等離子物理氣相沉積(PS-PVD)技術是結合等離子噴涂與物理氣相沉積技術發展起來的一種新型的薄膜與涂層制備技術。1998 年,瑞士 SulzerMetco公司在低壓等離子噴涂技術的基礎上,提出了低壓等離子噴涂-薄膜技術(lowpressureplasmaspraythinfilm,LPPS-TF),該技術也被稱作超低壓等離子噴涂技術[1] 。與低壓等離子噴涂相比,LPPS-TF的工作壓力更低,約為 0.1~1kPa,等離子射流進一步膨脹變寬,可實現致密金屬或陶瓷薄膜的大面積快速沉積。21 世紀初,LPPS-TF 技術在國際熱噴涂領域引起了廣泛關注。法國貝爾福-蒙博里亞理工大學(UTBM)LERMPS 實驗室與里摩日大學 SPCTS實驗室共同開展了低壓等離子體束流特性方面的研究,探索并確定了采用該噴涂方法可以獲得類似物理氣相沉積金屬及陶瓷涂層的可能性。2005 年,UTBM 組建了超低壓等離子噴涂設備[2] ,使用 Metco公司的單陰極 F4-VB 噴槍,工作壓力低于 100Pa,真空室體積達到 12m3 ,等離子射流長度超過 2m。2010 年,Metco 公司正式提出了等離子物理氣相沉積(PS-PVD)技術的概念,改進后的 PS-PVD 技術采用更高功率等離子噴槍(O3CP 或 MC-100),在大功率(50~100kW)和低氣壓(~200Pa)的工作條件下進行噴涂。
熱障涂層(thermalbarriercoatings,TBCs)是先進航空發動機和地面燃氣輪機研制的關鍵技術,由隔熱性能優良的陶瓷面層和起粘接作用的金屬底層構成,可以避免高溫燃氣與金屬基體直接接觸,對基體形成有效保護,起到延長發動機工作壽命、提高燃燒效率的作用。目前應用最廣泛的熱障涂層制備技術是大氣等離子噴涂(air?plasma?spray,APS)和電子束物理氣相沉積(electronbeamphysicalvapordeposition,EB-PVD)技術[4-7] ,航空發動機制造商使用 APS 和 EB-PVD 技術制備熱障涂層已有30 多年歷史[8] 。APS 工藝具有操作穩定性和經濟可行性,因此在航空發動機中很多靜態部件上的熱障涂層采用 APS 工藝制備,如燃燒室和渦輪盤。在固定式燃氣輪機中,工作葉片也經常通過 APS工藝涂覆[9] 。由于 APS 熱障涂層為層狀結構,熱循環過程中不斷積累的熱應力會導致涂層剝落失效[10] 。與 APS 相比,EB-PVD 熱障涂層具有柱狀結構,可在熱循環過程中釋放應力,其熱循環使用壽命遠遠超過 APS 涂層[11-12] 。同時,EB-PVD 涂層具有更低的表面粗糙度,可有效降低燃氣阻力,有利于保持葉片的空氣動力學性能,主要用于航空發動機的高壓渦輪工作葉片。EB-PVD 技術的局限性在于設備昂貴,沉積效率較低(1~3μm/min),制備的熱障涂層熱導率較高(1.5~1.9W/m·K),隔熱效果不如 APS 涂層[13] 。此外,APS 與 EB-PVD 均為視線沉積工藝,噴涂過程中粒子只能處于直線運動狀態,當基體前面有物體遮擋時,粒子不能繞過阻擋物進行涂層沉積。與 APS 和 EB-PVD 相比,PS-PVD 技術兼具二者的優點,用快速熱噴涂的方法實現了大面積、均勻化的物理氣相沉積[14-15] 。通過改變等離子射流狀態,PS-PVD 還可以實現多相復合涂層的沉積,拓展了不同組織結構熱障涂層的設計與制備。更為重要的是,PS-PVD 的等離子射流具有良好的繞鍍性,可以在外形復雜的工件表面實現非視線熱障涂層沉積[9] 。目前,PS-PVD 熱障涂層技術的報道主要集中在制備工藝及涂層結構等方面,該技術已經成為國際熱噴涂和熱障涂層領域的研究熱點和發展方向。
我國在 PS-PVD 方面研究進展很快。2013 年北京航空航天大學從瑞士 Medicoat 公司引進我國第一臺大功率 PS-PVD 設備,之后,航天材料及工藝研究所、廣東省新材料研究所(原廣州有色金屬研究院)、北京礦冶研究總院、上海硅酸鹽研究所相繼從瑞士 Sulzer?Meltco 公司引進 PS-PVD 設備。廣州有色金屬研究院、西安交通大學、北航等單位在國家 973、國家自然科學基金重大項目等支持下,開展了 PS-PVD 射流特性、噴涂材料與等離子射流交互作用、涂層沉積機理等基礎研究。本文將綜述近年來在 PS-PVD 工藝參數優化、模擬理論計算、涂層結構及沉積機理等方面的研究進展。
1 PS-PVD 的原理與技術特點
PS-PVD 設備主要由等離子噴槍、真空工作室、真空泵、送粉器、中央控制器等部件組成,如圖 1 所示。噴涂過程由中央控制器控制,等離子噴槍、工件及樣品臺均位于超低壓真空密閉室內,真空室與真空泵、過濾除塵系統相連,噴涂時也可以保持一定的真空度。PS-PVD 采用了超低壓的工作環境和高功率高熱焓值的等離子噴槍,等離子氣體流量可以達到 200?SLPM(standardlitersperminute,SLPM),噴涂功率可達到約 100kW,此時等離子射流形態和特性均會發生很大變化。等離子氣體在電極槍內被電弧加熱離解成高能高壓的等離子體,通過噴嘴進入真空室后急劇膨脹形成超音速等離子射流。PS-PVD 技術一般采用槍內送粉的方式,噴涂粉末被直接注入噴槍內的等離子射流中,這樣有利于粉末的加熱熔化和氣化。等離子噴槍一般配有 2 個或 4 個送粉口,可以同時注入單路或多路粉末。同時,PS-PVD 裝配了相關監測裝置,其中原子發射光譜儀用于表征等離子體性質及粉末氣化程度,紅外照相儀及熱電偶監測基體溫度。
PS-PVD 技術還可以進行自凈化表面預處理。通過動控制系統,引弧時將工件基體接電源負極,使電子從工件表面逸出,迅速氣化基體表面殘存的氧化物,起到清潔、凈化基體表面的作用。此外,等離子射流可以對基體材料進行加熱,有效提高涂層與基體的結合力。在工件基體不發生變形和組織變化的情況下,可以允許較高的預熱溫度,這樣可以減小涂層與基體的溫差,減少熱應力產生,避免涂層產生微裂紋。
圖 2 比較了大氣等離子噴涂(APS)、低壓等離子噴涂(LPPS)和等離子物理氣相沉積(PS-PVD)技術過程中的等離子射流狀態。普通真空系統的工作壓力一般為 5~20kPa,等離子射流長度約為50~500mm,射流直徑約為 10~40mm。與之相比,PS-PVD 系統的工作壓力更低(50~200Pa),等離子射流長度超過 2m,直徑可以達到 200~400mm 。等離子體射流區域的擴展使射流橫截面上的顆粒濃度和溫度分布更加均勻,顯著提高了涂層沉積的面積和均勻性。
2 PS-PVD 工藝影響及優化
一般來說,噴涂過程中的工藝參數直接影響噴涂粉末的溫度、速度、熔化和氣化比例等,進而影響涂層組織結構。研究表明,PS-PVD 工藝的主要噴涂參數包括:等離子氣體組成、送粉率、真空度、噴槍功率、基體溫度、噴涂距離、載氣流量等 。
2.1等離子氣體
常用的等離子工作氣體包括氫氣、氬氣、氦氣、氮氣等,組成和比例不同的等離子氣體具有不同的熱焓值和等離子體溫度,顯著影響等離子射流與噴涂粉末的相互作用。Mauer 等研究了等離子氣體種類對等離子射流特性的影響。圖 3 對比了不同氣體組分下 PS-PVD 的等離子射流狀態。當選用純氬氣作為等離子氣體時,等離子射流較窄,溫度較低。在氬氣中添加氫氣后,由于等離子體溫度降低且束流分散,噴涂粉末顆粒的氣化程度降低。而在氬氣中添加氦氣后,由于氦氣具有較好的黏性,等離子射流凝聚,有效提高了噴涂粉末的氣化程度,得到氣相沉積的柱狀結構熱障涂層。不同等離子氣體組分的溫度和焓值如表 1 所示。Ar-He 的熱焓值和溫度較高,分別約為838965J/mol,15550K,而 Ar-H 2 的熱焓值約為733496J/mol,溫度約為 12860K,較 Ar-He 均有明顯下降,說明 Ar-He 是較為匹配 PS-PVD 過程的等離子氣體組成。
Goral 等對 PS-PVD 中工作氣體使用比例對柱狀結構涂層組織形貌的影響進行了研究,結果如圖 4 所示。由圖 4 可以發現,在其他噴涂條件一定時,提高等離子氣體氬氣比率(Ar/He 比率從1∶1 增加到 2∶1)后,涂層中出現固相顆粒,說明增大氬氣含量不利于噴涂粉末的熔化及氣化。
郭洪波等采用理論模擬計算研究和揭示了PS-PVD 過程中不同條件下等離子射流的特性、噴涂粉末與等離子射流間的交互作用機制 。結果表明:粒子能量及涂層結構在極大程度上取決于等離子槍內部等離子體的特性;通過對 30Ar/60He,45Ar/45He 和 60Ar/30He 三種等離子氣體組成進行計算發現,等離子體組成為 45Ar/45He 時,在等離子噴槍內部轉移給噴涂粉末的熱焓值最高(約為9828kJ/kg),與 30Ar/60He 氣體組成相差不大,但明顯高于 60Ar/30He,如圖 5 所示。因而使用Ar/He 比例為 1:1 的等離子氣體獲得的涂層結構和性能值得進一步研究。
2.2噴涂粉末
噴涂粉末對 PS-PVD 過程的影響主要包括粉末本身特性及送粉率兩方面。PS-PVD 技術對噴涂粉末的要求高于 APS,需要粉末具有良好的流動性和較低的尺寸。郭洪波等計算得到了不同噴涂功率下完全氣化 YSZ 粉末時所需要的粉末顆粒尺寸,結果如圖 6 所示。當噴涂功率為 50?kW 時,只有直徑小于 0.65?μm 顆粒可以完全氣化,而當噴涂功率達到 60kW 時,直徑小于 1.5μm 的粉末顆粒可以被完全氣化。這一方面表明適當增加噴涂功率有利于粉末的氣化,另一方面說明粉末的尺寸直接影響其熔化和氣化過程。
Mauer 等利用原子發射光譜檢測了 PS-PVD沉積過程中不同送粉率條件下粉末的氣化程度。研究發現,當送粉率較小時(<2g/min),射流中的粉末可以被充分氣化,制備得到純氣相沉積的柱狀晶結構組織;增大送粉率時(5~20g/min),由于噴涂粉末氣化需要的能量增加,粉末不能被完全氣化,射流中氣相原子、液相以及固相顆粒共同存在,在基體上沉積后得到層狀和柱狀混合結構涂層。因此,送粉率的大小直接影響了噴涂粉末在射流中的狀態,進而影響了涂層的組織結構。
2.3真空度
PS-PVD 過程中的真空度對熱障涂層形貌也有重要影響,由圖 7 可知,當真空度約為 5000Pa 時,形成的是比較致密的層狀結構;當真空度為500~5000Pa 時,沉積得到的是層狀結構涂層;只有當真空度小于 300Pa,才可能形成柱狀晶結構。因此,大多數研究的真空度都控制在 100~200Pa。Goral 等對 PS-PVD 中工作氣壓對柱狀晶涂層組織形貌的影響也進行了研究 。結果發現,當工作氣壓從約 150Pa 增加到約 200Pa 時,噴涂顆粒的氣化程度減弱,涂層中存在固相顆粒,說明較低的工作氣壓有利于柱狀晶結構的形成。
2.4 噴涂功率
噴涂功率直接影響等離子射流的溫度、熱焓值和速度。噴涂功率越大,等離子射流溫度越高,對粉末熔化/氣化有顯著影響。郭洪波等對 30Ar/60He等離子氣體在不同功率條件下的動量和熱量轉換進行了理論模擬和計算研究 ,發現轉移到粉末上的能量和涂層形貌在很大程度上受等離子氣體特性和噴槍內粉末動力學的影響。隨著噴涂功率從50kW 增加到 60kW,等離子體氣體的熱量增加,但粉末速度沒有明顯的變化,此時粉末可以吸收更多熱量。當功率從 60kW 增加到 70kW 時,等離子氣體的總熱量依然增加,但粉末顆粒的速度也顯著增大,由此導致其在噴槍內停留的時間迅速減少,繼而使粉末所利用的有效熱量減少。選取直徑為 1μm 的 YSZ 粉末計算原料吸收的熱量百分比,結果如圖 8 所示。起初粉末顆粒吸收的有效功率隨噴槍凈功率的增加而增加,最高時約為 64kW,此時被原料粉末吸收的等離子體能量占比最高,約為3.4%。進一步增加功率則會降低等離子體和粉末之間的熱傳遞。此外,功率過大不僅對等離子噴槍負載過大,容易燒蝕噴槍內的陰極,降低噴槍使用壽命,還有可能燒損噴涂粉末,影響涂層成分和性能。
2.5噴涂距離和載氣流量
一般將噴槍的噴嘴端面到基體表面的直線距離定義為噴涂距離。噴涂距離不同導致射流狀態存在明顯差異。在傳統 APS 工藝中,隨著噴涂距離的增加,等離子射流的溫度、熱焓值及射流中的粒子溫度均呈下降趨勢。在 LPPS 噴涂過程中,等離子射流在噴嘴出口附近處溫度最高,可以達到約 10950K。隨著噴涂距離的增加,等離子射流的溫度不斷降低,射流的速度則先增加后降低,距離噴嘴出口約 25mm 處速度最大,約為 2024m/s 。而在 PS-PVD 工藝中,等離子束流的壓力、溫度、導熱率及速度在很大程度上受超低壓工作環境的影響,在噴涂軸向方向上與超音速流動相似,出現了連續的收縮和擴張區域。郭洪波等采用 PS-PVD在不同噴涂距離上制備了 YSZ 陶瓷涂層,研究了沿等離子射流軸向和徑向方向上涂層的微觀組織結構變化,建立了 PS-PVD 涂層微觀結構空間演變模型。研究顯示,隨著噴涂距離的增加,等離子射流中心處的粒子先后經歷了液相(含少量氣相和固相)、氣/液混合相(含少量固相)、氣相(含少量未熔化固相顆粒)、純氣相以及氣相(含冷凝固相顆粒)這幾種狀態的改變,在基體表面沉積后依次形成了致密層狀結構、層狀柱狀混合結構、準柱狀結構(含未熔化顆粒)、純氣相柱狀結構、準柱狀結構(含冷凝納米顆粒)結構的涂層。
載氣是指在噴涂過程中將粉末運輸到等離子射流內部的氣體,通常為氬氣,而載氣流量和噴涂距離對柱狀結構熱障涂層的形成有交互作用 。噴涂時選取的載氣流量不同會導致射流內部固相、液相和氣相的含量變化。圖 9 為 YSZ 粉末在噴涂過程中的飛行軌跡模型。使用較低的載氣流量(5~8L/min)時,固相顆粒和液相不能在一定距離內被送出等離子焰流,因而與氣相原子共同沉積在基體表面,形成致密的層狀或緊密填充的混合結構。提高載氣流量(>10L/min)后,大部分固相顆粒和液相在飛行過程中離開等離子束流,而氣相原子可以隨射流飛行很遠,并在基體表面進行沉積,從而得到氣相含量較高的柱狀結構涂層。因次,通過選取合適的載氣與噴涂距離,可以對 PS-PVD 涂層的微觀結構進行調控。
3 PS-PVD 熱障涂層的結構及沉積原理
目前,國內外通過 PS-PVD 工藝制備得到的YSZ 陶瓷涂層主要有四種結構,分別是致密層狀結構、層狀與柱狀混合結構、準柱狀結構及純氣相柱狀結構,這是由于沉積到基體表面的固相、液相和氣相組成及比例不同造成的 。不同結構 YSZ 涂層的斷口形貌如圖 10 所示。
郭洪波等通過 PS-PVD 短時噴涂方法及沉積物形貌特征分析對以上四種涂層的沉積機理進行了研究。致密結構涂層主要由完全熔化的液滴鋪展堆積而成,如圖 11 所示。此時,到達基體表面的 YSZ 主要以液相存在,還存在少量氣相原子和固相顆粒。液滴隨等離子束流高速飛行撞擊到基體表面后發生鋪展,形成盤狀的薄層并凝固,隨后到來的液滴再次發生撞擊鋪展,最終形成致密層狀涂層。同時,少量的固相顆粒沉積到基體表面,形成的凸起會導致涂層中出現空洞和缺陷。而少量氣相粒子則凝結在片層結構表面或者填充片層間隙,有利于提高涂層致密性。
混合結構熱障涂層主要由氣相和液相沉積而成,如圖 12 所示。其中,熔化的液滴撞擊在基體上形成片層狀組織;氣相原子到達基體表面時吸附在基體或片層組織表面并沿表面發生擴散、形核。當有連續氣相原子沉積時,原子團核以三維島狀模式生長,形成柱狀結構。大量液滴沉積不僅會打斷柱狀晶的生長,還會填入柱狀晶的間隙,顯著降低了涂層的孔隙率,使涂層較為致密。
準柱狀結構涂層的沉積機理如圖 13 所示。可以發現,準柱狀結構涂層主要由氣相原子沉積而成,因而具有明顯的柱狀結構;同時,部分微米級固體顆粒沉積導致準柱狀涂層具有“楔形”特征結構。這種楔形結構是由于氣相粒子直接在顆粒表面形核和生長得到的。微米級固相顆粒撞擊基體或涂層表面,會終止原有“楔形”結構上氣相原子的沉積。納米小顆粒和液滴也會沉積在柱狀晶內部和間隙中,但對準柱狀結構沒有明顯影響。
純柱狀結構涂層完全由氣相原子沉積而成,沉積機理如圖 14 所示。氣相原子和原子團簇隨等離子束流到達基板表面后,通過三維島狀生長模式生長成柱狀晶。在形核生長過程中,吸附粒子首先結合形成小原子團,當原子團達到或超過臨界尺寸后,原子團則會穩定存在并長大成為島狀結構。隨著島狀結構不斷長大,島之間的間距相應減小,最終相鄰的小島合并成為一個大島,聯并之后的大島將沿垂直于基體方向不斷生長,最終形成連續涂層。在 PS-PVD 中,柱狀晶的形核和島狀結構生長與 EB-PVD 相近。不同之處在于,EB-PVD 中氣相原子具有很好的擴散能力,當其到達柱狀晶表面時很難形核,而是在原有的柱狀晶上生長。因此,EB-PVD 沉積的柱狀晶通常形狀規則、排列整齊,呈現明顯的晶體學平面。而在 PS-PVD 中,氣相粒子本身具有較高的速度,加之等離子射流有一定黏滯力,導致氣相粒子很難在涂層表面發生擴散。這時,氣相粒子通常在原有柱狀晶上重新形核并長大成為新的柱狀晶。因此,PS-PVD 純柱狀結構涂層的柱狀晶較為粗大而且沒有擇優取向。
4 總結與展望
PS-PVD 技術代表了未來高性能熱障涂層制備技術的發展方向。PS-PVD 工藝在熱障涂層復合結構調控、大面積高效率沉積、多聯體復雜型面涂層均勻涂覆等方面都展現了巨大的技術優勢,有望在新一代超高溫、高隔熱、長壽命熱障涂層研制方面發揮關鍵作用。目前在 PS-PVD 熱障涂層基礎研究方面已經取得顯著進展,但尚未獲得工程應用。PS-PVD 技術未來的研究方向主要有:(1)超高溫高隔熱熱障涂層研究;(2)長壽命熱障涂層研究;(3)陶瓷基復合材料環境障涂層研究;(4)大面積致密透氧膜和固態燃料電池電極膜等。
更多關于材料方面、材料腐蝕控制、材料科普等方面的國內外最新動態,我們網站會不斷更新。希望大家一直關注中國腐蝕與防護網http://www.ecorr.org
責任編輯:殷鵬飛
《中國腐蝕與防護網電子期刊》征訂啟事
投稿聯系:編輯部
電話:010-62313558-806
郵箱:fsfhzy666@163.com
中國腐蝕與防護網官方 QQ群:140808414
免責聲明:本網站所轉載的文字、圖片與視頻資料版權歸原創作者所有,如果涉及侵權,請第一時間聯系本網刪除。
-
標簽: 等離子物理氣相沉積(PS-PVD), 熱障涂層, 工藝, 沉積機理
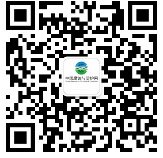
官方微信
《中國腐蝕與防護網電子期刊》征訂啟事
- 投稿聯系:編輯部
- 電話:010-62313558-806
- 郵箱:fsfhzy666@163.com
- 中國腐蝕與防護網官方QQ群:140808414