鋁合金的應力腐蝕及案例
鋁制焊接容器中使用的鋁和鋁合金主要有工業高純鋁(LG)、工業純鋁(L)和防銹鋁(LF),此外在鍛件、棒材螺栓中還有硬鋁(LY)和鍍鋁(LD)等,在航空航天、船舶、橋梁、大型容器、管道、車輛等領域中都廣泛使用鋁和鋁合金結構材料。多用于空分裝置的冷箱,包裝存儲的料倉。在硝酸生產裝置中,鋁制設備如漂白塔、濃硝貯槽等。小氮肥廠的碳化塔水箱,主要是用純鋁管。
01 鋁合金的耐蝕性能
鋁的耐蝕性基本上取決于在給定環境中鋁的保護膜的穩定性。按介質作用可分為3類:
鋁在pH4~8的介質中容易鈍化,所以,鋁在近中性的水中以及大氣中是非常耐蝕的,但當介質中存在某種陰離子時,會產生點蝕等局部腐蝕。
鋁耐硫和硫化物(如SO2和H2S)腐蝕,在許多有機酸中耐腐蝕,特別是耐無水醋酸腐蝕,但當含水量大于0.2% 及溫度大于50℃時,會發生嚴重的局部腐蝕。
對于純鋁和低強度鋁合金,一般不產生SCC。高強度鋁合金則容易產生SCC。例如 Al-Cu-Mg(2000系列)、Al-Mg-Mn(5000系列),Al-Cu、Al-Mn-Si(6000系列),Al-Mg、Al-Mg-Zn 和Al-Zn、Al-Zn- Mg -Cu(7000系列)等強度較高的鋁合金等。含銅、鎂、鋅量高的鋁合金SCC敏感性最高。
02 鋁合金SCC特征
鋁合金的SCC主要發生含在Cl-的水溶液、濕氣、某些液態金屬、有機溶劑等環境中。鋁合金在大氣中,特別是海洋大氣中和海水中常產生SCC。溫度、濕度、Cl-含量越高,pH值越低,則越易發生SCC。此外,在不含Cl-的高溫水和蒸氣中也會發生SCC。應力升高,SCC敏感性升高。
鋁合金在3.5%(mass) NaCl溶液環境中,呈活化狀態的表面為腐蝕電池的陽極,氧化膜未受破壞的部分保持鈍態為陰極,這樣組成的活化-鈍化電池,形成了小陽極大陰極,很快產生較深的點腐蝕。腐蝕產物體積膨脹,容易使鋁合金因腐蝕產物的楔入效應而形成晶界腐蝕、剝蝕腐蝕乃至SCC。
在NaCl水溶液中,鋁合金的SCC有以下幾個特征:
a.鋁合金的SCC是沿晶的;
b.強度高的鋁合金SCC的敏感性大,這種敏感性按照下列鋁合金系列的順序為:7000系列>2000系列>5000系列>6000系列;
c.溶液溫度升高和腐蝕性增強都會加大鋁合金的SCC敏感性;
d.電化學極化對鋁合金的SCC 敏感性有顯著的影響,并且陽極極化的作用要比陰極極化強。陽極極化時,其SCC機制以陽極溶解為主,陰極極化時以氫致開裂為主;
e.對于同一系列鋁合金,“過時效”處理比“欠時效”處理后的SCC的敏感性要小得多。
03 鋁合金SCC機理
滑移-溶解理論及氫脆理論[1]。Al-Li-Cu-Mg合金在NaCl溶液中SCC敏感性與合金在變形過程中的滑移特征有很大的關系。欠時效狀態下,粒子與基體間呈非共格關系,在滑移過程中形成平面滑移,滑移分布不均勻,容易破壞鈍化膜,增加SCC的敏感性;過時效條件下粒子是半共格的或共格的,形成的滑移分布均勻,不容易破壞鈍化膜,因而提高了合金的SCC抗力。
滑移-溶解理論中包括有經典的陽極溶解、氧化膜(鈍化膜)撕裂、晶界溶質偏析、裂紋尖端拉伸帶不穩定等假說,以及由它們發展出的陽極通道、無沉淀區的優先溶解、晶界上粒子大小與間距以及晶界溶質貧乏、晶界富溶質影響鈍化膜等子模式。
a.經典的陽極溶解。
即SCC是由于沿晶界優先腐蝕的結果,溶解的可以是晶界本身或晶界上的強化相,也可以是晶界附近的溶質貧乏區。如圖4-210a 所示。在這種假說中假定裂紋尖端的擴展受金屬與裂紋中介質間化學反應控制。化學反應是熱活化過程,其活化能對應力是敏感的,因此當裂紋尖端應力場比較大時,其化學反應也就比較快。陽極溶解是一個電化學過程,必須具備以下先決條件:
在晶界區域分布有連續不斷(或部分連續)陽極段;腐蝕介質的選擇性作用;拉伸應力加速陽極部分的溶解,并暴露了新的陽極部分。沿著晶界陽極選擇性地溶解伴隨形成了顯微缺口。當此處應力集中高于材料強度極限時就產生了裂紋的擴展;
b.氧化膜(鈍化膜)撕裂。
假定SCC是由于晶界鈍化膜撕裂引起的,如圖4-210b 所示。高強度鋁合金的SCC過程包含有裂紋尖端局部塑性變形、撕裂氧化膜、去除氧化膜和金屬表面暴露在腐蝕環境中并產生溶解等幾個階段,如圖4-211所示。氧化膜被破壞,而破損處相對其他有膜覆蓋的表面來說是陽極,金屬原子溶解成為離子,形成溝形裂紋。應力集中于裂紋尖端,使附近區域發生塑性變形。這種情況又反過來加快陽極溶解,阻礙膜的再生。同時在裂紋兩邊的有效應力很快消失,可以再生成膜又成為陰極。這樣裂紋在應力作用下,通過電化學過程繼續發展,最終導致金屬開裂;
c.“陽極通道”模式。
由于鋁合金晶界沉淀或晶界區域與晶內有較大電位差(有人測定達100mV),因此就有許多“陽極通道”,SCC就是沿陽極通道腐蝕的過程。由腐蝕產生的微裂紋,在垂直通道的拉應力作用下局部裂紋尖端產生應力集中。應力的作用是張開裂紋、破壞氧化膜、暴露新鮮表面,然后沿新的陽極通道溶解,如此反復進行即形成了SCC。“陽極通道”雖屬經典模式,卻很好地解釋了熱處理與抗SCC之間關系,特別是7075–T73比7075-T6有優越的抗蝕性的原因;
圖4-210 鋁合金SCC基本理論示意圖
圖4-211 氧化膜撕裂過程示意圖
d.“無沉淀區優先溶解”和“晶界上粒子大小、間距”子模式。
沉淀相之間形成無沉淀區(precipitate-free zone,PFZ),PFZ中的溶質濃度小、強度低,在應力作用下首先滑移,鈍化膜被撕裂并使PFZ溶解。Al-Zn-Mg合金中SCC速度受晶界處MgZn2粒子在鋁固溶體中的溶解量、遷移速度控制。因此,高強鋁合金SCC過程就是應力加速晶界處MgZn2粒子間鋁固溶體的溶解過程,晶界上粒子越密,抗SCC性就越差。反之,如粒子大而且間距寬,抗蝕性就好。過時效處理正是為獲得后一種顯微組織;
e.拉伸帶不穩定性。
假定在腐蝕裂紋尖端頭部能形成一個很薄、尺寸又很小的“自由帶”,它能切斷開裂的電橋作用。在拉應力作用下這個帶能被拉伸到不穩定程度。如果材料在腐蝕介質中,臨界應變值就會大大減小,自由帶也就很容易被破壞,抗蝕性下降。
自由帶圍繞較大的非共格粒子形成,自由帶尺寸等于粒子間距或者等于晶界沉淀的間距,當過時效使粒子長大,間距加寬時,這個“自由帶”也就加寬,抗SCC性隨之提高;
f.晶界區溶質偏析假說。
Cu、Mg和Zn 等對Al的電極電位有明顯影響,圖4-212為這種影響的示意圖。Zn、Mg的加入會使Al 的抗蝕性變差,Al-Zn-Mg 合金在固溶處理、時效之后在距晶界 0.5μm區域會產生溶質元素濃度差。在466℃/0.5h 水淬+180℃/0.5h 時效后,晶界處Zn的濃度幾乎與晶內一致,隨時效時間加長(180℃/7h)晶界處Zn的濃度減少,因此抗蝕性也就提高。Mg的變化也是如此,只是它對抗蝕性的影響比較小一些。
圖4-212 添加元素對純鋁電極電位影響
圖4-213 在氯化物溶液中裂紋尖端反應
晶界溶質的偏析對抗蝕性影響不僅在對晶界區域電化學特性的改變,更主要的是影響了氧化膜特性。純鋁氧化膜能有效地抵制氯的離解與穿透,但當各種合金元素進入到氧化膜后就大大降低了它的保護性能。
特別是Mg在中性和弱酸性溶液中比純鋁更容易溶解。因此,能使晶界處Zn、Mg濃度減少的熱處理對合金的抗蝕性都有利。在Al-Zn-Mg合金中加入Cr 或Cd 時能使晶界處Zn、Mg 含量明顯減少,在PFZ 內形成很陡的濃度變化剖面,因此抗SCC性能明顯改善。
g.氫脆理論。
假定SCC是由于材料吸附了氫并弱化了晶界而造成的,如圖4-210c所示,化學反應產生H是氫脆的先決條件。當Al在氯化物溶液中,其裂紋尖端的反應如圖4-213所示。
在拉伸應力作用下,晶界與表面相交處的水分與鋁合金反應生成活性原子H。H原子進入晶格中,沿晶界優先偏聚,導致晶界強度下降引起開裂。當合金經過人工時效處理或者在NaC1 溶液中加入HCl及As2O3時,合金的SCC敏感性增加。HCl使腐蝕電流密度和析氫量增加,H在腐蝕反應過程中進入合金中從而造成金屬力學性能降低。
氫對SCC有3種機理:
ⅰ。氫能使晶界的結合強度大大降低,弱化晶界,造成晶間斷裂。應力的作用是使金屬與氫的交換更容易,并促使氫沿晶界擴散。這種理論能很好地解釋在真空中已經氫脆材料在應力作用下能保持一段時間,塑性可以恢復,以及脆化了的試樣斷裂時有氫逸出等現象;
ⅱ。開裂是由氫壓力過高造成的。當裂紋尖端的氫一旦達到臨界含量,其壓力會使金屬機械破環,造成裂紋擴展。當空穴中的原子H形成H2時所產生的壓力足以使金屬開裂;
ⅲ。氫在晶界處降低晶界溶解的活化能,從而使晶界更容易被溶解。
在不同條件下導致SCC的主要作用機制可能發生變化。環境介質、預滲氫時間和極化電位都對SCC有影響。在干燥空氣中不發生SCC,而在潮濕空氣中發生SCC。在潮濕空氣和陽極極化條件下,鋁合金的SCC機理是以陽極溶解為主,氫幾乎不起作用;延長預滲氫時間可加速鋁合金的SCC。在預滲氫或陰極極化條件下,氫脆起主要作用。
從電位方面考慮,在高于臨界電位的極化下,合金的SCC 屬陽極溶解型,在足夠低(<-l000mV SCE)電位下,合金的SCC屬氫脆型,中間電位的SCC 屬混合型。
晶界沉淀往往作為陽極,使SCC 伴有晶界沉淀優先溶解的傾向。有人認為7xxx 系列鋁合金的SCC 機理包含氫脆,原因是SCC對H滲透具有敏感性。而且,在潮濕環境中預充氫使合金延伸率下降。位錯、空穴引起的扭曲晶格、固溶體中的Mg和相沉淀等都是合金中H 的陷阱點。
隨著應力強度的增加,SCC擴展時,發生了從陽極溶解到氫脆的過渡轉變。溫度與KISCC間的關系表明,在裂紋擴展第1階段,主要以陽極溶解模式為主;在裂紋擴展第2階段,主要是氫脆為主。
綜上所述,鋁合金SCC機理最基本的是陽極溶解理論和氫脆理論。前者對解釋2xxx系合金的SCC更合適,而對7xxx 系合金多用氫導致開裂理論來說明。
除了鋁合金SCC的陽極溶解和氫脆2種機理外,有人還提出一些理論[2]:
a.SCC的無位錯區模型。當裂紋尖端應力強度因子(Local Stress Intensity Factor)大于臨界值ke 時才會在裂紋尖端發射位錯,使裂紋尖端前存在DFZ。在這種力的作用下,裂紋沿晶界而不是沿鄰近滑移面擴展;
b.“Mg-H”復合體理論。由于7000系鋁合金的SCC裂紋擴展一般沿著晶界進行,因此晶界的化學成分必將對合金的SCC行為有重要的影響。晶界Mg偏析,由于Mg和H相互作用而易形成“Mg-H”復合體,氫在晶界上的偏聚將降低晶界的結合能,從而促進了裂紋的擴展。
04 SCC的影響因素
鋁合金SCC特征是晶間破裂,這說明鋁合金SCC與晶間腐蝕有關。
a.合金元素。
鋁中加入合金元素主要是為了獲得較高的力學、物理性能或較好的工藝性能,靠合金化的方法顯著提高鋁耐蝕性能的可能性較小,一般鋁合金的耐蝕性很少能超過純鋁。能使鋁強化的元素主要有Cu、Mg、Zn、Mn、Si等;補加的元素有Cr、Fe、Ti等;為特殊目的而少量加入的有Be、Bi、B、Pb、Ni、P、Zn、Sn、Sb等。
鋁合金的耐蝕性與合金中各種相的電極電位有很大的關系。一般基體相為陰極相,第二相為陽極相的合金有較高的耐蝕性;若基體相為陽極相,第二相為陰極相,則第二相電極電位越高,數量越多,鋁合金腐蝕越嚴重。鋁合金中各種常見相的電極電位列于表4-64。
表4-64 鋁合金各相在NaCl-H2O2 溶液中的電極電位
由表中數據可見,與純鋁相比,含鋅及鎂的固溶體為陽極,而含銅的固溶體為陰極;因此,Al-Mg和 Al-Mn 合金具有較高的耐蝕性,而Al-Cu合金耐蝕性能較差。
高強度鋁合金抗SCC能力受化學成分和顯微組織控制。如Al-Zn-Mg-(Cu)合金峰值時效敏感性比過時效大,而Al-Cu基合金欠時效比峰值時效易發生SCC。
Mg和Zn的含量越多,晶界沉淀越多,PFZ越窄,則SCC 敏感性越大。
添加微量Sc可提高Al合金的耐剝蝕性和力學性能,含Zr的鋁合金可提高抗SCC的性能,Al-Li,Al-Li-Zr,Al-Mg-Li-Zr合金抗SCC的能力都很強。高強鋁合金中添加質量分數0.05%~0.15% Zr能促進η′相的析出,合金中含有Sc和Zr可加速Al3(Sc1-x,Zrx)和Al3Sc顆粒沉淀,能提高合金的耐蝕性。T76處理的η相顆粒主要以分開的形式排列在晶界處,PFZ狹窄(20nm~35nm),因此可提高強度性能。
Sc、Ni、Ce的加入能凈化微結構,阻礙再結晶;而Ni能促進晶格的生長,因此C912系列合金的抗SCC 性有所提高。
Si與Al的電位雖然相差甚遠,但在雙相合金中抗蝕性能仍然很好,這是由于有氧存在或在氧化介質中,在合金表面生成有保護性的氧化膜緣故;
b.熱處理制度的影響[3,4]。
熱處理工藝的不同導致了7000 鋁合金組織參數的微小變化,其SCC敏感性會發生大幅度波動。常見的熱處理工藝主要有固溶處理、時效處理等,而時效處理對合金SCC敏感性影響較大。
峰值時效的影響。峰值時效后,晶界組織對SCC和剝落腐蝕十分敏感。尤其是在有Cl-存在的情況下,厚件的短橫向SCC敏感性十分明顯。另外,這種狀態下存在著嚴重的Mg偏析,很有可能是由于Mg-H作用導致合金的SCC敏感性較高。
雙級時效的影響。雙級時效后合金晶界上分布著斷續粗大的沉淀相,而這種相是H的陷阱,減少H在晶界上的偏聚,從而降低了合金的SCC敏感性。但這種粗大的相較大幅度地降低合金的強度、塑性等。因此,雙級時效并不是降低鋁合金SCC敏感性的理想途徑。
回歸再時效(Retrogression and Re-aging,RRA)處理的7xxx系列鋁合金,晶界內的MgZn2保持精細分布,從而降低SCC 敏感性。
“雙峰”時效的影響,第二峰狀態下合金SCC敏感性低。
在潮濕空氣和溶液環境中7xxx 系列峰時效T651的SCC門檻應力最小,SCC最敏感,欠時效T7651次之,過時效T7351耐SCC最好,但強度卻下降約10%;
c.預應變的影響。
時效前進行拉伸或壓縮變形可以提高合金的SCC抗力。通常冷變形2.5% SCC抗力會增加3-4倍;
d.外部環境對7000系合金SCC敏感性的影響[4-6]。
通常干燥的氣體(如H2、N2、O2、Ar等)或干燥空氣都不會引起鋁合金的SCC,但水蒸氣存在的情況下則不然,在水蒸氣中通入O2對SCC敏感性有重要影響,7050-T7451合金的SCC敏感性隨著O2含量的增加而提高。
水溶液的影響。蒸餾水對鋁合金的SCC幾乎沒有影響。但是當水溶液中的存在Cl-、Br-和I-等離子時則能加速鋁合金在溶液中的SCC的裂紋擴展速率。它們引起的SCC的擴展速率比其他陰離子的高2-3個數量級。一般認為Cl-、Br-和I-能加速縫隙腐蝕和晶間腐蝕從而促進了SCC。在水溶液中很少有陽離子對SCC的裂紋擴展產生影響,但是Hg+和H+離子除外。Hg+能引起較快的晶間腐蝕,而很可能因為Hg沉積而引起SCC,H+能夠阻止和防止SCC的陰極保護。
A13+通過水解反應生成AlOH2+,AlOH2+再和Cl-反應,又分別生成A1Cl2+和A1(OH)Cl+,然后它們再反復進行水解反應,隨著溶液逐漸呈酸性,裂紋表面生成Al(OH)2Cl 和Al(OH)3·H2O 之類的凝膠體物質。裂紋側壁上一旦形成這類腐蝕生成物的“鹽層”,就會發生鈍化,溶解反應只能集中在裂紋尖端,保持了裂紋尖端形狀的銳利度,具備了所謂由側壁抑制溶解的“電化學刀的條件”。這不僅是構成陽極溶解機理的前提條件,而且在氫脆機理中又起到H 的吸附和濃化局部介質集中在裂紋尖端的作用。
pH值,對7050-T7451Al 合金在溶氧的3.5%(mass)NaCl溶液中,pH<4 時,鈍化膜遭破壞,不能自動修復,晶間腐蝕將促進裂紋形成和長大;4<pH<10時,將產生點蝕,生成裂紋,增加SCC 敏感性;pH>10時,試樣遭受均勻腐蝕,極少發生SCC。然而,在去氧的3.5%(mass)NaCl 溶液中,幾乎不發生SCC。
05 防止鋁合金SCC措施
a.加入微量Mn、Cr、V、Zr等元素,改善SCC性能;
b.用熱處理方法調整鋁合金的組織狀態,減少Zn、Mg在晶界的偏析以及使晶界沉淀 MgZn2 粗糙,顆粒大,減輕基體中晶界附近H原子聚集。晶界內的MgZn2保持精細分布。從而降低SCC 敏感性;
c.采用滾壓或噴丸的方法使表面產生壓應力,消除表面殘余拉應力;
d.表面涂以保護層,隔離腐蝕介質。
06 高強鋁合金的SCC測試方法
SCC實驗可按GJB1742[7]附錄B“鋁鎂系合金抗應力腐蝕試驗方法”進行。實驗介質為3.5%(mass)NaCl溶液,實驗溫度35℃±1℃。剝落腐蝕按附錄A“鋁鎂合金抗剝落腐蝕試驗方法”進行。
實驗介質: 1.0M NH4Cl,0.25M NH4NO3,0.01M(NH4)3Cit,3g·L-1 H2O2,pH值調至5.2-5.4。溫度65℃,實驗時間24h。
a.恒載荷法。
該法的SCC評定指標為SCC壽命,還可求出初始應力對SCC的影響;
b.恒應變法。
按照ASTM G44[8],在3.5%(mass)NaCl 溶液中交替浸漬以評定金屬和合金的耐SCC性。試樣浸漬10min,然后從溶液中取出停放50min,重復上述步驟直至斷裂。鋁和鐵合金一般需要20-90d甚至更長,由合金在鹽水中的耐蝕性而定;
ASTM G64[9]為熱處理鋁合金耐SCC的分類標準。該標準適用于鍛造2xx x,6x xx 和7xx x 系列熱處理鋁合金。試樣按ASTM G44交替浸漬,分4個等級進行評定。ASTM G47[10]為高強鋁合金產品SCC敏感性的測定方法,適用于高強2xxx(18%-70%(mass)Cu)和7xxx(0.4%-2.8%(mass)Cu)鋁合金產品,特別是短橫取向(Short Transverse Direction)拉伸試樣在恒應變載荷下測定,C形環試樣在3.5%(mass)NaCl溶液中交替浸漬測試,其評定方法為宏觀裂紋和金相顯微分析;
c.SSRT法。
通常使用的應變速率范圍為10-4-10-8s-1,持續拉伸使表面鈍化膜反復破裂,出現滑移臺階。然后,裸露金屬表面發生活化溶解形成裂紋。
d.電子顯微鏡輔助分析方法。
用掃描電鏡分析斷口形貌,評定材料的耐SCC性。利用透射電鏡可研究材料微觀結構與材料SCC性能之間的關系;
E.電導率方法。
電導率可用于材料分類,熱處理狀態不同,電導率會發生變化,而熱處理條件對材料的SCC有影響,因此,電導率可作為評定材料耐SCC性能的指標之一。此法只是一種正在嘗試的評定高強鋁合金SCC敏感性的輔助方法,因此一般很少采用這種方法;
f.電化學測試方法。
在氯化物水溶液中,時效Ag-Zn-Mg-Cu合金對沿晶環境所致斷裂(Environment assisted Cracking,EAC)是敏感的,裂紋生長與電極電位相關。實驗結果表明,裂紋生長速度da/dt 隨著應用電極電位(Applied Electrode Potential,APP)的增大而增加。
各種SCC測試方法的評價指標如表4-65所示。
表4-65 SCC測試方法的評價指標
案例1.鋁合金管材破裂分析[11]
7075-T6鋁合金管材使用數月后,發現少數管材破裂。裂紋由表面開始沿受拉應力方向擴展,當裂紋達到一定尺寸后,擴展方向改為沿管材縱向撕裂(以下稱主裂紋),如圖4-216a 中(l)區和圖4-216b 所示。圖4-217為主裂紋的斷口,其上可見黑色和灰色相間的帶狀區在斷口的匹配面上對稱形分布,表明了裂紋的擴展過程。在斷口的起始部分和擴展區,表面均有明顯的覆蓋物。這種斷口特征,與SCC斷的特征相同。斷口表面覆蓋物的能譜分析結果如表4-66,可見,覆蓋物中有Cl元素的存在。
圖4-216 7075-T6 鋁合金管材破裂和表面裂紋形貌
圖4-217 斷口的匹配面上對稱形分布
表4-66 斷口上覆蓋物能譜分析結果
取未完全斷開的主裂紋,在表面、縱向和橫向3個顯微觀察,圖4-218a 為管材表面裂紋,為連續不斷的腐蝕坑和須狀的枝叉,延伸部分是被腐蝕顯現出的晶界;圖4-218b 為主裂紋縱向顯微組織,裂紋在擴展過程中伴隨腐蝕產物出現,沿著晶界與擠壓金屬流變相同的方向延伸;圖4-218c為主裂紋橫向顯微組織,其擴展裂紋呈爪狀。主裂紋的三向顯微組織反映出SCC特征。
圖4-218 裂紋擴展形貌和顯微組織
測定擠壓管材的應力狀態,試樣長為340~380 mm。將管材的橫截面等分為5個區,由測試數據可知,擠壓管材在T6 狀態下,表面應力分布很不均勻,有1/5的區城為壓應力,其他為拉應力,而且最高達22.9 MPa。這種表面狀態具備了產生SCC的力學條件。
研究人員將正在發生SCC的試樣,迅速投人液氮中冷凍,然后打開裂縫,緩慢溶化,用試紙檢驗pH 值的變化,結果裂縫尖端內溶液的pH值為3.5。
案例2.5A06鋁合金焊接接頭裂紋失效分析[12]
5A06鋁合金為Al-Mg系防銹鋁,具有較高的強度、化學穩定性和良好的焊接性等特點,是防銹鋁合金中的典型合金,在一些需嚴格防火的壓力容器等得到了廣泛應用。
某5A06防銹鋁合金壓力容器產品焊接后使用一段時間出現裂紋,裂紋1為橫貫焊縫的長裂紋,裂紋2較短,其長度為從內孔邊緣到達焊縫處。為了分析裂紋產生的原因,將產生裂紋的殼體和支柱局部取樣后進行分析,見圖4-219。殼體材料為軋制成型的鋁合板,經過卷圓成型;支柱材料經熱擠壓成型后機械加工而成。
圖4-219 試件裝配、焊接及裂紋存在部位示意圖
殼體與支柱通過焊接連接在一起,其中包括2條焊縫,如圖4-215中的外部焊縫和內部焊縫,兩焊縫均采用鎢極氬弧焊進行焊接。用手工鎢極氬弧焊打底,然后采用鎢極氬弧焊進行焊接,焊接電流150~160A,電壓12~15V。焊縫余高3mm,焊后采用機械加工的方法去除余高并磨平。內部焊縫不開坡口,焊接電流140~150A,電壓12~15V。由于結構的影響,內部焊縫采取斷續焊接,焊后未做清理。焊后產品整體進行200℃退火處理。
對殼體材料的橫截面和軋制面進行了金相組織分析見圖4-220。可見殼體組織較細小,晶粒大小不很均勻,平均晶粒尺寸為5~20μm,并且材料中存在一些夾雜物。支柱金相如圖4-221所示,可見支柱組織沿擠壓方向存在粗大的帶狀組織。
對外部焊縫進行金相觀察,焊縫宏觀照片如圖4-222所示,a為外部焊縫的整體形貌、b為焊縫熔合區、c為焊縫組織,由圖可以發現焊縫組織細小,較為均勻,熱影響區組織較粗大。
圖4-220 殼體組織(a)橫截面(b)軋制面
圖4-221 支柱組織(a)擠壓方向粗大的帶狀組織(b)垂直于擠壓方向
圖4-222 試件焊縫金相照片(a)焊縫全貌(B)熔合區金相照片(c)焊縫金相照片
裂紋的宏觀特征如圖4-223所示。發現支柱材料中心孔徑缺陷處為裂紋源,向殼體方向發展。裂紋呈斷續狀,穿過材料中的缺陷部位見圖4-224,圖4-224e可以發現母材晶界存在析出相,為裂紋擴展提供了有利條件;圖4-224f可以發現材料中存在缺陷,裂紋會在缺陷處產生并沿著晶界及缺陷的部位進行擴展
圖4-223 裂紋擴展方向
圖4-224 裂紋擴展特征
將試件沿裂紋1拉斷,斷口宏觀照片如圖4-225。圖4-225a中可見截面中大部分為陳舊性裂紋,殼體裂紋已通過外部焊縫,支柱裂紋已擴展至下部邊緣。支柱斷口存在大量的二次裂紋,見圖4-225B,可見支柱斷口中存在粗大的纖維狀,取向明顯。殼體斷口較細,焊縫及熱影響區斷口也均勻細致。
圖4-225 斷口宏觀
圖4-226a、b為殼體斷口微觀形貌,晶間存在大量的微觀裂紋,結合強度較低,斷面有腐蝕產物存在。圖4-226c、d為支柱的微觀斷口形貌,為粗糙的柱狀斷口,存在二次裂紋和腐蝕坑存在。圖4-226c、f為人為斷口的微觀形貌,斷口中以韌性斷裂為主,存在大量的撕裂韌窩。
由宏觀和微觀斷口分析可知,裂紋啟裂于支柱內孔邊緣夾雜物處,并沿徑向擴展,粗大的支柱材料組織,晶間結合強度較低,為裂紋擴展提供了條件。
圖4-226 斷口微觀形貌
支柱所處部位決定了內部焊縫只能斷續焊接,存在應力集中。裝配過程中,支柱圓弧面與殼體的圓弧面配合出現偏差,造成兩試件間距有較大的偏差,焊后產生較大的應力集中。裂紋均起源于焊縫端部,產生微裂紋后,在應力集中的作用下,引起裂紋的擴展。
5A06鋁合金焊后在280~305℃進行完全退火,可以消除殘余應力。支柱與殼體焊接后,產品整體進行了200℃的退火處理,因此,設備焊接后進行的整體退火溫度偏低,未使焊接殘余應力徹底釋放也會引起裂紋的產生。
參考文獻
[1] 趙英濤。鋁合金應力腐蝕開裂假定機理的文獻綜述[J].材料工程,1993,44(9):1-6
[2] 袁勁松,秦熊浦。 鋁鋰合金的應力腐蝕特征[J].腐蝕與防護,1999, 20(9):389-391
[3] 孫志華,劉明輝,張曉云。時效制度對 Al-Zn-Mg-Cu鋁合金應力腐蝕敏感性的影響[J].中國腐蝕與防護學報,2006,26(4):232-236
[4] 陳小明,宋仁國。7000系鋁合金應力腐蝕開裂的研究進展[J].腐蝕科學與防護技術,2010,22(2):120-123
[5] 劉繼華,李 荻,張佩芬。氫對LC4高強鋁合金應力腐蝕斷裂的影響[J].中國腐蝕與防護學報,22(5):53-55
[6] 杜愛華,龍晉明,裴和中。等。高強度鋁合金應力腐蝕研究進展[J].中國腐蝕與防護學報,2008,28(4):251-256
[7] GJB 1742-1993.艦用LF15、LF16鋁合金板材規范[S]
[8] ASTM G44-1999(2013)。Standard Practice for Exposure of Metals and Alloys by Alternate Immersion in Neutral 3.5 % Sodium Chloride Solution[S]
[9] ASTM G64-1999(2013)。Standard Classification of Resistance to Stress-Corrosion Cracking of Heat-Treatable Aluminum Alloys[S]
[10] ASTM G47-2020. Standard Test Method for Determining Susceptibility to Stress-Corrosion Cracking of 2XXX and 7XXX Aluminum Alloy Products[S]
[11] 侯繹,張錫龍。 7075 鋁合金T6 狀態管材破裂分析[J].輕合金加工技術,2002,30(11):42-45
[12] 張紅霞,劉曉晴,閆志峰。等。 5A06鋁合金焊接接頭裂紋失效分析[J].材料工程,2013,64(3):27-31+37
免責聲明:本網站所轉載的文字、圖片與視頻資料版權歸原創作者所有,如果涉及侵權,請第一時間聯系本網刪除。
相關文章
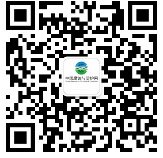
官方微信
《中國腐蝕與防護網電子期刊》征訂啟事
- 投稿聯系:編輯部
- 電話:010-62316606-806
- 郵箱:fsfhzy666@163.com
- 中國腐蝕與防護網官方QQ群:140808414
點擊排行
PPT新聞
“海洋金屬”——鈦合金在艦船的
點擊數:7130
腐蝕與“海上絲綢之路”
點擊數:5741