陶瓷顆粒,如SiC顆粒[7]、TiC顆粒[8]、TiB2顆粒[9]等,其強度和剛度高且價格較低,是目前最常用的增強相。Habibnejad[10]等用熔鑄法將Al2O3顆粒加入AZ31基體制備復合材料,其抗拉強度和屈服強度分別達到306 MPa和290 MPa。Deng[11,12]等用SiC顆粒和AZ91鎂合金制備的復合材料,其晶粒尺寸顯著減小,力學性能明顯提高。但是,陶瓷顆粒的尺寸較大、與鎂基體的界面潤濕性也較差,使制備出的復合材料塑性大大降低,限制了它的應用。石墨烯的力學性能優異、增強效率高且與鎂基體的化學相容性良好,是最理想的增強體[13]。Yuan[14,15]等用熱還原法制備石墨烯增強的鎂基復合材料,用原位生成的MgO顆粒調控界面,制備出的復合材料屈服強度和延伸率分別提高了76.2%和24.3%。Wang[16]等用原位反應制備了石墨烯增強鎂基復合材料,發現改善石墨烯與鎂的界面潤濕性可使其力學性能顯著提高,其抗拉強度和屈服強度分別達到316 MPa和221 MPa。
目前,制備石墨烯增強鎂基復合材料的常用方法有粉末冶金法、攪拌鑄造法和機械合成法。這些方法都有一定的不足之處:添加石墨烯容易產生燒損和出現團聚[17]。原位生成法,是通過化學反應直接合成石墨烯增強鎂基復合材料。與傳統的制備工藝相比,原位生成法能減少石墨烯的燒損,避免石墨烯在鎂基體中的分布不均和團聚。鑒于此,本文用原位合成法使葡萄糖與鎂發生化學反應制備石墨烯增強的鎂基復合材料,研究制備工藝對生成的石墨烯的質量和復合材料性能的影響。
1 實驗方法
1.1 實驗用材料
實驗用基體為AZ31鎂合金,其化學成分列于表1,制備增強體使用的葡萄糖粉末其純度為99.99%。
表1 AZ31鎂合金的化學成分
Table 1
Al | Zn | Mn | Si | Cu | Fe | Mg |
---|---|---|---|---|---|---|
2.80 | 1.00 | 0.25 | 0.06 | 0.01 | 0.01 | Bal. |
1.2 復合材料的制備
將AZ31鎂錠機加工成碎屑,放入酒精溶液中超聲清洗以去除表面的油污;將葡萄糖濃度為4%的葡萄糖粉末與去離子水混合,然后與鎂屑料一起放入200℃的高壓反應釜中進行水熱反應,反應時間為12 h。將得到的反應混合物放入300℃的烘箱中烘干,然后將其裝入冷壓模具中。在室溫和壓力為650 MPa條件下保壓30 s,制成半徑為20 mm、高30 mm的圓柱型坯料。將坯料裝入真空熱壓燒結爐中,分別在700℃、750℃、780℃燒結進行原位自生反應。將原位自生反應后的坯料裝入熱擠壓模具中,在420℃保溫15 min。然后在壓力為620 MPa、擠壓比25∶1、擠壓速度為3 mm/s條件下制備出石墨烯增強鎂基復合材料。實驗流程如圖1所示。
圖1
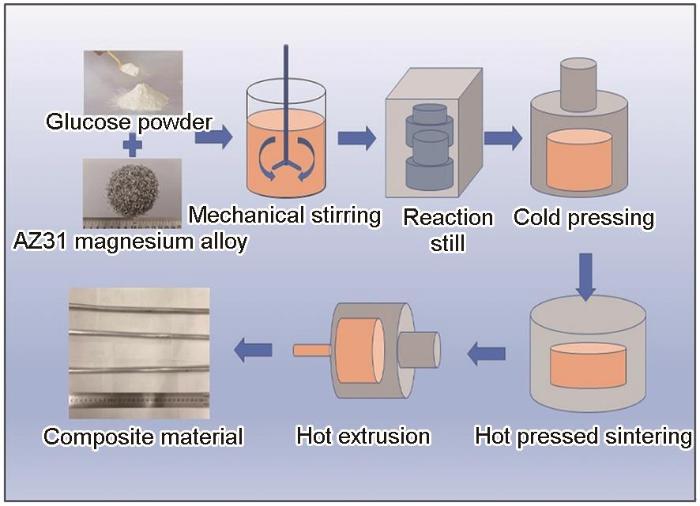
圖1 原位反應制備石墨烯/鎂復合材料的流程
Fig.1 Flow chart of in-situ reaction graphene/magnesium composite preparation
1.3 性能表征
為了驗證原位生成的反應產物是否含有石墨烯材料,將制備出的復合材料放入濃度為40%的硫酸溶液中腐蝕,然后將反應完全后的溶液抽濾,將抽濾后的產物冷凍干燥,將得到的黑色物質用于Raman分析。
用Raman光譜、XPS測試儀、FEI-SIRION掃描電鏡、原子力顯微鏡和型號為TECNAI-F30的透射電鏡等儀器表征反應產物的微觀組織。用電子萬能拉伸試驗機測試復合材料的力學性能,每組數據測試3個試樣取結果的平均值。
2 實驗結果和分析
2.1 石墨烯的微觀形貌
圖2給出了在不同反應溫度下原位自生的石墨烯的Raman分析。在圖2a、b和c中都出現了石墨烯的三個特征峰,位于1345 cm-1、1580 cm-1和2680 cm-1,分別對應石墨烯的D峰、G峰和2D峰。結果表明,所得反應產物為石墨烯。G峰為石墨烯的主要特征峰,是sp2雜化的碳原子面內振動引起的,此峰反應石墨烯的層數;D峰為石墨烯的無序振動峰,表征石墨烯所含缺陷的多少;2D峰可表征石墨烯內部碳原子的堆垛方式,通常用ID/IG表征石墨烯的缺陷含量,用I2D/IG表征石墨烯的層數[18]。
圖2
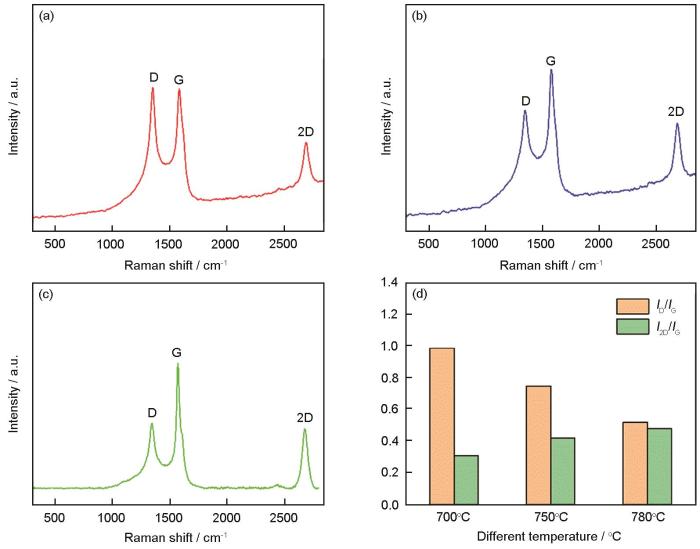
圖2 在不同反應溫度下原位自生的石墨烯的拉曼光譜和ID/IG和I2D/IG比值
Fig.2 Raman analysis of the in-situ generated graphene at700℃ (a), 750℃ (b), 780℃ (c) and ratio of ID/IG and I2D/IG (d)
從圖2a、b和c還可見,隨著反應溫度的提高原位自生的石墨烯的D峰的強度降低,2D峰的強度提高。這表明,原位生成的石墨烯中缺陷逐漸減少,石墨烯的層厚減小、質量提高。ID/IG和I2D/IG比值的計算結果,如圖2d所示。可以看出,隨著反應溫度的提高ID/IG的值降低,I2D/IG的比值提高。這表明,隨著反應溫度的提高得到的石墨烯的質量不斷提高。其原因是,隨著反應溫度的提高葡萄糖分解產生的CO2變得活躍,與Mg基體的反應更加充分,使石墨烯的質量提高。堿土金屬鎂的還原性較高,能與CO2發生氧化還原反應釋放大量的熱,促使還原的碳在高能量下轉變成石墨烯。同時,由于C與金屬的潤濕性較差,反應生成的C晶體優先相連形成片狀結構,最終得到石墨烯薄片。
Raman譜的分析結果表明,反應溫度越高得到的石墨烯的質量越高。對在780℃原位生成的石墨烯進行XRD分析,結果如圖3所示。可以看出,與標準PDF卡片對比發現,位于2θ=26.3°、44.3°和50.4°的明顯特征峰分別對應石墨烯的(002)、(101)和(102)晶面。XRD分析結果進一步證明,高溫熱壓燒結后葡萄糖粉末與鎂基體通過原位反應生成了石墨烯。
圖3
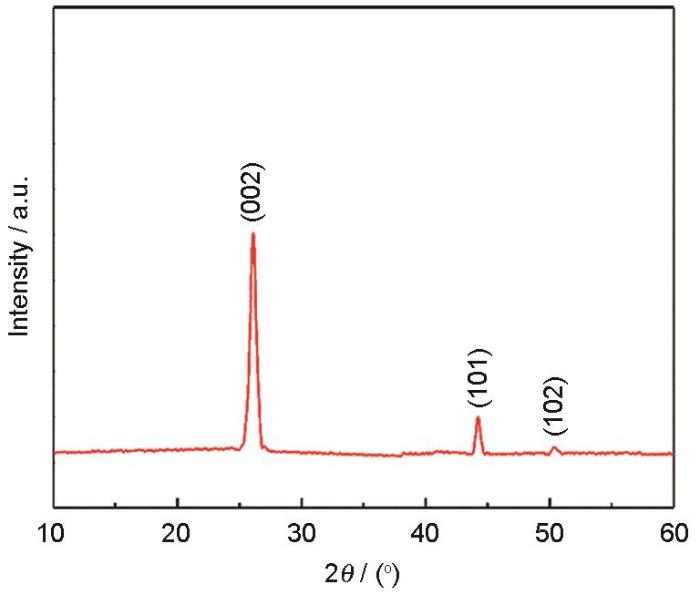
圖3 在780℃原位自生的石墨烯的XRD譜
Fig.3 XRD analysis of the in-situ generated graphene at 780℃
對在780℃原位生成的石墨烯進行XPS分析,結果如圖4所示。由圖4a可見,在780℃熱壓燒結反應生成的石墨烯氧含量較低,總的碳氧比:為92:5。對原位生成的石墨烯的碳峰進行分峰擬合,發現石墨烯的碳主要以sp2雜化的碳原子為主,且包含了C-O和C-O=C兩種官能團,如圖4b所示。XPS分析結果表明,原位反應生成的石墨烯氧含量較低,缺陷較少,表明石墨烯的質量較高。
圖4
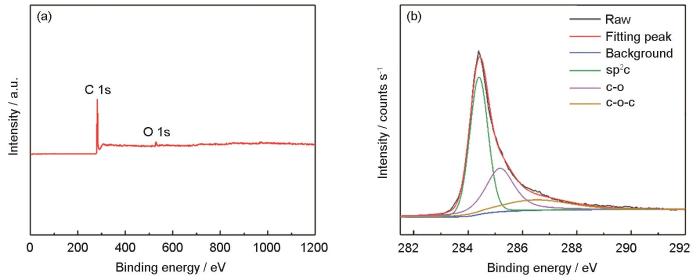
圖4 在780℃原位自生石墨烯的XPS分析
Fig.4 XPS analysis of in-situ graphene at 780℃ (a) Carbon-oxygen ratio of in-situ generated graphene; (b) Fitting of carbon peaks of in-situ graphene
圖5給出了在780℃原位生成的石墨烯的SEM微觀形貌以及在鎂基體中的分布。如圖5a所示,石墨烯的形狀較為完好,沒有明顯的空洞和缺陷。進一步觀察發現,原位生成的石墨烯呈現片狀,其尺寸為3~5 μm,如圖5b和c所示。觀察圖5d可見,原位反應生成的石墨烯在鎂基體中分散均勻,沒有出現明顯的團聚。這表明,用原位反應方法合成石墨烯增強的鎂基復合材料,能避免增強相在基體中的團聚,且石墨烯呈片狀分布,沒有明顯的缺陷,進一步證明該方法的有效性。
圖5
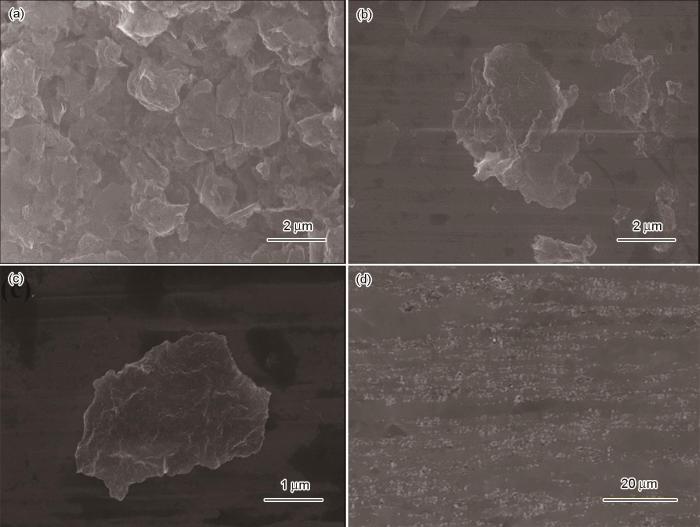
圖5 在780℃原位自生石墨烯的SEM形貌和在鎂基體中的分布
Fig.5 SEM morphology of in-situ graphene at 780℃ and its distribution in magnesium matrix (a) Micro morphology of in-situ generated graphene; (b) and (c) are enlargements of figure (a); (d) Distribution of in-situ graphene in magnesium matrix
圖6給出了在780℃原位生成的石墨烯的TEM微觀形貌。如圖6a和b所示,石墨烯的形貌完好,沒有明顯的空洞或缺陷。薄片狀石墨烯的曲卷程度較低,質量較高。HRTEM觀察發現,石墨烯的層厚為5~15層,厚度約為3~5 nm,如圖6c所示。TEM觀察發現,石墨烯的質量較高,形貌較為完好;完整的石墨烯形貌在基體中有增強效果,阻礙位錯運動和抑制晶粒的長大。如圖6d所示,石墨烯與鎂基體的界面結合良好,沒有明顯的微裂紋和微孔。良好的界面結合,有利于復合材料性能的提高。
圖6
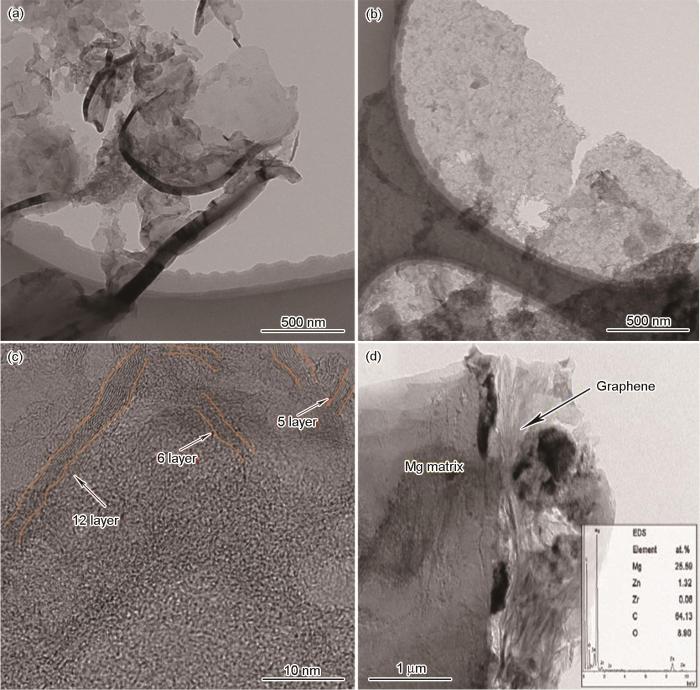
圖6 在780℃原位自生石墨烯的TEM形貌
Fig.6 TEM morphology of in-situ graphene at 780℃ (a) and (b) Micro morphology of in-situ generated graphene; (c) HRTEM of in-situ generated graphene; (d) The interface between graphene and magnesium matrix
2.2 石墨烯增強鎂基復合材料的力學性能
圖7給出了在不同溫度原位自生石墨烯增強鎂基復合材料的力學性能,其中反應溫度為25℃表示純AZ31鎂合金基體。如圖7所示,隨著原位反應溫度的提高鎂基復合材料的力學性能隨之提高。反應溫度為700℃時復合材料的屈服強度、抗拉強度和延伸率分別達到190 MPa、305 MPa和5.3%;反應溫度提高到780℃復合材料的屈服強度、抗拉強度和延伸率達到最大值,分別為245 MPa、340 MPa和6.7%,比以純AZ31基體的力學性能分別提高了40%、21.4%和48.8%。其原因是,對于用原位反應制備的復合材料,石墨烯與鎂基體的熱膨脹系數很大的差別,導致在熱擠壓過程中界面結合處出現較大的熱應變區。該區域較大的熱錯配殘余應力,使該處產生密度較高的位錯。這些位錯促進動態再結晶,從而使復合材料的晶粒細化,使其性能提高[19];另一方面,在復合材料的晶粒長大過程中,石墨烯在鎂基體中的均勻分布有效阻礙了晶粒生長,從而產生細晶強化[20],同時,在材料加載過程中,力學性能優異的二維石墨烯能分擔較多的載荷,使復合材料的綜合性能提高。
圖7
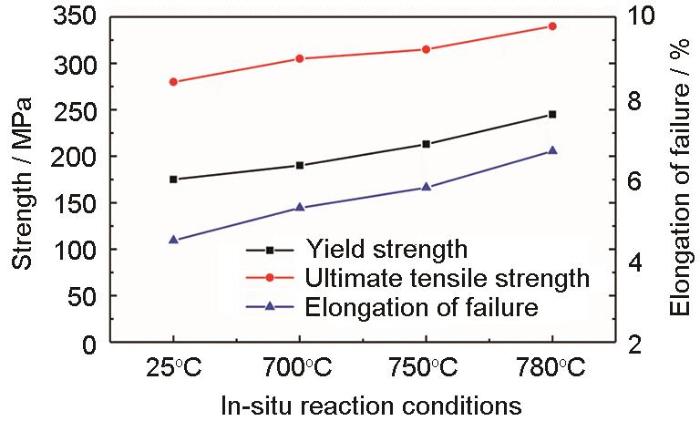
圖7 原位自生石墨烯增強鎂基復合材料的力學性能
Fig.7 In-situ in-situ graphene reinforced mechanical properties of magnesium matrix composites
圖8給出了在780℃原位自生石墨烯增強鎂基復合材料的拉伸斷口形貌。如圖8a所示,在拉伸斷口沒有明顯的微裂紋和微孔存在,表明石墨烯與鎂基體界面結合良好,沒有出現斷裂。對圖8a放大后可見,斷口處有大量的韌窩,表明復合材料的斷裂方式以韌性斷裂為主。觀察發現,在斷口表面有石墨烯碎片,因為石墨烯與鎂基體的潤濕性不好,復合材料承受較大的拉伸應力時,在石墨烯與鎂的界面結合處萌生裂紋。隨著應力的加大微裂紋擴展,最終使復合材料斷裂。
圖8
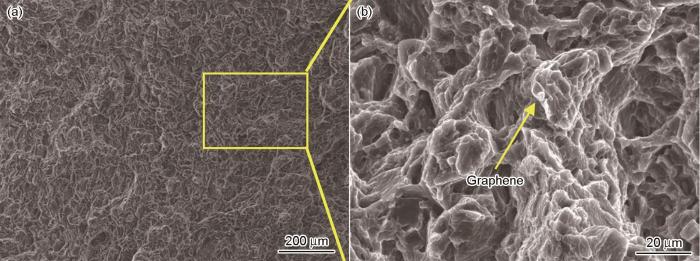
圖8 在780℃原位自生石墨烯增強鎂基復合材料的斷口形貌
Fig.8 Fracture morphology of in-situ graphene reinforced magnesium matrix composite at 780℃ (a) Tensile fracture morphology; (b) is an enlargement of (a)
3 結論
(1) 使葡萄糖粉末與鎂發生化學反應和在不同溫度進行熱壓燒結,可制備原位自生石墨烯增強鎂基復合材料,原位自生的石墨烯在鎂基體中分布均勻。
(2) 改變反應溫度,可使原位自生的石墨烯的質量不斷提高。反應溫度為780℃生成的片狀石墨烯缺陷較少、質量最高,其厚度為3~5 nm,尺寸約為4 μm。
(3) 石墨烯增強鎂基復合材料的力學性能隨著反應溫度的提高而提高,反應溫度為780℃制備的復合材料其性能最佳,屈服強度、抗拉強度和延伸率分別為245 MPa、340 MPa和6.7%,比AZ31基體的力學性能分別提高了40%、21.4%和48.8%。
免責聲明:本網站所轉載的文字、圖片與視頻資料版權歸原創作者所有,如果涉及侵權,請第一時間聯系本網刪除。
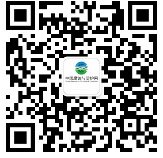
官方微信
《腐蝕與防護網電子期刊》征訂啟事
- 投稿聯系:編輯部
- 電話:010-62316606-806
- 郵箱:fsfhzy666@163.com
- 腐蝕與防護網官方QQ群:140808414