1 前言
因涂料的施工工藝簡單,能針對不同尺寸、形狀、部位的鋼結構、設備進行施涂,便于維修和重涂,工業大氣環境廠房鋼結構及設備表面一般采用涂料涂覆的方法進行防腐,防腐涂層保護效果與涂料體系和防腐施工(表面處理和施工工藝)有很大的關系;如果防腐涂層設計不合理,防腐施工和管理不科學,可能引起涂層早期失效,失去保護作用,本文介紹了幾個涂層體系早期失效案例,對化工大氣環境鋼結構防腐提出長效防范措施。
2 工業大氣環境條件及金屬鋼結構材料
腐蝕行為影響金屬大氣腐蝕行為的因素很多,其中大氣相對濕度、大氣溫度、大氣中污染物如 SO 2 、SO 3 、Cl - 、H + 、NH 4 、NOx 等以及降雨、大氣塵降、金屬表面狀態等等都影響著金屬的腐蝕發生。大氣環境的相對濕度自然是影響金屬大氣腐蝕重要原因之一,大氣相對濕度(RH)70% 時,金屬才會發生腐蝕。然而,薄液膜的形成還受其他因素如溫度、金屬表面狀態(清潔度、粗糙度、有無腐蝕產物覆蓋等等)、大氣中粉塵、大氣污染物、大氣輻射等等因素的影響,因此可能降低其臨界濕度,在低濕度下金屬材料會發生腐蝕。
工業大氣環境鋼結構的腐蝕,主要是由于大氣中含有的工業污染物,如硫化氫、二氧化硫、三氧化硫、氨等腐蝕介質;大氣中的污染物,在高溫潮濕條件下,吸附在鋼鐵表面,生成強的腐蝕介質,通過涂層的缺陷處滲透到鋼鐵表面,造成基材鋼鐵的腐蝕,同時引起涂層破壞,進一步加速腐蝕,將對廠房鋼結構產生嚴重腐蝕。
鋼結構的腐蝕:主要是電化學腐蝕,即金屬表面與離子導電的介質 ( 水、氧、無機酸、有機酸等 ) 因發生電化學作用而產生的破壞。腐蝕介質中存在著可以使金屬氧化的物質,它和金屬構成不穩定體系,形成腐蝕電池,加快金屬的腐蝕速度;其反應如下 : 2Fe+2H 2 O+O 2 → 2Fe(OH) 2 在氧的作用下,反應進一步進行:
4Fe(OH) 2 +2H 2 O+O 2 → 4Fe(OH) 3 ,Fe(OH) 3 脫水而形成鐵銹,2Fe(OH)3 →Fe 2 O 3 +3H 2 O。這種腐蝕由表面開始,逐漸向深層發展,形成大面積的腐蝕區域,腐蝕銹層的生成,吸附更多的水、氧、氯離子、酸霧等腐蝕介質,在工業大氣環境加速鋼鐵的腐蝕。
硫化氫的腐蝕:硫化氫氣體在空氣中吸潮,與水反應,生成液態硫化氫,屬于酸型腐蝕介質,沉積在金屬表面,加速金屬碳鋼等的腐蝕,腐蝕不只是均勻腐蝕,而且產生的氫氣能向鋼中滲入,引起鋼的氫脆和氫鼓泡,同時也可能發生硫化物應力腐蝕開裂。
二氧化硫的腐蝕:二氧化硫在空氣中可能氧化生成三氧化硫,他們吸潮后,生成亞硫酸和硫酸,均屬于強腐蝕介質,加速金屬鋼結構的腐蝕,同時二氧化硫具有循環加速作用,SO 2 、O 2 、Fe 形成 FeSO 4 ,然后 FeSO 4 被水解,形成 FeOOH和硫酸,酸又加速鐵的腐蝕,生成新的FeSO 4 ,如此循環反復,1 個分子的 SO2 可腐蝕多個 Fe 原子,腐蝕過程不斷進行。
氯離子的腐蝕:氯離子吸附的鋼鐵表明,具有較強的吸潮性,從而降低碳鋼腐蝕的臨界濕度,并溶于水膜中生成強腐蝕介質,增加腐蝕電池中電解質的導電性,降低臨界濕度,加速碳鋼的腐蝕。
3 工業大氣環境涂層早期失效案例
3.1 管廊鋼結構涂層失效某化工企業管廊鋼結構采用高氯化聚乙烯防腐涂層體系,2 道底漆和 2 道面漆配套,涂層厚度要求大于120μm,使用壽命 5-6 年,但在實際使用中,經 2 年使用,涂層多處鼓泡、脫落,失去保護作用,引起鋼結構腐蝕;其腐蝕形貌見圖 1。
涂層失效原因分析:
高氯化聚乙烯是高含氯量氯化聚乙烯,又稱 HCPE 樹脂,用于代替氯化橡膠的防腐涂料(由于環保的要求),其分子結構中不含雙鍵,氯原子又是無規則分布,雖具有良好的耐候性、耐臭氧性、耐熱老化性、耐燃性、耐化學藥品性和耐油性,但在工業大氣環境中,其防腐性能與環氧類、聚氨酯類涂料相比有一定的差距,單獨使用耐蝕性較差,需跟其它防腐涂料配套使用。
經 2 年實際應用,涂層已開裂、脫落,基材銹蝕,說明選用的高氯化聚乙烯防腐涂層體系在化工大氣環境中耐蝕性較差,不能滿足化工大氣環境長效防腐要求,現場檢測,涂膜厚度不均,有的涂層厚度只有 70-80μm,涂層厚度未達到設計要求,要加強施工質量管理,保障涂層厚度和涂裝質量。
3.2 儲罐涂層失效某石化新建儲罐外壁防腐,采用的是環氧富鋅底漆2道,氯化橡膠防腐涂料面漆 2 道的配套涂層體系,涂膜厚度大于140um,設計使用壽命 5-6 年,但實際情況,使用 1 年多,儲罐還未正式投入運行,發現儲罐涂層大面積鼓泡、開裂、脫落,碳鋼腐蝕,防腐涂層失去保護作用,其腐蝕形貌見圖2、3。
涂層失效原因分析:
防腐涂料進行分析:根據 HGT 3668-2000 《富鋅底漆》
要求,環氧富鋅底漆干膜中鋅粉含量大于 70%,但本項目使用的環氧富鋅底漆經檢測鋅粉含量為 43%,涂層不具有陰極保護效果,其耐蝕性較差;另外氯化橡膠防腐涂料雖具有一定的防腐和耐候性,但在化工大氣環境防腐性有一定的缺陷。
施工環境和工藝分析:根據施工日記記錄,涂料施工時環境溫度低,溫度為 2-3℃,涂層可能未完全固化,而對于環氧類防腐涂料要求施工溫度大于 10℃,涂層才能充分固化,達到其的防護性能。本項目采用的防腐涂層體系,涂層雖具有一定的保護作用,但經 1 年多使用,氯化橡膠面涂層的劣化,微觀缺陷放大,使水、氧和腐蝕介質容易滲入到底涂層及基材,而底涂層鋅含量不夠,不能起到有效的陰極保護作用,加之底涂層可能固化不完全,不具有較好的屏蔽作用,水和其他腐蝕介質很容易滲入到碳鋼基材表面,引起基材碳鋼的腐蝕,隨著碳鋼腐蝕加劇,導致涂層失去附著力,鼓泡,開裂、剝落,加速涂層的失效。
3.3 鋼結構涂層失效某化工企業儲罐和鋼結構,位于廣西海邊,防腐方案采用的是環氧富鋅底漆2道,聚氨酯面漆2道的防腐涂層體系,涂膜厚度 140um,設計使用壽命 5-6 年,但實際使用 1 年后涂層失效,對其進行檢測,發現儲罐和鋼結構表面涂層已出現大面積鼓泡、開裂、脫落,鋼結構腐蝕,涂層失去保護作用,其腐蝕形貌見圖 4。
涂層失效原因分析:
分析原因發現該企業靠近海邊,儲罐和鋼結構離海邊只有 100-200m 的距離,所處環境為海洋工業大氣環境,既有工業大氣環境污染介質的腐蝕,又有濕熱海洋離子環境的腐蝕;其防范措施必須采用重防腐涂層體系,而實際采用的防腐涂層體系,只有底漆和面漆,沒有中間漆,只能滿足一般的大氣環境防腐要求,而海洋工業大氣環境對鋼結構腐蝕嚴重,腐蝕等級一般達到 C4 和 C5 級,常規的涂層體系滿足不了該環境下的防腐要求,一般的涂層體系在鹽霧、濕熱和化工污染介質等的影響下,腐蝕介質很容易滲透的基材表面,引起基材腐蝕,造成涂層鼓泡、脫落,失去保護作用,其防腐必須采用重防腐涂層體系。
4 工業大氣環境長效防腐對策
根據長期的試驗結果和使用經驗,在工業大氣強腐蝕性的環境,鋼結構的防腐宜采用重防腐涂層體系。防腐涂層必須具備以下性能:(1)底涂層具有牢固的附著力和耐腐蝕性能,(2)優異的抗水和氧及腐蝕介質的滲透性能和對腐蝕介質的穩定性(3)面涂層具有優異的耐候性,抗紫外光老化。防腐涂層體系一般由底漆、中間漆和面漆組成,對他們具有不同的性能要求,常用的防腐涂料有:
1)底涂層常用的底涂層有環氧底漆、環氧富鋅、無機富鋅、氯化橡膠底漆、醇酸底漆、噴鋁,我們對它們與鋼基體表面之間的附著力進行測試 (1) ,結果如下:
由結果可知,噴鋁結合強度最大,環氧類的底涂層具有較高的附著力。我所在青島海洋環境對底涂層進行的腐蝕試驗研究,其腐蝕形貌見圖5,結果表明:噴鋁涂層耐蝕性最好,經8年曝露試驗,噴鋁表面未見明顯變化,碳鋼無任何腐蝕,具有較好的保護性能;環氧富鋅和無機富鋅涂層對鋼鐵的具有較好保護性能,其經 12 月實海曝露試驗,發現碳鋼無任何腐蝕,即使將漆膜劃透直至表面,裸露出鋼基的劃痕處,基體金屬仍然受到良好的陰極保護,噴鋁和兩種富鋅類底漆明顯具有優于其他類底漆的防銹效果。環氧鐵紅底涂層和高氯化底涂層具有一定的保護性能,海洋環境下可經受 3 月試驗而不會出現基體銹蝕,但 180 天以后,涂層局部已破壞,碳鋼開始腐蝕。醇酸底涂層耐蝕性最差,經 30 天曝露試驗,涂層已失去保護性能,碳鋼已發生明顯腐蝕。對于工業大氣環境推薦采用環氧富鋅或無機富鋅底涂層,其中環氧富鋅底漆,即具有優異的附著力,又具有陰極保護作用。
2)中間涂層常用性能優良的中間涂層材料有環氧云鐵和環氧玻璃鱗片防腐涂料。環氧云鐵防腐涂料:由于云母氧化鐵及環氧樹脂的優越性能,環氧云鐵中間漆漆膜堅韌,具有良好的附著力、柔韌性、耐磨性、封閉性以及對腐蝕介質的抗滲透性;環氧玻璃鱗片防腐涂料:由于其幾何形狀為片狀結構的玻璃鱗片顏填料在涂膜中的平行排列,可以將基體分割成許多小區域,將涂層中微小氣泡、裂紋及分子空穴相互分割切斷,當腐蝕性介質向復合涂層滲透時,受到一層層玻璃鱗片的物理阻礙,從而使環氧玻璃鱗片涂料大大地延長了介質的滲透時間,有效地抑制了介質的擴散,而且由于鱗片不連續地分散于涂膜中,能降低樹脂固化時產生的殘余應力,大大減少了涂層的收縮,使防蝕層的微裂紋、微孔大大減少,進而提高了保護層體系的防腐蝕效。
3)面涂層面涂層有環氧涂層、高氯化涂層、聚氨酯涂層、脂肪族丙烯酸聚氨酯涂層和氟碳涂層,他們均具有一定的耐腐蝕性能。但環氧涂層耐候性較差,一般只能用在室內大氣防腐。
氟碳涂層經 3000h 加速老化試驗后,失光率不到 10%;經3000 小時鹽霧試驗,涂層無明顯變化。而丙烯酸聚氨酯涂層經 1700h 加速老化試驗后,失光率可高數倍。我們在工業大氣環境暴露 2 年的失光率見表 2,結果說明,氟碳涂層失光率最小,耐候性最好 ; 丙烯酸聚氨酯次之 ; 氯化橡膠和高氯化聚乙烯失光率較大,耐候性差,表面已產生粉化。因此,從耐蝕性和耐候性綜合評定面涂層的性能,耐候性的優良順序是:氟碳涂層 > 丙烯酸聚氨酯 > 聚氨酯 > 氯化橡膠、高氯化聚乙烯涂層。
4)化工大氣環境長效防腐對策通過實際環境試驗結果可知,底涂層中噴涂層、富鋅涂層耐蝕性能較好,面涂層中氟碳涂層耐候性耐蝕性最佳,其次為脂肪族丙烯酸聚氨酯;對工業大氣環境鋼結構提出如下長效防范措施,可以達到防護期為 6-10 年的目標。
表面處理:采用噴沙除銹,要求基體表面清潔度達到GB8923 中所規定的 Sa2.5 級。由于施工限制無法實行噴砂去銹的部位,可采用手工電動工具除銹,使其表面清潔度達到St3級。
底漆:采用環氧富鋅底漆或無機富鋅,干膜厚度 70-80μm;特別嚴酷環境可以采用金屬噴涂層,包括噴鋁、噴鋅或噴鋅鋁涂層;中間漆:一般采用環氧云鐵中間漆,干膜厚度 150μm,嚴酷環境可以采用環氧玻璃鱗片涂料,干膜厚度 150-200μm;面漆:采用丙烯酸聚氨酯或氟碳涂料面,干膜厚度 70-80μm;涂層體系干膜總厚度要求大于300μm。
5 結束語
化工大氣環境的腐蝕是嚴酷的,腐蝕即造成資源和能源的浪費,還可能造成環境污染和生產安全,必須采取有效的防范措施;其鋼結構的防腐宜采用重防腐涂層體系,包括底漆、中間漆和面漆的配套體系。防腐涂料是個半成品,其優異的防腐性能必須通過科學的防腐設計和科學的施工管理,才能制備出性能優異的防腐涂層,滿足其防腐性能要求。
免責聲明:本網站所轉載的文字、圖片與視頻資料版權歸原創作者所有,如果涉及侵權,請第一時間聯系本網刪除。
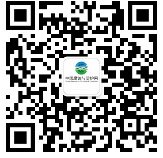
官方微信
《腐蝕與防護網電子期刊》征訂啟事
- 投稿聯系:編輯部
- 電話:010-62316606-806
- 郵箱:fsfhzy666@163.com
- 腐蝕與防護網官方QQ群:140808414