目前,國內已鋪設的石油天然氣管道總里程數已達13萬公里,其中天然氣管道總里程數近8萬公里。伴隨著油氣資源的大規模開發和利用,國內油氣輸送用鋼管制造企業數量在2010年前后大幅增加。而酸性油氣、深海油氣、頁巖氣、可燃冰等資源的深度開發也促進了國內油氣輸送用鋼管制造技術能力的提升。
油氣輸送用鋼管制造的基礎標準為API Spec 5L《管線管規范》、ISO 3183《石油天然氣工業 管線輸送系統用鋼管》、GB/T 9711《石油天然氣工業 管線輸送系統用鋼管》(該標準等同于ISO 3183)以及DNVOS-F101《海底管線系統》。國外陸上油氣輸送管制造標準多采用API Spec 5L 或ISO 3183、國內陸上油氣輸送管制造標準多采用GB/T 9711、海底油氣輸送管制造標準多采用DNV-OS-F101。另外,一些大型油氣公司在輸送管基礎制造標準的基礎上補充了一些技術要求,形成了自己的企業標準。如中國石油天然氣集團公司的企業標準《油氣輸送管道用管材通用技術條件》、殼牌石油公司的DEP標準、道達爾公司的GS標準等。
油氣輸送過程中泄漏或斷裂失效可造成無法估量的損失,尤其天然氣管道的泄漏或斷裂失效可造成毀滅性的災難,所以各油氣輸送用鋼管制造標準均要求應用無損檢測技術對質量進行把控。從某天然氣工程項目直縫焊接鋼管制造工藝流程(見下圖)中可以看出,無損檢測工序數量約占總檢測工序數量的70%。同時從工藝流程圖中也可看到,在原材料復驗、過程檢驗以及最終檢驗上均可用超聲檢測。
圖1 某天然氣工程項目直縫焊接鋼管制造工藝流程
下面將對超聲檢測技術在油氣輸送用鋼管制造行業的發展及應用現狀進行介紹,并對其在行業中的應用前景提出展望。
1 超聲檢測技術在油氣輸送 用鋼管制造行業的應用發展
油氣輸送用鋼管制造過程屬于流水線作業,為了滿足生產節拍的需求,檢測工序應具備較高的自動化程度,所以在鋼管制造過程中的超聲檢測常采用多通道自動化超聲檢測系統。多通道自動化超聲檢測技術是伴隨著計算機技術的發展而發展的,在2000年之前其成熟度落后于當時的X射線實時成像技術。因此API Spec 5L第42版(2000年發布)中對埋弧焊鋼管焊縫的無損檢測仍要求對全長焊縫進行X射線實時成像檢測。而隨著多通道自動化超聲檢測技術的進步,標準對于無損檢測的要求也進行了相應調整,API Spec 5L從第43版(2004 年發布)到第46版(2018年發布)各版標準中對埋弧焊鋼管焊縫的無損檢測均優先采用超聲檢測,全長焊縫X射線檢測僅作為協議條款,已不再作為硬性要求。油氣輸送用鋼管有著鋼級由低到高、壁厚由小到大的發展趨勢,較之射線檢測利用超聲檢測技術檢測高鋼級、大壁厚鋼管更具優勢,可見標準對檢測方法進行調整具有其合理性。另外,自動化超聲檢測系統可以做到自動評定、自動記錄,從而減少了過程中人的參與,目前這一優勢也是射線檢測技術所無法比及的,亦可見標準對檢測方法進行調整具有合理性。
在很長一段時期內,在多通道自動化超聲檢測系統的檢測設備制造水平方面,國內與國外存在較大差距,而高性能的全套進口多通道自動化超聲檢測系統動輒上千萬,同時還需要高額的使用和維護費用,這些情況導致高性能的多通道自動化超聲檢測系統在國內油氣輸送用鋼管制造行業得不到廣泛配置。出于對行業水平的整體考量,國內油氣管線項目雖要求對埋弧焊鋼管焊縫進行超聲檢測,但截至目前仍未舍棄焊縫全長的X 射線檢測。
近年來,隨著多通道自動化超聲檢測技術的進步,鋼管制造標準對超聲檢測系統提出了更高的要求,一些技術要求已經突破習慣做法。比如,DEP標準對檢測系統的穩定性提出了更高要求,在系統穩定性測試過程中,要求滿屏高度80%(±5%)的測試回波信號進行連續8次試驗,8次試驗測試信號波動不應超過信號幅度均值的25%。通常認為檢測系統不漏檢即可,如果回波信號波動較大,可適當提高整體增益水平以保證不漏檢。但是,回波信號波動較大的檢測系統如果按照DEP標準驗收,很可能就會歸于不合格檢測設備。再比如,澳大利亞天然氣管道公司APA集團的油氣鋼管技術規范對自動化超聲檢測結果的準確性提出了更高的要求,其要求最終檢測結果應以自動化超聲檢測的結果為準,不允許采用手工超聲檢測對自動化超聲檢測報警信號進行放行。通常認為自動檢測系統如果靈敏度設置偏高一些,可以在一定程度上保證不漏檢,但檢測過程中部分未超標的缺欠可能會因此發生報警標識。習慣做法是在自動檢測之后采用手工檢測進行進一步確認,但若按照APA的技術規范,存在被自動檢測系統報警標識的鋼管將不能被直接驗收。
2 超聲檢測技術在油氣輸送 用鋼管制造行業的應用現狀
油氣輸送用鋼管分為焊接鋼管和無縫鋼管,其中焊接鋼管分為直縫埋弧焊鋼管、直縫高頻焊鋼管、螺旋埋弧焊鋼管。鋼管制造過程中的超聲檢測采用自動超聲檢測輔以手工超聲檢測。其中手工超聲檢測廣泛采用數字便攜A型脈沖反射式超聲檢測儀,目前該類儀器已較為成熟,其性能滿足檢測要求。而自動化超聲檢測的應用現狀較為復雜,下面從焊接鋼管用鋼板(或鋼卷)的超聲檢測、焊接鋼管焊縫的超聲檢測、無縫鋼管管體的超聲檢測等3個方面對其應用分別進行介紹。
No.1焊接鋼管用鋼板(或鋼卷)的自動化超聲檢測
焊接鋼管用鋼板(或鋼卷)超聲檢測主要用以檢測分層缺欠,特殊情況下才用以檢測裂紋缺陷。以鋼板(或鋼卷)作為檢測面較為平整,易形成良好的耦合效果,通常情況會優先選擇成型前在鋼板(或鋼卷)上進行均布的平行帶掃查(即列線掃查),其常用的檢測機構形式如下圖所示。
圖2 鋼板(或鋼卷)的超聲檢測常用檢測機構形式
直縫埋弧焊鋼管進行管體超聲檢測將會受到焊縫余高的影響,檢測不易實現,通常選擇在鋼板上進行,如下圖所示。
圖3 直縫埋弧焊鋼管用鋼板的自動化超聲檢測
直縫高頻焊鋼管的管徑較小,在管體上進行超聲檢測如采用直接接觸法,則耦合效果較差;如采用液浸式耦合,檢測機構較為復雜,故通常選擇在鋼卷上進行,如下圖所示。
圖4 直縫高頻焊鋼管用鋼卷的 自動化超聲檢測
螺旋縫埋弧焊鋼管的管徑較大,而且在管體上采用螺旋方式檢測可以有效避開焊縫余高的影響,可以在成型和焊接后在管體上進行檢測,如下圖所示。
圖5 螺旋縫埋弧焊鋼管的管體 自動化超聲檢測
標準中對鋼板(或鋼卷)超聲檢測掃查覆蓋率的要求一般因鋼管服役環境不同而不同,海洋服役環境、酸性服役環境以及地質狀況復雜的服役環境通常要求較高的掃查覆蓋率。另外,鋼板(或鋼卷)的不同部位的超聲檢測掃查覆蓋率也有所不同,邊部以及端部如存在分層,易對質量造成不良影響(這一點筆者在《鋼板邊部分層對雙面埋弧焊鋼管的質量影響》一文中曾進行過專題論述,見《理化檢驗-物理分冊》2016年第52卷第3期),通常這些部位的掃查覆蓋率要求較高。高掃查覆蓋率可以通過多次掃查實現,也可以一次掃查實現。如果一次掃查實現高掃查覆蓋率就需要較多數量的檢測通道,比如一款國產新型的鋼板電磁超聲檢測系統配有800個檢測通道,可以同時檢測分層、裂紋以及進行厚度測量,如下圖所示。
圖6 800通道鋼板電磁超聲自動化 檢測系統
雖然鋼板(或鋼卷)自動化超聲檢測機構較為龐大,但實際結構較為簡單,因此國內油氣輸送用鋼管制造企業對該設備的配置較復雜,其中有進口設備、國產設備,也有自制設備。這也導致行業內設備性能參差不齊,高性能的設備系統穩定、檢測盲區小、檢測效率高、可以實現缺欠自動評定,而性能較低的設備則無法做到這些。
No.2 焊接鋼管焊縫的自動化超聲檢測
焊接鋼管焊縫的自動化超聲檢測按照耦合方式可以分為水膜法和射流法兩種,如下圖所示。
圖7 水膜法和射流法耦合示意
射流法檢測的優點較多,但對耦合水的控制要求較高、聲束入射角的控制要求較高、耦合狀態自監控較難實現,目前行業內仍以水膜法檢測為主。直縫埋弧焊鋼管焊縫自動化超聲檢測系統和螺旋縫埋弧焊鋼管焊縫自動化超聲檢測系統如下圖所示。
圖8 直縫埋弧焊鋼管焊縫的自動化超聲檢測
(a)探頭機架的結構
(b)檢測系統實物
圖9 螺旋縫埋弧焊鋼管焊縫的自動化 超聲檢測
焊接鋼管焊縫的自動化超聲檢測設備較為復雜,目前行業內多由專業設備廠家制作。近年來國內專業設備廠家也從單純模擬國外設備發展到能夠對檢測設備自主研發,設備的整體性能也得到了大幅度提升,進一步拉近了國內外的技術差距。同時,行業對自動化超聲檢測系統的要求也越來越高,比如焊縫自動跟蹤以及橫波斜探頭耦合監控已成為檢測系統的必備功能。另外,超聲檢測新技術也逐漸步入檢測系統,如一款帶PAUT功能的自動化超聲檢測系統在螺旋縫埋弧焊鋼管焊縫檢測上得以應用(見下圖),這將在很大程度上減小機械結構的復雜程度,也進一步提高了檢測的可靠性。
圖10 螺旋縫埋弧焊鋼管焊縫 帶有PAUT功能的自動化超聲檢測
焊接鋼管焊縫的自動化超聲檢測需要科學和嚴謹的檢測工藝作為技術支持,目前在行業內還存在一定程度的不足。比如檢測探頭的布置,很多人認為能夠按照標準要求發現人工缺陷即可,那么僅僅滿足標準的要求是否就可以了呢?從下圖可以看出,兩種探頭布置均能夠滿足標準的靈敏度校驗要求(即發現焊縫中心豎通孔以及焊縫邊緣人工刻槽),但兩種布置的有效聲束覆蓋狀況迥異,按圖11(b)布置將會導致嚴重的漏檢。
(a)一種檢測探頭布置
(b)另一種檢測探頭布置
圖11 自動化超聲檢測探頭的兩種不同 布置方式
No.3 無縫鋼管管體的自動化超聲檢測
油氣輸送用無縫鋼管管體自動化超聲檢測多采用局部液浸形式。探頭與鋼管之間的運動形式有兩種,一種是鋼管原地旋轉加探頭直線運動,另一種是鋼管直線運動加探頭高速旋轉,見下圖。
圖12 鋼管原地旋轉加探頭直線運動的無縫鋼管管體自動化超聲檢測
圖13 鋼管直線運動加探頭高速旋轉的無縫鋼管管體自動化超聲檢測(結合以無線通訊技術)
無縫鋼管如用于海洋服役環境、酸性服役環境或地質狀況復雜的服役環境,對其質量要求就較高。通常要求檢測縱向缺欠和分層缺欠,同時還有壁厚測量的要求,特殊情況下還會有橫向缺欠的檢測要求。
無縫鋼管管體自動化超聲檢測的機構較為簡單,檢測效果較好,目前應用較為成熟。隨著無線通訊的發展,結合以無線通訊技術的無縫鋼管管體自動化超聲檢測系統已得以應用(見圖13)。該檢測系統以數字信號替代了模擬信號,既提高了信噪比,也解決了模擬信號耦合困難的問題。
超聲檢測技術在油氣輸送用鋼管制造行業的應用前景展望
隨著科技的高速發展,超聲檢測技術本身將會向著超聲成像的方向發展,檢測系統中輔助技術將會變革升級,這些將使得超聲檢測系統不斷更新迭代。
自動化超聲檢測系統也將向著智能化超聲檢測系統發展。首先是超聲檢測技術本身的智能化,工藝的選擇、制定和執行等工作將不再過多地依賴于人。另外,超聲檢測技術將與其他檢測技術之間、與制造工序之間建立良好的智能互聯互通。
超聲檢測技術在油氣輸送用鋼管制造行業的應用將隨著工業體系的進步而進步,先進的超聲檢測技術也將為國家能源事業提供更加有力的保障。
免責聲明:本網站所轉載的文字、圖片與視頻資料版權歸原創作者所有,如果涉及侵權,請第一時間聯系本網刪除。
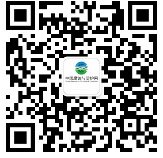
官方微信
《中國腐蝕與防護網電子期刊》征訂啟事
- 投稿聯系:編輯部
- 電話:010-62316606-806
- 郵箱:fsfhzy666@163.com
- 中國腐蝕與防護網官方QQ群:140808414