鎂合金是目前實際使用的密度最小的一種金屬材料,具有比強度高、導電導熱性能好、切削加工性好、生物相容性良好等特點,但由于其化學穩定性差且表面氧化膜疏松多孔,耐腐蝕性能差,導致其應用受到嚴重限制。
01 腐蝕行為
鎂的標準電極電位為-2.37V,其高電負性使鎂在不存在氧氣的情況下也會發生腐蝕,這致使鎂合金在應用時的耐腐蝕性較差。根據PB(Pilling-Bedworth)原理,鎂合金表面膜層并非是致密狀態,無法對鎂合金基體提供長期保護作用。通常使用致密系數來衡量氧化膜的致密程度,該參數是金屬與氧結合在其表面生成氧化膜的體積與所消耗金屬體積之比。MgO膜的致密系數為0.81,而當致密系數小于1時,氧化膜會因受拉應力而難以鋪滿金屬表面,所以MgO膜對基體不具備一定的保護能力。 鎂的標準電極電位低,在電化學腐蝕過程中鎂作為陽極失去電子而被腐蝕,陰極產生氫氣,在堿性或中性環境以及酸性環境下的陰極反應分別為 陰極可能是與鎂合金相接觸的其他金屬部件,也可能是合金元素或雜質,與鎂合金基體形成原電池,從而發生腐蝕;該反應與溶解在水中的氧氣含量無關。對于暴露在大氣環境中的鎂合金,還原反應主要是水的還原反應,反應式為 鎂合金腐蝕機理和過程十分復雜,表面雜質、鎂合金的合金元素、陽極溶解區域等均會對其腐蝕機理產生影響,因此仍需深入研究電化學反應過程中的各種因素對腐蝕的影響。 02 表面處理技術
由于鎂合金化學性質活潑,表面氧化膜無法對鎂合金基體起到有效的防護,因此為了使鎂合金得到高效的利用并獲得更長的使用壽命,需要對其表面進行處理。目前比較成熟的表面處理技術有化學氧化、陽極氧化、微弧氧化和有機涂層等。 化學氧化是鎂合金常用的表面處理技術之一,具有成本低、易于處理等優點。化學氧化的基本原理是金屬浸入轉化液中,與轉化液發生一系列化學-電化學反應,將一些難溶(化學性質穩定)化合物沉積在金屬表面而形成氧化膜,得到的氧化膜具有很好的耐腐蝕性能,并與基體具有較強的結合力,從而起到保護基體的作用。鎂合金化學氧化后形成的氧化膜可以分為含鉻氧化膜和不含鉻氧化膜,其中不含鉻氧化膜包括磷酸鹽系氧化膜、氟鋯酸鹽系氧化膜、錫酸鹽系氧化膜、高錳酸鹽系氧化膜、稀土氧化膜等。 含鉻氧化膜是目前應用比較成熟的化學氧化膜。鉻化處理可在鎂合金基體表面形成金屬基體氧化物和鉻酸鹽組成的混合氧化物膜,Cr6+的含量越高,氧化膜的自愈合能力越強。鉻化處理工藝成熟,但由于鉻酸鹽中的Cr6+具有毒性,對人體和生態環境有較大的危害,因此含鉻氧化膜已經被限制使用,不含鉻氧化膜成為了研究熱點。 ZAI等研究了轉化液pH(2.5,3.0,3.5,4.0)和制備溫度(40,60,80℃)對AZ31鎂合金表面磷酸鎂氧化膜耐腐蝕性能的影響,發現制備溫度比轉化液pH對氧化膜的耐腐蝕性能影響更大,在制備溫度80℃、轉化液pH為3.0條件下形成的氧化膜具有最好的耐腐蝕性能。 NIU等在鎂合金表面制備了釩酸鹽氧化膜,發現在含有4g·L-1NaVO3中形成的釩酸鹽氧化膜的微觀結構精細、無裂紋。 PHUONG等研究發現,在AZ31鎂合金表面制備的磷酸鋅氧化膜比磷酸鎂氧化膜具有更高的自腐蝕電位和更低的自腐蝕電流密度,但由于磷酸鋅氧化膜的孔隙率高,因此在鹽霧條件下比磷酸鎂氧化膜更易發生腐蝕。 稀土化學氧化可分為單一稀土化學氧化、雙稀土復合化學氧化和摻雜稀土鹽的其他金屬鹽化學氧化。稀土氧化膜具有較好的耐腐蝕性能,轉化液對環境友好,對人體無害,且稀土化學氧化的工藝簡單,因此稀土氧化膜具有良好的發展前景。 鎂合金的化學氧化膜較薄(厚度0.5~3 μm),且為多孔結構,導致其耐腐蝕性能仍不是很理想,且耐磨性較差,適用于對環境溫度和表面質量精度要求不高的構件,如筆記本、手機及其他電子產品的外殼。化學氧化膜只能減緩腐蝕速率,并不能長期防止腐蝕,因而不可作為長期防腐保護層。 陽極氧化是指在特定的電解液中,利用電流在鎂合金表面生成耐腐蝕性較好的沉積膜的過程。鎂合金陽極氧化技術優勢在于所形成的氧化膜與基體結合強度高,且其耐腐蝕性能較好。 電解液的開發是陽極氧化技術的核心之一,電解液必須滿足無毒無污染、環境兼容性好等特點。 章鈺等對陽極氧化電解液進行優化,在優化的工藝條件下制備的陽極氧化膜表面平整、致密,與基體的結合力強,主要由鎂、氧、硅3種元素組成,對鎂合金基體有良好的防護性。 張小玲等配制了一種不含鉻、磷、氟的鎂合金陽極氧化電解液,通過正交試驗優化電解液獲得一種既滿足環境保護又可有效提高鎂合金耐腐蝕性能的陽極氧化膜。 ZHANG等研究發現,單寧酸作為一種有機添加劑,可以促進鎂合金表面陽極氧化膜的形成,同時單寧酸可通過形成不溶性鎂-單寧酸絡合物來改善陽極氧化膜表面微孔均勻性,并增加陽極氧化膜的厚度,從而提高其耐腐蝕性能。 伏田田等研究發現,在堿性電解液中加入腺嘌呤后,AZ31鎂合金表面陽極氧化過程的電壓更為平穩,電火花放電更均勻,所得到的氧化膜更平整,并且膜中孔洞數量減少,氧化膜致密性提高,耐腐蝕性能增強。 畢燴元等研究發現,在電解液中添加納米碳化鈦后,鎂合金表面陽極氧化膜均勻致密,其中的微孔孔徑減小,自腐蝕電流密度減小,氧化膜的耐腐蝕性能提高。 付廣艷等研究發現,六次甲基四胺的添加降低了電解液的導電性,使得AZ91D鎂合金表面的陽極氧化電壓升高,反應加快,所得到的氧化膜厚度增加,耐腐蝕性能增強。 陽極氧化膜中含有微孔,這會影響其耐腐蝕性能。陽極氧化膜可以作為中間層來提高有機涂層或其他防護涂層與基體之間的結合力,從而達到長期防護的效果。陽極氧化過程需要消耗大量電能,生產成本高,限制了該方法的廣泛應用,因此研究出對環境友好、低能耗和膜性能高的鎂合金陽極氧化工藝是十分有必要的。 微弧氧化又稱微等離子體氧化,微弧氧化膜具有耐腐蝕、耐磨損、硬度高、介電常數低等優點。在微弧氧化工藝中,陽極為鎂合金,陰極為用不銹鋼制成的圓柱體容器。在微弧氧化過程中鎂合金表面先形成一層薄而致密的氧化層,隨后在其上沉積一層含有微孔和微裂紋的多孔層;這種雙層結構微弧氧化膜的形成可以提高鎂合金的耐腐蝕性能。 曹雅心等研究發現:隨著硅酸鹽體系電解液中KOH質量濃度由2 g·L-1增加到4 g·L-1,LA103Z鎂鋰合金表面微弧氧化膜中微孔孔徑變大,數量減少,當KOH質量濃度繼續增大至6 g·L-1時,微弧氧化膜結構疏松,內部缺陷增多;隨著KOH質量濃度的增大,微弧氧化膜在質量分數3.5% NaCl溶液中的耐腐蝕性能先變好后變差;當KOH質量濃度為4 g·L-1時,微弧氧化膜的均勻性最好,孔隙率最低,耐腐蝕性能最好。 利用微弧氧化技術,在鎂合金表面制備含耐腐蝕性好的其他物質也是提高微弧氧化膜耐腐蝕性能的一種方法。 TANG等采用微弧氧化方法在AZ31鎂合金表面制備了一層厚度為5 μm的含CaTiO3的氧化膜,與鎂合金基體相比,所制備的微弧氧化膜具有更高的自腐蝕電位、更低的自腐蝕電流密度,更優異的耐腐蝕性能。 SHI等使用一步法和兩步法在WE43鎂合金表面制備了含硒微弧氧化膜,硒以Se2-和Se0形式存在于微弧氧化膜中,含硒微弧氧化膜有效提高了WE43鎂合金的耐腐蝕性能;與采用一步法制備的微弧氧化膜相比,采用兩步法制備的微弧氧化膜中微裂紋較少,厚度較大,耐腐蝕性能更好。 微弧氧化膜與基體結合強度高,相比于陽極氧化膜,其厚度可控,可達幾百微米,但表面也存在微孔,會降低其耐腐蝕性能的提高程度,因此需對其進行有效的封孔處理。 常見的封孔處理有后處理封孔和自封孔工藝兩類,后處理封孔指在生成微弧氧化膜后進行封孔的技術,自封孔工藝指在微弧氧化膜形成的過程中同步進行封孔的技術。其中,自封孔微弧氧化膜具有結合力強、封孔效果好、耐腐蝕性能好等優點,主要通過電解液自封孔、外加電場自封孔兩種方法獲得。 微弧氧化工藝拓展了鎂合金的應用領域,使鎂合金的耐腐蝕性能、耐磨性均得到顯著的提高,具有良好的應用前景。 可用氟碳涂料、聚氨酯涂料、醇酸樹脂涂料以及環氧類涂料等有機涂層對鎂合金表面進行防護。有機涂層的保護機理主要是隔絕、屏蔽和電化學保護。有機涂層品類繁多,經濟實惠,適應性廣泛,施工簡單。選用合適的有機涂料,經過適當的預處理涂覆在鎂合金表面,可以有效提高鎂合金的耐腐蝕性能。但是有機涂層與基體的結合力不好,在嚴苛環境下可能會出現脫落問題,使鎂合金基體暴露在腐蝕介質中。 李浩等研究發現,與鎂合金表面直接涂覆的茶多酚層相比,陽極氧化/茶多酚復合涂層的耐腐蝕性能較好,且陽極氧化后表面與茶多酚涂層的結合力更好。作者所在課題組研究發現:在臭氧體積分數為0.0016%的臭氧老化試驗箱中放置30天后,涂覆氟碳涂料的鎂合金表面無明顯變化,具有良好的抗氧化性,這與氟碳涂料中C-F鍵鍵能大且分子鏈中不含不飽和鍵有關;在中性鹽霧環境中放置15天后,涂覆氟碳涂料的鎂合金表面無點蝕或其他腐蝕現象出現,具有良好的耐鹽霧腐蝕性能。 有機涂層種類繁多,適應性強且操作簡單,在提高鎂合金表面耐腐蝕性能方面具有很大的優勢,但因有機涂層比微弧氧化膜、陽極氧化膜厚,不適用于小構件。為了克服有機涂層與鎂合金結合力弱的問題,可以采用底漆加面漆的解決方法。 表面鍍鎳技術難以在不規則試樣表面形成均勻鍍層,而且存在著嚴重的廢水處理問題;氣相沉積方法可以制備出硬度高、耐腐蝕性能良好和孔隙率低的MgO層,但對制備溫度要求較高,工藝復雜;激光表面改性處理技術要求較高,在不規則試樣表面難以形成均勻涂層,難以投入使用。 WATAZU等采用射頻磁控濺射工藝和平面磁控濺射系統在低鋁單相鎂合金表面沉積了致密的MgO薄膜,在一定程度上提高了鎂合金的力學性能,但是在潮濕的大氣環境中鎂合金的耐腐蝕性能較差。作者所在課題組使用電鍍的方法在ME20M鎂合金表面鍍鎳后,試樣表面存在一些微小突起,經過5天鹽霧腐蝕試驗后,突起部分發生腐蝕并有向外擴散的趨勢,試樣其他部位無腐蝕現象出現。 03 結束語
近年來,鎂合金由于其獨特的性能優勢而受到國內外研究人員的關注,特別是在綠色經濟的背景下,鎂合金的受重視程度日益上升。 在無水干燥的天氣環境中,鎂與氧發生反應生成MgO,而在潮濕大氣環境中,鎂合金表面腐蝕產物主要為Mg(OH)2和MgO,且環境pH對其腐蝕速率有很大影響;但是多種環境下的腐蝕機理研究較少。陽極氧化、微弧氧化表面處理技術盡管在一定程度上可以增強鎂合金的耐腐蝕性能,但陽極氧化膜、微弧氧化膜中有許多微孔隙,目前自封孔技術中所使用的電解液多為含氟電解液,對環境不友好。針對上述問題,未來的研究應主要集中在: (1) 工藝流程以及工藝參數對各種表面處理技術影響方面; (2) 基礎研究方面,探索鎂合金在含有CO2、SO2、O3等大氣環境中的腐蝕機理及腐蝕過程; (3) 環保型自封孔電解液的研究; (4) 稀土氧化膜、磷酸鹽系氧化膜等不含鉻氧化膜等方面的研究,拓寬鎂合金在更多場景下的應用。
免責聲明:本網站所轉載的文字、圖片與視頻資料版權歸原創作者所有,如果涉及侵權,請第一時間聯系本網刪除。
-
標簽: 鎂合金
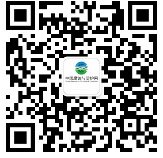
官方微信
《腐蝕與防護網電子期刊》征訂啟事
- 投稿聯系:編輯部
- 電話:010-62316606-806
- 郵箱:fsfhzy666@163.com
- 腐蝕與防護網官方QQ群:140808414