GH4169 合金是一種鎳基時效強化高溫合金,在高溫下具有較好的力學性能、熱工藝性能和焊接性能,可在-253~650 ℃范圍內使用,也可在約800 ℃短時間使用,目前多應用于航空發動機渦輪盤、葉片等結構件。隨著航空、航天技術發展,高溫合金的使用溫度越來越高,熱障涂層(TBCs) 對進一步提高合金材料的使用溫度發揮著重要作用,其可以提高使用溫度150~200 ℃,在提高航空發動機服役壽命的同時提升工作效率,降低油耗。
熱障涂層在服役過程中經常受到高溫氧化、熱腐蝕、沖蝕等侵害,特別是對航空發動機,燃料中的Na 和S 對涂層產生熔鹽熱腐蝕,是降低其使用壽命的一個重要因素[5,因此對熱障涂層熱腐蝕性能進行研究是非常必要的。由于目前等離子噴涂技術的局限性,制備的熱障涂層孔洞、裂紋較多,與基體結合性較差,抗熱疲勞與裂紋擴展能力相對較差。激光重熔為進一步改善等離子噴涂TBCs 性能提供了新的途徑。激光重熔能消除涂層的層狀結構、大部分孔隙和氧化物夾雜,形成均勻致密的陶瓷涂層,保證了涂層的性能,從而提高工件的使用壽命。
GH4169 合金作為航空發動機冷端部件材料在實際服役環境中,會存在短期極限工作溫度達到約950 ℃。為了探索熱障涂層在合金極限工作溫度下對基體的防護性能,故本工作中采用等離子噴涂方法在GH4169 合金表面先制備了NiCoCrAlY 粘結層,然后制備了ZrO2-7%Y2O3 (質量分數) 陶瓷涂層,并用激光重熔工藝對熱障涂層進行處理,最后對比研究了噴涂態和激光重熔熱障涂層在950 ℃下75%Na2SO4+25%NaCl (質量分數) 復合熔鹽中的熱腐蝕行為。
1 實驗方法
1.1 實驗材料
實驗所選用的基體材料GH4169 由北京航空材料研究院經鍛造加工制成,化學成分為52.4Ni -18.4Cr - 5.5Nb-3.2Mo- 1.4Co - 18.2Fe - 0.9Ti (質量分數,%)。使用電火花線切割機,將合金加工成10 mm×10 mm×4 mm的片狀試樣。實驗所選用粘結層材料是由中州合金材料有限公司提供的Ni-25Co-18Cr-10Al-Y合金粉末(質量分數,%)。實驗所采用的陶瓷層材料是由錦州金江材料公司提供的7%Y2O3穩定的ZrO2,原始粉末粒度為納米級,經噴霧干燥團聚后粒度在25~80 μm。
1.2 涂層制備工藝
實驗采用等離子噴涂制備粘結層和陶瓷層。噴涂前試樣經打磨、清洗、噴砂等預處理。經過前期的探索和實驗,兩種涂層的等離子噴涂工藝參數見表1。噴涂時,激光功率550W,掃描速率350 mm/min,光斑尺寸3 mm×3 mm,搭接量30%。
1.3 熱腐蝕實驗方法
將未處理和激光重熔的兩種熱障涂層試樣用精度為0.1 mg的電子天平稱取重量后,在試樣表面用毛刷涂抹一層預先配好的飽和鹽溶液,用干燥箱干燥后,再次稱取重量,控制試樣表面的鹽膜重量在2~3 mg/cm2。然后將涂有鹽膜的試樣分別放入陶瓷坩堝中,之后置于Muffle 爐中。升溫速率設定為15 ℃/min,到達950 ℃開始保溫,每10 h 取出試樣,并將其放入蒸餾水中多次煮沸,以除去試樣表面殘留的鹽膜,然后經過干燥后再次稱重并觀察涂層表面宏觀形貌的變化。繼續重復以上實驗過程,直至實驗時間達到100 h。根據熱腐蝕過程中試樣重量變化繪制熱腐蝕動力學曲線。取熱腐蝕10,40 和100 h 的兩種熱障涂層試樣,一部分用作觀察涂層表面宏觀形貌;另一部分進行鑲嵌、打磨、拋光、腐蝕后,用于掃描電鏡(SEM,HITACHI S-4800 型) 和X射線衍射(XRD,D8ADVANCE) 分析。
2 結果與討論
2.1 兩種熱障涂層的表面形貌
圖1a 是等離子噴涂熱障涂層的表面形貌??梢钥闯觯繉颖砻姘纪共黄?,顆粒大小不一,存在一定的孔隙和裂紋。這是由于等離子噴涂過程中,粉末顆粒被加熱至完全熔化或半熔化狀態后高速沖擊基體,部分粉末顆粒在等離子體焰流中停留時間短,未能完全融化,造成顆粒大小不同。由于顆??焖倌啼佌乖诨w表面,顆粒相互堆積,造成表面凹凸,且形成孔隙裂紋。圖1b 是等離子噴涂熱障涂層經過激光重熔后的表面微觀形貌。可以看出,涂層經過激光重熔之后,表面整體光滑平整,涂層致密度高,沒有明顯的孔洞和裂紋,僅存在少部分激光重熔時的濺射顆粒??紫堵实慕档蛯⑻岣咄繉訉w的保護作用。
2.2 熱腐蝕動力學曲線
圖2 是兩種熱障涂層在950 ℃下75%Na2SO4+25%NaCl 混合熔鹽中熱腐蝕100 h 的動力學曲線。可以看出,兩種熱障涂層的腐蝕動力學曲線規律完全不同。等離子噴涂熱障涂層在0~50 h 腐蝕時間內,試樣質量保持穩定上升的趨勢,大致呈線性變化,說明在這個時間段內涂層的抗腐蝕性能較好,很好地保護了基體合金。腐蝕達到50 h時,曲線出現極大值,增重為2.7 mg/cm2,說明此時涂層的抗腐蝕性能已經達到極限。在50~100 h 時間段內,動力學曲線出現了急劇的下降;當腐蝕100 h后,此時出現了嚴重的減重現象,除去坩堝重量后的值為-6.8 mg/cm2。通過顯微觀察和XRD分析可見,部分陶瓷層在陶瓷層層間產生了剝落,而粘結層并未發生剝落。原因主要是陶瓷層的內部缺陷導致的應力集中,高溫下陶瓷層的燒結和熔鹽的滲入使陶瓷層內裂紋擴展。此時涂層已經發生失效,對基體的保護作用在急劇衰退。熱腐蝕后試樣的截面照片可以進一步驗證這一結論。激光重熔熱障涂層在0~50 h 腐蝕時間內,保持類似的直線上升的趨勢,但在腐蝕增重的數值上明顯小于同時間未處理熱障涂層的。在50~100 h的腐蝕后期,由于陶瓷層激光重熔后致密的柱狀晶結構消除了內部大量的孔隙和裂紋,熔鹽僅消耗了表層的少量Y2O3和ZrO2后難以繼續滲透進涂層內部,使得腐蝕增重速率放緩,曲線趨于平滑。激光重熔在腐蝕100 h 后,腐蝕增重達到3.7 mg/cm2,涂層仍然保持著一定的抗腐蝕性能。
2.3 熱腐蝕后涂層表面物相分析
圖3 是兩種熱障涂層在950 ℃下75%Na2SO4+25%NaCl 混合熔鹽中熱腐蝕不同時間后表面XRD譜。從圖3a 中可以看出,噴涂態熱障涂層起初以t相、c 相為主,經過40 h 的熱腐蝕之后,m相衍射峰開始變強。隨著時間的延長,m相衍射峰進一步增強,t 相衍射峰減弱,表明m相體積分數逐漸增多,而t 相體積分數在逐漸減小,驗證了涂層內部在發生著t→m的轉變。同時出現了微弱的Y2(SO4)3相衍射峰,且隨腐蝕時間延長逐漸增強,說明不斷有新的Y2(SO4)3相生成,反應一直在進行。而從圖3b 中可以看出,隨著熱腐蝕的持續進行,涂層內部同樣地發生了t→m的相轉變,但和圖3a 相比,m相的峰較弱,說明m相的轉變速率更低,體積分數更小。同時,圖3b 中沒有出現Y2(SO4)3,100 h 后涂層表面成分主要還是ZrO2相,涂層表現出了良好的耐腐蝕性能。
2.4 熱腐蝕后涂層表面微觀形貌觀察
圖4 示出了噴涂態熱障涂層在950 ℃下75%Na2SO4+25%NaCl 混合熔鹽中熱腐蝕不同時間后的表面微觀形貌。從圖4a 中可以看出,涂層經過熱腐蝕10 h 后,表面開始變得疏松,出現了一些孔洞和溝壑,局部有剝落的現象,形成了腐蝕坑,且出現了一些細小的ZrO2顆粒,但此時涂層尚處于熱腐蝕孕育期,涂層具有較好的抗熱腐蝕性能。從圖4b 中可以看出,經過40 h 的熱腐蝕,涂層的疏松程度加劇,表面顆粒之間出現了大量的網狀連接,顆粒尺寸相比于圖4a 中的有一定程度的增大,但此時的涂層表面未出現大面積的剝落,說明涂層還保持著一定的抗腐蝕性能。從圖4c 中可以看出,經過100 h 的腐蝕后,涂層表面基本破裂,出現了大面積剝落,顆粒尺寸進一步長大,顆粒數量相比于圖4b 而言急劇增多。其中還夾雜著小部分的長條狀顆粒,是熔鹽與涂層表面反應產生的Y2(SO4)3。
圖5 是激光重熔熱障涂層在950 ℃ 下75%Na2SO4+25%NaCl 混合熔鹽中熱腐蝕不同時間后的表面微觀形貌照片。從圖5a 中可以看到,經過10 h熱腐蝕后,涂層表面依然平整光滑,結構致密,晶界清晰,僅能看到細微的裂紋,此時涂層的抗腐蝕性能較好。從圖5b 中可以得出,經過40 h 的熱腐蝕后,伴隨著體積的膨脹,產生了熱應力,涂層表面出現了明顯的網狀裂紋和孔洞;與10 h 腐蝕后的相比,表面依舊比較平滑,沒有發生涂層的剝落和破裂,此時涂層還具有抗腐蝕性能。從圖5c 中可以看到,涂層表面分層較為明顯,表面的粗糙度增加,裂紋擴展,導致涂層的表面發生了破裂,但未影響到涂層的核心部分。和噴涂態TBC 相比(圖4c),經過100 h 熱腐蝕后,激光熔覆熱障涂層仍然具有一定的抗腐蝕性能。
2.5 熱腐蝕后涂層截面微觀形貌觀察
圖6 是兩種熱障涂層在熱腐蝕100 h 后的截面微觀形貌。從圖6a 中可以看到,未激光重熔的涂層在經過950 ℃/100 h 熱腐蝕后,涂層內部出現了大量的孔洞以及明顯的橫向和縱向裂紋。涂層存在大量裂紋,表明涂層此時易于發生剝落。根據XRD分析可知,陶瓷層中大量的Y2O3與熔鹽發生如下反應:
反應生成Y2(SO4)3,Y含量的減少,導致陶瓷層中的ZrO2發生了t→m的轉變,同時伴隨著3%~5%陶瓷層體積的膨脹,使涂層中的拉應力轉變為壓應力,導致熱腐蝕后涂層的層狀結構出現破裂,部分破裂嚴重區域已經從表面脫落,出現孔洞,這是裂紋產生的主要原因。
從圖6b 中可以看出,激光重熔處理后的涂層經過950 ℃/100 h 熱腐蝕后,涂層內部也出現了一定數量的孔洞,但孔洞不連續,沒有看到裂紋的產生,各層之間依舊結合緊密,較腐蝕之前未發生大的變化。
同時從圖6a 和b 都可以看出,經過長時間的高溫腐蝕涂層出現了高溫氧化現象,在陶瓷層和粘結層中出現了明顯連續的熱生長氧化物(TGO),說明O通過熔鹽,滲透表面的陶瓷層進入到涂層內部,與粘結層中的元素發生反應,100 h 后TGO 的主要成分是Al2O3和Cr2O3[14-16]。但比較兩種熱障涂層中的TGO層,激光重熔熱障涂層中的TGO層更薄且不連續,說明激光重熔后的陶瓷層一方面有效地阻礙了O的滲入,極大程度上減慢了TGO層的形成;另一方面封堵了熔鹽的擴散通道,使熔鹽只能與表層的Y2O3和ZrO2反應,大大降低了體積膨脹應力和腐蝕產物的生長應力。相比于傳統的等離子噴涂陶瓷層的層片狀結構,激光重熔后的陶瓷層消除了層狀結構,同時也消除了大量裂紋、孔洞和未融化顆粒,形成柱狀晶結構的致密重熔層。在阻礙外部元素滲入的同時,也減緩了在高溫下陶瓷層內部裂紋向外擴展的速率,減弱了內應力的生成,對基體形成更有效的保護。
同時從圖6 中可以看到,在經過100 h 的熱腐蝕后,兩種熱障涂層與基體的界面都還保持良好的結合,界面清晰可見,說明涂層和基體的結合并沒有受到長時間熱腐蝕的影響。
結合熱腐蝕動力學曲線,從裂紋擴展角度分析,熱障涂層剝落失效主要分為3個階段:
第一階段:鈉鹽隨著溫度的上升,呈熔融態覆蓋在涂層表面形成鹽膜,經過由熱噴涂形成的孔隙和裂紋進入涂層內部,直接增加了熔鹽與涂層的接觸面積。
第二階段:熔融鹽與陶瓷層內的Y2O3 發生反應,生成腐蝕產物。由于Y2O3不斷被消耗,使ZrO2失穩,發生t→m的相轉變,相變過程中伴隨著體積膨脹,使原有的裂紋發生擴展,促進了熱腐蝕進一步深入涂層,腐蝕產物在裂紋處結晶長大,也為裂紋擴展提供了熱生長應力。經過長時間熱腐蝕后,促進了表面陶瓷層從陶瓷層內的剝落。
第三階段:在冷卻過程中,涂層間熱膨脹系數不匹配引起的熱應力,綜合作用于熱障涂層,最終導致涂層的失效剝落。
3 結論
(1) 等離子噴涂熱障涂層在950 ℃ 下75%Na2SO4+25%NaCl 混合熔鹽中腐蝕50 h 后達到性能極限,增重為2.7 mg/cm2;腐蝕100 h 后出現了腐蝕減重,達到了-6.8 mg/cm2,涂層發生剝落,涂層失效。激光熔覆熱障涂層腐蝕100 h 后,氧化增重為3.7 mg/cm2,涂層完好,仍然具有良好的抗熱腐蝕性能。
(2) 等離子噴涂熱障涂層在熱腐蝕過程中,涂層內部出現了明顯的裂紋,且生成了一定厚度的連續的TGO;涂層表面Y2O3和熔鹽發生化學反應生成Y2(SO4)3,Y2O3的減少使得ZrO2發生了t→m相的轉變,帶來涂層體積膨脹,加上腐蝕產物所帶來的熱生長應力,促進了內部裂紋擴展。激光重熔熱障涂層腐蝕100 h 后,涂層內部依然結合緊密,未產生裂紋;表面未與熔鹽發生反應,保持良好的抗熱腐蝕性能。
更多關于材料方面、材料腐蝕控制、材料科普等方面的國內外最新動態,我們網站會不斷更新。希望大家一直關注中國腐蝕與防護網http://www.ecorr.org
責任編輯:王元
《中國腐蝕與防護網電子期刊》征訂啟事
投稿聯系:編輯部
電話:010-62313558-806
郵箱:fsfhzy666@163.com
中國腐蝕與防護網官方 QQ群:140808414
免責聲明:本網站所轉載的文字、圖片與視頻資料版權歸原創作者所有,如果涉及侵權,請第一時間聯系本網刪除。
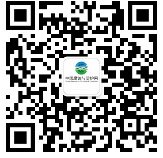
官方微信
《中國腐蝕與防護網電子期刊》征訂啟事
- 投稿聯系:編輯部
- 電話:010-62313558-806
- 郵箱:fsfhzy666@163.com
- 中國腐蝕與防護網官方QQ群:140808414