防滑涂層通過增強材料接觸表面的摩擦阻力達到防滑目的,接觸摩擦阻力的大小與兩個物體接觸表面狀況(如粗糙度、壓力)、配副材料的選擇等密切相關(guān)。防滑原理有粗糙表面凹凸處的物理咬合、銼削作用、粘滯作用等。配副材料的選擇對防滑性能十分重要,通常硬-硬施加載荷后咬合力比較大,軟-軟結(jié)合的后接觸面積大、范德華力大,硬-軟施加載荷后接觸面產(chǎn)生犁削效應(yīng)。涂層防滑性能的好壞可用涂層的摩擦系數(shù)來定量表征,按照摩擦副相對運動的速度一般分為靜態(tài)防滑系數(shù)和動態(tài)防滑系數(shù),按照摩擦副的接觸類型一般分為干態(tài)、水濕態(tài)和油潤滑狀態(tài)下的防滑系數(shù) 。我國國家標準、美國軍標等相關(guān)規(guī)定中提出平面牽引法和平面滑動法是常用的測量靜摩擦系數(shù)和動摩擦系數(shù)的方法。表 1 給出了摩擦系數(shù)安全等級的劃分。但在一些特殊場合,如甲板漆的摩擦系數(shù)應(yīng)在 0.7 以上,以確保人員和設(shè)備的安全,且要有較高的水濕態(tài)和油潤態(tài)摩擦系數(shù),并滿足抗沖蝕性能、耐腐蝕的要求 。
在工程實踐中,利用摩擦傳遞動力或防止滑動的應(yīng)用非常廣泛,如工業(yè)生產(chǎn)中各種依靠摩擦傳動的起重運輸機械、爬壁機器人、車用離合器和剎車片等 。船舶及海上鉆井平臺也需要提高工作接觸面上的摩擦系數(shù),以確保操作人員和機械裝備的安全。高分子聚合物涂層以及金屬基涂層是常用的防滑涂層。
采用熱噴涂技術(shù)制備的金屬基防滑涂層作為一種功能涂層,可以增強材料表面的摩擦系數(shù)和硬度,起到防滑耐磨等作用。熱噴涂技術(shù)是利用熱源將粉末、絲材或棒材加熱至熔融或半熔融狀態(tài),在基體表面形成結(jié)構(gòu)與功能涂層的一類表面技術(shù),具有噴涂材料廣泛、基體形狀與尺寸不受限制、涂層厚度易控制、工藝操作簡單、效率高等特點,能夠?qū)崿F(xiàn)零部件的表面強化、修復(fù)及改性 。金屬基防滑涂層作為無機防滑涂層中的一類,相較于高分子聚合物防滑涂層,具有壽命長、摩擦系數(shù)穩(wěn)定、不使用毒性有機溶劑以及更好的抗磨損和抗高溫氧化性能。20 世紀六七十年代,采用熱噴涂鋁酸鎳防滑涂層的 CVA-59 號航母偏流板經(jīng)起飛飛機 4200 架次,其中 1119 架次經(jīng)受了燃氣噴射氣流的作用,只有少量點蝕并可進一步使用。20 世紀 90 年代初,美國 NKF 工程公司曾用熱噴涂方法把含 SiC 的鋁線材料涂覆到艦載飛機的鋼質(zhì)甲板表面,與此同時,Duralcan 90/10 鋁基防滑涂層也相繼進入了試驗階段,并在美國海軍 5 艘艦船上進行了實踐,取得滿意的效果 。我國全軍裝備維修表面工程研究中心采用鋁基氧化鋁金屬陶瓷復(fù)合粉芯絲材,成功制備了一種艦船鋼板用防滑涂層,在海軍某潛艇上進行的應(yīng)用表明,防滑復(fù)合涂層體系的性能優(yōu)良 。
近年來,由于廣泛的需求,金屬基防滑涂層得到了迅猛發(fā)展,現(xiàn)代船舶及海洋裝備對防滑性能提出了更高要求,很多研究者正在從事金屬陶瓷復(fù)合涂層和非晶合金等防滑涂層的研究和應(yīng)用,以 NiCr-Cr 3 C 2為代表的金屬基涂層已被廣泛應(yīng)用于船舶及海洋平臺等場合 。在汽車工業(yè)中,防滑涂層有重要的應(yīng)用價值,如汽車離合器、剎車片等部位噴涂防滑耐磨涂層,不僅可以提高汽車的剎車性能,還能有效延長零部件的使用壽命。
1 熱噴涂技術(shù)
熱噴涂技術(shù)能夠改變零部件表面特性,使材料表面獲得不同于基體的性能,如更好的耐磨、耐蝕、抗氧化和潤滑等性能。熱噴涂技術(shù)可噴涂材料的范圍極廣(金屬、陶瓷、高分子聚合物),尤其在金屬基防滑涂層制備方面有著廣泛應(yīng)用。目前應(yīng)用較廣的是火焰噴涂、電弧噴涂、等離子噴涂、爆炸噴涂和超音速火焰噴涂等技術(shù),圖 1 是常用熱噴涂工藝的粒子溫度范圍和速度范圍 。
粉末火焰噴涂以燃燒火焰為熱源,操作簡單、投資少,但焰流溫度較低,粒子飛行速度較小,僅適用于熔點較低的金屬或合金。涂層常含有半熔化顆粒,孔隙率較高,氧化比較嚴重,致密度較低 。雙絲電弧噴涂以兩根金屬絲材在噴槍端部短路產(chǎn)生的電弧為熱源,使用壓縮氣體將熔化的金屬絲霧化,并迅速噴射到基體表面形成涂層。由于電弧噴涂具有很高的能量密度,從而使熔化粒子獲得較高的溫度和速度 。電弧噴涂技術(shù)符合室外作業(yè)要求,可進行大面積噴涂作業(yè),因此在工程實際中應(yīng)用較廣。等離子噴涂由于等離子弧溫度高(約 15 000 ℃),粒子速度達 300~400 m/s,適于噴涂高熔點材料。與前兩種方法相比,等離子噴涂的涂層孔隙率低,結(jié)合強度高,噴涂效率高,因此在航空、冶金、機械、車輛等領(lǐng)域得到廣泛應(yīng)用 。
爆炸噴涂于 20 世紀 50 年代問世,它通過爆炸燃燒產(chǎn)生的高速熱氣流將粉末粒子加熱到塑性或熔化狀態(tài),并使粉末粒子加速噴射到基體表面形成涂層,其涂層結(jié)合強度高、孔隙率低,但噴涂噪音大,對基體形狀要求高,設(shè)備成本和使用成本較高,其應(yīng)用也受到了限制。超音速火焰噴涂于 20 世紀 80 年代研發(fā)成功,該方法噴涂的粒子溫度低、飛行速度快,涂層孔隙率低、氧化程度低、結(jié)合強度高,可有效解決硬質(zhì)合金涂層沉積過程中的脫碳問題,逐漸成為一種應(yīng)用廣泛的熱噴涂技術(shù) 。
因此在涂層制備過程中,應(yīng)針對不同材料體系,采用不同熱噴涂技術(shù),通過控制試驗參數(shù),以獲得最佳的涂層結(jié)構(gòu)及其服役性能。
2 金屬基防滑涂層
金屬基防滑涂層包括合金、非晶和金屬基復(fù)合涂層。金屬基復(fù)合涂層中的陶瓷相通常采用燒結(jié)破碎法、包覆法和霧化法制備而成,通過噴涂,和金屬基材料形成復(fù)合涂層。涂層除了滿足防滑性能外,還需具備較好的耐磨性能,以確保涂層的使用壽命長,在一些特殊場合還需要具備良好的耐腐蝕性能,因此在研究中常側(cè)重于涂層的上述性能分析。國內(nèi)外學(xué)者對于金屬基防滑涂層的材料體系、噴涂工藝以及應(yīng)用條件等方面進行了大量研究。
2.1 Al 基防滑涂層
鋁基防滑涂層因其較好的耐腐蝕性能,多用于橋梁、船舶、海洋平臺等一些腐蝕性較強的環(huán)境中。對于高強度橋梁栓接面,電弧噴涂鋁絲材可有效增強接觸面的抗滑移系數(shù),具有良好的抗老化性能,即使是進行油漆封閉后的涂層,也能滿足連接面的抗滑移系數(shù)要求 。但純鋁絲材的耐磨性相對較差,導(dǎo)致使用壽命受到限制。粉芯絲材的出現(xiàn)有效增強了鋁基涂層的性能,同時解決了復(fù)合絲材冶煉和拉絲的難題,與純鋁絲材相比,粉芯絲材可添加陶瓷顆粒、碳化物等增強相,絲材外皮經(jīng)軋制、拉拔后,表面光滑、剛度好,具有良好的工藝穩(wěn)定性,涂層防滑綜合性能得到提高。劉謙等制備了電弧噴涂 Al-Al 2 O 3 復(fù)合粉芯絲材涂層,在對偶材料為鋼時,涂層的摩擦系數(shù)達到 0.75~0.80;對偶材料為橡膠時,封孔后涂層的摩擦系數(shù)達到 0.85 以上。靳生等制備了 Al-Al 2 O 3 復(fù)合粉芯絲材涂層,在以 45 # 鋼為對偶件的環(huán)塊干摩擦試驗中,測得涂層的摩擦系數(shù)可穩(wěn)定在 0.68 左右。
熱噴涂 Al 基防滑涂層的優(yōu)勢在于涂層中生成了Al 2 O 3 增強相,復(fù)合粉末中的 α-Al 2 O 3 相在沉積過程中快速冷卻轉(zhuǎn)化為 γ-Al 2 O 3 相,γ-Al 2 O 3 相能夠增強涂層的耐磨和防滑性能 [28-29] 。氧化鋁的硬度高、耐磨耐蝕性能好,因此常在純鋁粉末中添加氧化鋁顆粒。
Huang 等研究發(fā)現(xiàn) Al 2 O 3 添加量為 20wt%時,Al-Al 2 O 3 復(fù)合涂層的抗磨耐蝕性能最好,在鹽霧腐蝕過程中,由于彌散強化的 Al 2 O 3 骨架結(jié)構(gòu)切斷了氯離子進入涂層內(nèi)部的通道(如圖 2),從而減緩了腐蝕的進程,相比純鋁涂層能夠提高和穩(wěn)定摩擦系數(shù)。
相同防滑材料摩擦系數(shù)產(chǎn)生的差異,除噴涂工藝的因素外,還取決于對偶件材料以及施加的載荷大小。前文所述的涂層在不同條件下均顯示出較高的防滑系數(shù),證明了 Al 基作為防滑涂層的優(yōu)勢。事實上,鋁基涂層即使添加氧化鋁增強相,在高速條件下,其耐磨性仍稍遜于鐵基、鈷基涂層,但其防腐性能極為優(yōu)越,在海水腐蝕環(huán)境下可以生成一層致密的鈍化膜,這對鋼結(jié)構(gòu)起到緩蝕作用。此外,鋁基材料多做成粉芯絲材用于電弧噴涂,噴涂成本低,效率高,操作方便,可用于戶外施工,廣泛用于貯水容器、船體和閘門等。因此在提高 Al 基涂層的耐磨損性能方面還有很多工作要做。
2.2 Fe 基防滑涂層
Fe 基合金粉末以 Fe、Cr、B、Si、C、Mo 等元素為主,噴涂態(tài)涂層為典型的層狀結(jié)構(gòu)(圖 3 ),主要存在硬質(zhì)相((Fe, Cr)、Fe 2 B、Fe 3 B、Cr 2 B 等)、氧化物以及非晶相。非晶相的形成需要具有較大的過冷液相區(qū)、較低的玻璃化轉(zhuǎn)變溫度,因此相對于其他金屬基材料,F(xiàn)e 的非晶形成能力較高 ,在熱噴涂快速冷卻過程中更易形成非晶相。非晶涂層是 Fe 基防滑涂層重要的組成部分和重點研究方向。目前,非晶合金涂層作為新一代高性能防滑涂層,因其高強度、高耐磨耐蝕等物理化學(xué)性能,越來越受到國內(nèi)外研究人員的青睞。因此,采用先進的熱噴涂技術(shù)制備非晶防滑涂層是金屬基防滑涂層發(fā)展的重要方向之一 。
非晶合金沒有位錯和晶面,若使材料產(chǎn)生變形或斷裂,須施加更大的外力,有著不同于常規(guī)合金的特殊性能,因此非晶相的形成對于提高涂層耐磨耐蝕性能有著積極的作用。熱噴涂技術(shù)由于其快速冷卻的特點,被廣泛運用于制備非晶涂層。控制各元素的添加量以控制涂層非晶相的形成,如 SAM 系列非晶合金添加少量 Cr 元素(4at%)能夠有效提高合金的耐腐蝕性能,但過量添加反而會引起晶化 [35] 。超音速火焰噴涂過程中,燃油與氧氣的比例會影響涂層的結(jié)晶程度,當(dāng)燃油與氧氣的比例較大時(火焰溫度較高),粒子完全熔融并快速冷卻沉積到基體上形成非晶相;當(dāng)燃油與氧氣比例較小時(火焰溫度較低),涂層中會出現(xiàn)結(jié)晶相 [36] 。熱處理能夠使涂層中的非晶相再結(jié)晶形成硬質(zhì)相,獲得更加致密的涂層組織。研究發(fā)現(xiàn),涂層在 600 ℃左右經(jīng)過熱處理后會獲得最優(yōu)的性能,此時的涂層硬度可達到 1275 HV 0.3 。
通常基材(如不銹鋼)的顯微硬度只有約 200 HV,而 Fe 基涂層的硬度可以達到 1000 HV 以上。WU 等采用爆炸噴涂技術(shù)制備的 Fe 51.33 Cr 14.9 Mo 25.67 Y 3.4 C 3.44 B 1.26非晶涂層,硬度為 1095.6 HV,涂層孔隙率低于 2.1%,在室溫球盤摩擦實驗中獲得比 Q235 基體更加穩(wěn)定的摩擦系數(shù),載荷為 20 N 時的摩擦系數(shù)可達到 0.7,涂層的耐磨性是基體材料的 5 倍左右,涂層的主要失效機制是磨粒磨損和層狀剝落。上述磨損機制也是 Fe基涂層常見的磨損機制,涂層表面由于摩擦形成的摩擦膜不斷地產(chǎn)生、磨損、剝落,在一定程度上起到保護涂層的作用,即使在高溫摩擦條件下仍表現(xiàn)出較好的防滑耐磨性能 [39-40] 。除 Fe 基粉末外,有研究者采用電弧噴涂技術(shù)噴涂 Fe 基粉芯絲材制備防滑涂層,即使在 600 ℃的高溫環(huán)境下仍具有較高的防滑系數(shù)(約 0.6) [41-42] 。
選用合適的噴涂工藝、控制噴涂參數(shù)以及原始粉末對獲得性能優(yōu)異的涂層至關(guān)重要。當(dāng)噴涂過程中粒子的速度和溫度較低時,涂層易萌生大的孔洞和微裂紋,影響涂層壽命 [43] 。鐵基粉末顆粒越小,則涂層的孔隙率越低,裂紋越少,涂層的結(jié)合強度和硬度提高,涂層的耐磨性能增強 [44] 。研究人員發(fā)現(xiàn),噴涂工藝對鐵基涂層磨損率的影響較大,而對涂層摩擦系數(shù)的影響相對較小 [39, 45-46] 。由于噴涂工藝改變了涂層的組織結(jié)構(gòu),影響涂層的層間結(jié)合力,導(dǎo)致磨損率變化較大,而涂層的摩擦系數(shù)與接觸摩擦阻力的大小、兩個物體接觸表面狀況、配副材料的選擇等密切相關(guān),因而噴涂工藝對防滑系數(shù)的影響相對較弱。
鐵基涂層作為防滑涂層的優(yōu)點在于其特殊的非晶形成能力,涂層具有較高的硬度,尤其高溫抗磨損及抗腐蝕性能較為突出,研究的關(guān)鍵是如何控制其非晶相的形成,減小涂層的孔隙率。此外,F(xiàn)e 基非晶粉末造價高,如何降低制粉成本,提高噴涂中粉末沉積效率也是值得關(guān)注的地方。
2.3 NiCr 基防滑涂層
NiCr 合金具有良好的耐熱耐蝕性,常與一些硬質(zhì)相(如 TiB 2 、WC、Al 2 O 3 等)形成復(fù)合涂層,在防滑涂層的應(yīng)用中,NiCr-Cr 3 C 2 涂層的應(yīng)用最廣泛。Cr 3 C 2 在金屬碳化物中的抗氧化能力最強,涂層在保持高摩擦系數(shù)的同時,在高溫條件下依然能夠保持相當(dāng)高的硬度和耐蝕耐磨性能。NiCr-Cr 3 C 2 金屬陶瓷涂層具有硬度高、孔隙率低、斷裂韌性高、抗高溫氧化及循環(huán)氧化性好等優(yōu)點,在低溫和高溫條件下均保持高摩擦系數(shù),表現(xiàn)出良好的摩擦學(xué)性能,被廣泛用作海洋環(huán)境防滑耐磨防腐涂層 。
涂層在滿足防滑系數(shù)要求的前提下應(yīng)具備較長的使用壽命,在 NiCr 基防滑涂層中加入稀土氧化物(La 2 O 3 或 CeO 2 )能大幅提高涂層的耐磨損性能。Zhang 等采用超音速等離子噴涂制備了稀土氧化物 La 2 O 3 和 CeO 2 含量不同的 NiCr-Cr 3 C 2 涂層,摩擦系數(shù)在 0.6~0.7 之間,相比原涂層的磨損率(2.0×10 9 μm 3 ),其磨損率幾乎為零。稀土元素容易與氧反應(yīng)形成稀土氧化物,可以增加晶核數(shù)量,Ce 2 O 3 和CeCrO 3 相會阻礙晶粒生長,達到細化晶粒、致密涂層組織的作用,提高涂層的耐磨及抗氧化性能,但對涂層防滑系數(shù)的影響較小 。Zhou 等在以氧化鋁為對磨球的高溫球磨試驗中發(fā)現(xiàn),添加了 WC 顆粒的 NiCr 基涂層具有很高的摩擦系數(shù),并且在 450 ℃時磨損率僅為原來的五分之一。Matikainen 等 [52] 的研究也證實了 WC 顆粒的加入會增強涂層的摩擦系數(shù),NiCoCr-Cr 3 C 2 -WC 涂層的室溫干摩擦系數(shù)為 0.7。Liu等發(fā)現(xiàn) Al 2 O 3 能夠提高 NiCr 合金的力學(xué)和摩擦學(xué)性能,從室溫到 600 ℃溫度范圍內(nèi),NiCr-Al 2 O 3 涂層都顯示出較高的摩擦系數(shù)(0.5~0.8),但 Al 2 O 3 含量過高會引起涂層脆性斷裂,降低耐磨性。
為了有效增強防滑涂層在海水中的耐腐蝕性能,Bai 等制 備 了 一 種 新 型 雙 層 防 滑 涂 層 , 在NiCr-Cr 3 C 2 涂層與基體間采用低壓冷噴涂技術(shù)噴涂Ni-Zn-Al 2 O 3 中間層,克服了單層涂層中氣孔、微裂紋和層狀結(jié)構(gòu)作為渠道引起界面腐蝕,造成涂層起泡的缺點。雙層涂層中,腐蝕產(chǎn)物在中間層的形成可以起到進一步阻擋腐蝕介質(zhì)的作用,從而抑制腐蝕。在摩擦試驗中,涂層顯示出優(yōu)異的性能,無論在干磨還是鹽霧條件下,涂層的摩擦系數(shù)均在 0.9 以上,表現(xiàn)出極好的防滑性能。
適當(dāng)?shù)臒崽幚砜梢愿纳仆繉拥哪Σ翆W(xué)性能 。
Gariboldi 等在研究熱處理對 NiCr-Cr 3 C 2 涂層(采用 HVOF 技術(shù)制備)摩擦學(xué)性能的影響中發(fā)現(xiàn),涂層在 400 ℃保溫 100 h 的條件下,其綜合性能最好,摩擦系數(shù)約為 0.55,略低于噴涂態(tài)涂層,但熱處理后的涂層磨損率比噴涂態(tài)的涂層減少 80%。熱處理會提高涂層層間凝聚力,減小涂層孔隙率。另一方面,適當(dāng)?shù)臒崽幚頃淖兺繉拥南嘟Y(jié)構(gòu),影響涂層的磨損機制。
因此添加新的組元及后處理是 NiCr 基涂層未來研究的重點,并且在粘結(jié)相與硬質(zhì)相的添加比例方面應(yīng)做進一步研究。
2.4 Co 基防滑涂層
Co 本身硬度較低,是最理想的粘結(jié)劑,作為防滑涂層需要加入 W、Cr、C、氮化物、碳化物等物質(zhì),以增強涂層的耐磨性能,適當(dāng)?shù)丶尤?Cr 能減輕噴涂粉末在噴涂熔化過程中的氧化程度,氮化物及碳化物添加可增強涂層硬度。Co 基涂層作為防滑涂層,應(yīng)用最廣泛的是 WC-Co 防滑涂層 ,圖 4 是典型的超音速火焰噴涂 WC-12Co 涂層結(jié)構(gòu)。WC 在 1250 ℃會發(fā)生脫碳,形成脆性的 Co-W-C 三元相、W 2 C 相和較軟的 W 相,導(dǎo)致涂層耐磨性下降 。因此,Co 基涂層在低溫摩擦環(huán)境中表現(xiàn)出極好的耐磨性能。超音速火焰噴涂技術(shù)因其噴涂溫度較低,粒子受熱時間短,能有效減輕 WC 的分解脫碳。
粉末的粒徑對涂層摩擦學(xué)性能也有至關(guān)重要的影響,碳化物顆粒越小,脫碳現(xiàn)象越嚴重 ,制備致密的涂層并同時減少脫碳現(xiàn)象對于研究者來說是一項挑戰(zhàn)。Yuan 等 [65] 在 HVOF 制備的 WC-Co 涂層中加入亞微米 WC-Co 顆粒,添加 WC 顆粒的質(zhì)量分數(shù)為 3%和 5%時,涂層的顯微硬度和滑動耐磨性得到了提高。Ma 等也得到了相同結(jié)論。這是由于復(fù)合涂層增強了扁平粒子間的結(jié)合,減少了微裂紋的產(chǎn)生,且能夠有效改變應(yīng)力狀態(tài),抑制裂紋擴展,使涂層的致密度高、結(jié)合強度高、斷裂韌性好。
涂層的服役條件(如溫度、氣氛、載荷)是影響涂層壽命的重要因素之一。Geng 等 [67] 研究發(fā)現(xiàn),在600 ℃以下,WC-Co 涂層都可以作為耐磨涂層使用,當(dāng)摩擦環(huán)境溫度超過 600 ℃時,涂層發(fā)生嚴重氧化,生成大量多孔結(jié)構(gòu)的 WO 3 、CoWO 4 、CoO 等相,不利于涂層的耐磨性。但在氬氣環(huán)境中(缺氧環(huán)境下),WC-Co 涂層不適宜作耐磨涂層,原因是氣氛中缺少氧元素,摩擦過程不能產(chǎn)生保護涂層的摩擦膜,會導(dǎo)致涂層磨損嚴重。而 Wesmann 等研究認為 WC-10Co-4Cr 涂層在氮氣中的磨損率比在空氣中低得多,在 200 ℃的空氣氛圍中,摩擦系數(shù)最高達到 1.0。Jin等研究了 40、80 和 120 N 載荷下超音速噴涂WC-12Co 涂層的摩擦性能,結(jié)果表明,隨著載荷的增加,涂層的摩擦系數(shù)增加,磨損嚴重。涂層在負載40 和 80 N 時的磨損機理為磨粒磨損,而 120 N 負荷下的磨損機制是脆性斷裂。
在涂層中添加 MoS 2 -Ni、稀土氧化物(La 2 O 3 或CeO 2 )等能有效減小涂層的磨損量。WC-Co 涂層隨著 MoS 2 -Ni 質(zhì)量分數(shù)的增加,摩擦系數(shù)降低,磨損率隨之降低,但 MoS 2 -Ni 添加量達到 7.2%時,涂層磨損率驟增,甚至超過純 WC-Co 涂層,因此 MoS 2 -Ni對涂層性能有重要影響 。Zhang 等研究了不同含量 La 2 O 3 或 CeO 2 稀土氧化物對 CoCrW 涂層摩擦學(xué)性能的影響,稀土氧化物能改善涂層表面粗糙度,提高顯微硬度,添加 2% La 2 O 3 或 2% CeO 2 ,可使涂層獲得較高摩擦系數(shù)的同時,具有較低的磨損率。
因此在研發(fā)涂層時,應(yīng)找出最優(yōu)材料和最適當(dāng)?shù)奶砑恿浚垣@得最優(yōu)的涂層性能。對于 Co 基涂層,如何控制硬質(zhì)相的分解應(yīng)是重點研究問題。
3 熱噴涂防滑涂層的展望
熱噴涂技術(shù)的持續(xù)進步促進了防滑涂層技術(shù)的工業(yè)應(yīng)用,熱噴涂技術(shù)為防滑裝備提供了低成本、高效益的解決方案。在防滑材料方面,需要開發(fā)新材料體系,優(yōu)化材料配方,在提高涂層性能的同時降低成本,將材料體系標準化、系列化。在涂層制備工藝方面,以提高涂層性能為目的,針對特定材料體系,通過研發(fā)和選擇合適的噴涂方法,優(yōu)化前處理與噴涂參數(shù),有效增強涂層與基體、涂層內(nèi)部的結(jié)合強度,以解決涂層沉積過程中的問題,如硬質(zhì)合金脫碳化問題、非晶涂層金屬玻璃形成能力。
另外熱噴涂技術(shù)也存在一個比較嚴重的缺陷,其施工、維護、修補只能采取熱噴涂方式進行,需要專業(yè)施工人員,不利于在緊急狀態(tài)下實施,應(yīng)提高制備工藝的自動化程度,向著高速、高效噴涂發(fā)展,開發(fā)出方便、實用、移動式的噴涂設(shè)備。服役條件對涂層壽命有較大影響,因此在防滑耐磨涂層性能表征方面,應(yīng)在考慮實際使用的工況條件,以獲得更加貼近工程實際的防滑與耐磨數(shù)據(jù),實現(xiàn)防滑數(shù)據(jù)的在線測量。
國內(nèi)熱噴涂防滑涂層的研究與發(fā)達國家仍有差距,提高涂層制備效率、降低制備成本、制備出符合實際工況要求的防滑涂層,仍然是今后一段時間亟待解決的問題。
更多關(guān)于材料方面、材料腐蝕控制、材料科普等方面的國內(nèi)外最新動態(tài),我們網(wǎng)站會不斷更新。希望大家一直關(guān)注中國腐蝕與防護網(wǎng)http://www.ecorr.org
責(zé)任編輯:王元
《中國腐蝕與防護網(wǎng)電子期刊》征訂啟事
投稿聯(lián)系:編輯部
電話:010-62313558-806
郵箱:fsfhzy666@163.com
中國腐蝕與防護網(wǎng)官方 QQ群:140808414
免責(zé)聲明:本網(wǎng)站所轉(zhuǎn)載的文字、圖片與視頻資料版權(quán)歸原創(chuàng)作者所有,如果涉及侵權(quán),請第一時間聯(lián)系本網(wǎng)刪除。
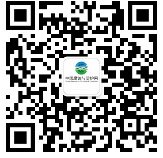
官方微信
《中國腐蝕與防護網(wǎng)電子期刊》征訂啟事
- 投稿聯(lián)系:編輯部
- 電話:010-62313558-806
- 郵箱:fsfhzy666@163.com
- 中國腐蝕與防護網(wǎng)官方QQ群:140808414