鎂合金作為一種輕質(zhì)金屬結(jié)構(gòu)材料,不僅密度小(約1.7 g/cm3),比強度和比剛度高,而且擁有較好的切削性能,對航空、航天、汽車及電子等領(lǐng)域的輕量化設計與制造具有重要意義。然而,鎂合金化學性質(zhì)非常活潑,其標準電位為-2.37 V,比鐵、鋁、鋅及銅等金屬的電位都低,在空氣中即可氧化并形成稀疏多孔的氧化膜,導致基體的耐腐蝕性較差。由于硬度較低,表面耐磨損性能也較低,因而鎂合金表面防護成為其進一步推廣應用面臨的重要課題。
為提升表面耐蝕耐磨等性能,鎂合金應用研究發(fā)展了兩個方向:一方面是材料制備,可通過合金本身純凈化,改善鎂合金微觀結(jié)構(gòu),從而增強耐蝕性;另一方面是合金表面處理,通過合金表面制備涂層,隔絕基體與外部環(huán)境,從而提升鎂合金表面防腐耐磨等性能。
金屬表面防護的常見方法有:化學轉(zhuǎn)化膜、陽極氧化、激光表面處理、微弧氧化、氣相沉積和熱噴涂等。傳統(tǒng)的化學轉(zhuǎn)化膜法是通過金屬表層原子與電解液中的粒子發(fā)生原子反應,形成具有保護功能的薄膜。陽極氧化方法則是將金屬作為陽極,在酸性或堿性溶液中通過電解使金屬表面發(fā)生氧化。這兩種方法所制備的保護層厚度偏薄、脆性大、硬度較低,對金屬的防護能力有限,而且由于采用含鉻、氟、磷等元素的電解液,對環(huán)境造成嚴重污染。微弧氧化技術(shù)是在電解液脈沖電場環(huán)境作用下微弧放電,以冶金結(jié)合方式在基體表面生成氧化物陶瓷層。該技術(shù)對環(huán)境無污染,但能耗高(電流密度大于1500 A/m2)且處理效率低下, 例如在電源系統(tǒng)輸出電流為l00~300 A 的條件下,一次性處理面積僅為0.05~0.2m2。氣相沉積技術(shù)是在真空條件下通過物理或化學方法,將固態(tài)鍍料轉(zhuǎn)化為原子、分子或離子態(tài)的氣相物質(zhì)后,再沉積于基體表面形成固體薄膜。該方法的優(yōu)點是可以大幅減少沉積層中的雜質(zhì)元素含量,膜與基體結(jié)合良好,但同樣面臨效率低的問題,而且制備的膜層薄,容易發(fā)生微孔腐蝕。
表面噴涂是工業(yè)應用最廣泛的表面防護方法,最顯著的特點是實施簡單且效率高。熱噴涂技術(shù)可快速大面積實現(xiàn)鎂合金表面涂層保護。然而,熱噴涂采用高溫熱源,涂層材料易發(fā)生熔化,對熱敏感的基體材料而言,基體組織與力學性能將發(fā)生顯著變化,而且由于熱噴涂層內(nèi)存在較高的殘余拉應力,限制了涂層防護性能的提升。此外,隨著近年來激光應用技術(shù)的快速發(fā)展,激光表面處理技術(shù)在材料表面的處理中也引起了較多關(guān)注。利用激光束快速、局部地加熱工件,可實現(xiàn)局部急熱或急冷調(diào)控基體表面性能,但相比噴涂技術(shù),其保護涂層厚度和效率尚有較大差距。
冷噴涂是建立在合理利用空氣動力學原理基礎上的一種新型噴涂技術(shù)。該技術(shù)以高壓氣體(He、N2、Ar、空氣或它們的混合氣體)為載體,通過縮放噴嘴加速,使噴涂顆粒速度達到300~1200 m/s,在固態(tài)下高速撞擊基體表面,主要依靠大的塑性變形而形成涂層。噴涂材料的粉末粒子在熱的非氧化性氣流束中加速,氣流溫度較低,對基體的熱影響小,涂層基本無氧化現(xiàn)象且孔隙率低。由于粒子撞擊基體時速度高,會產(chǎn)生較大的塑性變形,在涂層內(nèi)部主要受壓應力作用,因此涂層內(nèi)部以及涂層與基體之間結(jié)合緊密,不易開裂。
基于冷噴涂技術(shù)以上優(yōu)點,該技術(shù)為鎂合金表面防護提供了一種新的可行方法。近年來,相關(guān)研究者采用冷噴涂技術(shù)在鎂合金表面進行涂層制備,并對涂層的耐腐蝕性以及耐磨損性開展了相關(guān)探討。本文就冷噴涂層對鎂合金基體的防護研究現(xiàn)狀進行了綜述,并對冷噴涂防護研究趨勢進行了展望。
1 鎂合金表面冷噴涂防腐涂層
鋁和鋁合金密度低、硬度適中、塑性較好,是冷噴涂采用最多的原材料之一,由于在自然環(huán)境中氧化形成的氧化膜A12O3 堅硬致密,可有效保護基體,因而被廣泛應用于金屬表面防腐。大量的研究表明,純鋁或鋁合金涂層能夠在各種金屬基體表面實現(xiàn)保護,并且噴涂沉積工藝參數(shù)可在較大范圍內(nèi)調(diào)整。對暴露在大氣以及海洋環(huán)境中的鎂合金結(jié)構(gòu)件進行冷噴涂鋁金屬涂層防護處理,可大幅降低大氣腐蝕和海水中電化學腐蝕速率,減少鎂合金結(jié)構(gòu)件的損耗。目前,在鎂及鎂合金基體上冷噴涂鋁金屬或金屬基復合涂層的方法主要分為三種:純鋁涂層、鋁合金涂層、陶瓷顆粒增強鋁基復合涂層。
1.1 純鋁涂層
已有學者對AZ91D、ZE41A-T5、AZ31B等鎂合金表面開展了冷噴涂純鋁涂層防腐蝕研究。其中純鋁在冷噴涂沉積過程中可采用氮氣、氦氣或者壓縮空氣作為載氣,工作氣體的溫度可以從室溫至350 ℃,工作氣體的壓力可以從小于1 MPa 到接近5 MPa。
Tao 等人在AZ91D 鎂合金基體上制備了純Al涂層,如圖1 所示,涂層無明顯裂紋等缺陷,與基體結(jié)合良好,但在局部粒子界面處存在少量的微孔和微裂紋。對比純Al 涂層與純Al 塊的耐蝕性,結(jié)果表明純Al 涂層的Er-Ecorr 值與Epit-Ecorr 值均大于純Al 塊。圖2 結(jié)果表明,純Al 涂層抵抗點蝕的水平高于純Al塊,且更容易出現(xiàn)再鈍化現(xiàn)象。
此外,有研究表明,冷噴涂所用鋁粉的純度對試樣的耐蝕性能存在顯著影響。Brian等人以AZ41A-T5 合金為基體,對比了商用純Al(99.5wt.%)粉末以及高純Al(99.95wt.%)粉末的冷噴涂層性能,結(jié)果發(fā)現(xiàn)高純Al 粉末制備的涂層腐蝕速率遠低于普通商用Al 涂層,且腐蝕過程中的高純Al 涂層的電流密度僅為0.05 mA/cm2。由于雜質(zhì)的存在,商用純Al涂層的電流密度與其他鋁合金涂層的腐蝕電流密度相當,大約為2.35 mA/cm2。因此,純Al 的純度越高,涂層的耐蝕性越好。
Diab 等人對冷噴涂鋁涂層進行鹽霧腐蝕研究,圖3 為AZ31B 基體與冷噴涂試樣在5%NaCl 鹽霧腐蝕試驗后的結(jié)果對比:相比于無Al 涂層保護的試樣,冷噴涂純鋁涂層的試樣的腐蝕速率大幅降低,而且在33 d 試驗期內(nèi),Al 涂層可較好地保護鎂合金基體。
圖4 為在腐蝕試驗中的鎂合金基體與冷噴涂試樣的腐蝕速率與平均質(zhì)量損失情況:40 d 前,冷噴涂試樣的質(zhì)量損失低于1.5%,且腐蝕90 d 后的質(zhì)量損失僅為9%,遠低于鎂合金基體的質(zhì)量損失。
為了對冷噴涂純鋁涂層的耐蝕性進行綜合評價,表1 列出了通過不同技術(shù)制備的純Al 涂層的電化學測試結(jié)果。表1 的試驗結(jié)果均為涂層在3.5%NaCl 溶液中的電化學測試結(jié)果,盡管部分基體材料并非鎂合金,但不影響涂層本身腐蝕性能的對比。從表1 可以看出,冷噴涂、磁控濺射、電弧噴涂以及多弧離子鍍得到的純Al 涂層的腐蝕電位較高,均高于-1 V,其中冷噴涂純Al 涂層的最高腐蝕電位可達-0.68 V,接近純鋁塊的腐蝕電位(-0.63 V)。不難發(fā)現(xiàn),與其他涂層技術(shù)相比,冷噴涂層的抗腐蝕性能具有更大優(yōu)勢,這可能與冷噴涂層致密度高且為壓應力狀態(tài)有關(guān),二者共同作用減少了腐蝕通道的形成。
1.2 鋁合金涂層
對比鎂合金,鋁合金也同樣具有較好的耐腐蝕性,但目前為止,針對鎂合金防腐的冷噴涂鋁合金涂層研究不多。Brian 等人利用冷噴涂技術(shù)在鎂合金表面制備了AA5356、AA4047 和Al-5wt.%Mg 合金涂層,并對比了三種涂層的硬度、涂層與基體的結(jié)合強度和在0.6 mol/L NaCl 溶液中的電偶腐蝕特性。結(jié)果發(fā)現(xiàn),采用氦氣冷噴涂的Al-5wt.%Mg 合金涂層與基體的結(jié)合強度最高,達到60 MPa,涂層硬度達到124HV100,與AA4047 和AA5056 鋁合金冷噴涂層的硬度接近(圖5)。圖6 為試樣在不同涂層條件下的電偶腐蝕速率。Al-5wt.%Mg 合金涂層-Mg 合金基體的電偶腐蝕速率為0.155 mA/cm2,雖然略高于高純Al 涂層-Mg 合金基體以及Mg 合金涂層-Mg 合金基體的電偶腐蝕速率,但明顯低于商用Al 涂層-Mg 合金基體以及Al 合金涂層-Mg 合金基體的電偶腐蝕速率。
1.3 鋁基復合材料涂層
近年來,鋁基復合材料因其低密度、高比強度、高比模量以及良好的耐磨損性等優(yōu)異的綜合性能,被譽為未來最具有競爭力的綠色工程材料之一。在制備冷噴涂防腐鋁涂層時,引入適量陶瓷顆粒或采取合金化措施制備鋁基復合材料涂層,不僅可以保持鋁涂層優(yōu)良的耐腐蝕性,同時還可使涂層具有較高的硬度、強度和耐磨損能力。
Spencer 等人在AZ91E鎂合金基體上制備了不同Al2O3 陶瓷含量的Al-Al2O3 以及AA6061-Al2O3 復合涂層。從圖7 可以看出,AA6061 合金粉末冷噴涂層內(nèi)部含有少量的微孔,當噴涂粉末中添加了Al2O3時,陶瓷顆粒對冷噴涂粒子沉積具有較好的夯實效應,使涂層的孔隙含量明顯減少,并且隨著Al2O3 顆粒含量的增加,涂層組織的致密度增加。類似夯實效應已被廣泛報道。Wang 等人與Kumar 等人在冷噴涂制備AA5056-SiC和Al-SiC 復合涂層中進行了深入分析。Spencer 等人研究陶瓷顆粒含量對復合涂層耐蝕性、摩擦磨損性能以及硬度的影響,發(fā)現(xiàn)含有Al2O3 顆粒的復合涂層,其耐蝕性優(yōu)于AZ91E 合金,但Al2O3 含量對其耐蝕性的影響不大(見圖8)。此外,添加Al2O3 顆粒使涂層的硬度以及耐磨損性都有所提高。隨著添加Al2O3 陶瓷粉末含量的增加,涂層的硬度升高,磨損速率迅速降低(見圖9)。
Wang 等人在純Al 上制備了AA5056-SiC 復合涂層,雖然基體材料不是鎂合金,但對鎂合金表面冷噴復合涂層防腐具有一定的指導意義。如圖10 所示,涂層內(nèi)部無明顯孔洞及裂紋,且與基體結(jié)合緊密。由于SiC 對涂層的夯實作用,AA5056-SiC 復合涂層的孔隙率明顯下降,從AA5056 涂層孔隙率2.25%下降到0.61%。微觀組織分析發(fā)現(xiàn),涂層內(nèi)部分SiC 顆粒具有明顯裂紋,推測原因是硬脆SiC 顆粒在噴涂高速撞擊條件下易形成裂紋或發(fā)生斷裂。由于SiC 粒子沉積時無法發(fā)生塑性變形,因此硬質(zhì)粒子發(fā)生碰撞破碎,這也間接反映了顆粒對塑性金屬涂層具有強烈的撞擊夯實作用。
表 2 對比了AA5056 和三種不同SiC 含量的AA5056-SiC 復合涂層在0.1 mol/L Na2SO4 溶液中的電化學測試數(shù)據(jù)。從表2 可以看出,添加體積分數(shù)15%SiC 明顯提升了AA5056 涂層的耐蝕性,這與微觀組織的致密化具有重要關(guān)系。對比還可以發(fā)現(xiàn),當增加涂層中SiC 含量時,復合涂層的耐蝕性變化不大。這是因為三種復合涂層的孔隙率差別較小(0.93%、0.61%、0.85%),且均低于AA5056 涂層的孔隙率(2.25%),較小的孔隙率差異對耐蝕性無明顯影響。
眾所周知,在顆粒增強金屬基復合涂層的制備中,增強相顆粒的尺寸、含量、形貌等均對涂層組織與性能具有重要影響。Wang 等人[研究了5 種尺寸(2.3、4.7、15.6、29.6、72.8 μm)的SiC 顆粒對冷噴涂AA5056-SiC 復合涂層孔隙率(見圖11)和耐蝕性的影響(見圖12)。其中D1 代表AA5056 與SiC-2.3μm 混合粉末,D2 代表AA5056 與SiC-4.7 μm 混合粉末,D3 代表AA5056 與SiC-15.6 μm 混合粉末,D4代表AA5056 與SiC-29.6 μm 混合粉末,D5 代表AA5056 與SiC-72.8 μm 混合粉末。隨著SiC 顆粒尺寸的增加,SiC 對涂層的夯實效應越明顯,且涂層孔隙率不斷降低,提高了涂層的耐蝕性。當SiC 尺寸大于 15.6 μm 時,隨著尺寸進一步增加,涂層孔隙率下降不明顯。因為SiC 尺寸過大時,顆粒碰撞反彈脫落較多,有效沉積的陶瓷顆粒數(shù)量不斷減少,且AA5056與SiC 的接觸面積增加,SiC/AA5056 粒子界面成為弱結(jié)合區(qū),兩者界面處存在微孔易發(fā)生腐蝕。因此對增強顆粒的尺寸必須進行合理優(yōu)化,才能獲得力學和抗腐蝕性能俱佳的涂層。
Bu 等人將Mg17Al12 粉末與純Al 粉末混合,在AZ91D 鎂合金基體表面通過冷噴涂技術(shù)制備了Al-Mg17Al12 復合涂層(圖13)。借助Mg17Al12 顆粒在冷噴涂層沉積過程中的夯實效應,鋁基復合涂層的孔隙率低于0.4%,復合涂層/基體的結(jié)合強度比純Al涂層/基體的結(jié)合強度提升了2~3 倍。從圖14 可以看出,復合涂層的腐蝕電位比AZ91D 基體提高了約0.6V,腐蝕電流密度為3.4?10?6 A/cm2,降低一個數(shù)量級。
2 鎂合金表面冷噴涂耐磨涂層
在鎂合金表面涂層的研究中,耐磨涂層是重要的研究方向之一。在航空、航天以及車輛行動系統(tǒng)的鎂合金結(jié)構(gòu)件表面采用冷噴涂防護技術(shù),可大幅度提高結(jié)構(gòu)件的耐磨性,并且與傳統(tǒng)的螺栓緊固或鑲鑄鋼質(zhì)構(gòu)件方法相比,冷噴涂防護涂層的質(zhì)輕且涂層不易脫落。目前,研究人員研究了不少合金體系的冷噴涂層,用來提高鎂合金表面的耐磨性,如鋁基復合涂層、鋅鋁合金涂層、不銹鋼涂層、碳化鎢鈷涂層及其他合金復合涂層(如銅-鎢復合涂層等)。
Shockley 等人發(fā)現(xiàn)Al-Al2O3 復合涂層中陶瓷顆粒形貌與含量對涂層的耐磨損性有重要影響。研究的四種涂層分別為含有體積分數(shù)10%多邊形Al2O3 顆粒的涂層(ANG10)、含有22%多邊形Al2O3 顆粒的涂層(ANG22)、含有3%球形Al2O3 顆粒的涂層( SPH3) 以及含有11%球形Al2O3 顆粒的涂層(SPH11)。四種涂層內(nèi)部致密,除斷裂的陶瓷顆粒內(nèi)部存在微裂紋外,涂層內(nèi)部無明顯孔隙(見圖15)。研究四種涂層的耐磨性發(fā)現(xiàn),含有22%多邊形Al2O3顆粒的復合涂層,其磨損速率最低,且隨著磨損時間的增加,磨損速率基本保持不變(圖16—17)。
趙慧等人[59]在AK63 鎂合金表面制備鋅鋁合金(ZA20)涂層,涂層與基體結(jié)合良好,界面處無裂紋、孔洞和分層等缺陷。研究結(jié)果顯示,在相同的干摩擦條件下,鋅鋁合金冷噴涂層的質(zhì)量損失為鎂合金的48%,冷噴涂層的腐蝕電位(-0.26 V)遠高于基體鎂合金的腐蝕電位(-1.62 V),腐蝕電流比鎂合金低2~3 個數(shù)量級。戴宇等人發(fā)現(xiàn)在AZ80 鎂合金表面制備的420 不銹鋼涂層具有較好的耐磨性,磨損率為1.641×10-6 mm3/(N.m),比AZ80 鎂合金的磨損率(1.321×10-3 mm3/(N.m))降低了3 個數(shù)量級(圖18)。
陳杰等 采用冷噴涂和超音速火焰噴涂兩種方法,在AZ80 鎂合金表面制備了納米WC-17Co 涂層(圖19)。結(jié)果表明, 冷噴涂層的磨損率為9.1×10?7 mm3/(N.m),比HVOF 涂層(2.3×10?6 mm3/(N.m))低一個數(shù)量級,較鎂合金基材(5.5×10-4 mm3/(N.m))降低了3 個數(shù)量級。同時,由于冷噴涂層的孔隙率更低,因此涂層的耐蝕性更優(yōu),其開路電位(-0.38 V)高于超音速噴涂層(-0.54 V)。賈平平等人采用冷噴涂與化學氣相沉積相結(jié)合的方法,在鎂合金表面制備了Cu/W 復合涂層,磨損后的質(zhì)量損失從0.032%降到0.020%,腐蝕電位比基體正移了1.3 V(見圖20)。
3 熱處理對冷噴涂涂層的影響
熱處理作為調(diào)控涂層綜合性能的一種手段,可使涂層內(nèi)部原子擴散、內(nèi)應力降低、微觀結(jié)構(gòu)改變等,同時可提高涂層的力學性能,如拉伸強度、延伸率、粘結(jié)強度等。大量研究表明,熱處理可改善涂層的微觀結(jié)構(gòu),降低孔隙率,從而提高涂層的耐腐蝕能力。因此,冷噴涂層的后續(xù)熱處理受到研究學者的廣泛關(guān)注。
Spencer 等人在AZ91E 鎂合金上制備了純Al涂層,并將涂層在400 ℃下熱處理20 h,發(fā)現(xiàn)在涂層/基體界面處的組織明顯分層,生成Mg17Al12 以及Al3Mg2 兩種金屬間化合物(見圖21a),硬度分別為250HV0.2 和275HV0.2,均遠高于鎂合金基體的硬度(60HV0.2)。研究表明,Mg17Al12 和Al3Mg2 的耐蝕性優(yōu)于AZ91E(圖21b)。因為Mg17Al12 和Al3Mg2 具有比鎂合金更優(yōu)異的耐腐蝕能力,所以在較高的氯離子濃度中和較寬的pH 值范圍內(nèi),其均可作為Mg 基體的陽極保護層,阻止Mg 的腐蝕。
Spencer 等人對Al-Al2O3 復合涂層同樣進行了400 ℃熱處理,熱處理時間為2 h(圖22)。涂層/基體界面處主要為Mg17Al12 及少量的Al3Mg2。對比熱處理后純Al 涂層、Al-25%Al2O3、Al-50%Al2O3 和Al-75%Al2O3 復合涂層的極化曲線,發(fā)現(xiàn)熱處理對涂層電化學行為的影響不大(見圖23),但在鹽霧環(huán)境下,熱處理后復合涂層的耐蝕性能明顯提高(見圖24)。
4 結(jié)論與展望
表面腐蝕與磨損是鎂合金工程應用必須攻克的關(guān)鍵難題。冷噴涂技術(shù)作為一種新興技術(shù),在鎂合金表面防護中已展現(xiàn)出了巨大的潛力。一方面,針對冷噴純鋁、鋁合金和鋁基復合涂層等涂層的工藝開發(fā)、耐腐蝕性均有大量報道;另一方面,針對鎂合金表面耐磨涂層制備,冷噴涂也展現(xiàn)了良好的技術(shù)可行性,尤其是冷噴涂鋁基復合涂層、熱處理技術(shù)等,可使鎂合金表面的耐蝕和耐磨損等性能同時提高,為鎂合金提供了重要的防護手段。然而,目前鎂合金防護冷噴涂層種類仍較少,涂層脆性、微裂紋和殘余應力等關(guān)鍵基礎問題仍面臨重要挑戰(zhàn)。未來構(gòu)建涂層材料研發(fā)與加工成形一體化理念,提出冷噴涂防護技術(shù)新思路,將對鎂合金表面實現(xiàn)高效高性能防護具有重要意義。
更多關(guān)于材料方面、材料腐蝕控制、材料科普等方面的國內(nèi)外最新動態(tài),我們網(wǎng)站會不斷更新。希望大家一直關(guān)注中國腐蝕與防護網(wǎng)http://www.ecorr.org
責任編輯:王元
《中國腐蝕與防護網(wǎng)電子期刊》征訂啟事
投稿聯(lián)系:編輯部
電話:010-62313558-806
郵箱:fsfhzy666@163.com
中國腐蝕與防護網(wǎng)官方 QQ群:140808414
免責聲明:本網(wǎng)站所轉(zhuǎn)載的文字、圖片與視頻資料版權(quán)歸原創(chuàng)作者所有,如果涉及侵權(quán),請第一時間聯(lián)系本網(wǎng)刪除。
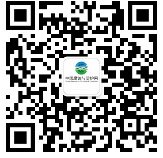
官方微信
《中國腐蝕與防護網(wǎng)電子期刊》征訂啟事
- 投稿聯(lián)系:編輯部
- 電話:010-62313558-806
- 郵箱:fsfhzy666@163.com
- 中國腐蝕與防護網(wǎng)官方QQ群:140808414