摘要
研究了化學組分和顯微組織結構對AZ31,AZ91,AM60和ZK61等4種鎂合金在含有不同濃度NH4NO3的0.1 mol/L NaCl溶液中腐蝕行為的影響。通過浸泡實驗、電化學測試、SEM和CLSM表面分析等探討了4種鎂合金的腐蝕機理。結果表明,NH4NO3的存在會加快鎂合金的腐蝕;并且由于在特定濃度范圍內,Cl-,NH4+和NO3-的協同作用,會發生自催化點蝕。不同鎂合金的耐蝕性與合金的化學成分和顯微組織密切相關。
關鍵詞: 鎂合金; 硝酸銨; 自催化點蝕; 化學組分; 顯微結構
鎂合金是最輕的一種金屬結構材料,由于其低密度和良好的力學性能而受到越來越多的關注 [1],被廣泛應用于航空、航天和汽車工業[2-4]。然而,由于較差的耐腐蝕性能[5],其應用范圍比鋁合金更受限制。霧霾的存在對金屬的腐蝕行為有一定的影響。Cui等[6]研究了AZ31鎂合金在Cl--NH4+-NO3-溶液體系內的腐蝕機制,研究結果表明特定的溶液體系會影響暴露在霧霾環境中鎂合金的腐蝕過程。
對于鎂合金而言,Al可以通過形成第二相 (β-Mg17Al12) 顯著提高合金的抗拉強度[7]。添加一定量的Al會提高鎂合金中β相的含量,當β相形成連續網狀結構時,會顯著改善材料的耐腐蝕性[8]。Zn對于鎂合金的強度也有著至關重要的影響,它的存在可以抑制Fe及Ni對鎂合金腐蝕的不利影響。當Zn含量較少時 (Zn<1%),可以提高Al在鎂合金中的固溶度,提高Al的固溶強化作用[9]。Song等[10]認為,為保證鎂合金的耐蝕性能,AZ系鎂合金中的Zn添加量應該控制在1%~3% (質量分數)。Mn在鎂合金中會與Fe形成熔渣,可以在一定程度上消除Fe對于鎂合金耐腐蝕性的不利影響。因此,一般耐腐蝕的鎂鋁合金中都含有一定量的Mn。除以上合金元素外,Zr也是一種較常見的元素,通常被添加到非鋁系鎂合金中。添加到鎂合金中的Zr不僅能很好地細化晶粒,而且可以有效地去除雜質[11]。在熔融的鎂基體中,Zr與Fe反應形成Fe-Zr金屬間化合物,由于該金屬間化合物具有較高密度,會快速沉積,因而可以提高鎂合金的純度,這在一定程度上改善了鎂合金的耐蝕性。然而,Zr在非鋁合金晶粒中通常分布不均勻,Zr會富集在晶粒的中心。此外,不能固溶的Zr顆粒可能會作為腐蝕電偶的陰極從而加速鎂合金的腐蝕速率,因此應該注意避免Zr的過量添加。
基于此,本文研究了不同化學組分和顯微結構的鎂合金 (AZ31,AZ91,AM60和ZK61) 在模擬濱海霧霾環境下的腐蝕行為。研究采用在NaCl溶液中添加NH4NO3模擬濱海霧霾環境,探討了NH4+和NO3-對4種鎂合金在NaCl溶液中腐蝕行為的影響,以及它們發生點蝕和均勻腐蝕的演變過程。
1 實驗方法
本實驗采用的實驗材料為軋制的AZ31 (Mg2.6Al1.0) 和AZ91 (Al8.2Zn0.4) 板材以及AM60 (Al5.9Mn0.3Zn0.001) 和ZK61 (Zn5.5Zr0.5Mn0.008) 鑄錠。溶液環境為0.1 mol/L NaCl溶液和添加不同濃度NH4NO3的0.1 mol/L NaCl溶液,溶液的初始pH是直接通過pH計測量得到。實驗中所有使用的化學藥品都為分析級試劑。在整個實驗過程中,溶液溫度控制在 (25±1) ℃。
試樣加工成20 mm×20 mm×3 mm的方形試樣,用砂紙打磨到1500#,之后用酒精脫脂并用去離子水清洗后冷風干燥。為保證實驗結果具有重復性,每個條件均使用5個平行試樣。用分析天平對樣品原始重量 (w0) 進行稱量并記錄,試樣在300 mL的溶液中浸泡12 h。之后,將試樣放置在除銹液 (200 g/L CrO3,10 g/L AgNO3和20 g/L BaNO3) 中浸泡去除腐蝕產物,用去離子水沖洗并冷風干燥。對干燥好的試樣進行稱重并記錄最終質量 (w1)。試樣的失重 (C,mg/cm2) 由下式得到:
其中,A是試樣的暴露面積。
電化學測試所用儀器為CS350電化學工作站,試樣加工成10 mm×10 mm×3 mm方形試樣,測試采用傳統的三電極體系,以試樣為工作電極,Pt片為對電極,飽和甘汞電極 (SCE) 為參比電極。測試前用砂紙將工作面逐級打磨到1500#,之后用酒精和去離子水對工作面進行仔細清洗并用冷風干燥。以開路電位 (OCP) 為測試起始點,分別對試樣動電位極化曲線的陽極分支和陰極分支進行測試,動電位掃描速率為0.333 mV/s。
采用掃描電鏡 (SEM,Quanta 250) 對浸泡試樣表面的腐蝕形貌進行表征,之后采用激光共聚焦顯微鏡 (CLSM, KEYENCE VK-X250) 對試樣表面點蝕坑進行表征和分析。CLSM的每個視場面積為0.015 cm2,每個試樣選取5個視場進行統計分析。
2 結果與討論
2.1 原始微觀組織結構
AZ31,AZ91,AM60和ZK61合金的原始組織如圖1所示。從圖1a和b中可以看出,AZ91合金的SEM像包含更多的β相 (Mg17Al12),而在AZ31合金中幾乎看不到β相。從圖1c中可以看出,除基體相外,AM60合金的顯微組織還包含β相和Al8Mn5相。圖1d中顯示,ZK61合金的微觀組織還包含基體Mg相和Zn2Zr。除基體α相外,共晶α相在腐蝕系統中充當陰極,這會促進基體α相的腐蝕,從而導致ZK61合金的耐腐蝕性較差。
圖1 AZ31,AZ91,AM60和ZK61合金的微觀結構
2.2 失重及腐蝕速率比較
圖2是4種鎂合金的失重和腐蝕速率。可以看出,加入NH4NO3后,4種鎂合金的重量損失都有所增加,但增幅各不相同,這歸因于鎂合金的化學組成和微觀結構的差異。
圖2 AZ31,AZ91,AM60和ZK61 4種鎂合金在0.1 mol/L NaCl和0.1 mol/L NaCl+0.01 mol/L NH4NO3兩種溶液中浸泡12 h的失重和腐蝕速率
鎂合金腐蝕速率的計算公式如下[12]:
其中,V是腐蝕速率 (mg·cm-2·d-1);t是浸泡時間 (h)。通過等式PW?=?2.1 V將V值轉換為腐蝕速率 (PW,mm/a),如圖2b所示。在0.1 mol/L NaCl溶液中,AZ91合金的腐蝕速率最低,ZK61合金的腐蝕速率最高。加入0.01 mol/L NH4NO3溶液之后,4種鎂合金的腐蝕速率均有所提高,而AM60合金的腐蝕速率最低,表明AM60合金在該溶液體系中具有更好的耐蝕性。ZK61合金的腐蝕速率仍然是最高的,說明ZK61合金的耐蝕性較差,這些結果也可從表1中得出。
表1 NH4NO3對4種鎂合金的腐蝕加速倍率
圖3分別顯示了AZ31,AZ91,AM60和ZK61合金在未含有和含有0.01 mol/L NH4NO3的0.1 mol/L NaCl溶液中的極化曲線。在圖3a中,ZK61合金的陰極Tafel斜率明顯高于其他3種鎂合金,另外3種鎂合金的陰極極化曲線在0.1 mol/L NaCl溶液中具有相同的變化趨勢,均為典型的氫析出反應,具有極為接近的Tafel斜率。從表2中可以看出,圖3a中的陰極曲線依次向右移動 (從左至右依次為AZ91,AM60,AZ31和ZK61合金) ,腐蝕電流密度依次增加,表明腐蝕速率依次增加。ZK61合金的腐蝕電流密度比AZ91和AM60合金的高出一個數量級,約是AZ31合金的6~7倍,這表明ZK61合金的腐蝕速率遠高于其他3種合金的。表2為4種鎂合金在0.1 mol/L NaCl溶液中極化曲線的擬合數據,參照之前的研究表明,腐蝕電流可以作為腐蝕速率的標準度量之一,即腐蝕電流越小,耐腐蝕性越好[13]。綜上所述,4種鎂合金耐蝕性的順序依次為:AZ91>AM60>AZ31>ZK61,極化曲線測試結果與失重實驗一致。
圖3 AZ31,AZ91,AM60和ZK61鎂合金在0.1 mol/L NaCl和0.1 mol/L NaCl+0.01 mol/L NH4NO3溶液中的極化曲線
表2 4種鎂合金在0.1 mol/L NaCl溶液中的自腐蝕電流密度 (Icorr) 和腐蝕速率 (Pi)
與圖3a中的曲線相比,添加NH4NO3后,極化曲線發生了很大變化。圖3b中掃描曲線的陰極部分表明,AZ91合金的氫析出電流密度值低于其他合金的,AM60,AZ31和ZK61合金的依次降低。這表明從動力學上來講,ZK61合金的陰極反應比其他3種合金更容易發生,這可能是由于ZK61合金中存在更多的陰極第二相,這可能會導致電偶腐蝕。圖3b中AZ91和AM60合金掃描曲線的陽極部分有明顯的拐點,在此之前電流密度緩慢增加,然后隨著電位的增加而迅速增加。但是,隨著電流密度的增加,ZK61合金的陽極曲線上沒有明顯的拐點。Song等[14]認為,極化曲線掃描過程中腐蝕電位的差異是由于未腐蝕表面的陰極氫逸出速率不同所致。如果陽極過程沒有明顯改變,較低的陰極極化曲線通常會導致更大的負腐蝕電位[13]。
2.3 腐蝕形貌觀察
2.3.1 SEM形貌觀察
前期研究[6]表明,AZ31鎂合金在含有NH4NO3的NaCl溶液中發生了明顯的點蝕行為,且與傳統鎂合金點蝕橫向生長不同,這種情況下的點蝕沿深度方向生長。為了探討合金元素對自催化點蝕的影響,本文通過添加不同NH4NO3含量,研究4種鎂合金的“自催化”點蝕的離子濃度區間。圖4顯示了去除腐蝕產物的AZ31,AZ91和ZK61合金的SEM形貌 (AM60合金沒有出現“自催化”點蝕行為)。可以看出,AZ31,AZ91和ZK61 3種合金在去除腐蝕產物后顯示出各不相同的腐蝕形態。此外,3種鎂合金發生自催化點蝕的NH4NO3濃度范圍也不同。
圖4 AZ31,AZ91和ZK61合金在NaCl溶液中浸泡12 h后的腐蝕形貌
由圖4a可以看出,隨著NH4NO3濃度的逐漸增大,AZ31試樣表面由淺坑到強點蝕再到均勻腐蝕,自催化點蝕濃度在0.001~0.1 mol/L之間。在圖4b和c中可以看到相似的腐蝕趨勢,AZ91合金的自催化點蝕濃度在0.007~0.04 mol/L之間,ZK61合金的自催化點蝕濃度在0.0002~0.09 mol/L之間。濃度區間的大小可以反映出鎂合金的耐蝕性差異,AZ91合金的耐蝕性優于AZ31和ZK61鎂合金的。對于AM60合金來說,沒有特定的自催化點蝕的NH4NO3濃度范圍,僅在某些濃度 (0.001和0.01 mol/L NH4NO3) 時出現少量的腐蝕坑。這些腐蝕特征可以在圖5中看出。
圖5 4種鎂合金在0.1 mol/L NaCl和0.1 mol/L NaCl+0.01 mol/L NH4NO3兩種溶液環境中的點蝕參數
2.3.2 點蝕參數統計
點蝕參數具有6種指標,如圖5所示。除了AZ91合金外 (圖5a),其他合金的點蝕密度在添加0.01 mol/L NH4NO3的NaCl溶液中發生下降,這表明點蝕坑合并或某些點蝕坑的優先生長取決于NH4NO3的濃度。在兩種溶液中,最大點蝕深度 (圖5b) 和平均點蝕深度 (圖5c) 有所不同。加入NH4NO3后,ZK61合金的最大點蝕深度 (圖5b) 和平均點蝕深度 (圖5c) 增加了約100倍。說明在含0.01 mol/L NH4NO3的NaCl溶液中,ZK61合金的耐腐蝕性最差。添加NH4NO3后,點蝕坑直徑 (圖5d) 與點蝕坑深度的變化趨勢相同。AZ31和AZ91合金的單個點蝕坑體積 (圖5e) 變化不大,加入0.01 mol/L NH4NO3后,AM60合金的點蝕坑體積減小。ZK61合金的點蝕坑體積在添加NH4NO3后會成倍增加,腐蝕坑由淺變深。圖5f所示的點蝕坑的幾何形狀是用于闡明點蝕坑特性的有效參數[15]。根據點蝕坑直徑 (d) 與點蝕坑深度 (D) 的比值,點蝕坑形狀可以簡單地分為半圓形 (d/2D=1),深孔形 (d/2D<1) 和淺碟形 (d/2D>1)。與其他3種鎂合金相比,ZK61合金的d/2D值下降最多,這間接表明ZK61合金的耐腐蝕性最差。
2.4 討論
合金元素在一定程度上決定著鎂合金的微觀結構。然而,鎂合金的不均勻組織容易造成微電偶腐蝕[16,17]。因此,鎂合金的微觀結構在其腐蝕機理中起著重要作用。
Pardo等[16]指出,β相在腐蝕過程中具有雙重作用。根據β相的數量和分布,可以起到腐蝕阻擋層或加速陰極電偶的作用。本文中AZ91合金的β相呈網狀結構連續地分布在基體相中,可以有效地阻止AZ91合金進一步發生腐蝕。相反,AZ31合金中很少且不連續分布的β相會起到加速腐蝕的作用。在Cl--NH4+-NO3-溶液體系中,連續的β相也可以起阻礙腐蝕的作用,可以明顯看到AZ91合金的耐蝕性要優于AZ31合金的。
Zn有助于克服Fe和Ni的有害腐蝕作用,但高含量的Zn會導致第二相沉淀物的形成,從而導致不可避免的電偶腐蝕。Huan等[18]證明了ZK30合金的耐腐蝕性優于ZK60合金的,認為ZK30合金中Zn含量較低,形成較少的第二相顆粒和微電偶腐蝕。當Zn含量超過3% (質量分數) 時,根據Mg-Zn二元相圖可知[19],大量形成的Mg7Zn3相將導致微電流與基質偶聯,從而加速材料的腐蝕。從圖1d可以看出,ZK61合金中存在一些Mg2Zn相和枝晶,這可能會導致微電偶腐蝕,是ZK61合金耐腐蝕性差的原因之一。Zn含量的差異會影響4種鎂合金在含有0.01 mol/L NH4NO3的NaCl溶液中的腐蝕行為。Zn可與溶液環境中的NH4+絡合,導致鎂基體脫落并腐蝕。4種鎂合金中自催化點蝕的NH4NO3濃度范圍最大的是ZK61合金,這可能與其Zn含量較高有關。
Zr可以細化晶粒,在一定條件下,Mg-Zn-Zr合金具有良好的耐蝕性。但是,如果Zr含量過高會導致鎂合金的耐蝕性降低。Song等[8]研究表明,當Zr含量超過0.48%時,鎂合金的腐蝕速率會增加,這與Zr在鎂合金中的固溶度有關。當Zr含量超過其在鎂合金中的固溶度時會析出沉淀,含Zr沉淀充當鎂合金中的有效陰極相,從而加速了鎂合金基體相的腐蝕。在該實驗中,ZK61合金含有0.512%的Zr,超過文獻中的0.48%,這可能是ZK61合金耐腐蝕性差的另一個原因。
Mn可通過去除Fe和其他重金屬元素來避免形成有害的金屬間化合物,從而提高合金的耐腐蝕性。AM60合金中的Mn可以形成AlMnFe相,降低合金中Fe的含量,凈化合金,從而提高合金的耐腐蝕性。Mn被添加到大多數Mg-Al合金中以去除雜質Fe和Ni,對于AZ91和AM60合金,通常添加足夠的Mn以確保Fe:Mn比小于0.032,從而顯著提高耐腐蝕性[10,20]。另外,AM60鎂合金中不含Zn,其也未觀察到“自催化”點蝕區間,這進一步說明,Zn的存在可能是引起鎂合金“自催化”點蝕的重要因素。這一部分內容將通過煉制不同含量的Mg-xZn合金來進一步研究。
實驗結果表明,引入NH4NO3會加快4種鎂合金的腐蝕速率,原因主要在于NH4NO3的引入會降低溶液的pH,酸性環境下鎂合金會更容易腐蝕;再者由于NH4+的緩沖作用,添加NH4NO3會使Mg(OH)2保護膜遭到破壞并促進陰極NO3-的還原反應,從而加速了鎂合金的腐蝕。
3 結論
(1) 在0.1 mol/L NaCl溶液中添加0.01 mol/L NH4NO3可加快AZ31,AZ91,AM60和ZK61 4種鎂合金的腐蝕速率。
(2) 在0.1 mol/L NaCl溶液中,4種鎂合金的腐蝕速率排序為ZK61>AZ31>AM60>AZ91;而在0.1 mol/L NaCl溶液中添加0.01 mol/L NH4NO3時,4種鎂合金的腐蝕速率排序變為:ZK61>AZ31>AZ91>AM60。
(3) 當在溶液中添加0.001~0.1 mol/L NH4NO3時,AZ31鎂合金就會出現“自催化”點蝕;當溶液中添加0.007~0.04 mol/L NH4NO3時,AZ91鎂合金會出現自催化點蝕。ZK61鎂合金自催化點蝕發生在溶液中NH4NO3的濃度范圍為0.0002~0.09 mol/L時,AM60鎂合金未發現自催化點蝕。
(4) Zn可能是導致鎂合金在一定NH4NO3濃度區間發生自催化點蝕的關鍵因素。
參考文獻
[1]Wang X J, Xu D K, Wu R Z, et al.
What is going on in magnesium alloys?
[J]. J. Mater. Sci. Technol., 2018, 34: 245
DOI:10.1016/j.jmst.2017.07.019 URL [本文引用: 1]
[2]Song G L, Bowles A L, StJohn D H.
Corrosion resistance of aged die cast magnesium alloy AZ91D
[J]. Mater. Sci. Eng., 2004, A366: 74
[本文引用: 1]
[3]Li J X, Zhang Y, Li J Y, et al.
Effect of trace HA on microstructure, mechanical properties and corrosion behavior of Mg-2Zn-0.5Sr alloy
[J]. J. Mater. Sci. Technol., 2018, 34: 299
[4]Atrens A, Johnston S, Shi Z M, et al.
Understanding Mg corrosion in the body for biodegradable medical implants
[J]. Scr. Mater., 2018, 154: 92
DOI:10.1016/j.scriptamat.2018.05.021 URL [本文引用: 1]
[5]Wu Z N, Li P J, Liu S X, et al.
Present state of research on corrosion of magnesium alloys
[J]. Foundry, 2001, 50: 583
[本文引用: 1]
(吳振寧, 李培杰, 劉樹勛等.
鎂合金腐蝕問題研究現狀
[J]. 鑄造, 2001, 50: 583)
[本文引用: 1]
[6]Cui Z Y, Ge F, Lin Y, et al.
Corrosion behavior of AZ31 magnesium alloy in the chloride solution containing ammonium nitrate
[J]. Electrochim. Acta, 2018, 278: 421
DOI:10.1016/j.electacta.2018.05.059 URL [本文引用: 2]
[7]Cheng Y L, Qin T W, Wang H M, et al.
Comparison of corrosion behaviors of AZ31, AZ91, AM60 and ZK60 magnesium alloys
[J]. Trans. Nonferrous Met. Soc. China, 2009, 19: 517
DOI:10.1016/S1003-6326(08)60305-2 URL [本文引用: 1]
[8]Zhao J M, Li T, Zhao X H.
Corrosion behavior of four cast magnesium alloys in simulated body fluid
[J]. Corros. Sci. Prot. Technol., 2015, 27: 444
[本文引用: 2]
(趙景茂, 李彤, 趙旭輝.
4種鑄造鎂合金在SBF溶液中的腐蝕行為研究
[J]. 腐蝕科學與防護技術, 2015, 27: 444)
DOI:10.11903/1002.6495.2014.348 URL [本文引用: 2]
[9]Li L J, Yu S H, Lei J L, et al.
Corrosion electrochemical behavior of AZ31 and AZ61 magnesium alloys in simulated sea water
[J]. Electrochemistry, 2008, 14: 95
[本文引用: 1]
(李凌杰, 于生海, 雷驚雷等.
AZ31和AZ61鎂合金在模擬海水中的腐蝕電化學行為
[J]. 電化學, 2008, 14: 95)
[本文引用: 1]
[10]Song G L, Atrens A.
Corrosion mechanisms of magnesium alloys
[J]. Adv. Eng. Mater., 1999, 1: 11
DOI:10.1002/(ISSN)1527-2648 URL [本文引用: 2]
[11]Xia L T, Gao S, Luo X P, et al.
Corrosion factor analysis of magnesium alloy at different circumstance
[J]. Foundry, 2005, 54: 794
[本文引用: 1]
(夏蘭廷, 高珊, 羅小萍等.
影響鎂合金腐蝕性能的因素分析
[J]. 鑄造, 2005, 54: 794)
[本文引用: 1]
[12]Cui Z Y, Li X G, Xiao K, et al.
Corrosion behavior of field-exposed zinc in a tropical marine atmosphere
[J]. Corrosion, 2014, 70: 731
DOI:10.5006/1177 URL [本文引用: 1]
[13]Li T, Zhang H, He Y, et al.
Comparison of corrosion behavior of Mg‐1.5Zn‐0.6Zr and AZ91D alloys in a NaCl solution
[J]. Mater. Corros., 2015, 66: 7
[本文引用: 2]
[14]Song G L, StJohn D.
The effect of zirconium grain refinement on the corrosion behaviour of magnesium-rare earth alloy MEZ
[J]. J. Light Met., 2002, 2: 1
DOI:10.1016/S1471-5317(02)00008-1 URL [本文引用: 1]
[15]Aouina N, Balbaud-Célérier F, Huet F, et al.
Single pit initiation on 316L austenitic stainless steel using scanning electrochemical microscopy
[J]. Electrochim. Acta, 2011, 56: 8589
DOI:10.1016/j.electacta.2011.07.044 URL [本文引用: 1]
[16]Pardo A, Merino M C, Coy A E, et al.
Influence of microstructure and composition on the corrosion behaviour of Mg/Al alloys in chloride media
[J]. Electrochim. Acta, 2008, 53: 7890
DOI:10.1016/j.electacta.2008.06.001 URL [本文引用: 2]
[17]Yu G, Liu Y L, Li Y, et al.
Corrosion and protection of magnesium alloys
[J]. Chin. J. Nonferrous Met., 2002, 12: 1087
[本文引用: 1]
(余剛, 劉躍龍, 李瑛等.
Mg合金的腐蝕與防護
[J]. 中國有色金屬學報, 2002, 12: 1087)
[本文引用: 1]
[18]Huan Z G, Leeflang M A, Zhou J, et al.
In vitro degradation behavior and cytocompatibility of Mg-Zn-Zr alloys
[J]. J. Mater. Sci: Mater. Med., 2010, 21: 2623
DOI:10.1007/s10856-010-4111-8 URL [本文引用: 1]
[19]Liu M, Uggowitzer P J, Nagasekhar A V, et al.
Calculated phase diagrams and the corrosion of die-cast Mg-Al alloys
[J]. Corros. Sci., 2009, 51: 602
DOI:10.1016/j.corsci.2008.12.015 URL [本文引用: 1]
[20]Zeng G, Xian J W, Gourlay C M.
Nucleation and growth crystallography of Al8Mn5 on B2-Al(Mn,Fe) in AZ91 magnesium alloys
[J]. Acta Mater., 2018, 153: 364
DOI:10.1016/j.actamat.2018.04.032 URL [本文引用: 1]
免責聲明:本網站所轉載的文字、圖片與視頻資料版權歸原創作者所有,如果涉及侵權,請第一時間聯系本網刪除。
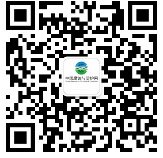
官方微信
《中國腐蝕與防護網電子期刊》征訂啟事
- 投稿聯系:編輯部
- 電話:010-62316606-806
- 郵箱:fsfhzy666@163.com
- 中國腐蝕與防護網官方QQ群:140808414