1極化曲線
由圖1可見,陰極極化曲線的陰極段上有兩個明顯的拐點,拐點1電位在-0.75V~-0.85V,在此電位下,材料的陰極反應由氧的活化極化控制轉變為氧的擴散控制;拐點2電位在-0.95V~-1.05V,此電位下,材料的陰極反應由氧濃差擴散控制轉變為析氫活化控制,拐點2電位即為材料的析氫轉變電位。一般而言,陰極保護電位范圍應在兩個拐點之間。
2.2最正陰極保護電位
本工作以保護度達到90%時的極化電位為最正保護電位。由圖2可知,隨著陰極極化電位的負移,高強鋼的腐蝕速率不斷降低,保護度逐漸增大。高強鋼在自腐蝕狀態下的腐蝕速率為0.2450mm/a;當極化電位負移至-0.85V時,腐蝕速率僅為0.0066mm/a,保護度達到了94.27%,可以認為此時高強鋼得到有效保護。對曲線進行高斯擬合后可以得出:極化電位為-0.76V時,高強鋼的保護度達到90.00%,因此確定高強鋼在海水中的最正陰極保護電位為-0.76V。
圖2 高強鋼腐蝕速率和保護度隨極化電位變化曲線
2.3最負陰極保護電位
2.3.1力學性能分析
由圖3可見,在海水中自腐蝕電位下,高強鋼的延伸率小比在去離子水中的以及-0.75V、-0.80V電位下的。說明在海水中自腐蝕電位下,高強鋼的韌性較低。當極化電位負于-0.80V時,隨著陰極極化電位負移,高強鋼的應變量逐漸降低,反映出材料的脆性增加。在電位為-0.80V和-0.85V時,高強鋼的應力-應變曲線與在去離子水中的較接近。在所試驗的極化電位中,當極化電位負于-0.85V時,材料的應變量開始低于自腐蝕電位下的值,并且從-0.90V電位下開始明顯降低,-0.95V和-1.00V電位下,材料應變量相差不大。
圖3 不同陰極極化電位下高強鋼的應力-應變曲線
由圖4(a)可見,隨極化電位負移,高強鋼的抗拉強度和屈服強度的波動性較小,且三種強度并沒有呈現規律性的變化。
由圖4(b)可見,隨極化電位負移,試樣延伸率先增大后減小,在-0.80~-0.85V,取得最大值后而逐漸減小,斷面收縮率整體呈下降趨勢,當極化電位為-0.90V時,急劇下降至約65.00%,表明材料的韌性降低,脆性逐漸增加。
圖4 不同陰極極化電位下高強鋼力學性能指標變化曲線
(a)最大抗拉強度、屈服強度、斷裂強度;(b)延伸率、斷面收縮率
利用工程上常用的氫脆系數FH來評價高強度船體結構鋼氫脆敏感性。
式中:FH為氫脆系數,為甘油試驗樣品,即材料在惰性介質中的斷面收縮率;為試樣在腐蝕介質中的斷面收縮率。將FH>35%視為斷裂區,即材料在這種環境下必定會發生氫脆破壞;將25%≤FH≤35%視為危險區,即材料在這種環境下會有發生氫脆破壞的潛在危險;將FH≤25%視為安全區,即在這種環境下不會由于氫脆導致材料破壞,為使材料在陰極保護中服役安全,陰極保護電位的施加應確保氫脆系數在25%以內,以此確定最負陰極保護電位。
不同極化電位下高強鋼的氫脆系數的變化曲線如圖5所示。從中可看出:隨極化電位負移,高強鋼的氫脆系數剛開始平穩波動,隨后逐漸增大。在-0.75~-0.85V的電位區間內,高強鋼的氫脆系數變化較小,變化范圍為1.5%~5.1%。材料還處于安全區范圍內,極化電位負于-0.85V以后氫脆系數明顯上升,材料脆性迅速增加。根據不同電位下氫脆系數的點進行高斯曲線擬合,在極化電位負于-0.94V之后氫脆系數已高于25%,材料處于危險區。由此確定高強鋼的最負陰極保護電位應為-0.94V。
圖5 不同極化電位下高強鋼的氫脆系數
2.3.2 斷口形貌分析
由圖6可見,隨著陰極極化電位負移,頸縮現象逐漸減小并趨于消失,反映出脆性增加的特征。在海水中自腐蝕電位下,拉伸試樣斷口有明顯的頸縮現象,斷口呈杯錐形,有韌性斷裂的特征三要素:纖維區、放射區和剪切唇區,掃描電鏡觀察到大量大小不等的韌窩。隨著電位負移,在所加陰極電位為-0.90V時,纖維區仍有部分韌窩,但是并不多見,并且在放射區邊緣出現小面積局部河流花樣、解理單元細小的準解理組織形貌,表明此時材料雖以韌性斷裂為主,但具有一定的脆性斷裂傾向。在-0.95V電位下,宏觀斷口由明顯的杯錐形轉變為與拉伸方向成近似45°角的斷口,且斷口比較平齊、光亮,微觀形貌絕大部分為解理組織、沿晶、穿晶結構或者兩者混合,說明該電位下拉伸斷裂主要為脆性斷裂,氫脆已非常明顯。在-1.00V電位下,斷口的縮頸已不明顯,出現細小撕裂痕,斷口表面出現了大量的沿晶斷裂的特征。
圖6不同陰極極化電位下高強鋼慢拉伸試驗斷口的三維電鏡和SEM照片
(a,b)Ecorr (c,d)-0.75V(e,f)-0.80V (g,h)-0.90V(i,j)-0.95V(k,l)-1.00V
3、結論
模擬深海環境中,陰極極化電位在負于-0.76V時,船用高強鋼保護度達到90%以上,即最正陰極保護電位為-0.76V。
在-0.71V~-0.90V電位區間,高強鋼主要為韌性斷裂;當極化電位負于-0.95V后,斷口開始呈現典型脆性斷裂,高強鋼已進入氫脆的危險區。根據氫脆系數擬合曲線以及氫脆系數在25%進入危險區的判定,在極化電位不超過-0.94V時,船用高強鋼在海水中氫脆系數不超過25%,不具有解理、沿晶等脆性斷裂特征,即-0.94V為高強鋼的最負陰極保護電位。
該船用高強鋼的陰極保護電位區間為-0.76V~-0.94V。
選自《腐蝕與防護》 Vol.37 2016.3
作者:閆永貴,博士,高級工程師,任職于中國船舶重工集團公司
更多關于材料方面、材料腐蝕控制、材料科普等方面的國內外最新動態,我們網站會不斷更新。希望大家一直關注中國腐蝕與防護網http://www.ecorr.org
責任編輯:王元
投稿聯系:編輯部
電話:010-62313558-806
中國腐蝕與防護網官方 QQ群:140808414
免責聲明:本網站所轉載的文字、圖片與視頻資料版權歸原創作者所有,如果涉及侵權,請第一時間聯系本網刪除。
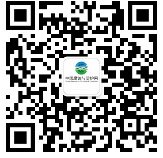
官方微信
《中國腐蝕與防護網電子期刊》征訂啟事
- 投稿聯系:編輯部
- 電話:010-62316606-806
- 郵箱:fsfhzy666@163.com
- 中國腐蝕與防護網官方QQ群:140808414