鋁基復合材料具有高比強度、高比模量、良好的阻尼性能以及較低的膨脹系數[1~3],在航空、航天、航海和尖端武器等高科技領域顯示出十分廣闊的應用前景,一些種類的鋁基復合材料已經走向工業化規模的應用。按照增強相的添加方式,鋁基復合材料的制備方法可分為外加法和原位自生2種。由于原位自生法克服了外加法存在的應力集中、顆粒表面易污染,顆粒與基體界面結合力差等問題,已逐漸成為鋁基復合材料制備技術的研究熱點。其中,原位自生TiB2顆粒增強鋁(TiB2/Al)基復合材料因其具有優異的力學性能和物理性能、較低的生產成本、顆粒強化效果顯著等特點受到了普遍的重視。目前,原位自生TiB2/Al基復合材料的制備方法主要有:放熱彌散法[4]、接觸反應法[5]、混合鹽反應法[6~8]等。放熱彌散法因預制塊中的原位自生顆粒尺寸和含量難以控制,且稀釋重熔的過程中原位自生顆粒難以分散均勻,在實際生產應用中受到限制。采用接觸反應法制備的TiB2/Al基復合材料所形成的增強顆粒尺寸較大,且反應過程難以控制。混合鹽反應法制備的TiB2/Al基復合材料,制備工藝簡單、可操作性強,且自生顆粒尺寸小,有利于材料液態成型,適合于大規模工業化生產。
上海交通大學材料科學與工程學院特種材料研究所多年來潛心研究采用混合鹽反應法原位合成TiB2/Al基復合材料并攻克了熔體反應控制、熔體純凈化處理等關鍵難題[9]。所制備的TiB2顆粒在熔體中直接反應生成,其尺寸細小(納米和亞微米級),外形圓整,且顆粒與基體間具有良好的相容性。顆粒與基體界面干凈、無任何界面反應物,使得該材料具有高強度、高模量、良好鑄造性,實現了大型構件和復雜構件的直接鑄造成形[10,11]。同時,具有良好塑性成形性和機械加工性能的變形鋁基復合材料通過軋制、鍛造、擠壓工藝可實現各種零件近凈成形[12]。近年來,增材制造用原位自生TiB2/Al基復合材料粉末、線材以及大型構件也逐漸在復雜結構輕量化中發揮作用。在此基礎上,原位自生TiB2/Al基復合材料具有良好的切削加工性和可焊性,進一步擴大了此類鋁基復合材料的應用范圍。目前,此類原位自生TiB2/Al基復合材料的應用范圍已涉及航空、航天、航海、武器裝備、軌道交通、汽車輕量化等領域[9]。
然而,原位自生TiB2/Al基復合材料中增強相的存在使其內部組織結構不均勻,TiB2增強相與基體之間的電位差、雜質相的析出、增強相與基體界面的高密度位錯,以及材料制備過程中形成的缺陷等問題,導致復合材料在使用過程中易形成腐蝕微電池,而遭受點蝕、剝蝕、磨蝕等不同形式的破壞[13,14], 極大地限制了復合材料在潮濕空氣、海洋等腐蝕環境中的有效應用。這顯然不能滿足原位自生TiB2/Al基復合材料日益增長的應用需求。因此,探索原位自生TiB2/Al基復合材料的表面防護方法,提高其耐腐蝕性能,具有重要的應用價值。同時,原位合成TiB2/Al基復合材料腐蝕與防護的機理也是材料科學中的一個重要研究方向。
本文對國內外原位自生TiB2/Al基復合材料的表面處理及腐蝕防護技術現狀作簡要評述,包括原位自生TiB2/Al基復合材料的腐蝕機理研究、原位自生TiB2/Al基復合材料表面處理方法(主要包括:陽極氧化+稀土轉化膜技術、低溫熔鹽沉積技術、微弧氧化技術、激光表面合金化技術、冷噴涂等)與防護效果、未來表面改性技術在相關重點領域的展望等方面。
1 原位自生TiB2/Al基復合材料的耐蝕特點
原位自生TiB2/Al基復合材料作為一類極具應用價值的金屬基復合材料,其耐腐蝕性能也是影響進一步應用的重要因素。因此,詳細了解TiB2/Al基復合材料的抗腐蝕性能,研究其在特定環境中的腐蝕機理,掌握復合材料腐蝕原因及影響腐蝕的相關因素,對于推進新材料產業化具有重大現實意義。尤其是準確掌握此類復合材料的腐蝕特性,有利于制定切實可靠、經濟有效的腐蝕防護工藝。
例如,Sun等[15]借助電化學阻抗和動電位極化技術,對原位自生TiB2/A356復合材料(主要組成相為α-Al、Si和TiB2)電化學腐蝕行為進行研究,通過對比A356合金(主要成分為Al-7.0%Si-0.35%Mg)、5%TiB2/A356 (質量分數,下同)和15%TiB2/A356復合材料試樣在3.5%NaCl (質量分數,下同)溶液中的電化學阻抗譜(圖1a[15]),發現復合材料表面天然氧化膜層的電阻隨著材料中顆粒含量增加而降低,材料腐蝕速率隨顆粒含量的增加而逐漸增大。此外,從Bode圖(圖1b[15])中可以更清晰比較出,復合材料的阻抗比基體低近1個數量級。因此,認為復合材料中的TiB2和與其聚集在一起的短棒狀Si (圖1g和i[15])能夠破壞材料表面氧化膜的完整性,削弱其對材料基體的保護作用,而TiB2顆粒與活性Al基體間的微電偶腐蝕是導致該復合材料耐蝕性差的主要原因。極化曲線的測試結果(圖1c[15])進一步說明在3.5%NaCl溶液中復合材料比基體具有更高的腐蝕敏感性,且其耐蝕性隨著顆粒含量的增加而降低。極化腐蝕試樣表面形貌(圖1d~i[15])揭示出復合材料的電化學腐蝕主要發生在有大量TiB2顆粒聚集的晶間位置,且沿晶間區域延伸到Al基體內部。
圖1 A356鋁合金和不同TiB2含量復合材料的Nyquist圖、Bode圖、極化曲線以及極化后試樣腐蝕形貌[15]
在此基礎上,Huang等[16]系統研究了原位自生TiB2/7050Al基復合材料在不同pH值(pH = 4、6、7和10) NaCl溶液中的耐蝕性行為。從Nyquist圖(圖2a[16])可見,復合材料耐腐蝕性隨著pH值降低而變差,酸性和堿性條件都會降低復合材料抗腐蝕能力。但在pH = 7的NaCl溶液中,復合材料阻抗遠大于其他條件,腐蝕程度最低。極化曲線(圖2c[16])結果表明腐蝕電位(Ecorr)隨著pH值增加而降低。同時,腐蝕電流密度(icorr)在pH = 7時呈現最小值,表明復合材料在中性NaCl溶液中的腐蝕性最小。在酸性和堿性溶液中,腐蝕電流密度都增大,腐蝕行為加劇。靜態浸泡測試結果顯示,復合材料在酸性NaCl溶液中由于H+作用而表現出明顯腐蝕現象;在堿性NaCl溶液中,OH-對于Al基體的強化學溶解也會使復合材料產生明顯腐蝕;在中性或近中性NaCl溶液中,復合材料腐蝕性最小。在復合材料中,點蝕傾向于在TiB2顆粒富集帶發生,TiB2顆粒主要作為有效的電偶陰極相,增加復合材料腐蝕速率。不同pH值環境下其腐蝕行為也并不相同,在酸性環境中(圖2d~f[16])點蝕是主要的腐蝕形式;在中性環境中(圖2g[16]),點蝕和均勻腐蝕會形成;而在堿性環境中(圖2h和i[16])則主要以均勻腐蝕為主。
圖2 原位自生TiB2/7050Al在不同pH值溶液中的Nyquist圖、Bode圖、極化曲線及不同pH值條件下靜態浸泡8 d后試樣腐蝕形貌[16]
所以,原位自生TiB2/Al基復合材料在NaCl溶液中極易發生腐蝕,是由于TiB2顆粒與Al基體之間的微電偶反應。因此,研發并采用抑制TiB2和Al之間電偶腐蝕的表面技術是提高復合材料耐蝕性的關鍵。目前,鋁基復合材料的表面處理研究大多集中在SiC/Al體系,而對于TiB2/Al體系的研究還有待于進一步的發展。由于TiB2顆粒具有一定導電性,其亞微米粒徑比微米級SiC顆粒尺寸小得多,將現有鋁基復合材料防護方法直接應用于TiB2/Al基復合材料將存在一定的問題。對于不同種類以及在不同使用環境中的復合材料,相同的防護方法往往表現出迥異的防護效果,并且單一的方法可能存在一定局限性。因此,研究行之有效的防護方法以提高原位自生TiB2/Al基復合材料的耐蝕能力已經成為該領域一項重要工作。
2 陽極氧化和稀土轉化膜技術
鋁合金陽極氧化是將鋁合金作為陽極置于適當的電解液當中,并向鋁合金施加陽極電流,使其表面生成一層蜂窩狀非晶態Al2O3膜層。由于原位自生TiB2/Al基復合材料組織的復雜性特點,使得氧化膜的均勻性和完整性受到很大影響。因此,單一陽極氧化處理可能無法為原位自生TiB2/Al基復合材料提供良好耐蝕性保護。另一方面,陽極氧化膜層孔隙率較高,采用合適的封孔工藝是進一步提高其耐蝕性的重要方法。Hinton等[17]發現7075鋁合金在含有少量CeCl3的NaCl溶液中腐蝕速率顯著下降,這一現象引起了科研工作者們對鋁合金表面稀土轉化封孔膜研究的興趣。Mansfield等[18~20]率先展開鋁基復合材料表面稀土轉化封孔膜的研究,為復合材料應用尋求了一條很有應用價值的防腐途徑。Yu等[21]采用稀土鹽對SiC/6061Al陽極氧化膜進行封閉處理,發現稀土封孔處理氧化膜與鉻酸鹽封閉處理氧化膜的耐腐蝕性具有可比性,且稀土鹽價格低、無毒害作用。這些優勢使得該處理工藝具有很大應用潛力。Hu等[22]研究了Al18B4O33/6061Al浸入添加不同含量H2O2的CeCl3溶液中制備鈰轉化膜層的組織形貌和成分,并采用電化學方法比較各轉化膜抗腐蝕效果,發現轉化膜層主要由Ce4+化合物組成。該膜層抑制了復合材料在含Cl-溶液中的陽極反應,顯著改善了材料耐蝕性。
對于原位自生10%TiB2/A356復合材料,利用陽極氧化和稀土轉化封孔處理2種途徑可提高其耐蝕性[23]。復合材料陽極氧化后表面Al2O3膜形貌如圖3a和b[23]所示,氧化膜呈現多孔結構,孔尺寸在20 nm左右。該Al2O3膜并不平整,局部表面存在一些凹坑(A)和孔洞(B) (見圖3a[23])。這些凹坑和孔洞主要是由于TiB2顆粒和Si粒子從氧化膜表面脫離造成。此外,多孔結構也在氧化膜凹坑中形成,即陽極氧化膜可以繞過一些粒子或聚集物向復合材料內部生長。經過化學沉積后的鈰轉化膜形貌如圖3c和d[23]所示,許多球形顆粒覆蓋了整個氧化膜表面,顆粒尺寸都在100 nm左右,而且大顆粒之間存在許多尺寸較小顆粒。化學沉積法得到的球形顆粒不但封閉了氧化膜多孔結構,同時有效地覆蓋了氧化膜表面大部分凹坑、裂紋和孔洞,從而在復合材料表面獲得一層由陽極氧化膜和鈰轉化膜所共同組成的完整復合防護膜層。此稀土鈰轉化膜主要成分為Ce2O3、Ce(OH)4和Ce(OH)3等(圖3e[23])。
圖3 原位自生TiB2/A356復合材料氧化膜形貌,陽極氧化膜表面化學沉積鈰轉化膜形貌,復合材料表面鈰轉化膜的XPS Ce3d譜,復合材料、表面陽極氧化膜以及鈰轉化膜極化曲線,以及鈰轉化膜形成示意圖[23,24]
原位自生10%TiB2/A356復合材料表面稀土鈰轉化膜的形成機理如圖3g[24]所示。由于H2O2的加入導致溶液中Ce3+發生如下氧化反應[24]:
當TiB2/A356復合材料被浸入到鈰鹽溶液中,材料表面的Al就開始發生溶解。同時,H2O2也在陽極Al上發生分解反應:
TiB2顆粒是一種導電性較好的陶瓷,在稀土轉化膜形成過程中是還原反應生成OH-的有利位置,還原反應方程如下:
隨著上述還原反應在陰極TiB2顆粒上不斷進行,復合材料表面區域pH值逐漸升高,當pH值達到或者超過8,一些氫氧化物就會在其表面形成并沉積成膜,可能發生的化學反應如下:
Si是原位自生TiB2/A356復合材料中非常重要的組成相,導電性差的特點使其不是轉化膜沉積的有利位置。但Si相大都與TiB2顆粒聚集在一起,高濃度OH-也存在于Si顆粒周圍,具有較高Ce含量的稀土轉化膜層就在聚集有大量TiB2顆粒和Si相的晶間區域形成。轉化膜干燥后,部分Ce的氫氧化物就會發生脫水反應,生成氧化物CeO2和Ce2O3。另外,轉化膜外表面的部分含Ce4+化合物,可能是由于膜層中Ce3+氧化形成,不穩定的Ce3+化合物與空氣中O2接觸就會自動轉化為含Ce4+化合物[25]。相比于復合材料基體,陽極氧化和封孔后的鈰轉化膜均能降低腐蝕電流密度(圖3f[23])。但是,鈰轉化膜的腐蝕電流密度最小(1.045 × 10-7 A/cm2),比復合材料基體(2.633 × 10-5 A/cm2)降低2個數量級,表現出更加優異的耐蝕性。
此外,采用陽極氧化+陰極電解沉積方法在原位自生15%TiB2/A356復合材料表面制備鈰沉積膜的復合膜層,亦能提升材料耐腐蝕性能[26]。沉積膜層主要分為2種區域,一種是圖4a[26]中A位置的淺色區域,另一種是B位置的深色區域。從放大圖(圖4b和c[26])可知,A區由許多球形顆粒組成,顆粒尺寸約100 nm,與化學沉積膜形貌相似;而B區域形成的稀土膜呈現平板狀組織,僅有少量球形顆粒沉積。B區域Ti和Si元素含量高于TiB2顆粒聚集區。同時,在B區域的Ce元素含量(43.78%,質量分數,下同)要遠大于A區(7.42%),即電解沉積過程中鈰膜更容易在阻礙氧化膜生長的TiB2顆粒聚集物上形核。在凹坑C位置,球形鈰化物顆粒也有效地沉積到了氧化膜上(圖4d[26])。由此推測因為鈰沉積膜下面的氧化膜不完整、不均勻導致了陰極電解沉積在不同位置的形成機制不同。
圖4 陽極氧化TiB2/A356復合材料表面陰極電解沉積鈰膜形貌以及鈰沉積膜在不連續復合材料氧化膜表面形成過程示意圖[26]
鈰沉積膜在不連續復合材料氧化膜表面形成過程如圖4e~h[26]所示。由于復合材料中TiB2顆粒和Si相形成的聚集物嚴重阻礙了氧化膜生長并破壞了氧化膜連續性,當陰極電壓作用于聚集物上時方程(5)更容易在這些具有電負性的聚集物上發生。隨著復合材料表面OH-濃度不斷增加,導致鈰鹽溶液的pH值不斷增加,并在氧化膜附近形成OH-濃度梯度(圖4f[26])。當復合材料附近pH值增加到8時,化學沉積反應將在多孔表面和未成膜聚集物上發生方程(9)。如果OH-濃度達到更高,鈰膜沉積將按照方程(10)進行[26]:
方程(9)和方程(10)中化學反應快速發生,導致大量細小鈰化合物在聚集物位置快速形核并緊密沉積在一起,最終在聚集物的附近形成大厚度平板態膜層組織(圖4g[26])。同時,氧化膜表面高OH-濃度會導致Al2O3膜發生如方程(11)所示化學溶解。隨著電解沉積時間的延長,稀土沉積膜生成速率將超過氧化膜化學溶解速率。氧化膜溶解被徹底抑制,使得多孔氧化膜被電解沉積生成的鈰化合物顆粒逐漸封閉,稀土化合物不斷沉積,導致膜層厚度增加(如圖4h[26]所示)。隨著稀土化合物不斷沉積,聚集物逐漸被覆蓋,沉積膜形核速率大幅減慢,導致少量大尺寸鈰化合物顆粒也在板狀膜層上沉積。此外,陰極電化學沉積的鈰膜具有與陽極氧化膜相當的腐蝕電位,但腐蝕電流密度(5.957 × 10-7 A/cm2)遠小于單一陽極氧化膜并且比復合材料基體要低2個數量級。在陽極氧化TiB2/A356復合材料表面采用陰極電解沉積制備稀土膜的方法,成膜時間短,比化學沉積方法更適合于工業生產應用,尤其適合綜合力學性能優異的高顆粒含量原位自生TiB2/Al復合材料的表面防護。
3 低溫熔鹽沉積技術
現有鋁基復合材料的腐蝕防護技術,尤其以傳統陽極氧化為代表,會因TiB2顆粒增強體存在而降低生成氧化膜層的完整性和平整度。因此,研究一種耐蝕性能較好且完整而連續的防腐膜層,對有效提高原位自生TiB2/Al基復合材料抗腐蝕能力具有重要意義[27]。金屬電沉積是利用金屬離子陰極電化學還原作用使固體材料表面附著一層完整、連續鍍膜的工藝。該鍍膜可起到防止腐蝕、增強導電、反光及增進美觀等效果。Al表面能夠天然地形成一層保護性氧化膜,使其具有較高耐腐蝕性能;另外,Al與鋁基復合材料的基體元素相同,如果能將鋁層鍍覆于原位自生TiB2/Al復合材料表面,將有效提高復合材料耐蝕性能[27]。目前,Al及鋁合金電沉積的體系主要包括有機溶劑、無機熔鹽和有機熔鹽(即離子液體) 3種體系[28,29]。其中,AlCl3-NaCl-KCl熔鹽體系是研究最多的無機熔鹽體系。該體系熔鹽制備簡單、電導率高、使用周期長、Al的沉積速率快,可獲得均勻且不容易剝落的沉積層。此外,AlCl3型無機熔鹽(AlCl3-NaCl、AlCl3-NaCl-KCl無機熔鹽)相對NaCl-KCl無機熔鹽來說為低溫熔鹽(98℃左右)[28,29],其電沉積溫度較低,不會影響基體材料力學性能,并且生產成本低,具有節能降耗的特點。
Huang等[30]創新性地采用熔鹽電沉積鋁的方法,通過優化低溫AlCl3-NaCl-KCl無機熔鹽電沉積液及鋁層制備工藝,在原位自生TiB2/A356復合材料表面成功制備出致密、均勻和完整的鋁鍍層。系統研究了沉積時間對鋁層組織的影響,發現Al在復合材料表面電沉積的初期是有選擇性地優先沉積在TiB2和Si表面(圖5a[30]A區域和圖5a1[30])。隨著電沉積時間延長(圖5b和b1[30]),TiB2和Si相全被鋁層覆蓋后,基體中的Al相也逐漸沉積上鋁層。鋁層在逐漸生長,鋁層大致覆蓋住基體表面。當電沉積45 min時,基體表面全部沉積上了連續、致密、完整的鋁層,如圖5d和d1[30]所示。對這種選擇性沉積機制進行了深入研究,并將其主要歸因于如下3個因素:(1) 陰極復合材料表面TiB2和Si相凸起處增加了局部電流密度,加速了鋁沉積[31];(2) TiB2和Al之間存在著很大電位差,鋁層會在電位較高的相(TiB2和Si相)上優先沉積并向四周擴展;(3) Al、Si和TiB2相表面能影響鋁的電沉積。金屬表面總是以最穩定的狀態呈現,最穩定的晶面是原子最密排面,而Al相比TiB2或Si有更低的表面能[32~35],電沉積鋁層在TiB2和Si表面生成所需的激活能要比在Al上生成鋁層所需激活能小得多。綜上,鋁層在沉積初期優先在TiB2和Si相表面沉積。
圖5 電沉積鋁層在不同沉積時間下的SEM像及其對應的形成機制,基體上形成的二維和三維鋁晶核示意圖,純Al、A356、TiB2/A356復合材料和TiB2/A356復合材料電沉積鋁層在3.5%NaCl溶液中的極化曲線[30]
電沉積鋁晶粒的生長模式如圖5e和f[30]所示。由于界面能越小,臨界晶核尺寸越小,相應形成的沉積層晶粒尺寸就越小,反之亦然[36]。因此,二維生長的鋁層表面形成的新鋁晶粒比直接在基體表面生成鋁層晶粒細小(如圖5d[30]所示)。極化曲線測試結果(圖5g[30])表明,TiB2/A356復合材料表面電沉積鋁后的耐蝕性能相比原始復合材料有很大提高,并接近純Al的耐腐蝕性。這是因為復合材料表面發生了Al的選擇性沉積,有效減緩了TiB2和基體復合材料中Al之間的電偶反應,從而提高了復合材料的耐蝕性能。
為了進一步提高原位自生TiB2/Al復合材料表面熔鹽沉積鋁層耐蝕性,Huang等[37]將低溫熔鹽沉積技術與后續陽極氧化技術相結合,將連續、致密鋁層轉化為Al2O3膜層以提高其耐蝕性。如圖6a[37]電沉積鋁層與基體的截面形貌所示,鋁層完整、平整、連續且厚度均勻(約9.1 μm),與基體結合良好。復合材料表面的鋁層(圖6b[27])經過陽極氧化后的表面保留了氧化前的大致輪廓且存在納米級的不規則孔洞,生成的氧化膜連續、無缺陷存在。這避免了對原始復合材料直接進行陽極氧化時,因TiB2和Si相的存在而生成完整性和致密性較差的氧化膜。相比于只經過陽極氧化的復合材料(圖6c和d[37]),由低溫熔鹽沉積結合陽極氧化后復合材料的耐蝕性得到了進一步提高(腐蝕電位:-0.686 V,腐蝕電流密度:4.236 × 10-7 A/cm2),并具有與陽極氧化后的純Al (腐蝕電位:-0.685 V,腐蝕電流密度:4.055 × 10-7 A/cm2)相似的耐腐蝕性能。
圖6 鋁層和基體截面形貌[37],TiB2/A356復合材料表面電沉積鋁層陽極氧化膜形貌[27],陽極氧化后復合材料、電解沉積鋁層以及純Al的Bode圖[37],陽極氧化后復合材料、電解沉積鋁層以及純Al的極化曲線[37]
4 微弧氧化技術
由于鋁基材料硬度較低、耐磨性較差,在高速流體中會出現較為嚴重的空泡腐蝕現象[38]。因此,當材料用于高速水流工況下時,鋁基復合材料需要具備較高的耐空泡腐蝕和耐Cl-侵蝕的能力,這對該材料表面防護提出了嚴峻的挑戰。本文中陽極氧化+稀土轉化膜和低溫熔鹽沉積的2種工藝都能夠顯著提高TiB2/Al基復合材料的耐蝕性能,但氧化膜層硬度較低,在空泡作用下容易被破壞。陶瓷材料具有較高硬度,在耐空泡腐蝕方面具有很大優勢[39]。微弧氧化(MAO)是一種將Al、Mg等金屬置于電解液中(主要為堿性)并作為陽極,將材料從Faraday放電區提升到火花放電以及弧光放電區,在高壓放電的作用下發生復雜的化學、電化學和等離子化學變化,并在材料表面生成一層晶態陶瓷膜層的表面處理技術[40,41]。微弧氧化技術可在復合材料表面形成一層連續的高硬度陶瓷氧化膜層[42]。因此,對原位自生的TiB2/Al基復合材料表面進行微弧氧化處理有望同時提高其耐蝕性和耐空泡腐蝕性能。
張弘斌[43]采用微弧氧化工藝在原位自生TiB2/A201復合材料表面以鋁酸鈉溶液為電解液體系,制備出的微弧氧化膜層孔隙率為3%,表面硬度達到1265 HV。將TiB2/A201復合材料與約50 μm厚的微弧氧化膜層進行耐空泡腐蝕實驗,空泡腐蝕5、10、15、30、60和120 min后復合材料和氧化膜層宏觀形貌如圖7[43]所示。復合材料(圖7a[43])經過5 min空泡腐蝕后表面失去了金屬光澤。隨著空蝕時間的延長,腐蝕區域的顏色逐漸變得暗淡,且粗糙度也有所增加。空蝕120 min后,試樣表面還出現肉眼可見的蝕坑。微弧氧化膜層(圖7b[43])經過5 min的空蝕后,膜層顏色加深,并且膜層出現了少量破損,露出了基底顏色。隨著空蝕時間的延長,試樣表面膜層脫落情況加劇;在經過120 min的空蝕后,空蝕區域的微弧氧化膜層脫落殆盡,且也出現了肉眼可見的蝕坑。
圖7 TiB2/A201復合材料和微弧氧化膜層空泡腐蝕后的宏觀形貌[43]
膜層經過空泡腐蝕后的微觀形貌如圖8a~e和a1~e1[43]所示。空蝕5 min后,試樣表面出現了少量的空蝕坑,試樣表面多數的“瘤狀物”和“火山口”被破壞剝離,留下碎石狀的陶瓷表面。空蝕10 min后,表面空蝕坑數量增多,并且其尺寸也有所增加。隨著空蝕時間進一步延長,膜層表面空蝕坑數量增多,尺寸增大,“瘤狀物”和“火山口”基本消失。空蝕120 min后,膜層基本被剝離,留下裸露的基底,表面存在大量空蝕坑。從失重量和空泡腐蝕時間的關系曲線(圖8f[43])可以看出,試樣在空泡腐蝕初期(0~10 min)質量損失較為明顯,之后失重速率減小。此后,空蝕進入上升期,試樣表面出現由空蝕針孔聚集而形成的空蝕坑,并且逐步擴展到整個表面,失重率達到最大值。空蝕30 min后,微弧氧化膜層已基本失去對基底的保護作用,空蝕主要對象逐漸由微弧氧化膜層轉變為膜層下方的復合材料基底。微弧氧化膜層硬度顯著高于Al基體,但是在空泡腐蝕30 min后就基本失去了對基底的保護作用,推測這主要是由于微弧氧化膜層中存在許多微裂紋等缺陷所導致。
圖8 微弧氧化膜層空泡腐蝕不同時間后微觀形貌,累計失重量與空蝕時間關系曲線,TiB2/A201復合材料和微弧氧化膜層在3.5%NaCl溶液中極化曲線,以及微弧氧化膜層截面圖[43]
TiB2/A201復合材料和在3種電流密度(6、10和15 A/dm2)下制備微弧氧化膜的極化曲線(圖8g[43])顯示經過微弧氧化處理后,其自腐蝕電流密度出現了顯著下降,并且在陽極極化過程中電流密度上升的趨勢被顯著抑制,這說明微弧氧化膜層有效地阻礙了復合材料陽極極化過程。在10 A/dm2電流密度下制備的膜層的自腐蝕電流密度最低,為3.1 × 10-8 A/cm2;10 A/dm2電流密度下制備的微弧氧化膜層缺陷較少(圖8h和h1[43]),沒有平行于基底的裂紋存在,且只有少數細小的垂直于基底裂紋存在,其抗腐蝕能力最強;15 A/dm2電流密度下制備的膜層自腐蝕電流密度最高,為1.6 × 10-6 A/cm2,但仍比TiB2/A201復合材料的自腐蝕電流密度(4.2 × 10-6 A/cm2)降低了約2.6倍[43]。所以,微弧氧化膜層有效地減少了腐蝕介質與基底接觸,使自腐蝕電流密度大大降低,進而抑制復合材料基底在陽極極化過程中的進一步腐蝕。
表面處理工藝除了可以提高材料的耐蝕性、耐磨性以外,所賦予的顏色也能夠在醫學識別、光學吸收、航天器應用等領域起到裝飾性和功能性的作用。Wang等[44]在AZ91D鎂合金上制備了不同顏色(黑色、白色以及灰色)微弧氧化膜層;通過在多磷酸電解液中添加TiO2溶膠,在Mg-Li合金表面也獲得了耐蝕性良好藍色微弧氧化膜。Han等[45]報道了通過堿性硅酸鹽溶液在鈦合金表面可制備一層黑色的微弧氧化膜;而Jiang等[46]在鈦合金表面通過微弧氧化實現了一種新型黃色陶瓷膜層制備。目前,關于原位自生TiB2/Al基復合材料表面著色膜報道很有限,各種彩色陶瓷薄膜研究對其實際應用具有重要價值。Xia等[47]采用微弧氧化工藝,通過向堿性電解液中添加KMnO4,在原位自生TiB2/7050Al復合材料表面制備了棕色薄膜。由堿性電解液(9 g/L Na2SiO3 + 4 g/L NaOH + 2 g/L EDTA-2Na)經過微弧氧化制備膜層的宏觀形貌呈現灰白色(圖9a[47]),膜層表面孔洞(圖9c[47])平均尺寸約1.1 ?m,孔隙率為4.23%。當電解液中添加KMnO4后,MnO
在堿性溶液中很容易被還原為MnO
(方程(12))。在此過程中薄膜顏色逐漸變為棕色[48],并在電場力驅動下轉移到陽極,然后還原為MnO (方程(13))。隨著微弧氧化反應的進行,更多MnO沉積在放電外層,最后薄膜呈現棕褐色(圖9b[47])。
圖9 堿性電解質中添加和不添加KMnO4的微弧氧化膜層,微弧氧化膜層的XPS分析,添加KMnO4膜層的Mn2p圖譜[47]
棕褐色膜層微觀形貌與灰白色膜層相似(圖9d[47]),平均孔隙率減小為1.79%。此外,對比添加和不添加KMnO4的膜層表面的X射線光電子能譜(XPS)結果(圖9e和f[47]),說明大部分的MnO
在微弧氧化過程中被還原為MnO。相比之下,棕褐色膜層具有最低的腐蝕電流密度(2.452 × 10-6 A/cm2),表現出優異耐蝕性。電流密度的降低表明表面形成的膜層限制了腐蝕性離子的滲透,有效降低了金屬-電解質界面中離子傳輸。另外,在需要耐腐蝕和裝飾的領域如手機殼、筆記本殼、體育用品等,原位自生TiB2/Al基復合材料表面制備的有色薄膜有著良好的應用前景[47]。
5 其他表面處理技術
基于高能量輸入、良好冶金結合以及靈活的加工性等優勢,激光表面改性正逐漸發展為一種可替代傳統表面處理的新方法。比如,Man等[49]采用激光合金化在6061鋁合金表面融化NiCrBSi混合粉末,通過調節Ni-Al金屬間化合物的細枝晶狀結構顯著提高了涂層的硬度和耐腐蝕能力。由于添加TiC、SiC、TiB2、SiO2等陶瓷增強體的金屬基復合涂層有望獲得更高的強度、耐磨性等綜合性能,通過激光表面合金化在鋁合金表面制備含陶瓷相的金屬基復合涂層逐漸成為重要研究方向。Tomida等[50]采用激光合金化在Al-Mg合金表面制備了TiC-Cu復合涂層,通過調節Cu含量和TiC體積分數可使復合涂層的最高硬度達到600 HV,耐磨性是Cu基體的近6倍。為了提高A6061鋁合金的耐磨性,Chi等[51]使用鐵基合金、B4C和Ti的混合粉末,通過激光合金化的方式在鋁合金表面原位制備了TiB2-TiC增強的Fe-Al復合涂層,發現TiC在棒狀的TiB2表面發生不均勻形核,2者界面處的失配度僅為1.049%,能夠形成良好的結合。同時,復合涂層平均硬度約為520 HV (約為基體的7倍),磨損體積相比基體減少了92.8%,耐磨性得到了顯著提高。目前關于采用激光表面合金化制備原位自生TiB2/Al基復合材料表面涂層的研究還未見報道,激光的高能量密度不可避免地會對低熔點的鋁合金復合材料基體產生明顯的熱影響區等不利影響。因此,合理控制參數范圍和選取與鋁合金復合材料熔點相近的涂層材料體系顯得尤為重要。
不同于激光表面合金化的方法,冷噴涂工藝是通過將粉末原料加速到超音速后沉積在基體表層并通過顆粒間的塑性變形而形成機械咬合或者冶金結合并最終形成涂層的過程[52,53]。在這個過程中,顆粒與顆粒以及顆粒與基體的結合是由動能所產生的塑性變形實現。因此,冷噴涂被認為可最大限度地減少或消除涂層殘余熱應力、氧化和相變[54,55],在提高鋁合金表面耐蝕性和耐磨性等領域有著較好應用前景。Meydanoglu等[56]研究發現,在冷噴涂的7075鋁合金涂層中通過外加陶瓷顆粒會增加涂層內部塑性變形區域,從而為腐蝕行為提供更多活性位點,增大了復合涂層腐蝕速率。為了盡量避免這種現象,Xie等[57]使用原位TiB2/7075Al復合粉末作為冷噴涂的新原料,在7075鋁合金表面制備了含TiB2納米顆粒增強的復合涂層。但是,經過電化學測試研究發現,相比于冷噴涂的純7075Al合金涂層,TiB2顆粒增強體與Al基體之間的電偶腐蝕也增大了復合涂層的腐蝕速率。此外,還發現低溫退火處理(230℃、6 h)引起的晶格應變和位錯湮滅有助于耐蝕性的提升,但高溫固溶處理形成的晶粒長大和析出相的形成會顯著惡化其耐蝕性。
基于能夠有效地細化晶粒、節能高效以及可避免如氣孔、開裂、變形等凝固缺陷的優勢,攪拌摩擦焊在鋁合金上的應用越來越廣泛[58,59]。Sharma等[60]采用攪拌摩擦焊的方法對原位自生TiB2/Al基復合材料表面進行加工后,相比鑄態的復合材料(晶粒尺寸(16.8 ± 2.4) μm)顯著地細化了表面的晶粒尺寸((5.3 ± 2.3) μm);此外,攪拌摩擦焊處理和鑄態的TiB2/Al基復合材料均比SiC/Al基復合材料、B/Al基復合材料以及石墨/Al基復合材料更能抵御點蝕的發生。此外,攪拌摩擦焊處理后的樣品表面細小的晶粒尺寸和高密度的小角晶界減小了晶間腐蝕形成的傾向,但是膜層表面出現的TiB2和Al3Ti顆粒會削弱其保護作用并在長時間的浸泡實驗中發生晶間腐蝕。
高熵合金作為由5種或5種以上元素按照等原子比或近等原子比所組成的簡單結構的固溶體材料,被Yeh等[61]和Cantor等[62]發現并問世以來,因其特有的高熵效應、晶格畸變效應、緩慢擴散效應以及雞尾酒效應等賦予了此類材料優異的物理及機械性能,比如高的強度和硬度、良好的熱穩定性、優異的耐磨性和耐腐蝕性等[63,64]。另外,由3到4種組元所構成的中熵合金兼具高熵合金的優勢,但相比于高熵合金具有更低的理論密度,應用前景也較為廣闊。基于高熵/中熵合金的優異綜合性能,關于這2類材料涂層的研究也引起了廣大科研工作者的重視[65~67]。目前的研究[68~71]表明,激光表面合金化是制備高熵/中熵合金涂層的主流技術且大部分基體以鋼和鈦合金為主。鋁合金及鋁基復合材料表面高熵/中熵合金涂層的報道相對較少。鋁合金和此類合金間的高熔點差異是限制它們在鋁合金表面應用的難點。不同于主流的高熵/中熵合金涂層制備方法,Zhao等[72]創新性地采用電阻縫加工的方法在6061鋁合金表面快速地實現了AlFeCrCoNi高熵合金涂層的制備。該技術不同于激光或電子束等高能量密度的無差別式加熱,它是利用粉末間電流的Joule效應(Q = I2Rt,其中Q為Joule熱,I為電流,R為粉末電阻,t為作用時間)而自發形成高熵合金涂層, 且制備過程不會對鋁合金基體產生明顯的熱影響區等不利影響。高熵合金涂層在腐蝕性環境中表現出優異的耐磨蝕性。此外,Zhao等[73]進一步將該技術應用于鎂合金并大幅度提高了其在不同環境介質下的耐磨性。采用電阻縫加工的方法制備原位自生TiB2/Al基復合材料表面高熵/中熵合金涂層的方法(如圖10所示),在原位自生TiB2/Al基復合材料表面高性能的高熵/中熵合金制備有著良好的研究與應用價值。
圖10 電阻縫加工法制備原位自生TiB2/鋁合金基復合材料表面高/中熵合金涂層示意圖
6 總結與展望
過去幾十年,有關原位自生TiB2/Al基復合材料表面處理及其腐蝕防護技術已取得了重要進展。主要體現在以下幾個方面。(1) 陽極氧化結合稀土轉化膜技術很好地封閉了氧化膜的不連續區域和多孔結構,填補氧化層中的孔洞和裂紋;相比于單一陽極氧化膜層,復合膜層的耐蝕性得到了進一步提高;化學沉積和陰極電解沉積稀土膜的形成都是由于陰極區的pH值升高引起的化學或電化學沉積過程,但電解沉積速率快,成膜時間短,更適合工業應用。(2) 低溫熔鹽沉積技術主要借助AlCl3-NaCl-KCl無機熔鹽電沉積,在原位自生TiB2/Al復合材料表面實現致密、均勻和完整鋁層的制備,復合材料的耐蝕性能有很大提高,性能接近于純Al;其次,對TiB2/Al復合材料電沉積的鋁層進行陽極氧化封孔處理,可進一步提高復合材料的耐蝕性能且非常接近純Al陽極氧化封孔試樣。(3) 微弧氧化技術在TiB2/Al復合材料表面制備的氧化膜層能與基底形成良好的冶金結合且硬度較高,膜層可極大提高復合材料的耐Cl-侵蝕能力,有效抑制復合材料的陽極過程;但是,脆性的微弧氧化膜層不能經受長時間的空泡腐蝕,膜層中的微裂紋等缺陷也會加劇涂層的剝離;此外,通過合理設計電解液成分,借助微弧氧化工藝可在原位自生TiB2/Al復合材料表面制備兼具耐腐蝕性和裝飾性的有色薄膜并有著良好的應用前景。(4) 眾多新型表面處理工藝的開發與應用,將有助于提升原位自生TiB2顆粒增強鋁基復合材料的腐蝕防護性能,對推動新材料的廣泛應用起到重要支撐作用。
為進一步拓寬原位自生TiB2/Al基復合材料的應用范圍,未來其表面腐蝕防護技術急需開展的工作包括:(1) 開發適用于原位自生TiB2/Al基復合材料表面處理及腐蝕防護的新技術,制備可與基體形成冶金結合的大厚度(> 400 ?m)、高致密性(致密度> 99%)的涂層,徹底解決TiB2顆粒引起的微電偶腐蝕及自然膜層或氧化膜層不連續的問題,大幅度提高復合材料的耐蝕性;(2) 簡化表面改性工藝流程,加快涂層制備速率,降低涂層工藝的成本,加快工業化應用進程;(3) 使用高性能的涂層材料(例如特定成分的高熵合金或中熵合金),賦予原位自生TiB2/Al基復合材料表面兼具優異耐腐蝕性、耐空泡腐蝕性和耐磨性、自潤滑等多功能性的涂層;(4) 深入研究并完善原位自生TiB2/Al基復合材料表面處理、腐蝕防護的理論及相應的成套技術,促進原位自生TiB2/Al基復合材料的應用與發展。
參考文獻
1 Bhuvaneswari V, Rajeshkumar L, Nimel Sworna Ross K. Influence of bioceramic reinforcement on tribological behaviour of aluminium alloy metal matrix composites: Experimental study and analysis [J]. J. Mater. Res. Technol., 2021, 15: 2802
2 Zhao S L, Zhang H M, Cui Z S, et al. Superplastic behavior of an in-situ TiB2 particle reinforced aluminum matrix composite processed by elliptical cross-section torsion extrusion [J]. Mater. Charact., 2021, 178: 111243
3 Dong B X, Li Q, Wang Z F, et al. Enhancing strength-ductility synergy and mechanisms of Al-based composites by size-tunable in-situ TiB2 particles with specific spatial distribution [J]. Composites, 2021, 217B: 108912
4 Taheri-Nassaj E, Kobashi M, Choh T. Fabrication and analysis of an in situ TiB2Al composite by reactive spontaneous infiltration [J]. Scr. Mater., 1996, 34: 1257
5 Tee K L, Lu L, Lai M O. Synthesis of in situ Al-TiB2 composites using stir cast route [J]. Compos. Struct., 1999, 47: 589
6 Lu L, Lai M O, Chen F L. Al-4 wt% Cu composite reinforced with in-situ TiB2 particles [J]. Acta Mater., 1997, 45: 4297
7 Ma Z Y, Tjong S C. High temperature creep behavior of in-situ TiB2 particulate reinforced copper-based composite [J]. Mater. Sci. Eng., 2000, A284: 70
8 Han Y F, Liu X F, Bian X F. In situ TiB2 particulate reinforced near eutectic Al-Si alloy composites [J]. Composites, 2002, 33A: 439
9 Wang H W. Preparation and application of in-situ ceramic particles reinforced Al matrix composites [J]. Aeronaut. Manuf. Technol., 2021, 64(16): 14
9 王浩偉. 原位自生陶瓷顆粒增強鋁基復合材料制備及應用 [J]. 航空制造技術, 2021, 64(16): 14
10 Le Y K. Study on in-situ A356/TiB2 composite and its solid-state phase transformation process [D]. Shanghai: Shanghai Jiao Tong University, 2006
10 樂永康. 原位合成A356/TiB2復合材料及其固態相變過程的研究 [D]. 上海: 上海交通大學, 2006
11 Zhang Y J. High-damping and high-strength cast aluminum-based composite material [D]. Shanghai: Shanghai Jiao Tong University, 2006
11 張亦杰. 高阻尼高強度鑄造鋁基復合材料 [D]. 上海: 上海交通大學, 2006
12 Chen D. Preparation and properties of in-situ TiB2/7055 aluminum matrix composite [D]. Shanghai: Shanghai Jiao Tong University, 2008
12 陳 東. 原位合成TiB2/7055鋁基復合材料的制備與性能 [D]. 上海: 上海交通大學, 2008
13 He C L, Cai Q K. Recent developments in research on corrosion of aluminum metal matrix composites [J]. Mater. Rep., 2003, 17(1):45
13 賀春林, 才慶魁. 鋁金屬基復合材料的腐蝕研究進展 [J]. 材料導報, 2003, 17(1): 45
14 Nie J F, Wang F, Chen Y Y, et al. Microstructure and corrosion behavior of Al-TiB2/TiC composites processed by hot rolling [J]. Results Phys., 2019, 14: 102471
15 Sun H H, Chen D, Li X F, et al. Electrochemical corrosion behavior of Al-Si alloy composites reinforced with in situ TiB2 particulate [J]. Mater Corros., 2009, 60: 419
16 Huang J, Chen D, Wu Y, et al. Corrosion behavior of in-situ TiB2/7050Al composite in NaCl solution at different pH values [J]. Mater. Res. Express, 2019, 6: 056541
17 Hinton B R W, Arnott D R, Ryan N E. The inhibition of aluminium alloy corrosion by cerous cations [J]. Met. Forum., 1984, 7: 211
18 Mansfeld F, Lin S, Kim K, et al. Pitting and surface modification of SIC/Al [J]. Corros. Sci., 1987, 27: 997.
19 Mansfeld F, Lin S, Kim S, et al. Corrosion protection of Al alloys and Al-based metal matrix composites by chemical passivation [J]. Corrosion, 1989, 45: 615
20 Mansfeld F, Lin S, Kim S, et al. Pitting and passivation of Al alloys and Al-based metal matrix composites [J]. J. Electrochem. Soc., 1990, 137: 78
21 Yu X W, Cao C A, Yao Z M. Application of rare earth metal salts in sealing anodized aluminum alloy [J]. J. Mater. Sci. Lett., 2000, 19: 1907
22 Hu J, Zhao X H, Tang S W, et al. Corrosion protection of aluminum borate whisker reinforced AA6061 composite by cerium oxide-based conversion coating [J]. Surf. Coat. Technol., 2006, 201: 3814
23 Sun H H, Ma N H, Chen D, et al. Fabrication and analysis of anti-corrosion coatings on in-situ TiB2p reinforced aluminum matrix composite [J]. Surf. Coat. Technol., 2008, 203: 329
24 Sun H H, Wang H W, Chen D, et al. Conversion-coating treatment applied to in situ TiB2p reinforced Al-Si-alloy composite forcorrosion protection [J]. Surf. Interface Anal., 2008, 40:1388
25 Dabalà M, Armelao L, Buchberger A, et al. Cerium-based conversion layers on aluminum alloys [J]. Appl. Surf. Sci., 2001, 172: 312
26 Sun H H, Li X F, Chen D, et al. Enhanced corrosion resistance of discontinuous anodic film on in situ TiB2p/A356 composite by cerium electrolysis treatment [J]. J. Mater. Sci., 2009, 44: 786
27 Huang W M. Study on low temperature molten salt deposition of anticorrosive aluminum layer in in-situ TiB2/Al matrix composite material [D]. Shanghai: Shanghai Jiao Tong University, 2013
27 黃文貌. 原位自生TiB2/鋁基復合材料低溫熔鹽沉積防腐鋁層研究 [D]. 上海: 上海交通大學, 2013
28 Chen Z P. Special Electroplating Technology [M]. Beijing: Chemical Industry Press, 2004: 1
28 陳祝平. 特種電鍍技術 [M]. 北京: 化學工業出版社, 2004: 1
29 Kan H M. Study on low temperature aluminium electrolysis [D]. Shenyang: Northeastern University, 2007
29 闞洪敏. 低溫鋁電解的研究 [D]. 沈陽: 東北大學, 2007
30 Huang W M, Liu B, Wang M L, et al. Study on the initial electrodeposition behavior of aluminum on TiB2/A356 composite [J]. Mater. Corros., 2014, 65: 502
31 Kunieda M, Katoh R, Mori Y. Rapid prototyping by selective electrodeposition using electrolyte jet [J]. CIRP Ann., 1998, 47: 161
32 Qin X J, Shao G J. Study on the initial electro-deposition behavior of Ni-P alloy [J]. J. Chin. Soc. Corros. Prot., 2004, 24(1): 6
32 秦秀娟, 邵光杰. 電沉積Ni-P合金初期沉積行為的研究 [J]. 中國腐蝕與防護學報, 2004, 24(1): 6
33 Wang C L, Zhou L H, Hu X H, et al. Density functional theory on characteristics of TiB2(0001) surface [J]. Chin. J. Nonferrous Met., 2008, 18: 145
33 王春雷, 周理海, 胡雪慧 等. TiB2(0001)表面性質的密度泛函理論 [J]. 中國有色金屬學報, 2008, 18: 145
34 Yang J, Chen Q J, Lin Z D, et al. An experimental study: Heteroepitaxial growth of diamond thin films on silicon (111) surface [J]. Prog. Nat. Sci., 1995, 5: 233
35 Plitzko J, R?sler M, Nickel K G. Heteroepitaxial growth of diamond thin films on silicon: Information transfer by epitaxial tilting [J]. Diam. Relat. Mater., 1997, 6: 935
36 Shao G J, Chen L, Wang F Y, et al. Study on the initial electrodeposition behavior of Ni-P alloys [J]. Mater. Chem. Phys., 2005, 90: 327
37 Huang W M, Zhou C, Liu B, et al. Improvement in the corrosion resistance of TiB2/A356 composite by molten-salt electrodeposition and anodization [J]. Surf. Coat. Technol., 2012, 206: 4988
38 Zhang S, Zhang C H, Zhang L T, et al. Cavitation erosion and microstructure of laser surface cladding MMC of SiCp on AA6061 aluminium alloy [J]. J. Mater. Eng., 2002, (2): 47
38 張 松, 張春華, 張錄廷 等. 鋁合金表面激光熔覆SiC顆粒增強表層金屬基復合材料的組織及空泡腐蝕性能 [J]. 材料工程, 2002, (2): 47
39 Yang Z, Tian J M. Cavitation erosion of structural ceramics [J]. J. Funct. Mater., 2003, 34: 200
39 楊 政, 田杰謨. 結構陶瓷的空蝕性研究 [J]. 功能材料, 2003, 34: 200
40 Sah S P, Tsuji E, Aoki Y, et al. Cathodic pulse breakdown of anodic films on aluminium in alkaline silicate electrolyte—Understanding the role of cathodic half-cycle in AC plasma electrolytic oxidation [J]. Corros. Sci., 2012, 55: 90
41 Wang D Y, Dong Q, Chen C Z, et al. Recent progress of micro-arc oxidation technique [J]. J. Chin. Ceram. Soc., 2005, 33: 1133
41 王德云, 東 青, 陳傳忠 等. 微弧氧化技術的研究進展 [J]. 硅酸鹽學報, 2005, 33: 1133
42 Xue W B, Jin Q, Zhu Q Z, et al. Anti-corrosion microarc oxidation coatings on SiCp/AZ31 magnesium matrix composite [J]. J. Alloys Compd., 2009, 482: 208
43 Zhang H B. Study on the preparation and corrosion resistance of the micro-arc oxidation film of in-situ TiB2/A201 composite [D]. Shanghai: Shanghai Jiao Tong University, 2017
43 張弘斌. 原位自生TiB2/A201復合材料微弧氧化膜層的制備及其耐蝕性能研究 [D]. 上海: 上海交通大學, 2017
44 Wang L Q, Zhou J S, Liang J, et al. Thermal control coatings on magnesium alloys prepared by plasma electrolytic oxidation [J]. Appl. Surf. Sci., 2013, 280: 151
45 Han J X, Cheng Y L, Tu W B, et al. The black and white coatings on Ti-6Al-4V alloy or pure titanium by plasma electrolytic oxidation in concentrated silicate electrolyte [J]. Appl. Surf. Sci., 2018, 428: 684
46 Jiang Y L, Wang J K, Hu B, et al. Preparation of a novel yellow ceramic coating on Ti alloys by plasma electrolytic oxidation [J]. Surf. Coat. Technol., 2016, 307: 1297
47 Xia C J, Huang J, Tao J M, et al. The preparation and properties of the brown film by micro-arc oxidized on in-situ TiB2/7050Al matrix composites [J]. Coatings, 2020, 10: 615
48 Li K, Li W F, Zhang G G, et al. Preparation of black PEO layers on Al-Si alloy and the colorizing analysis [J]. Vacuum, 2015, 111: 131
49 Man H C, Zhang S, Yue T M, et al. Laser surface alloying of NiCrSiB on Al6061 aluminium alloy [J]. Surf. Coat. Technol., 2001, 148: 136
50 Tomida S, Nakata K, Saji S, et al. Formation of metal matrix composite layer on aluminum alloy with TiC-Cu powder by laser surface alloying process [J]. Surf. Coat. Technol., 2001, 142-144: 585
51 Chi Y M, Gong G H, Zhao L J, et al. In-situ TiB2-TiC reinforced Fe-Al composite coating on 6061 aluminum alloy by laser surface modification [J]. J. Mater. Process. Technol., 2021, 294: 117107
52 Rokni M R, Nutt S R, Widener C A, et al. Review of relationship between particle deformation, coating microstructure, and properties in high-pressure cold spray [J]. J. Therm. Spray Technol., 2017, 26: 1308
53 Raoelison R N, Xie Y, Sapanathan T, et al. Cold gas dynamic spray technology: A comprehensive review of processing conditions for various technological developments till to date [J]. Addit. Manuf., 2018, 19: 134
54 Li W Y, Zhang C, Guo X P, et al. Study on impact fusion at particle interfaces and its effect on coating microstructure in cold spraying [J]. Appl. Surf. Sci., 2007, 254: 517
55 Xie X L, Chen C Y, Ji G, et al. A novel approach for fabricating a CNT/AlSi composite with the self-aligned nacre-like architecture by cold spraying [J]. Nano Mater. Sci., 2019, 1: 137
56 Meydanoglu O, Jodoin B, Kayali E S. Microstructure, mechanical properties and corrosion performance of 7075 Al matrix ceramic particle reinforced composite coatings produced by the cold gas dynamic spraying process [J]. Surf. Coat. Technol., 2013, 235: 108
57 Xie X L, Hosni B, Chen C Y, et al. Corrosion behavior of cold sprayed 7075Al composite coating reinforced with TiB2 nanoparticles [J]. Surf. Coat. Technol., 2020, 404: 126460
58 De P S, Mishra R S. Friction stir welding of precipitation strengthened aluminium alloys: Scope and challenges [J]. Sci. Technol. Weld. Joining, 2011, 16: 343
59 Nandan R, DebRoy T, Bhadeshia H K D H. Recent advances in friction-stir welding—Process, weldment structure and properties [J]. Prog. Mater. Sci., 2008, 53: 980
60 Sharma R, Singh A K, Arora A, et al. Effect of friction stir processing on corrosion of Al-TiB2 based composite in 3.5 wt.% sodium chloride solution [J]. Trans. Nonferrous Met. Soc. China, 2019, 29: 1383
61 Yeh J W, Chen S K, Lin S J, et al. Nanostructured high‐entropy alloys with multiple principal elements: Novel alloy design concepts and outcomes [J]. Adv. Eng. Mater., 2004, 6: 299
62 Cantor B, Chang I T H, Knight P, et al. Microstructural development in equiatomic multicomponent alloys [J]. Mater. Sci. Eng., 2004, A375-377: 213
63 Zhang Y, Zuo T T, Tang Z, et al. Microstructures and properties of high-entropy alloys [J]. Prog. Mater. Sci., 2014, 61: 1
64 George E P, Raabe D, Ritchie R O. High-entropy alloys [J]. Nat. Rev. Mater., 2019, 4: 515
65 Li J C, Huang Y X, Meng X C, et al. A review on high entropy alloys coatings: Fabrication processes and property assessment [J]. Adv. Eng. Mater., 2019, 21: 1900343
66 Li W, Liu P, Liaw P K, Microstructures and properties of high-entropy alloy films and coatings : A review [J]. Mater. Res. Lett., 2018, 6: 199
67 Yan X H, Li J S, Zhang W R, et al. A brief review of high-entropy films [J]. Mater. Chem. Phys., 2018, 210: 12
68 Lu J B, Wang B F, Qiu X K, et al. Microstructure evolution and properties of CrCuFe x NiTi high-entropy alloy coating by plasma cladding on Q235 [J]. Surf. Coat. Technol., 2017, 328: 313
69 Li X F, Feng Y H, Liu B, et al. Influence of NbC particles on microstructure and mechanical properties of AlCoCrFeNi high-entropy alloy coatings prepared by laser cladding [J]. J. Alloys Compd., 2019, 788: 485
70 Tüten N, Canadinc D, Motallebzadeh A, et al. Microstructure and tribological properties of TiTaHfNbZr high entropy alloy coatings deposited on Ti-6Al-4V substrates [J]. Intermetallics, 2019, 105: 99
71 Tian Y, Shen Y F, Lu C Y, et al. Microstructures and oxidation behavior of Al-CrMnFeCoMoW composite coatings on Ti-6Al-4V alloy substrate via high-energy mechanical alloying method [J]. J. Alloys Compd., 2019, 779: 456
72 Zhao D C, Yamaguchi T, Shu J F, et al. Rapid fabrication of the continuous AlFeCrCoNi high entropy alloy coating on aluminum alloy by resistance seam welding [J]. Appl. Surf. Sci., 2020, 517: 145980
73 Zhao D C, Yamaguchi T, Tusbasa D, et al. Fabrication and friction properties of the AlFeCrCo medium-entropy alloy coatings on magnesium alloy [J]. Mater. Des., 2020, 193: 108872
免責聲明:本網站所轉載的文字、圖片與視頻資料版權歸原創作者所有,如果涉及侵權,請第一時間聯系本網刪除。
-
標簽: 原位自生TiB2/Al基復合材料, 表面處理, 腐蝕防護, 涂層
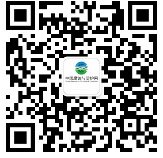
官方微信
《腐蝕與防護網電子期刊》征訂啟事
- 投稿聯系:編輯部
- 電話:010-62316606-806
- 郵箱:fsfhzy666@163.com
- 腐蝕與防護網官方QQ群:140808414