直升機在海洋環境服役過程中(飛行和露天停放過程),涂層體系不可避免地受到太陽輻射、鹽霧腐蝕、海浪沖刷及自身工況等多因素耦合作用,從而引起涂層的新型腐蝕損傷問題。這不僅影響涂層的外觀,而且還導致涂層防護體系失效,基體結構腐蝕,甚至引起重大事故。因此,防護體系在海洋大氣環境中的防護性能是衡量直升機海洋服役性能的重要指標。40CrNiMoA 結構鋼強度高,用于直升機起落架等承力結構,但耐腐蝕性能較差,通常采用涂層體系進行防護。由于對40CrNiMoA 結構鋼防護體系在海洋大氣環境中多因素耦合作用下的防護性能的研究較少,因此文中針對其在海洋環境中服役的耐腐蝕性能展開相關研究。
針對直升機結構鋼40CrNiMoA 的防護體系,利用模擬海洋大氣環境加速試驗方法,再現其在實際服役過程中出現的損傷形式和特征。通過電化學阻抗(EIS)、微觀形貌等方法研究其防護性能變化,為考核海洋大氣環境下服役的直升機結構鋼涂層體系的耐腐蝕性能提供數據支撐。
1 試驗
1.1 試驗件試
驗件為標準試片,尺寸為100 mm×50 mm×3 mm。
試驗件的材料、表面防護體系見表1。
1.2 實驗室加速試驗
模擬海洋大氣環境實驗室加速試驗方法見表2,其中紫外照射試驗采用美國Q-Panel 公司的QUV- SPRAY型紫外老化試驗箱進行,鹽霧試驗采用美國Q-Panel 公司的Q-FOG/CCT1100 型鹽霧試驗箱進行,周期浸潤試驗采用丹麥的CCX200 自然環境模擬綜合實驗箱進行,振動實驗在垂直振動臺和三綜合試驗箱中進行。結合相關模擬海洋環境加速試驗環境譜以及試驗件的工況環境,制定加速試驗方法,其中鹽霧試驗和周期浸潤試驗所用溶液的pH 均為2.0,以反應結構件實際服役過程中的酸性環境。另外,按照GJB 150.16A 序I 進行振動試驗,用來反映工況環境下結構件受到的振動作用。按照表2 所述試驗步驟,重復8 次,進行8 個周期試驗。
1.3 防護性能評價
目測檢查(試驗件外觀)借用放大鏡進行,試驗件表面的宏觀腐蝕現象采用NiKon D50 數碼相機在熒光燈下進行拍照記錄。采用VHX-100K 視頻顯微鏡和FEIQUANTA 600 環境掃描電子顯微鏡,對腐蝕過程中涂層的表面微觀形貌進行觀察分析。使用Princeton AppliedResearch Model 273A 恒電位儀和Signal Recovery 5210鎖相放大器進行電化學阻抗測試,利用三電極體系在3.5%中性氯化鈉溶液中完成,鉑作為輔助電極,飽和甘汞電極作為參比電極。將帶O 型圈的聚氯乙烯管壓在試驗件表面,使暴露在溶液中的測試面積為1cm2,并保持同一試驗件每次測試位置相同。測試區域在溶液中浸泡20 min,待開路電位穩定,測試過程中三電極體系置于法拉第籠中。測試的激勵信號為幅值10 mV 的正弦波,頻率的掃描范圍為0.1 Hz~100 kHz。
2 結果及分析
2.1 宏觀形貌
涂層A 的宏觀形貌如圖1 所示。初始狀態時,目測檢查涂層A 試驗件,表面涂層完整(圖1a)。
第2 周期加速試驗后,涂層A 表面局部區域出現肉眼可見的不連續鼓泡。在經歷每周期的鹽霧試驗和周期浸潤試驗后,鼓泡逐漸擴大,并在鼓泡處出現微小裂紋和輕微銹蝕,如圖1b、c 所示。產生鼓泡現象的原因可能是涂層與基體界面處存在某種氣體,氣體膨脹的力超過了涂層與基體的粘結力,導致涂層鼓起。
在該次試驗中,推測涂層表面可能存在微小缺陷,在鹽霧和周期浸潤試驗中,涂層暴露在高濕環境或浸入溶液中,水或水氣和腐蝕溶液從表面缺陷處滲透進入涂層,在金屬基體處積聚,產生相應的滲透壓,并發生腐蝕反應,引起體積膨脹,從而導致涂層鼓泡。隨著試驗周期的增加,鼓泡內壓力逐漸增大,在垂直方向上大大超過涂層界面上的粘結力時,將發生涂層表面龜裂,龜裂處基體腐蝕加劇,并沿著裂紋滲出,所以在后期鼓泡處出現銹蝕。為了研究涂層表面是否存在缺陷,后續對涂層微觀形貌進行觀察。
始時表面平整,無明顯缺陷。經過8 個周期加速試驗,表面未出現涂層粉化、開裂、起泡、剝落等現象,如圖2b 所示。根據宏觀形貌變化,可以初步看出,在模擬海洋大氣環境中,涂層B 的防護性能優于涂層A。
2.2 微觀形貌結果分析
采用視頻顯微鏡和掃描電子顯微鏡對不同周期加速試驗后的微觀形貌進行分析。圖3 為涂層A 的微觀形貌,可以看出涂層A 表面較為疏松,存在微米尺寸孔洞。試驗前,在局部位置存在微小的腐蝕銹點,尺寸約為2~5 μm(見圖3a)。隨著試驗周期的增加,發生腐蝕的位置不斷增多,產生了較多的紅色腐蝕產物(見圖3b、c)。這表明由于涂層A 結構較為疏松,局部位置存在孔洞,空氣及水分子已通過微孔與結構鋼基體接觸,并發生化學反應。金屬基體與有機涂層界面的主要反應方程式為:
圖 4 為涂層B 的微觀形貌,涂層B 表面較為致密。經過8 個周期加速試驗,表面未發生明顯變化,沒有銹蝕等現象出現,與前期的宏觀形貌結果一致。
2.3 電化學阻抗測試結果
單純根據形貌變化判斷涂層的防護性能往往是不充分的,因此采取電化學阻抗法進一步研究涂層的防護性能。由于電化學阻抗譜的詳細解析比較復雜,在工程上應用不便,因此通常采用電化學阻抗譜中低頻部分的阻抗模值作為檢測涂層防護性能變化的指標。相關研究結果表明,有機涂層低頻區的阻抗模值與其防腐蝕性能存在著對應關系,阻抗模值在≥109、108~109、107~108、106~107、≤106 Ω·cm2 范圍內時,涂層性能分別為優、良、中、差、很差。當有機涂層的交流阻抗模值低于107 Ω·cm2 時,就表明該有機涂層的防腐蝕能力已經下降,但仍具有一定的防護能力;當有機涂層的交流阻抗達到甚至低于106 Ω·cm2時,表明該有機涂層的防腐蝕能力已經很差,在有機涂層與基體金屬界面有可能已經發生了電化學腐蝕反應。由此106 Ω·cm2 可以作為有機涂層是否完全喪失防護能力的臨界值。
由圖 5a 可見,從試驗前到經歷了8 周期實驗室加速試驗過程中,在較寬的低頻區域,涂層A 的阻抗模值出現水平段,呈現電阻特征,說明涂層下基體的腐蝕已經發生。從表2 可以看出,試驗前涂層A 的特定頻率電化學阻抗模值|Z| f=0.1 Hz 的數值較低,為4.3×104 Ω。
表明在電化學阻抗測試過程中,溶液離子通過表面微孔,已與基體接觸發生電化學腐蝕反應,導致涂層的特定頻率電化學阻抗模值|Z| f=0.1 Hz 很低,說明該有機涂層的防腐蝕能力很差。隨著試驗周期的增加,電化學阻抗模值略有增加,表明隨著試驗周期的開展,腐蝕有輕微減緩的趨勢。這是因為腐蝕產物覆蓋在基體表面,對溶液離子的滲入產生了一定的阻礙作用,降低了腐蝕速率,提高了電化學阻抗模值。
由圖 5b 和表2 可見,從試驗前到經歷了8 周期實驗室加速試驗過程中,隨著頻率的變化,涂層B的阻抗模值呈現電容特性,不同周期后阻抗模值變化幅度微小。特殊頻率模值阻抗|Z| f=0.1 Hz 的數值一直保持在108~109 之間,處于較高數值,說明涂層防護性能較好,與前期分析結果一致。
結論文中通過模擬海洋環境的實驗室加速試驗,對比分析了兩種涂層的防護性能。
1)涂層A 結構相對疏松,經過8 個周期實驗室加速試驗后,溶液通過涂層表面孔洞滲入,引起基體腐蝕,導致涂層局部鼓泡。同時,涂層A 的電化學阻抗譜阻抗模值|Z|f=0.1 Hz 也相對較低,說明涂層耐腐蝕性能較差。
2)涂層B 結構相對致密,試驗前表面完整,無明顯缺陷。經過8 個周期實驗室加速試驗后,涂層表面未出現涂層粉化、開裂、起泡、剝落等現象。同時,涂層B 的電化學阻抗譜阻抗模值|Z|f=0.1 Hz 也相對較高,說明涂層耐腐蝕性能優異。
3)對于涂層A 試驗件,可以嘗試改善涂層涂覆工藝,改變涂層結構,降低孔隙率,從而提高其耐腐蝕性能。
免責聲明:本網站所轉載的文字、圖片與視頻資料版權歸原創作者所有,如果涉及侵權,請第一時間聯系本網刪除。
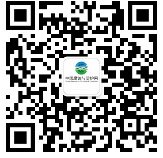
官方微信
《中國腐蝕與防護網電子期刊》征訂啟事
- 投稿聯系:編輯部
- 電話:010-62313558-806
- 郵箱:fsfhzy666@163.com
- 中國腐蝕與防護網官方QQ群:140808414