0 前言
鋁合金輕質(zhì)、導(dǎo)熱性好、塑性高、使用噪聲低,是工業(yè)中應(yīng)用最廣泛的有色金屬結(jié)構(gòu)材料,在航空航天、交通運輸、機械制造領(lǐng)域中已大量使用[1]。但耐蝕性差、硬度低、耐磨性較差,限制了鋁合金的廣泛應(yīng)用。因此,通過合適的表面處理工藝來增強鋁合金的摩擦學(xué)性能顯得至關(guān)重要。工業(yè)上常采用硬質(zhì)陽極氧化技術(shù)對鋁合金材料表面進行改性處理, 利用硬質(zhì)陽極氧化技術(shù)能夠在鋁合金表面生成厚度較大、與基體結(jié)合較好且具有較高硬度的陶瓷氧化膜,可有效地改善鋁合金表面的耐磨耐蝕性能[2]。然而,隨著工業(yè)技術(shù)的發(fā)展鋁合金摩擦部件的應(yīng)用環(huán)境變得越來越苛刻,在工程應(yīng)用過程中硬質(zhì)陽極氧化后鋁合金部件作為摩擦部件使用時,表面膜層存在表面摩擦因數(shù)偏高、對偶相容性差和難以被潤滑的缺點,限制了其在一些高速、高頻運動及不適宜液體潤滑場合的應(yīng)用[3]。
為改善鋁合金表面的耐磨潤滑性能,向氧化液中加入固體潤滑顆粒,利用陽極氧化技術(shù)制備出含有固體潤滑顆粒的自潤滑復(fù)合膜層,能夠有效降低氧化膜的摩擦因數(shù),提高其減摩性能是一種技術(shù)解決途徑[2-7]。許多學(xué)者通過在氧化液中加入超細(xì)增強耐磨和減少摩擦的顆粒同時進行雙顆粒或者多顆粒復(fù)合氧化膜制備的研究。其中常見的增強顆粒有Al2O3、Fe2O3、SiC、TiO2、ZrO2 等難溶粉體,常用的減磨顆粒有PTFE、石墨、MoS2 等。然而,固體潤滑微粒的復(fù)合往往導(dǎo)致膜層結(jié)構(gòu)的致密性下降,降低了自身的硬度。膜層的自身硬度的提升有利于提高其耐磨性能,相反,膜層自身硬度的下降又會降低其耐磨性能。此外,由于該類工藝復(fù)雜、槽液穩(wěn)定性控制難度較大,該類技術(shù)在工業(yè)中應(yīng)用較少。
單一的陽極氧化技術(shù)在工業(yè)上似乎無法滿足鋁合金部件的耐磨自潤滑要求,近年來真空氣相沉積技術(shù)在解決高耐磨自潤滑領(lǐng)域發(fā)揮著重要作用。目前已經(jīng)發(fā)展了以二硫化鉬屬、軟金屬、碳材料等為主的潤滑材料體系[8-10]。航天領(lǐng)域中固體潤滑薄膜主要以二硫化鉬屬的固體潤滑膜為主,研究表明,由于純的濺射二硫化鉬膜的耐潮解性能較差,金屬共濺射MoS2 薄膜成為提高MoS2 薄膜在潮濕環(huán)境下的存儲和摩擦學(xué)性能的研究熱點[11-15]。其中,金屬Ti的摻雜對MoS2 的摩擦學(xué)性能和耐潮解性能具有最好的效果[16]。此外,學(xué)者們在研究真空鍍MoS2 基膜層的潤滑性能時大多采用的基底為耐蝕性較好的不銹鋼或鈦合金材料,而采用鋁合金作為基底進行研究時, 其表面耐蝕性差的特點很少被考慮。
綜上所述,本文在鋁合金表面設(shè)計陽極氧化膜/濺射二硫化鉬基固體潤滑膜層,通過將傳統(tǒng)的鋁合金陽極氧化技術(shù),與先進的濺射二硫化鉬膜技術(shù)相結(jié)合,來提高鋁合金表面的防護性能。目前,這種復(fù)合鍍技術(shù)對增強鋁合金表面潤滑耐蝕性能的影響少有人研究。
1 試驗準(zhǔn)備
1.1 樣品制備
使用的材料為? 50×3mm的T6態(tài)2A14表面不包鋁的鋁合金圓片,所用鋁合金2A14的化學(xué)成分 (以質(zhì)量分?jǐn)?shù)計)為:Si 0.6~1.2%,Cu 3.9~4.8%,Mg 0.40~0.8%, Zn ≤0.30%, Mn 0.40~1.0%, Ti ≤ 0.15%,Ni ≤0.10%,Fe 0.00~0.70%,Al余量。
先采用硫酸陽極氧化技術(shù)對鋁合金表面進行預(yù)處理。制備工藝參數(shù)為:硫酸濃度230~270g/L,操作條件: 溫度-5℃, 陰極選用鉛板, 電流密度2A/dm 2,初始電壓18V,通過控制終電壓控制氧化膜層的厚度。再采用磁控濺射技術(shù)在Teer CF-800氣相沉積系統(tǒng)中制備MoS2/Ti薄膜。該系統(tǒng)包括兩個MoS2 濺射靶(純度為99.9%) 和兩個Ti濺射靶 (純度為99.9%)。鍍膜前試樣分別在石油醚、丙酮和乙醇中超聲清洗20min,將試樣干燥后放入真空室中。抽背底真空至2mPa,通入純度為99.999%的高純氬氣。先進行氬離子清洗,再進行真空鍍膜, 鍍膜結(jié)束后,試樣隨爐冷卻至室溫,打開真空室取出試樣。具體制備過程如圖1所示。
圖1 復(fù)合膜層制備方法
樣品制備步驟如下:機械拋光→蒸餾水清洗→ 冷風(fēng)吹干→堿腐蝕(NaOH 40g/L,Na2CO3 30g/L, 溫度50℃) →熱水清洗→冷水清洗→酸洗出光 (HNO3,400g/L)→冷水清洗→陽極氧化→冷水清洗→熱水清洗→干燥→超聲波清洗→真空獲得→氬離子清洗→鍍MoS2/Ti潤滑層→表征。試驗中制備了四種復(fù)合薄膜,其中濺射MoS2/Ti膜層厚度為2 μm,預(yù)處理氧化膜的厚度隨著終止電壓的增加而增加,氧化膜厚度依次為5、10、15 μm,具體工藝參數(shù)見表1。
表1 涂層的沉積參數(shù)
1.2 結(jié)構(gòu)表征及力學(xué)性能測試
采用FEI Quanta200F型場發(fā)射掃描電子顯微鏡(SEM)對涂層的表面形貌和截面特征進行分析, 并利用SEM配備的能譜儀(EDS)對涂層表面元素成分和含量進行分析。采用日本PHI Quanta型X射線光電子能譜儀(XPS)對涂層表面進行分析,X-射線源是Al-Kα 單色化X射線源,能量為1 486.6eV,分析區(qū)域直徑為200 μm。利用能量為45W的Ar +進行刻蝕,全譜和窄譜的通過能為280eV,每刻蝕20min對測試區(qū)域能譜掃描6次以得到可重復(fù)數(shù)據(jù)。采用Mini Test600B渦流測厚儀測試試樣任意8個位置的陽極氧化膜厚度,取其算數(shù)平均值作為膜層平均厚度。采用Tarlsurf表面輪廓儀對濺射MoS2/Ti膜的厚度進行測試,任意取3個位置,取其算數(shù)平均值作為膜層平均厚度。采用德國Fischerscope HM2000微納米硬度計測試涂層的承載能力,壓頭為平面角是136°的Vickers金剛石錐體壓頭,最大壓入深度為2 μm,以保證Vickers金剛石不壓穿MoS2/Ti薄膜,取8次測量的平均值作為最后的結(jié)果。采用布魯克的UMT-3摩擦測試系統(tǒng)測試復(fù)合測試復(fù)合膜層的摩擦學(xué)行為。考慮到膜層的實際應(yīng)用工況,采用往復(fù)滑動方式進行摩擦磨損測試。相關(guān)測試參數(shù)如下:摩擦配副為 ?8mm的9Cr18鋼球,球固定不動,頻率10Hz,單次滑動行程5mm,環(huán)境溫度為25℃,環(huán)境濕度為45%,運行20 000次,法向載荷分別為1、 5、 10、 20N。采用NeXview非接觸式3D光學(xué)輪廓儀測試磨痕截面輪廓來計算膜層的磨損率。膜層磨損率的計算式為:
(1)
式中,W 是磨損率,m 3/(N·m);V 是通過磨損體積, m 3,可對輪廓截面進行積分計算得到磨痕輪廓積分面積,再乘以運行步長得到磨損體積;F 是法向載荷,N;S 是滑行距離,m。采用傳統(tǒng)的三電極體系在P4000A型電化學(xué)站對膜層的動電位極化曲線測試來評估其耐腐蝕性能。其中,鉑片為輔助電極,飽和甘汞電極為參比電極,試樣為工作電極,試樣有效面積為1.0cm 2。在溫度為25℃ 下,將試樣浸泡在質(zhì)量分?jǐn)?shù)為3.5%(質(zhì)量分?jǐn)?shù))NaCl溶液中,測試前先進行開路電位檢測,確保測試前開路電位達(dá)到穩(wěn)定狀態(tài)。動電位極化曲線的掃描速率為5mV/s。
2 結(jié)果與討論
2.1 涂層顯微形貌
圖2 是利用掃描電子顯微鏡觀察到的試樣膜層表面,鋁合金表面直接濺射沉積MoS2/Ti,膜層表面有大量的球狀顆粒嵌在上面且膜層表面有少量的孔洞。對鋁合金表面進行陽極氧化預(yù)處理后,膜層表面中的凸出的小顆粒數(shù)量慢慢減少,膜層表面均有少量的孔洞。大量的文獻報道,在硫酸陽極氧化體系中,氧化膜由致密的阻擋層和多孔層組成[17]。 anodized1+ MoS2/Ti膜層表面顯得比較致密,可能是陽極氧化過程中的氧化電壓較小,膜層表面主要是致密的阻擋層。隨著氧化電壓增加到35V,氧化膜正處于多孔層生長的初期,膜層最外層的缺陷較多, 導(dǎo)致anodized2+ MoS2/Ti膜層中含有5~10 μm的孔洞。當(dāng)氧化電壓增加到45V時,氧化膜的多孔層生長方式已經(jīng)趨于穩(wěn)定,膜層表面較為致密。事實上,磁控濺射MoS2/Ti膜在鋁合金上生長的方式是島狀生長,能量較小得不到遷移必然導(dǎo)致膜層表面的粗糙度增加,活性位點增多。濺射離子在吸附、擴散等作用下堆積成島狀,后續(xù)的離子在原來的基礎(chǔ)上進一步擴大島狀,最終連接形成連續(xù)的薄膜材料。當(dāng)濺射膜在氧化膜上生長時,氧化膜表面上的大量的孔洞為膜層遷移制造了條件,導(dǎo)致形成的島狀顆粒較小[18-20]。
圖2 不同陽極氧化預(yù)處理方式下的復(fù)合膜層表面形貌
2.2 涂層力學(xué)性能
圖3 為試樣的載荷-位移曲線圖,可以看出,隨著壓入深度的增大,表面處理過的2A14鋁合金的表面承載能力要高于未作處理的2A14鋁合金表面的承載能力。納米壓痕曲線的區(qū)別體現(xiàn)在所加載荷同為200mN時的最大壓入深度差異,2A14基底、濺射MoS2/Ti膜、陽極氧化膜(5 μm厚) +濺射MoS2/Ti膜、陽極氧化膜(10 μm厚) +濺射MoS2/Ti膜、陽極氧化膜(15 μm厚) +濺射MoS2/Ti膜的最大壓入深度為2.69、1.58、1.44、1.34、1.40 μm。即在同樣載荷下的陽極氧化預(yù)處理后濺射二硫化鉬膜層的最大壓入深度明顯低于直接濺射二硫化鉬膜層的最大壓入深度,這說明鋁合金上陽極氧化預(yù)處理后濺射二硫化鉬復(fù)合膜具有較強的抵抗外加載荷的能力, 且抵抗外加載荷的能力與陽極氧化膜的厚度有關(guān)。
圖3 不同陽極氧化預(yù)處理方式下的復(fù)合膜層載荷-位移曲線
2.3 涂層摩擦磨損性能
圖4a為試樣分別在載荷1、5、10和20N下的平均摩擦因數(shù),可以看出,不同試樣的摩擦因數(shù)均隨著載荷的增加而減小,觀察測試過程中摩擦曲線,四種膜層在測試過程中均未發(fā)生膜層失效現(xiàn)象。其中,Anodized3+MoS2/Ti膜層在上述載荷下的摩擦因數(shù)均小于0.1,膜層的摩擦學(xué)穩(wěn)定性優(yōu)于其他膜層。圖4b為試樣在不同載荷下的磨損率,當(dāng)載荷為1N時,四種膜層均表現(xiàn)出較高的磨損率,這與膜層表面發(fā)生氧化有關(guān)。鋁合金上直接沉積MoS2/Ti膜的磨損率隨著載荷的增加而增加,鋁合金上做過陽極氧化預(yù)處理后沉積MoS2/Ti膜的復(fù)合薄膜磨損率隨著載荷的增加磨損率降低。其中,Anodized3+MoS2/Ti膜層在不同載荷下均有較小的磨損率。這種現(xiàn)象可能與陽極氧化預(yù)處理對鋁合金表面提高了膜層的承載能力有關(guān)[21-22]。相比于未做陽極氧化處理的鋁合金試片,陽極氧化處理生成的陶瓷相膜層增加了鋁合金表面的硬度,這層氧化膜作為中間層,使得復(fù)合薄膜相比于單一的濺射膜在鋁合金表面應(yīng)對大載荷的對偶件接觸時表現(xiàn)出更好的承載能力,從而表現(xiàn)出較好的耐摩擦磨損性能。 Anodized1 +MoS2/Ti和Anodized2+MoS2/Ti復(fù)合薄膜的摩擦學(xué)性能表現(xiàn)不夠優(yōu)異的原因可能與陽極氧化膜的狀態(tài)有關(guān)。
圖4 不同載荷下的復(fù)合膜層摩擦因數(shù)(a)和磨損率(b)
對Anodized3+ MoS2/Ti膜層在20N載荷下摩擦試驗后的磨痕形貌進行分析,研究復(fù)合膜層磨損機制。圖5為往復(fù)摩擦20 000次后的摩擦形貌,可以看出復(fù)合膜層表面存在片狀附著物,磨痕內(nèi)部有少量犁溝。對整個膜層表面的組分進行分析,可見膜層表層分布著S、Mo、AI、O、Ti、Fe元素,各個元素在膜層中分布并不均勻。其中,Fe、C元素是9Cr18中的元素成分,這說明摩擦過程中,對偶件9Cr18材料轉(zhuǎn)移到復(fù)合薄膜表面形成了轉(zhuǎn)移膜,主要發(fā)生了粘著磨損。粘著磨損主要發(fā)生在MoS2/Ti膜層與9Cr18的對磨中[23-26]。
圖5 摩擦20 000次后的磨痕形貌
對磨痕的三處特殊區(qū)域單獨進行測試,具體結(jié)果見圖6。其中區(qū)域1為非劃痕區(qū)域,主要是S、 Mo、Ti,即表層的MoS2/Ti膜層;區(qū)域2為磨痕的凹處,主要為AI、O、S,表明該處位置MoS2/Ti膜層已經(jīng)被磨穿,露出了底層的氧化膜。從2處形貌觀察可以看出底層的氧化膜并未表現(xiàn)出多孔結(jié)構(gòu)且膜層未有壓潰的現(xiàn)象出現(xiàn),這證明氧化膜在復(fù)合膜層起到了較好的承載能力;區(qū)域3為劃痕中的凸處,成分中有S、Mo、O、Ti、Fe、C元素的存在,說明該區(qū)域的膜層主要為對磨中形成的轉(zhuǎn)移膜。此外,分別對摩擦5 000次、10 000次后復(fù)合膜層的磨痕分析,也發(fā)現(xiàn)了類似的現(xiàn)象,較大的區(qū)別是磨痕的寬度隨著摩擦次數(shù)的增加而變大。
圖6 圖5中不同位置區(qū)域能譜的磨痕成分分析
2.4 涂層的耐蝕性能
多位學(xué)者發(fā)現(xiàn)[27-30],濺射二硫化鉬膜層在大氣環(huán)境中易潮解,導(dǎo)致膜層的摩擦性能會大幅降低,更嚴(yán)重時,膜層會從基底脫落。實際生產(chǎn)中,不可避免地會使得沉積有濺射二硫化鉬的零件在空氣中長期暴露。因此,對陽極氧化預(yù)處理后表面濺射二硫化鉬復(fù)合膜層的耐蝕性評價是十分有必要的。將帶有Anodized3+ MoS2/Ti膜層的鋁合金按照GJB3032— 1997中4.6.7.3條規(guī)定的條件進行濕熱存儲2 160h。圖7為試樣在3.5%的NaCl溶液中的動電位極化曲線,其中紅色線代表濕熱存儲前的樣品動電位掃描曲線,藍(lán)色線代表濕熱存儲后的樣品動電位掃描曲線。可以直觀地看出,進行陽極氧化預(yù)處理后濺射二硫化鉬復(fù)合膜層處理的2A14試片的腐蝕電位明顯高于未做表面處理的2A14試片,表明Anodized3+MoS2/Ti膜層提高了2A14試片的耐蝕性,試片表面的物質(zhì)狀態(tài)更為穩(wěn)定,使得腐蝕不容易發(fā)生。
圖7 試樣在3.5%的NaCl溶液中的動電位極化曲線
利用Tafel直線外推法計算試片的Ecorr和Jcorr,由表2可知試片未做表面處理的2A14基底的腐蝕電位為-0.654V,沉積有Anodized3+ MoS2/Ti膜層的試片的濕熱存儲前的腐蝕電位為-0.170V,但是濕熱存儲后,該試片的腐蝕電位降低為-0.369V。這表明濕熱存儲過程中Anodized3+ MoS2/Ti膜層表層的物質(zhì)成分發(fā)生了改變,采用XPS對濕熱存儲后的試片表層刻蝕進行成分分析。圖8為膜層刻蝕20min前后膜層的Mo 3 d、S 2p、O 1 s、Ti2p 圖,Mo 3d 譜圖中,結(jié)合能位于231.4eV的峰對應(yīng)于MoS2 中的Mo 4+,235.0eV的峰對應(yīng)于MoO3 中的Mo 6+,; S 2p 譜圖中,161.6eV的峰對應(yīng)于MoS2 中S 2-; O 1 s 譜圖中,532.1eV的峰對應(yīng)于吸附氧分子中的氧,529.8的峰對應(yīng)于O-Mo鍵的結(jié)合能。濕熱存儲后,復(fù)合膜層最外層Mo 6+的峰和吸附氧分子的峰的出現(xiàn), 表明膜層最外層發(fā)生了氧化。 XPS刻蝕20min后,Mo 6+對應(yīng)的峰消失,Mo 4+對應(yīng)的結(jié)合能降低,吸附氧分子對應(yīng)的峰消失,這說明復(fù)合膜層的表層發(fā)生了氧化。盡管對該膜層進行了連續(xù)刻蝕且每隔20min對膜層表面能譜進行收集,在第15次數(shù)據(jù)收集時發(fā)現(xiàn)了Al峰的出現(xiàn),表明刻蝕到氧化膜層。刻蝕過程中, Ar + 刻蝕功率是一定的, 由于MoS2/Ti為梯度復(fù)合薄膜,刻蝕速率無法確定,只能定性的說明濕熱存儲過程中的氧化反應(yīng)僅發(fā)生在MoS2/Ti膜層的表面。此外,O-Mo鍵對應(yīng)的結(jié)合能刻蝕前后均存在著,表明在濺射沉積MoS2/Ti過程中,真空室中仍有微量的O存在且與Mo發(fā)生了反應(yīng)。 Ti2p 中未發(fā)現(xiàn)明顯的峰,這與MoS2/Ti膜層表層Ti含量過少有關(guān)。
表2 試樣濕熱存儲前后的電化學(xué)參數(shù)
圖8 濕熱存儲2 160h后試片在XPS刻蝕20min前后的能譜圖
對于動電位極化曲線中腐蝕電位Jcorr的分析, 可以從腐蝕動力學(xué)角度看出膜層的耐蝕性能。未做表面處理的2A14的試片J corr為2.35 μA·cm 2,濕熱存儲前、后進行Anodized3+MoS2/Ti復(fù)合膜層處理過的2A14試片對應(yīng)的J corr分別為7.80 μA·cm 2 和8.79 μA·cm 2,這表明表面處理后的2A14試片的腐蝕速率增大。造成這種現(xiàn)象的原因可能是與Anodized3+MoS2/Ti膜層的結(jié)構(gòu)和成分有關(guān)。由圖1可知,Anodized3+MoS2/Ti中最外層為致密MoS2/Ti的層,在電化學(xué)測試過程中該層物質(zhì)可能與電解質(zhì)中的Cl- 和水發(fā)生反應(yīng),生成H2 SO4、 H2 S等物質(zhì)[29-30]。由于陽極氧化技術(shù)生成的氧化膜為多孔層,無法有效阻擋腐蝕介質(zhì)與基底的接觸,且由于測試過程中生成的H +加速了腐蝕反應(yīng)的發(fā)生。
2.5 涂層濕熱存儲2 160 h后的摩擦學(xué)性能
圖9 為濕熱存儲后Anodized3+MoS2/Ti復(fù)合膜層的摩擦因數(shù)曲線。在1、5、10、20N載荷下平均摩擦因數(shù)分別為0.092、0.090、0.081和0.078,平均摩擦因數(shù)均小于0.1,且摩擦曲線比較平穩(wěn)。該試樣的濕熱存儲后的摩擦因數(shù)與濕熱存儲前摩擦因數(shù)相比,濕熱存儲后的摩擦因數(shù)在四種不同載荷下的變化率均不超過10%,這表明,陽極氧化預(yù)處理后濺射二硫化鉬膜層的摩擦學(xué)性能比較穩(wěn)定。
圖9 濕熱存儲后Anodized3+MoS2/Ti復(fù)合膜層的摩擦因數(shù)曲線
3 結(jié)論
通過對鋁合金表面進行陽極氧化預(yù)處理,再在其表面濺射二硫化鉬膜層工藝,研究表明,該復(fù)合鍍技術(shù)能夠有效提高鋁合金表面的潤滑耐蝕性能。主要結(jié)論如下:
(1) 預(yù)處理的氧化膜厚度為15 μm,二硫化鉬膜為2 μm時,復(fù)合膜層在1、5、10、20N載荷下,濕熱存儲2 160h前后,摩擦因數(shù)均小于0.1,摩擦壽命為20 000次以上,且摩擦因數(shù)的變化率不超過10%,摩擦學(xué)性能較好且穩(wěn)定。
(2) 復(fù)合鍍技術(shù)處理后的鋁合金試片表面的腐蝕電位從-0.654V增加至-0.170V,濕熱存儲后, 試片的腐蝕電位降低為-0.369V,復(fù)合膜層具有良好的耐蝕性能,在大氣環(huán)境中放置具有較好的儲存能力。
(3) 鋁合金陽極氧化預(yù)處理后表面濺射二硫化鉬的復(fù)合膜層與9Cr18對偶件磨損機制主要為粘著磨損。
參考文獻
[1] 王曼.2A12 鋁合金硬質(zhì)陽極氧化工藝及復(fù)合自潤滑膜的研究[D].鎮(zhèn)江:江蘇大學(xué),2016.
WANG Man.2A12 aluminum alloy hard anodizing process and composite research of self-lubricating film [ D ].Zhengjiang:Jiangsu University,2016.(in Chinese)
[2] HU N N,GE S H,FANg L.Tribological properties of nano-porous anodic aluminum oxide template [J].J.Cent.South Univ.Technol,2011,18,1004-1008.
[3] 郭清兵,袁海兵,李翠金,等.自潤滑型鋁合金硬質(zhì)陽極氧化膜的摩擦磨損性能[J].表面技術(shù),2010,39(2):21-23.
GUO Qingbing,YUAN Haibing,LI Cuijin,et al.Sliding wear performance of self-lubricating aluminum alloy hard anodic oxidation film[J].Surface Technology,2010,39(2):21-23,37.(in Chinese)
[4] JIA Y,ZHOU H,LUO P,et al.Preparation and characteristics of well-aligned macroporous films on aluminum by high voltage anodization in mixed acid[J].Surface and Coatings Technology,2006,201,513-518.
[5] KIM H S,KIM D H,LEE W,et al.Tribological properties of nanoporous anodic aluminum oxide film [J].Surface and Coatings Technology,2010,205,1431-1437.
[6] 付景國,馬圣林,朱新河,等.固體潤滑劑WS2對鋁合金微弧氧化陶瓷膜摩擦學(xué)性能的影響[J].表面技術(shù),2019,48(7):150-157.
FU Jingguo,MA Shenglin,ZHU Xinhe,et al.Influence of solid lubricant WS2 on the tribological properties of micro-arc oxidation ceramic coating of al alloy [J].Surface Technology,2019,48(7):150-157.(in Chinese)
[7] 劉婉穎,邱宇洪,劉穎,等.納米TiO2對D16T鋁合金微弧氧化膜耐磨性的影響及機理[J].表面技術(shù),2019,48(10):180-189.(in Chinese)LIU Wanying,QIU Yuhong,LIU Ying,et al.Effect and mechanism of nano-TiO2 on wear resistance of micro-arc oxidation film on D16T aluminum alloy[J].Surface Technology,2019,48(10):180-189.
[8] SPALVINS T.A review of recent advances in solid film lubrication[J].Journal of Vacuum Science and Technology A,1987,5(2):212-219.
[9] ARSLAN E,TOTIK Y,EFEOGLU I.Comparison of structure and tribological properties of MoS2-Ti films deposited by biased-DC and pulsed-DC [J].Progress in Organic Coatings,2012,74(4):772-776.
[10] LIU X,WANG L,XUE Q.A novel carbon-based solid-liquid duplex lubricating coating with super-high tribologicalperformance for space applications [J].Surface and CoatingsTechnology,2011,205(8-9):2738-2746.
[11] WANG L L,NIE X Y.Investigation into tribological properties of TD-treated D2 steel for applications in dry machining of aluminum alloy[J].Advanced Materials Research,2011,314-316:263-266.
[12] GOEKE R S,KOTULA P G,PRASAD S V.Synthesis of MoS2-Au nanocomposite films by sputter deposition [J].Office of Scientific & Technical Information Report,2012.
[13] MARTINS R C,MOURA P S,SEABRA J O.MoS2/Ti low-friction coating for gears [J].Tribology International,2006,39(12):1686-1697.
[14] SUN J,DENG J,LI X,et al.Preparation and tribological properties of MoS2-based multiple-layer structured films fabricated by electrohydrodynamic jet deposition[J].Surface and Coatings Technology,2020,384:125334.
[15] ARSLAN E,BüLBüL F,EFEOGLU I.The structural and tribological properties of MoS2Ti composite solid lubricants[J].Tribology Transactions,2004,47(2):218-226.
[16] ARSLAN E,BüLBüL F,ALSARAN A,et al.The effect of deposition parameters and Ti content on structural and wear properties of MoS2 Ti coatings[J].Wear,2005,259(7-12):814-819.
[17] 肖金濤,陳妍,邢明秀,等.工藝參數(shù)對2195鋁鋰合金陽極氧化膜的耐蝕性影響[J].中國腐蝕與防護學(xué)報,2019,39(5):431-438.
XIAO Jintao,CHEN Yan,XING Mingxiu,et al.Effect of process parameters on corrosion resistance of anodizing film on 2195 Al-Li alloy [J].Journal of Chinese Society for Corrosion and Protection,2019,39(5):431-438.(in Chinese)
[18] 李浩.MoS2 基薄膜可控制備及其摩擦學(xué)性能研究[D].蘭州:中國科學(xué)院蘭州化學(xué)物理研究所,2016.
LI Hao.Controllable preparation and tribological performance of MoS2-based coating [ D ].Lanzhou:Lanzhou Institute of Chemical Physics,Chinese Academy of Sciences,2016.(in Chinese)
[19] ZHANG R,CUI Q,WENG L,et al.Modification of structure and wear resistance of closed-field unbalanced-magnetron sputtered MoS2 film by vacuum-heat-treatment[J].Surface and Coatings Technology,2020:126215.
[20] TEKKOUK N,ARBAOUI M,SA?D Abdi,et al.Transition between severe and mild wear of 2024A-T4 anodized aluminum alloy under severe wear conditions [J].J.Korean Phys.Soc.,2020,76(10):899-903.
[21] WANG D Y,CHANG C L,CHEN Z Y,et al.Microstructural and tribological characterization of MoS2-Ti composite solid lubricating films[J].Surface and Coatings Technology,1999,120:629-635.
[22] KIM S K,AHN Y H,KIM K H.MoS2-Ti composite coatings on tool steel by D.C.magnetron sputtering [J].Surface and Coatings Technology,2003,169:428-432.
[23] 李云玉,任西鵬,陳兆祥,等.DLC 薄膜沉積對不同表面形貌的鈦微弧氧化膜層摩擦學(xué)性能的影響[J].表面技術(shù),2019,48(7):112-121.
LI Yunyu,REN Xipeng,CHEN Zhaoxiang,et al.Influence of DLC film deposition on the tribological property of micro-arc oxidation films with different surface morphologies on titanium [J].Surface Technology,2019,48(7):112-121.(in Chinese)
[24] GUILLAUME Colas,AURéLIEN Saulot,DAVID Philippon,et al.Tribochemical competition within a MoS2/Ti dry lubricated macroscale contact in ultrahigh vacuum:A time-of-flight secondary ion mass spectrometry investigation[J].ACS Applied Materials & Interfaces,2018,10(23):20106-20119.
[25] ARSLAN E,TOTIK Y,EFEOGLU I,et al.Comparison of structure and tribological properties of MoS2-Ti films deposited by biased-DC and pulsed-DC[J].Progress in Organic Coatings,2012,74(4):772-776.
[26] LUO Zhuangzi,ZHANG Zhaozhu,LIU Weimin,et al.Tribological properties of solid lubricating film/microarc oxidation coating on Al alloys [J].Transactions of Nonferrous Metals Society of China,2005,15(6):1231-1236.
[27] SALOMON G,DE Gee A,ZAAT J.Mechano-chemical factors in MoSO2-film lubrication[J].Wear,1964,7(1):87-101.
[28] STEWART Thomas B,PAUL D Fleischauer.Chemistry of sputtered molybdenum disulfide films[J].Inorganic Chemistry,1982,21(6):2426-2431.
[29] FUSARO R L.Lubrication and failure mechanisms of molybdenum disulfide films.2:Effect of substrate roughness [R].NASA Technical Paper,1979.
[30] KAY E.The corrosion of steel in contact with molybdenum bisulphide[J].Wear,1968,12(3):165-171.
免責(zé)聲明:本網(wǎng)站所轉(zhuǎn)載的文字、圖片與視頻資料版權(quán)歸原創(chuàng)作者所有,如果涉及侵權(quán),請第一時間聯(lián)系本網(wǎng)刪除。
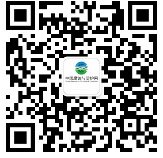
官方微信
《中國腐蝕與防護網(wǎng)電子期刊》征訂啟事
- 投稿聯(lián)系:編輯部
- 電話:010-62316606-806
- 郵箱:fsfhzy666@163.com
- 中國腐蝕與防護網(wǎng)官方QQ群:140808414