摘要
采用等離子噴涂法制備了鉭金屬涂層, 用電子顯微鏡分析了不同工藝條件下鉭涂層的化學成分、表面形貌,測試了涂層與基材的結合強度。 結果表明,采用優化的等離子噴涂工藝參數,可以制取組織致密、厚度均勻的鉭涂層;鉭粉的顆粒尺寸對材料的熔化狀態影響較大;在試驗的噴距范圍內,噴距對粉末的熔化狀態和涂層結合強度均無明顯影響。
前言
鉭具有優良的化學穩定性和抗腐蝕性能, 且加工性能良好,已廣泛應用于電子、冶金、能源、化學化工、生物等領域。 在現代醫學中, 鉭與人體組織具有良好的生物相容性;在化學工業領域,用鉭替代不銹鋼, 耐蝕壽命可提高幾十倍; 特別是在電子工業, 鉭是性能優異的現代電容材料之一, 對X射線、電磁波有著優良的屏蔽能力, 可以取代貴重金屬鉑, 大大降低使用成本。
國內外已開展采用粉末冶金、真空離子濺射等工藝生產鉭制品的研究,但是采用熱噴涂方法制備鉭涂層的研究目前還鮮見相關報道。在高溫環境中,鉭易發生氧化作用,利用等離子體焰流還原氣氛可調的特點可以降低鉭的氧化程度,制備結合強度高、組織致密的金屬涂層。本文研究了等離子噴涂工藝參數對鉭涂層熔化狀態和結合強度的影響,為獲得優質的鉭涂層提供可靠的試驗依據。
試驗方法
基材選用 LY12 硬鋁,涂層材料選擇粒度為 140 目、300 目的冶金一級鉭粉[ w( Ta)=99.50%,w(O)≤0.40 %]。基材利用噴砂方法進行預處理,以獲得新鮮干凈的工作表面。
采用SULZER &METCO 9M 等離子噴涂裝置制備鉭涂層, 主氣采用氬氣,輔氣采用氫氣,噴涂試驗參數見表1。
采用РЭММА-102 型掃描電鏡定性觀察涂層的表面形貌及微觀組織結構。采用KYKY-1010B 掃描電鏡附帶能譜儀進行涂層微區成分定量分析。在1196 INSTRON力學試驗機上測定涂層的結合強度。
結果與討論
(1)等離子功率對粉末熔化的影響
采用3種不同功率制備的 300 目鉭粉涂層表面形貌見圖 1,鉭顆粒熔化后撞擊到金屬表面,充分變形后凝固形成致密涂層。
對比分析可知, 等離子弧功率與粉末的熔化狀態并不成正比。 等離子弧功率為 20 kW 時, 就可以使鉭粉熔化, 但是鉭顆粒的溫度低、速度慢、冷卻快, 撞擊基材表面后不能充分延展, 造成涂層表面粗糙度較大。 等離子弧功率為 30 kW 時, 鉭顆粒溫度高 、速度較快, 撞擊基材表面后充分延展, 涂層表面的均勻性最佳。 當等離子弧功率達到 36 kW 時, 隨著等離子的焰流速度加快, 涂層氧化減少, 鉭粉在等離子焰流停留時間縮短, 受熱不充分, 熔化反而變差。 在相同的功率條件下, 在本試驗的噴涂距離內, 改變噴距對粉末熔化狀態的影響不大,100,150 mm 噴距下鉭粉的熔化效果幾乎相同。
(2)粉末粒度對涂層組織的影響
采用 2 號工藝制備的 140 目鉭粉涂層形貌見圖 2 。 由圖 1b和圖 2 比較分析可知, 鉭粉的粒度對噴涂效果有極大的影響。 粒度較大時, 由于涂層快速凝固的特點, 粉末顆粒來不及鋪展即凝固, 因此表面的均勻性較差。 粒度較小時, 顆粒的熔化狀態好, 但是粉末的損耗大, 沉積效率較低。
采用 2 號工藝制備的鉭涂層剖面組織見圖 3, 其中右邊黑色部分為 LY12 硬鋁基材, 左邊灰色部分為鉭涂層。 鉭涂層組織致密, 基本上消除了各層之間的宏觀層間界面, 但仍然出現了少量孔隙。 改善粉末的熔化效果, 就可以有效地控制孔隙的數量。 由圖 4 鉭涂層表面高倍形貌可以清晰地觀察到, 涂層外表凝固冷卻速度較快, 熱應力較大, 產生了微裂紋。 而涂層內部由于緩冷作用, 減少了熱應力的影響, 未發現明顯的微裂紋。 由于大氣等離子噴涂工藝的快速凝固特點, 難以完全消除孔隙與微裂紋。
(3)噴涂距離和氣體流量對涂層成分的影響
采用能譜技術分析了 300 目鉭涂層的化學成分, 結果見表 2。在電弧電流保持不變的情況下, 改變電弧電壓, 隨著氫氣流量的增加、等離子焰流還原性氣氛的加強, 減緩了涂層的氧化。 由于等離子焰流還原效應主要集中在約 100 mm 長的范圍內, 若噴距超過 100 mm 時 , 涂層的氧化作用必然加劇。
(4)涂層結合強度測試
參照 GB 8642 —88《熱噴涂層結合強度的測定》,拉伸試樣的尺寸選定為40 mm×50mm;采用表1所列2號工藝制作了厚度0.5mm的鉭涂層,將噴涂試樣與對接件用環氧膠粘結起來,5 對試樣經過 48 h 固化后, 進行拉伸測試,夾頭速率0.5mm/s,記錄最大斷裂載荷P(kN),按照公式σ=P/S計算涂層與基材之間的結合強度σ。式中,S為粘結涂層面積(mm2)。結果1~5號試樣抗拉結合強度值分別為39.4,45.6,38.6,42.5MPa和46.7MPa,平均值為43.0MPa,可見由于孔隙、微裂紋等缺陷的存在,降低了鉭涂層的強度。
(5)涂層物相及成分的深度剖析
鉭涂層的 AES( 俄歇能譜儀)成分深度剖析結果見圖 5, 濺射速度為 100 nm/ s, 鉭涂層表面 X 射線譜圖見圖 6。 由圖 5, 6 可見,從涂層表面至內部, 氧所占原子百分比的逐漸減小, 由于等離子噴涂的快速凝固, 使氧的擴散受到了限制, 氧主要集中于涂層表面, 以 Ta2O、Ta2O5形式存在,Ta2O為主。
結論
(1)采用適宜的等離子噴涂工藝參數, 可以在鋁基體上制備組織致密、結合良好的鉭涂層。適當提高電弧電壓、控制噴涂距離,鉭涂層的氧化是可控的。
(2)鉭粉的粒度對涂層的熔化狀態影響較大, 針對具體的技術要求, 可以選取不同粒度的鉭粉。 在試驗噴距范圍內, 噴距對鉭的熔化狀態無明顯影響。
(3)鉭涂層中的氧主要集中于表面, 以 Ta2O、Ta2O5 形式存在,Ta2O為主。
更多關于材料方面、材料腐蝕控制、材料科普等方面的國內外最新動態,我們網站會不斷更新。希望大家一直關注中國腐蝕與防護網http://www.ecorr.org
責任編輯:王元
投稿聯系:編輯部
電話:010-62313558-806
中國腐蝕與防護網官方 QQ群:140808414
免責聲明:本網站所轉載的文字、圖片與視頻資料版權歸原創作者所有,如果涉及侵權,請第一時間聯系本網刪除。
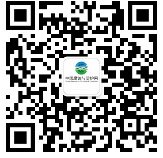
官方微信
《中國腐蝕與防護網電子期刊》征訂啟事
- 投稿聯系:編輯部
- 電話:010-62316606-806
- 郵箱:fsfhzy666@163.com
- 中國腐蝕與防護網官方QQ群:140808414