事故背景
某井油管下井投入使用6個月后,發現電潛泵運行正常,但產量降低,初步判斷為油管發生泄漏,于是關井停產。起泵檢查發現,泄漏位于泵出口上端400m處的油管接頭。此處深度約2640m,溫度為83℃,壓力為26MPa。管內介質為油含水,其中水含量為18.5% (體積分數),產量為800m3·d-1。該井不含H2S,CO2含量為6.1%(體積分數)。入井前油管均為新油管,規格為?88.9mm×6.45mm,L80鋼級。
理化檢驗
1 宏觀分析
圖1 泄漏油管接頭宏觀形貌
如圖1所示,螺紋部位腐蝕極其嚴重,原有的螺紋齒已基本被腐蝕掉,表面有較明顯的腐蝕產物,且腐蝕產物與基體結合較好,不易剝落。
圖2 泄漏油管接頭截面形貌
從圖2可以看出:管體部位內壁和外壁均腐蝕較輕,無明顯的腐蝕坑和壁厚減?。宦菁y部位內表面腐蝕較輕,無明顯的腐蝕坑和壁厚減薄,但外表面螺紋處腐蝕極其嚴重,存在明顯的壁厚減薄現象,最大壁厚減薄量約2.8mm,對應的最大腐蝕速率為5.6mm·a-1。
2 金相分析
對油管發生腐蝕的螺紋部位取樣,依據GB/T 13298-2015,GB/T 10561-2005,GB/T 6394-2017進行顯微組織、非金屬夾雜物、晶粒度檢驗分析,并對試樣內、外表面的腐蝕坑及裂紋進行觀察分析。
圖3 油管螺紋部位顯微組織形貌
圖4 油管螺紋部位外表面腐蝕坑形貌
圖5 油管螺紋部位外表面腐蝕坑周圍變形組織形貌
結果如下:油管螺紋部位顯微組織為回火索氏體,晶粒度為9級,可見油管顯微組織無異常,晶粒細小,且無超尺寸非金屬夾雜物,如圖3所示;油管螺紋部位外表面存在明顯的腐蝕坑,局部腐蝕坑坑底發現有裂紋,裂紋內填滿灰色物質,腐蝕坑周圍顯微組織亦為回火索氏體,但局部組織存在變形,如圖4和圖5所示。
3 化學成分分析
依據ASTM A751-2014對泄漏油管進行化學成分分析,結果見表1。
表1 油管化學成分分析結果(質量分數)
可見該油管的化學成分符合API SPEC 5CT-2018要求。
4 腐蝕微觀形貌分析
圖6 油管螺紋部位外表面SEM形貌
如圖6所示,油管螺紋部位外表面存在明顯的腐蝕產物,晶體相互穿插,堆垛非常致密,但有大量的裂紋及孔洞。
5 腐蝕產物成分分析
表2 油管螺紋部位外表面腐蝕產物EDS分析結果
如表2所示,油管螺紋部位外表面腐蝕產物中主要含有鐵、碳、氧元素,另還含有鈣、鎂、鈉等元素。
圖7 油管螺紋部位外表面腐蝕產物XRD譜
如圖7所示,油管螺紋部位外表面的腐蝕產物主要為FeCO3。
模擬工況腐蝕試驗試驗
材料為50mm×10mm×3mm的L80鋼掛片,由現場所取管段加工而成。依據油管的現場服役工況,在高溫高壓釜內進行模擬腐蝕試驗,分析L80鋼在現場環境下的腐蝕行為。水樣分析結果如表3所示,試驗參數如表4所示。
表3 腐蝕介質的成分
表4 腐蝕試驗參數
表5 L80鋼試樣腐蝕試驗結果
由表5可見,試樣平均腐蝕速率為0.0853 mm·a-1,根據NACE RP0775對腐蝕程度的分級,屬輕度腐蝕。
圖8 腐蝕試樣表面微觀形貌
由圖8可見,試樣表面腐蝕比較輕微,無明顯的腐蝕坑,可觀察到原始表面的磨痕,僅存在少量的腐蝕產物,在掃描電鏡下腐蝕產物的形態與現場管樣螺紋部位外表面的腐蝕產物形態相同。
綜合分析
1 腐蝕機理分析
能譜及X射線衍射分析結果表明,試樣表面腐蝕產物主要為FeCO3,為典型的CO2腐蝕產物。模擬工況腐蝕試驗后的試樣表面腐蝕產物形態與現場管樣螺紋部位表面腐蝕產物的形態相同,在掃描電鏡下可觀察到表面是相互穿插的斜六方晶體結構。油管螺紋部位表面的腐蝕產物類型及形態均呈現出典型的CO2腐蝕產物特征。結合該井的工況特點,該井不含H2S,CO2含量為6.1%,地層水礦化度較高,由此可初步判斷存在CO2腐蝕。
CO2引起油套管材料的電化學腐蝕是氫去極化腐蝕,在夾雜物、晶界等處,H+ 被還原成氫原子,隨后聚合成氫氣析出。CO2腐蝕機理如下:
能譜分析結果顯示,腐蝕產物表面鈣元素含量較高,但X射線衍射譜中沒有出現含鈣化合物CaCO3,這主要是因為在腐蝕過程中,溶液中的Fe2+含量與CO32-含量乘積[Fe2+]×[CO32-]超過FeCO3的溶度積Ksp時,FeCO3在材料表面沉積成膜,形成外層腐蝕產物膜,而Ca2+則取代FeCO3中的Fe2+形成(Fe,Ca)CO3復鹽。
2 螺紋接頭腐蝕集中分析
模擬工況腐蝕試驗結果表明,在現場的介質和工況條件下,L80鋼的腐蝕速率僅為0.0853mm·a-1,屬輕度腐蝕。然而,現場管樣的螺紋表面腐蝕相當嚴重,輪廓已模糊不清,最大腐蝕速率達5.6mm·a-1,而內壁及與螺紋連接的管體腐蝕相對較輕,因此油管的腐蝕主要集中在螺紋部位,且在該部位存在局部加速的現象。金相及掃描電鏡分析結果顯示,螺紋部位表面存在大量的裂紋及孔洞,且局部組織存在變形,據此可以判斷,該油管在下井時,螺紋部位存在粘扣現象,從而導致螺紋接頭的密封性能下降。因此,油管腐蝕局部集中主要是由于螺紋連接處高礦化度地層水及CO2等腐蝕介質的滲入,形成了縫隙腐蝕,如圖9所示。
圖9 油管螺紋連接示意圖
其腐蝕過程包括兩個階段:
①縫隙內外的金屬表面發生相同的陰、陽極反應;②隨著反應的進行,縫隙內介質逐漸被消耗,而縫隙外的介質向縫隙內擴散較慢,使縫隙內外介質含量差增大,從而形成濃差電池,其中縫隙外介質供給充分,形成陰極,而縫隙內則形成陽極,致使縫隙內的金屬發生腐蝕,而縫隙外金屬受到保護。
結論及建議
(1)該L80油管螺紋接頭表面的腐蝕產物主要為FeCO3,腐蝕局部集中主要是由于油管在下井時,螺紋部位存在粘扣現象,從而導致螺紋接頭的密封性能下降,高礦化度地層水及CO2等腐蝕介質滲入螺紋連接處,形成了縫隙腐蝕。
(2)建議進一步規范油管上扣作業過程,嚴格執行相關操作規程,避免油管螺紋發生粘扣現象。
免責聲明:本網站所轉載的文字、圖片與視頻資料版權歸原創作者所有,如果涉及侵權,請第一時間聯系本網刪除。
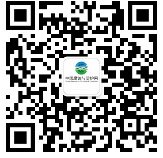
官方微信
《中國腐蝕與防護網電子期刊》征訂啟事
- 投稿聯系:編輯部
- 電話:010-62313558-806
- 郵箱:fsfhzy666@163.com
- 中國腐蝕與防護網官方QQ群:140808414