摘要:采用FEMFAT疲勞仿真軟件,結合曲軸材料、表面加工工藝、應力循環特征等各方面因素,綜合分析后得出曲軸的疲勞壽命及安全系數。應用曲軸疲勞試驗機,通過升降法獲取6對有效數據分析曲軸的疲勞極限和安全系數。對比仿真與臺架試驗計算數據及結果,找尋曲軸發生應力集中的部位,對仿真及試驗結果進行安全系數評估,分析影響曲軸壽命的因素,最終得出2種試驗方法所得試驗結果均滿足安全要求。
關鍵詞:曲軸 疲勞 安全系數
1 疲勞研究方法
在工程機械零件的疲勞壽命預測及分析的研究中最為經典的方法是S-N、e-N疲勞裂紋擴展壽命法。通過高周疲勞分析法得到的材料S-N曲線,通常在試驗中用一組標準試件,對其施加不同的應力幅,測出試件斷裂時的循環數N,然后以應力σ縱坐標,N為橫坐標,得出S-N曲線。
一條完整的S-N曲線,被劃分為低循環疲勞段(LCF),宏觀屈服,非線性段;高循環疲勞段(HCF),線性段,N=10E4~10E6;疲勞極限段(SF),N>10E7,這樣三個疲勞階段。
而對于S-N曲線進行修正時,主要需要考慮理論應力集中系數、尺寸系數、表面精度、加載方式4個方面的影響因素。
2 曲軸疲勞分析
2.1 參數設置
試驗及仿真所用曲軸材料為42CrMo4,在FEMFAT軟件中載入曲軸的應力分析結果并設置曲軸的材料屬性,定義曲軸模型當前節點組的表面粗糙度,離散度和溫度場,曲軸表面采用感應淬火加工工藝等重要參數。在影響參數設置界面,勾選應力梯度、滲碳、感應硬化和鍛造選項。疲勞分析參數中選擇耐久安全系數,定義全局參數,定義存活率,等效應力等。
2.2 曲軸疲勞分析結果
曲軸的強度很大程度上決定了發動機的使用壽命及其可靠性,因此對曲軸的安全可靠性提出了很高的要求。如圖1所示,若設xq0是曲軸的理論設計強度。xy0是曲軸的理論工作應力,曲軸的安全系數為n=xq0/xq0>1,理論上不應該發生破壞。而實際工作應力和零件強度都呈現正態分布,因此存在一個概率曲線與強度概率曲線相重疊的區域,如果零件的強度和工作應力都落在這個區域,就會發生破壞。這個區域的大小,就是可靠性中零件發生破壞的概率。
圖1 應力強度干涉模型
運用FEMFAT軟件將曲軸動力學分析結果進行了疲勞計算,其中包含各節點疲勞安全系數、疲勞壽命、損傷結果以及破壞程度較大節點應力循環等,基于這些結果對曲軸進行全壽命評價。
通過對曲軸材料、加工工藝等方面的參數設置后,分析得出曲軸的各部位的安全系數,如圖2所示,為曲軸在額定轉速下,曲軸的最小疲勞安全系數出現在第八曲柄臂主軸頸圓角處,在存活率為99.9%時,曲軸全工況下,與連桿所連接軸頸處的最小安全系數為2.218,查找許用安全系數為1.3~1.5,說明曲軸滿足疲勞計算要求。
圖2 最小安全系數
計算得出最小疲勞壽命為1.339 28E×1010個工作循環,所在節點為36 384。折合曲軸的運轉時間約10年以上。而在現實生活中,汽車大多數情況下行駛時間不會超過10 h,且在行駛過程中車速也會隨行駛路況發生快慢變化,因此這個運轉時間一定程度上滿足曲軸使用強度需要。
3 曲軸疲勞試驗研究
3.1 疲勞試驗機工作原理
依托仿真軟件進行曲軸疲勞模擬試驗,得出曲軸的最小疲勞壽命及安全系數。但與曲軸實際工況仍存在些許差距,一般可以通過臺架試驗,與仿真分析結果做以對比,以使試驗結果更加可靠。
據統計,由于疲勞引起的汽車零部件損壞占比80%。ZQP-6000型曲軸疲勞試驗機是由函數發生器發出指定頻率和指定幅度的正弦波,驅動功率放大器使激振器產生振動波形,機械諧振系統隨之產生振動,調整函數發生器發出的頻率至系統的共振頻率,即進入正常的工作狀態。根據共振頻率下降的情況測試并觀察曲軸試件在拉、壓或拉壓、交變載荷下的疲勞特性。其試驗結果用于曲軸優化設計、變更加工工藝、鑒定貨源、產品質量抽檢等。試驗臺結構如圖3所示,表1為試驗機主要技術指標。
圖3 試驗臺結構圖
表1 試驗臺主要技術參數
3.2 曲軸疲勞試驗結果
通過曲軸疲勞試驗,能夠為曲軸的設計、結構優化等方面提供可靠的研究數據。對各種材料、加工工藝的曲軸進行多次反復試驗,總結分析試驗結果,這些結果能夠為曲軸的結構優化、加工工藝以及表面粗糙度的調整等方面起到指導作用。
根據QC/T 637—2000《汽車發動機曲軸彎曲疲勞試驗方法》,循環基數取107次,通過升降法測定曲軸的疲勞極限和安全系數。
進行試驗時,彎矩增量ΔM小于5%,試驗在四到五級應力水平下進行。圖4為試驗結束后的結果升降,圖中圓點代表試驗結果越出,十字標記代表試驗結構未達到循環基數,試件發生疲勞損傷,根據升降圖取6對有效數據。
圖4 結果升降
通過計算承載彎矩疲勞極限為M-1(50%)=1 479.17 N·m,標準差為Sn-1=58.07 N·m,變異系數Y=0.039,置信度為95%,相對誤差≤5%時,試驗結果滿足零件加工精度要求,M-1(99.9%)=1 344.59 N·m。計算曲軸名義彎矩為M-1=787.73N·m,安全系數為n(99.9%)=1.707
將試驗得出的安全系數與有限元仿真得出的安全系數做以比較,略低于FEMFAT疲勞分析結果,n>1.3~1.5,證明曲軸滿足工作需求。
4 影響曲軸壽命的因素
導致曲軸失效的最常見形式是疲勞損壞。通過實驗及仿真分析后可知,曲軸在正常工作條件下所能承受交變負荷的循環次數能夠得到曲軸的疲勞壽命,疲勞壽命一般包括曲軸的裂紋萌生壽命和裂紋擴展壽命2個階段。
曲軸所產生的裂紋一般出現在曲柄臂與連桿軸頸的過渡圓角處,這種裂紋是由于曲軸發生了扭轉疲勞所引起的,一旦曲軸出現裂紋,隨之而來的是裂紋快速發展成的界面斷裂。而導致曲軸產生裂紋的原因,主要是由于曲軸的自身材料有缺陷,剛度強度未達到生產要求;或者在曲軸的設計階段,曲軸主軸頸、連桿軸頸和曲柄臂等部位的尺寸及受力分析存在誤差;甚至在加工過程中,由于加工工藝的不完善導致曲軸某部位出現嚴重的應力集中現象,以上這些都是在曲軸的設計及生產過程中導致其出現裂紋的幾點原因。當曲軸被安裝在發動機中時,在運行過程中,由于發動機爆缸導致曲軸受載過高,氣缸內出現拉缸現象,導致曲軸連桿軸頸磨損嚴重,且受力不均,致使曲軸出現裂紋。而曲軸在工作過程中產生的不平衡振動導致曲軸受力不均的現象是無法避免的,甚至由此出現扭轉共振現象而導致曲軸受到額外的扭轉應力,進而產生了裂紋。
曲軸自身所受應力值在遠低于曲軸材料抗拉強度的情況下也會發生疲勞破壞,而且疲勞破壞在零件斷裂前基本上是沒有征兆的,會發生突然斷裂,這是一種極具危險的失效形式。
5 結束語
利用FEMFAT軟件計算,分析曲軸在額定轉速下,曲軸的主軸頸和連桿軸頸上最小安全系數為2.218,查找許用安全系數為1.3~1.5,說明曲軸滿足疲勞計算要求。
依據QC/T 637—2000,曲軸疲勞試驗所得曲軸部件安全系數為1.707滿足設計需要。
仿真分析方法日趨成熟,但其結果與實際臺架實驗仍存有一定差距,本文通過對比仿真分析結果及臺架試驗結果,證明仿真分析能夠快速的分析出試件的疲勞結果,與實際臺架實驗結果具有較好的一致性,都滿足設計與工作所需條件。仿真及試驗結果也可作為零件突發斷裂時,快速分析原因及優化設計的重要手段,若需要更為精確的分析結果,還需通過臺架試驗做以對比分析。
免責聲明:本網站所轉載的文字、圖片與視頻資料版權歸原創作者所有,如果涉及侵權,請第一時間聯系本網刪除。
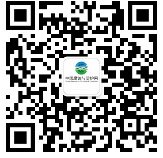
官方微信
《中國腐蝕與防護網電子期刊》征訂啟事
- 投稿聯系:編輯部
- 電話:010-62316606-806
- 郵箱:fsfhzy666@163.com
- 中國腐蝕與防護網官方QQ群:140808414