復合層能夠有效提高零部件的表面質量、降低維護成本并延長使用壽命,因此廣泛用于石油化工、工程機械、航海等領域零部件的表面性能改善等。
碳化鎢材料具有良好的熱穩定性、化學穩定性、抗氧化性,還具有熔點高、硬度大,耐磨性好的特點,因此常用作表面涂層。然而,純碳化鎢的潤濕性較差,不能直接用于涂層制備,因此常將Co、Ni等金屬作為黏結金屬與純碳化鎢粉末混合,制造硬質合金和耐磨涂層。
超聲速火焰噴涂
超聲速火焰噴涂技術又稱高速氧燃料火焰(HVOF)(噴涂)技術,是一種基于高速度粒子獲得涂層的技術。利用特制的燃燒室或特殊的噴嘴,噴射引燃燃氣或液體燃料形成高速、高壓、高溫的燃燒焰流,金屬粉末經惰性氣體送入焰流中加熱,熔融的金屬粉末加速撞擊基體表面并快速凝固,連續沉積從而形成涂層。
01 工藝參數對涂層性能的影響
姚舜暉采用HVOF技術制備了碳化鎢(WC,質量分數為20%)增強鎳基合金涂層,研究表明WC顆粒的幾何形狀對于涂層耐磨性影響較大,對于圓形WC顆粒來說,在一定粒徑范圍內,其耐磨增強效果與顆粒直徑正相關。
趙文勝分析了粉末粒徑和噴涂道次對涂層耐磨性和耐蝕性的影響,結果表明所得涂層的孔隙率均小于1.5%,顯微硬度為1000 HV,粉末粒徑越小,涂層的孔隙率越低,且粉末粒徑為5~15 μm,噴涂8道次條件下所得涂層在3.5%氯化鈉溶液中的耐蝕性較好。
王大鋒等研究了納米結構、亞微米結構和常規結構的WC-10Co-4Cr涂層,發現涂層的脫碳率和孔隙率呈現先增大后減小的趨勢,納米結構涂層的顯微硬度最高,亞微米結構涂層的顯微硬度最低。
趙立英等研究表明,在HVOF噴涂過程中添加丙烷,可有效降低涂層的氧化和脫碳問題,涂層硬度和附著力隨丙烷流量提高呈現出先升高后降低的趨勢、而涂層孔隙率則先降低后升高。
張磊等的研究結果表明:涂層的孔隙率隨送粉速率和噴涂距離的增大先降低后升高,隨噴涂角度和丙烷流量的升高而降低;涂層顯微硬度隨噴涂角度的增大而升高,隨丙烷流量、噴涂距離和送粉速率的增大先升高后降低。
劉杰等分析了煤油流量對于WC-12Co/NiCrBSi復合涂層的影響,結果表明隨著煤油流量提高,涂層硬度提高,涂層孔隙率和耐磨性先降低后升高,涂層孔隙率最低為0.11%,硬度為927 HV。
韓旭等研究發現,粒子速度、溫度和直徑不沿火焰中心線對稱,并且粒徑越小,速度越高。
SONESTEDT等研究發現隨著粉末粒徑的增大和火焰功率的減小,涂層中Ti2AlC的含量增加,但涂層厚度減小,黏結性降低。
CABRAL-MIRAMONTES等研究發現涂層厚度隨著噴射距離的增加而減小,火焰中粒子的溫度隨著噴射距離增加而升高,最佳噴射距離為229~254 mm。
MENDEZ-MEDRANO等分析了火焰類型(還原性、中性和氧化性)和噴槍噴嘴出口區域對于涂層組織、晶體結構的影響后發現,WC顆粒在噴涂過程中發生了相當程度的脫碳和溶解,相變程度取決于火焰化學成分,涂層的微觀結構主要受噴嘴的影響。
JONDA等分析了基于HVOF制備的AZ31基體上WC-Co-Cr涂層的相組成、殘余應力,結果表明相組織的峰值與WC有關,殘余應力為壓應力。
02 涂層的耐磨耐蝕性
代雪婷等采用HVOF技術在AF1410鋼表面制備了厚200~220 μm的WC-10Co-4Cr涂層,并與電鍍硬Cr涂層進行對比,結果表明WC-10Co-4Cr涂層的摩擦因數低于后者,磨損質量和磨損深度也遠低于后者,但是二者的耐蝕性無明顯區別。
劉福朋采用HVOF技術在304不銹鋼基體上制備了WC-Co和NiCr-Cr3C2合金涂層,其硬度為1100~1400 HV,硬質相和黏結相相互錯落分布,WC-Co在H2SO4中的腐蝕速率與H2SO4溫度和濃度呈現正相關規律。
劉建武等采用HVOF技術制備了WC-10Co4Cr涂層,其硬度為1315 HV,孔隙率為0.33%,與傳統鍍鉻層相比,硬度和耐磨性分別提高了約2倍和3.6倍。此外,WC-10Co4Cr涂層結構致密、結合強度高,具有良好的抗鹽霧腐蝕性能。
黃博等研究發現WC-10Co-4Cr涂層的硬度隨噴涂距離增大而提高,但是涂層孔隙率隨噴涂距離增大而降低,涂層硬度最高為1100~1400 HV,此時涂層孔隙率小于1%,且在鹽溶液中,涂層的耐磨性比304不銹鋼高2個數量級。
范俊等研究發現WC-Co-Ni涂層中的WC相較多,力學性能較均衡,抗電化學腐蝕性能較好。
KOMAROV等討論了不同粒徑碳化鎢粉末和顆粒組合對涂層疏水性的影響。結果表明粗粉和超細碳化鎢顆粒組合可用于制備高疏水性硬質涂層,通過化學改性可使涂層進一步變為超疏水性硬質涂層。
JIN等分析了表面載荷對于HVOF技術制備的WC-12Co涂層耐磨性的影響。結果表明Fe和W在涂層與基體界面處的相互擴散使涂層具有良好的附著力,摩擦因數隨著表面載荷增加而增大。
ASL等研究發現,采用HVOF技術所得WC-17Co涂層結構致密,厚度為500 μm,但后續進行真空熱處理易導致涂層附著失效。
等離子噴涂
等離子噴涂(PS)是一種以直流驅動的等離子弧為熱源的熱噴涂技術。
01 工藝參數對涂層性能的影響
宋超群等研究發現當噴涂功率過低時,WC顆粒融化程度低;而當噴涂功率過大時,WC又會出現脫碳現象,最佳噴涂功率為65 kW,此時涂層孔隙率最低(0.87%)。
李萬青等研究發現采用PS技術所得納米結構涂層的致密性和結合強度高于微米涂層,前者孔隙率僅為0.56%,兩者硬度相差不大。
黎紅英等對比分析了大氣等離子噴涂(APS)和HVOF技術的工藝參數對WC-Ni涂層性能的影響。結果表明較大功率下,APS所得涂層致密,但脫碳程度大;當噴涂距離較小時,HVOF技術所得涂層致密,脫碳程度小。
AFZAL等研究發現,在一定范圍內,較遠噴涂距離條件所得涂層的孔隙率較低,厚度較小,界面良好。
鮑君峰等研究發現0.8 μm粒徑條件下,WC-17Co涂層的力學性能最好,隨著WC粒徑增大,涂層孔隙率增大,結合強度和硬度降低,磨損量增大。
富偉等研究發現,在適當的噴涂距離下,涂層脫碳程度和致密度隨噴涂功率上升而上升。
安連彤等分析發現,提高電弧電壓有利于粉末的融化,提高涂層耐磨性和硬度,但電壓過高會反而使Wc-Co涂層質量劣化。
伏利等利用高焓等離子噴涂法所得WC-10Co-4Cr涂層的孔隙率為0.77%,硬度達到1210 HV,耐磨性為0Cr13Ni4Mo鋼基體的143倍,適當提高粒子速率和溫度可提高涂層結合強度。
KUZMIN等基于超音速空氣等離子噴涂噴槍,制作了孔隙率小于0.4%的WC-10Co-4Cr涂層,其硬度也比HVOF所得涂層更高。
ANWAR等采用氮氣包裹CO2激光對WC-12Co涂層進行表面處理后發現,表面涂層的附著力和基體硬度顯著提高,且表面無缺陷。
02 涂層的耐磨耐蝕性
梁存光等的研究表明噴涂距離太近,WC涂層的脫碳行為嚴重,耐磨性較差,而噴涂距離過遠,涂層結合強度低,抗沖蝕及磨蝕能力差。
徐一等分析了基于超音速等離子噴涂的WC-10Co4Cr涂層在不同條件下的耐磨行為,結果表明涂層中存在未融化顆粒,涂層硬度達到1408.2 HV,干燥條件下涂層磨損以磨料磨損為主,濕潤條件下以黏著磨損為主,后者磨損率遠低于前者。
袁曉靜等研究發現采用PS所得納米結構WC-10Co4Cr涂層在高低溫下的摩擦因數和磨損率優于微米結構涂層,可有效提高1Cr18Ni9Ti鋼在3.5% NaCl溶液中的腐蝕電位。
JIANG等對比分析了基于APS和HVOF技術制備的Al2O3-40TiO2和WC-10Co-4Cr兩種涂層在NaCl溶液中的耐蝕性,結果表明短期內WC-10Co-4C涂層的耐蝕性更好,但是Al2O3-40TiO2涂層的長期耐蝕性更好。
HOU等研究了噴涂功率對WC-(W,Cr)2C-Ni涂層性能的影響,結果表明中等噴涂功率下所得涂層的斷裂韌性最高,界面結合力最強,耐磨性最好。
等離子熔覆
等離子熔覆技術的原理在于將等離子弧熱源作用在預制的熔覆層粉末或者同步送粉,使熔融的粉末與部分熔化的基體呈現冶金結合。
01 工藝參數對熔覆層的影響
盧金斌等利用等離子熔覆技術在Q235碳鋼表面制備了含50% Ni-WC的Fe-Cr-B-Si合金涂層,其顯微硬度為560~820 HV。
屈平等采用等離子熔覆技術在Q235碳鋼表面制備了Ti(C,N)-WC涂層,結果表明在一定范圍內,涂層硬度和耐磨耐蝕性隨碳化鎢含量提高而提高,并且當碳化鎢質量分數為12%時,涂層的耐磨耐蝕性最優。
王笑生采用等離子熔覆技術在Q235鋼板上制備了鎳基碳化鎢熔覆層,并分析了鑄造和單晶碳化鎢含量對鎳基合金防護性能的影響。結果表明在Ni25合金熔覆層中加入60%鑄造碳化鎢,涂層耐磨性最佳,單晶碳化鎢熔覆層的耐磨性較低。
PENG等研究發現隨著WC含量的增加,FeCoCrNi高熵合金/碳化鎢復合涂層的組織變得更加復雜,當WC質量分數為60%時,涂層具有最佳的耐磨性,硬度為690 HV。
02 熔覆層的耐磨耐蝕性
XIE等研究表明,三種鎳基WC涂層表面無裂紋且孔隙率極低(<1%)。等離子熔覆層的維氏顯微硬度隨熔覆WC量的增加而增加。熔覆層的顯微硬度和電化學行為與鍍鎳WC粉的含量有關,熔覆層的腐蝕可能是熔覆層中相間的微鍍鋅腐蝕。
胡明強采用等離子熔覆技術在高錳鋼表面制備碳化鎢-鎳基合金復合涂層,結果表明熔覆涂層厚度可達1~2 mm,且涂層質量好,表面無缺陷,涂層表面硬度最高為621.77 HV。
吳磊等利用等離子熔覆技術制備了涂層,研究碳化鎢含量對于鎳基碳化鎢涂層組織性能的影響,結果表明涂層表面無氣孔缺陷,在一定范圍內,涂層耐磨性和硬度隨碳化鎢含量顯著提高,當碳化鎢質量分數為50%時,涂層硬度和耐磨性最好,硬度達到1024 HV。
XIE等研究發現在室溫下,涂層的耐磨性隨著WC含量的增加而逐漸提高,硬度最高達到954.64 HV,隨著溫度的升高,涂層的耐磨性下降,碳化鎢/鈷基涂層的磨損機制為氧化磨損。
激光熔覆
激光熔覆(LC)是將高功率密度激光束輻照到基材表面,使基材與熔覆層材料迅速熔化凝固,獲得與基材冶金結合的涂層。
01 工藝參數對熔覆層的影響
張煜等對比分析了超高速和低速激光熔覆技術對涂層的影響,結果表明采用超高速激光熔覆技術,可以在保證冶金結合的同時,大大抑制基體元素對涂層稀釋,同時抑制涂層中WC顆粒熱損傷和空隙的形成,降低殘余應力,避免裂紋產生。
邱煥霞等通過數值模擬方法發現預熱可明顯降低激光熔覆層的溫度梯度和冷卻速度,抑制表面裂紋生成,且最優預熱溫度為200 ℃。
劉澤研究了不同尺度WC對Ni基熔覆層微觀結構的影響,結果表明在微米尺度涂層的界面結合力和晶粒尺寸隨熱處理溫度的提高而升高,但是硬度和耐蝕性則隨熱處理溫度的提高而下降;亞微米結構涂層的摩擦因數和磨損率隨熱處理溫度的升高呈現出先降低后增加的現象;微納米結構涂層的沖蝕磨損速率分別為微米和亞微米結構涂層的1/24、1/6。
朱繼祥研究發現,當WC質量分數為20%~50%時,WC鐵基涂層的硬度值隨WC含量的上升而提高,且當WC質量分數為30%時,涂層的耐磨性最優。采用數值模擬方法研究發現熔覆層與基材結合處存在較大殘余拉應力,易產生縱向裂紋。
樊帥奇等討論了Ni60+30% WC涂層和Ni60+30% Ni涂層中WC初始形態對涂層性能的影響。結果顯示前者內部存在少量孔洞和微裂紋,后者組織均勻致密,無氣孔和裂紋。
ZHOU等研究發現激光熔覆涂層的裂紋主要源于熔覆層和基體的界面,提高激光熔覆速率可以降低復合涂層的孔隙率,此外,提高基體預熱溫度可大大降低涂層出現裂紋可能性。
ERFANMANESH等對比分析了鍍鎳WC-12Co粉末和商用WC-12Co粉末對激光熔覆層性能的影響,結果發現前者能顯著降低復合涂層的孔隙率,獲得高質量的復合涂層。
BARTKOWSKI等分析了工藝參數對于Fe/WC金屬基復合涂層性能的影響,結果表明復合層厚度隨著激光功率和進粉速度提升而增厚,當送料速度為12.50 g/min時,復合涂層的顯微硬度達到1400 HV,涂層的耐蝕性隨著涂層中WC含量的增大而增強。
02 熔覆層的耐磨耐蝕性
李禮等在Cr12MoV鋼表面激光熔覆Ni60A-35% WC涂層,研究顯示涂層與基體間無裂紋和氣孔缺陷,硬度為基體的1.7倍。涂層的磨損機理為疲勞磨損和磨粒磨損,而基體則為黏著磨損和磨粒磨損。
肖奇等研究發現在一定范圍內,WC可細化Ni60A-WC涂層晶粒,Ni60A-WC 涂層在不同pH環境中的耐蝕性與WC加入量呈負相關,復合涂層在中性、堿性和酸性腐蝕環境中的耐蝕性依次遞減。
楊行等分析了WC含量對于WC-Cr覆層耐磨性影響,結果表明25WC-1.5C覆層的顯微硬度達到666.3 HV,磨損率僅為基體的30%。
何波等研究發現碳化鎢/鈷基合金復合涂層的顯微硬度和耐磨性比Co基合金涂層明顯提高,且磨損質量損失量僅為后者的48%。
真空熔覆
真空熔覆技術是將具有需某種特殊性能的金屬粉末涂敷在預處理后的零件表面,在一定真空度下,經一段時間高溫燒制后,涂覆層與基體間產生分子間結合或化學結合,進而提高零件的使用性能和壽命的技術。
01 參數對熔覆層的影響
路王珂等分析了WC含量、熔覆溫度對鎳基真空熔覆層的影響。結果表明隨著WC質量分數從20%增大到40%,熔覆層的耐磨性提高,但是結合力出現先增后降趨勢,當WC質量分數為40%時,WC顆粒之間或者周圍出現大量孔洞。熔覆層厚度隨熔覆溫度升高而增厚,但若溫度過高,WC顆粒會分解嚴重,熔覆層耐磨性下降,最優熔覆溫度為1225 ℃。
馬世博等研究發現,當WC質量分數小于60%時,涂層缺陷較少,耐磨性、顯微硬度均隨WC含量上升而增強;但當WC質量分數超過60%,涂層出現氣孔和未浸潤缺陷,結合力下降。
何力分析指出WC-10Ni/NiCrBSi涂層中WC的適宜加入量為30%~45%,此時涂層與基體達到冶金結合,當WC含量過少時涂層表面成型較差,當過多時涂層與基體潤濕反應較差,無法形成有效冶金結合。
蘇科勇等研究發現能與正火態45鋼基體形成有效冶金結合的WC質量分數為10%~40%,隨著WC含量提高,WC顆粒周圍孔洞增多,涂層耐蝕性降低,最佳WC質量分數為30%。
姚永強等分析了真空和基體預熱溫度對于WC-Ni基涂層性能的影響,結果表明基體預熱和真空環境中涂層顯微硬度低于大氣環境中氮氣吹掃和不預熱的涂層,但是前者的穩定摩擦因素僅為0.5,且耐磨性更高。
YANG等研究發現基于真空熔覆技術制備的Ni/WC復合涂層由復合層、過渡層、熔合層和擴散影響層組成,復合層的顯微硬度為基體的6倍、整個復合材料熔覆層的形成主要取決于燒結頸的形成和長大、WC顆粒的浸潤以及其隨溫度和保溫時間的增加而完全融合。
TAO等研究表明,原位合成的WC增強相在復合層中的分布比外部添加的WC相更加均勻,并且后者易發生斷裂和WC顆粒脫落。
02 熔覆層的耐磨耐蝕性
黃新波等研究發現當添加15% WC時涂層的耐蝕性最佳,在10%鹽酸溶液中,涂層耐蝕性為45鋼基體的10倍,腐蝕出現在基體和涂層界面處。
周新星研究發現熔覆層硬度隨WC含量提高而提高,少量WC可以增強涂層的耐蝕性,但WC量過大會導致位錯和點陣畸變,降低涂層耐蝕性。
張喜冬研究表明當熔覆溫度為1225 ℃,WC質量分數為30%時,熔覆層的耐磨性和耐蝕性分別為基體45鋼的6倍和10倍。
ZHANG等在制備真空熔覆WC/NiCrBSi層的過程中發現,原位合成WC增強相和外部添加WC增強相涂層的耐蝕性都高于316L不銹鋼基材,但是前者WC顆粒與基體緊密結合,其錨定作用可防止微裂紋的形核和擴展,故前者的耐蝕性、抗空化能力更強。
HAN等分析了熔覆溫度和WC含量對于NiFeCrBSi/WC熔覆層硬度和耐磨性的影響,表明熔覆溫度越高,WC溶解越嚴重,當熔覆溫度為1225 ℃時,涂層的耐磨性隨WC含量的增加先增大后減小,當熔覆層WC質量分數為30%時,其耐磨性較好。
結束語
超聲速火焰具有較低的溫度和高速的焰流優點,所制備的WC涂層具有硬度高、孔隙率低、氧化物、脫碳少和耐磨性好等特點,因此可用于快速制備大面積且厚度可控的梯度耐磨涂層。但是由于設備運行成本高且粉末價格較高,因此WC涂層的制備成本較高,且涂層容易存在夾雜和副產物。
等離子噴涂由于噴涂溫度較高,涂層具備結合強度高、工作環境適應性強優點,且在制備過程中輔助惰性氣體保護,因此粉末不易被氧化,但是涂層制備成本比較高,設備比較復雜。基于等離子噴涂技術制備的金屬涂層與基體的結合屬于機械結合范疇,涂層中的硬質顆粒很容易脫落。
激光熔覆技術具備速度快、熱影響區域小、工件形變小、熔覆層稀釋率小等特點,因此環保、高效、靈活,自動化程度高,但是由于其能量集中、能量大,因此涂層中會存在較大的殘余應力,且容易產生裂紋和氣孔缺陷。
等離子熔覆技術的熔化速度快,涂層和基體結合力強,硬度均勻,孔隙率低,不容易產生質量缺陷,且涂層中的氧化物與雜質相對較少,因此涂層更厚、耐磨性和耐蝕性也更高,但存在涂層質量控制比較困難,涂層精度難以精準控制、實際性能難以滿足預期目標等缺點。
如何進一步優化工藝參數,提高涂層的致密度、強化涂層與基體的結合力,是不同WC涂層制備技術后續發展的重點。當前涂層耐磨性和耐腐蝕性的研究主要針對單一因素,比如干摩擦或者濕摩擦,或者單一腐蝕環境。但在涂層實際服役過程中,可能是腐蝕、磨損和疲勞等多因素協同作用,因此有必要對復雜服役環境中涂層的性能開展深入研究。
免責聲明:本網站所轉載的文字、圖片與視頻資料版權歸原創作者所有,如果涉及侵權,請第一時間聯系本網刪除。
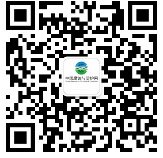
官方微信
《腐蝕與防護網電子期刊》征訂啟事
- 投稿聯系:編輯部
- 電話:010-62316606
- 郵箱:fsfhzy666@163.com
- 腐蝕與防護網官方QQ群:140808414