CO2/H2S引起的碳鋼腐蝕是油氣田行業中常見的腐蝕類型,由其引發的事故屢見不鮮。抑制CO2/H2S腐蝕的方法有很多,其中加注緩蝕劑是一種操作簡單、經濟有效的腐蝕防護手段,目前已得到廣泛應用。單一的緩蝕劑在實際應用中一般無法滿足設備設施的防腐需求,此時可利用兩種或多種緩蝕劑間的協同效應來制備復合緩蝕劑,在降低成本的同時提高了緩蝕劑的性能[1]。
雖然緩蝕協同效應相關研究已取得長足進展,產生了包括架橋理論[2,3,4,5,6,7]、補強理論[8,9]、協同吸附理論[10,11]等在內的緩蝕協同效應理論,但整體來說,協同效應的研究多數還集中在無機酸性體系 (如HCl,H2SO4,H3PO4)[1,6,7,12,13,14,15]或CO2腐蝕體系[8,11],在CO2/H2S共存的鹽水溶液中,相關報道較少。
此外,之前對協同效應的研究往往依賴于大量的實體實驗,如失重法、電化學測試、表面分析等,這些方法只能在宏觀上研究緩蝕劑間的協同效應,較難從微觀上解釋協同機理,且實驗過程缺乏一定的理論指導。分子模擬技術目前已成為研究微觀機理的有效手段,并已被眾多學者用來評估緩蝕劑的性能[16,17,18,19,20,21,22,23]。本課題組首次將分子模擬技術應用于緩蝕協同效應的研究,并取得一定進展[24],但這方面的報道依然較少。
本文采用分子模擬技術研究了IAS與3種陽離子表面活性劑間的緩蝕協同效應,發現IAS與DTAB和TTAB間可能存在協同效應;進而通過靜態失重、極化曲線、XPS等方法對緩蝕劑間的協同效應進行驗證,并探討了緩蝕協同機理。此外,本文的研究成果證明了課題組在文獻[24]中提出的方法在一定程度上可以預測緩蝕劑間協同效應,有繼續深入研究的價值。
1 實驗方法
1.1 實驗材料
實驗中所用腐蝕試片為Q235鋼,化學成分 (質量分數,%) 為:C 0.12-0.20,Si 0.10-0.25,Mn 0.30~0.70,P<0.045,S<0.045,Cu<0.15,Al<0.020,Fe余量。實驗前將鋼片切割成50×10×3 mm用于失重實驗,10 mm×10 mm×3 mm用于電化學測試,5 mm×5 mm×2 mm用于XPS測試,用砂紙逐級打磨至2000#后,去污粉清洗,丙酮去脂,乙醇脫水,熱風吹干后備用。
實驗介質為3.5% (質量分數) NaCl溶液,實驗前通1 h N2除氧,除氧結束后繼續向溶液中通CO2/H2S混合氣體 (20:20 mL/min) 1 h,制備腐蝕溶液,60 ℃時腐蝕溶液的pH值約為4.1。咪唑啉季銨鹽 (IAS) 由北京龍飛恒信科技有限公司提供,純度為95%;3種陽離子表面活性劑分別是十二烷基三甲基溴化銨 (DTAB)、十四烷基三甲基溴化銨 (TTAB) 和十六烷基三甲基溴化銨 (CTAB),均為分析純。IAS與3種陽離子表面活性劑的分子結構如圖1。
圖1 IAS與3種陽離子表面活性劑的分子結構式
1.2 分子模擬
采用Material Studio中的Discover模塊構建用于計算自由體積分數 (FFV) 的緩蝕劑膜模型并進行分子動力學模擬。模型包含一種或兩種緩蝕劑分子 (分子總個數為50)。計算過程中先進行500 ps的NPT模擬用以計算緩蝕劑膜層的真實密度;之后用所得密度重新構建模型,并進行1000 ps的NVT模擬,NVT模擬后的終態結構用于計算膜層FFV值。模擬過程采用Compass力場;溫度為333 K (采用Andersen恒溫器控制);壓力為1.01×105 Pa (采用Berendsen恒壓器控制);長程Coulomb力及van der Waals作用力分別采用Ewald和Atom Based,截斷半徑為1.25 nm。詳盡的模型構建及模擬過程可參見本課題組前期工作[24]。FFV的計算公式如下:
其中,Vfree為腐蝕粒子能夠進入的所有孔洞的體積;除Vfree外,剩余的體積為Voccupy。
1.3 靜態失重法
將稱重后3個相同的試片置于700 mL腐蝕溶液中,用704室溫固化硅橡膠封閉瓶口,并在60 ℃恒溫水浴鍋中保溫。72 h后,取出的試片先浸泡在酸洗液 (15%鹽酸+1%酸洗緩蝕劑) 中5 min,并用去污粉清洗,乙醇脫水,熱風吹干后稱重。
1.4 動電位極化曲線測試
在Gamry interface 1000電化學工作站上進行電化學測試,采用傳統的三電極體系,參比電極和輔助電極分別為飽和甘汞電極 (SCE) 和Pt電極。測試前,需將工作電極浸泡在200 mL腐蝕溶液中1 h,使電極達到穩定狀態。測試過程中,電位掃描范圍為-200~+200 mV,掃描速率0.167 mV·s-1。采用弱極化區三參數法對極化曲線進行擬合,得到腐蝕電流密度 (Icorr) 等電化學參數進行擬合,緩蝕率 (ηp) 可由下式計算:
其中,Icorr與Icorr (int) 分別為溶液中不含有和含有緩蝕劑時的自腐蝕電流密度值。
1.5 XPS測試
樣品制備過程與失重實驗相同。試樣從腐蝕溶液中取出后,直接熱風吹干,置于干燥器中備用。采用PHI-5300 ESCA光電子能譜儀 (XPS) 進行能譜分析,掃描范圍為0~1255 eV,步長1 eV,高分辨窄譜的掃描范圍與所測元素有關,步長為0.05 eV。XPS數據采用XPSPEAK軟件進行擬合分析,分析過程中以C在284.6 eV處的結合能校準其它結合能。
2 實驗結果
2.1 分子動力學模擬
有機緩蝕劑通常會自發地吸附在金屬表面來達到抑制金屬腐蝕的目的。雖然緩蝕劑膜層可以有效防止腐蝕介質向金屬基體表面擴散,但腐蝕介質依然可以通過緩蝕劑膜中較大的孔洞[19],且孔洞越大,腐蝕粒子的擴散速度就會越快。因此,緩蝕劑膜中孔洞的尺寸直接影響了緩蝕劑的性能。本課題組在分子動力學模擬研究中發現[24],兩種緩蝕劑復配后對FFV值的降低程度與二者間的緩蝕協同效應強度存在相關性。依據這一研究成果,本節以H2O、H3O+、HCO3-、Cl-和HS-為探針,計算了IAS與3種表面活性劑按一定質量濃度比 (1∶0,1∶0.1,1∶0.2,1∶0.3,1∶0.4,1∶0.5,1∶0.7,1∶0.8,1∶1,1∶1.5,1∶2,1∶5,1∶8和0∶1) 復配后的緩蝕劑膜的FFV值,見圖2。可以看出,隨著探針直徑的增大,各緩蝕劑膜的FFV值也相應減小,但無論使用何種探針,曲線的形狀均一致。
圖2 以H2O、H3O+、Cl-、HCO3-或HS-為探針時不同復合緩蝕劑膜層的FFV值隨c%IAS的變化曲線
對圖2a中3種復配體系的FFV計算結果進行分析可以看出,與表面活性劑相比,IAS單獨成膜時,緩蝕劑膜的FFV值更小,為7.95%;當3種表面活性劑分別以不同比例與IAS混合時,復合緩蝕劑膜層的FFV值出現了不同程度的變化:(1) 對于IAS+DTAB體系來說,當IAS的質量濃度在復合緩蝕劑中的占比 (c%IAS) 在65%附近時,部分曲線在虛線下方,說明膜層的FFV值在這一區域內低于7.95%,也就是說,IAS與DTAB復合使用,可以顯著增加膜層致密性,二者間可能存在較好的緩蝕協同效應;(2) 對于IAS+TTAB體系,當c%IAS在60 %附近時,有少部分曲線處于虛線下方,說明IAS與TTAB間也可能存在緩蝕協同效應,但協同強度小于IAS+DTAB體系;(3) 當IAS與CTAB復合使用時,曲線全部處于虛線上方,說明二者間可能存在拮抗效應。
總之,根據分子動力學模擬計算結果,推測IAS與DTAB、TTAB間存在協同效應,與CTAB間存在拮抗效應;協同效應強度的排序為DTAB+IAS> TTAB+IAS>CTAB+IAS。
2.2 失重實驗結果
本節采用失重法對分子動力學模擬的推測結果進行驗證。表1為靜態失重法實驗結果。從表中可以看出,與3種表面活性劑相比,IAS對碳鋼的緩蝕效果更好。當3種表面活性劑分別與IAS復配時,復合緩蝕劑的性能排序為IAS+DTAB>IAS+TTAB>IAS+CTAB。此外,5 mg/L IAS+5 mg/L DTAB和5 mg/L IAS+5 mg/L TTAB的復配組合,復合緩蝕劑的緩蝕率明顯大于分別使用5 mg/L單一緩蝕劑所得緩蝕率的和,即1+1>2,說明這兩種復配體系具有較好的緩蝕協同效應。根據公式 (3) 可計算得到不同復配體系的S值,用以表明緩蝕劑間的協同效應強度。
表1 不同緩蝕劑在含CO2/H2S鹽水中對Q235鋼的緩蝕效果
其中,ηA和ηB分別表示A與B各自單獨使用時測得的緩蝕率;ηAB表示A與B混合使用時測得的緩蝕率。若S值大于1,表明存在協同效應,S值越大,協同效應越明顯。S值的計算結果列于表2中,可以看出,IAS與DTAB、TTAB間存在較好的緩蝕協同效應,與CTAB間存在拮抗效應;3種體系緩蝕協同效應強度的排序為IAS+DTAB>IAS+TTAB>IAS+CTAB。失重實驗與分子動力學模擬所得結論完全一致,說明考察不同緩蝕劑復合后對緩蝕劑膜FFV值的降低程度,可以在一定程度上預測緩蝕劑間的協同效應。當然,該方法的適用性還需要通過更多的研究進行驗證。
2.3 動電位極化曲線測試
極化曲線實驗主要是對失重結果的驗證。圖3為Q235鋼在含有不同緩蝕劑的CO2/H2S共存鹽水溶液中測得的極化曲線。從圖中可以看出,緩蝕劑的加入對碳鋼陽極溶解和陰極反應均有一定的影響,曲線均有向左上方移動的趨勢。當IAS與DTAB及TTAB復配使用時,腐蝕電位明顯向正方向移動,而IAS與CTAB復配時,腐蝕電位略微正移。無論怎樣,腐蝕電位的偏移程度均未超過85 mV,說明這些復合緩蝕劑均是以抑制陽極為主的混合型緩蝕劑[25,26]。
圖3 Q235鋼在含有不同緩蝕劑的CO2/H2S共存鹽水溶液中測得的極化曲線
表2為對極化曲線進行擬合后得到的電化學參數,可以看出,IAS與DTAB或TTAB形成的復合緩蝕劑可有效抑制碳鋼在CO2/H2S溶液中的腐蝕,而IAS與CTAB復配形成的緩蝕劑緩蝕性能較弱。極化曲線與失重實驗所得結論保持一致。
表2 通過擬合Q235鋼在含有不同緩蝕劑的CO2/H2S共存鹽水溶液中測得的極化曲線得到的電化學參數
2.4 XPS測試結果
為了進一步研究IAS與3種表面活性劑間的緩蝕協同效應,本節采用XPS技術對帶有緩蝕劑膜的鋼片試樣進行檢測分析。圖4為添加不同緩蝕劑時測得的緩蝕劑膜的XPS全譜。從圖中可以明顯地觀察到F2p、O1s、N1s、C1s、和S2p峰的存在。C1s和N1s主要來源于吸附在碳鋼表面的IAS和表面活性劑分子。O1s和S2p來自于鐵的氧化物、碳氧化物和硫化物。Fe2p則歸因于鐵基體和它的腐蝕產物。
圖4 Q235鋼在含有不同緩蝕劑的CO2/H2S共存鹽水溶液中浸泡24 h后測得的XPS全譜
圖5為IAS與3種表面活性劑形成的緩蝕劑膜的N1s窄譜。圖5中的譜圖均可分解為位于402.3和399.8 eV處的兩個峰。402.3 eV處的峰源于表面活性劑中的—N+(CH3)3及IAS中季銨化后的N原子[27,28],這些N原子周圍均帶有一個正電荷,因此下文中將402.3 eV處的峰簡稱為N+峰;而399.8 eV處的峰則歸屬于IAS中的C—N=C[29]。
圖5 Q235鋼在含有不同緩蝕劑的CO2/H2S共存鹽水溶液中浸泡24 h后測得的N1s高分辨窄譜
通過對N1s高分辨窄譜的擬合,可以得到N+及C—N=C峰的面積及N+峰面積的占比,見表3。可以看出,IAS與DTAB復配使用時,N+峰面積的占比最大,說明緩蝕劑膜層中含表面活性劑 (DTAB) 的含量最多,證明了IAS與DTAB可以較好的共吸附在碳鋼表面。N+峰面積的占比排序為IAS+DTAB>IAS+TTAB>IAS+CTAB,與緩蝕劑間協同效應強度排序一致。
表3 通過分析Q235鋼在含有不同緩蝕劑的CO2/H2S共存鹽水溶液中浸泡24 h后測得的N1s高分辨窄譜得到的參數
3 緩蝕協同機理分析
從表3可知,IAS與3種表面活性劑復配時,碳鋼表面IAS的含量明顯多于表面活性劑,而IAS的緩蝕性能卻好于表面活性劑,說明復合緩蝕劑中,起主要緩蝕作用的物質可能為IAS,而表面活性劑則起到填補緩蝕劑膜層缺陷的作用。此外,雖然3種表面活性劑緩蝕性能的排序為CTAB>TTAB>DTAB,但與IAS復配后,協同效應強度的排序卻為IAS+DTAB>IAS+TTAB>IAS+CTAB,說明協同作用的強度可能與表面活性劑本身的性能差異無關,而與緩蝕劑膜層的致密程度有關。
結合上述分析繪制圖6,可以較形象的闡明IAS與3種表面活性劑間的協同作用機理。IAS單獨使用時,緩蝕劑膜層存在大量的缺陷 (圖6a);當IAS與DTAB復配使用時 (圖6b),由于DTAB分子的空間位阻相對較小,其可以較充分的填充IAS膜層的缺陷,使得復合緩蝕劑的膜層更加致密;當IAS與TTAB復配使用時 (圖6c),TTAB分子的空間位阻比DTAB大,其填充缺陷的能力有限,使復合緩蝕劑膜層產生較大孔隙,導致TTAB與IAS間的協同作用程度較小;而當IAS與CTAB復配時 (圖6d),由于CTAB分子的空間位阻較大,其無法填補IAS膜層的缺陷,因此IAS與CTAB間不存在緩蝕協同效應。此外,CTAB的緩蝕性能相對較好,其與IAS間可能還存在著競爭吸附,這也可能是導致二者間產生拮抗效應的原因。
圖6 CO2/H2S共存鹽水溶液中IAS與3種表面活性劑在碳鋼表面的成膜機理示意圖
4 結論
(1) 在3種緩蝕劑復配體系中,復合緩蝕劑膜FFV值的降低程度與緩蝕協同效應強度間具有一定的相關性,所得結論與課題組前期研究成果保持一致。
(2) IAS可有效抑制Q235鋼在含CO2/H2S鹽水溶液中的腐蝕;IAS與DTAB間存在較好的緩蝕協同效應,與TTAB間的協同作用較弱,而與CTAB間存在明顯的拮抗作用。
(3) IAS與3種表面活性劑形成的復合緩蝕劑均屬于以抑制陽極為主的混合型緩蝕劑。
(4) IAS與3種表面活性劑復配使用時,起主要緩蝕作用的物質可能為IAS,而表面活性劑則起到填補緩蝕劑膜層缺陷的作用。不同復配體系協同效應的差異,可能與緩蝕劑分子的空間位阻有關。
免責聲明:本網站所轉載的文字、圖片與視頻資料版權歸原創作者所有,如果涉及侵權,請第一時間聯系本網刪除。
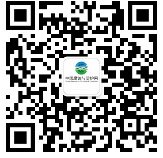
官方微信
《中國腐蝕與防護網電子期刊》征訂啟事
- 投稿聯系:編輯部
- 電話:010-62316606-806
- 郵箱:fsfhzy666@163.com
- 中國腐蝕與防護網官方QQ群:140808414