硫酸腐蝕是烷基化裝置最普遍的腐蝕方式,防止硫酸腐蝕是烷基化裝置平穩運行的根本保障。通過某煉油廠烷基化裝置反應器管束腐蝕的現象,著重分析硫酸溫度、濃度和流速等因素對裝置腐蝕的影響,探究硫酸對管線腐蝕的機理,找尋腐蝕原因并制定相應措施。
某公司煉油廠22×104 t/a烷基化裝置由蘭州寰球工程公司設計,采用硫酸法C4烷基化工藝技術,以醚后C4為原料,經過原料預處理、烷基化反應、閃蒸及壓縮制冷、反應產物精制、反應產物分餾等工序,最終生產出烷基化油。
烷基化反應器(R‐2201ABC)為臥式偏心雙支點內置U型管換熱器式攪拌反應器,屬Ⅱ類壓力容器。反應器內硫酸與醚化后C4混合乳化,生成異辛烷,即烷基化油。反應器內部存在硫酸,發生腐蝕即可造成后路帶酸,需將反應器切除系統,反應烴進料和酸混合進入反應器,經攪拌混合形成乳化液,并完成烷基化反應;葉輪背部形成負壓區,乳化液向壓力低區域流動進入外套筒,一部分進入反應器上方沉降器進行酸烴分,分離的酸通過下酸管線循環利用,分離出的烷基化油和烴的混合物作為冷劑進入反應器管束,吸走烷基化反應熱;另一部分乳化液進入內套筒循環。
裝置反應器
1 反應器腐蝕泄漏
2020年4月,發現后路閃蒸罐反應物側帶酸嚴重,經過對比,反應器C冷劑出口渾濁,初步確定反應器C內管束腐蝕泄漏。將反應器C切除系統后,發現反應器U型管管束外壁腐蝕嚴重。
2 泄漏位置及腐蝕原因分析
2.1 管束位于支撐圈處腐蝕
此類腐蝕外觀非常明顯,均位于管束與支撐圈相近部位,最深處腐蝕坑達2.5 mm,泄漏的管束也為此類腐蝕。通過現場情況來看,管束迎著介質流動方向腐蝕明顯,背對介質流動方向無腐蝕,且迎著介質流動方向的支撐圈也有明顯的腐蝕,而背對介質流動方向的支撐圈則未見腐蝕,因此判斷此處腐蝕為硫酸在流動過程中遇支撐件,改變流動方向,在局部形成擾流狀態,不斷沖刷碳鋼表面,使其無法形成鈍化膜,進而發生腐蝕。
2.2反應器套筒折流處管束腐蝕
U 型管管束在套筒邊緣處管表面腐蝕嚴重,且分布密集,從方位上來看,均是迎著介質流動方向腐蝕較為嚴重。在反應器內介質在攪拌槳的作用下由外側流向套筒內部,流動方向發生180°的改變,在管束表面存在渦流狀態,不斷沖刷碳鋼表面,發生腐蝕。
2.3腐蝕分析
由上述腐蝕部位及腐蝕程度來看,管束是否腐蝕,與硫酸在金屬表面形成的鈍化膜有直接關系,在反應器套筒內部,酸烴乳化液在攪拌槳的作用下處于層流狀態,流速較低,沒有把金屬表面鈍化膜破壞。所以,處在此區域的管束沒有腐蝕現象。而在管束支撐及套筒邊緣的管束,由于流體流動方向的改變,不斷沖刷管束,使金屬表面的鈍化膜被破壞,導致管束腐蝕。
酸濃度和溫度的控制
不同條件下硫酸對碳鋼的腐蝕速率見表1。
由表1 可以看出,酸濃度低和酸溫度高易造成碳鋼管束腐蝕。酸濃度高的硫酸易在金屬表面形成鈍化膜,所以在反應器運行期間要保證酸濃度,根據化驗測量數據補充新酸,將酸濃度控制在90% 以上。保證硫酸酸溫度不會過高。
管束外表面加裝護板
根據乳化液流動特性,在管束腐蝕嚴重的區域加裝護板,對沖刷嚴重、鈍化膜破壞的區域進行保護,見圖2。
圖2 管束加護板
同時使乳化液流動狀態趨于平緩,減少腐蝕發生。可以將管束升級為316L 或Alloy20 合金材質,在本質上消除硫酸腐蝕,保證裝置平穩生產。
反應溫度的控制
反應溫度為烷基化裝置重要參數之一,維持合理的反應溫度有利于減少腐蝕發生。同硫酸溫度對碳鋼腐蝕的影響,反應溫度高也將提高腐蝕速率,低反應溫度可抑制聚合反應,并促進烷基化反應。但反應溫度低于4 ℃,會抑制烴中的酸沉降分離,大量的酸從酸沉降器中攜帶出來,導致酸耗增加,腐蝕加劇。反應溫度控制在4~10 ℃之間。
通過裝置反應器泄漏的現象,可以推斷硫酸腐蝕主要是鈍化膜被破壞,鈍化膜的破壞主要和乳化液流動狀態和酸溫度密切相關;通過降低反應器溫度,保護流動狀態不穩定的管束區域,有效控制反應器管束腐蝕,保證裝置平穩生產。
免責聲明:本網站所轉載的文字、圖片與視頻資料版權歸原創作者所有,如果涉及侵權,請第一時間聯系本網刪除。
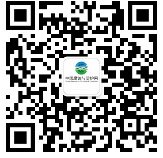
官方微信
《中國腐蝕與防護網電子期刊》征訂啟事
- 投稿聯系:編輯部
- 電話:010-62316606-806
- 郵箱:fsfhzy666@163.com
- 中國腐蝕與防護網官方QQ群:140808414