材料是現代科學技術發展和經濟建設的重要支柱,就航空來說,材料是航空工業實現現代化的物質基礎,先進的飛機和發動機設計方案,必須有相應的航空材料和精湛的制造技術方能實現。新中國成立以來,我國航空工業從無到有、到壯大走過了一段艱辛的歷程。
材料是現代科學技術發展和經濟建設的重要支柱,材料對于增強國防能力和國際競爭力起著決定性作用,所以世界各國都把材料研究列入本國的關鍵技術計劃。就航空來說,材料是航空工業實現現代化的物質基礎,先進的飛機和發動機設計方案,必須有相應的航空材料和精湛的制造技術方能實現。
有資料表明,飛機性能的提高,發動機性能的改善,在很大程度上受材料的制約。因此,材料在航空工業中的位置就不言而喻了。航空材料品種繁多,涉及范圍廣泛,性能要求高,可靠性要求嚴格,又要易于加工,成本也不能太高,這對材料科學工作者來說,既是一個機遇,又是一個挑戰。一種新型材料從研究到應用,少則幾年,多則十幾年;
即使一種在市面已流通多年的傳統材料,用于航空也要有特殊的規定。可以說,我國航空工業從無到有、到壯大走過了一段艱辛的歷程。
我國航空材料發展的艱辛歷程
1、領導重視,組織得力,有一個良好的起步
早在1950年年底,周恩來總理在一次研究中國航空工業建設問題的會議上指出:“中國航空工業的建設道路,要從中國的實際出發,先修理后制造,再發展到自行設計。原則是由小到大,在設計修理廠時,就要考慮到日后轉變為制造廠的安排和部署,同時,爭取蘇聯幫助我們建設航空工業。”在這一方針指引下,我國航空工業獲得了迅速發展。 新中國航空工業在創建初期,國家的基礎工業極其薄弱,盡管當時所用的材料可以從蘇聯進口。但從建設獨立自主的完整的航空工業出發,國家領導人十分注意航空材料生產立足國內,如1952年4月,中央財經委副主任李富春召集會議專門研究航空工業走上自行制造所需解決的問題,陳云副總理到會明確指出:“走向飛機制造最困難的是技術人員和原材料問題。如果原材料不能立足國內,那才是最大的困難。”根據這一論斷,國家重點安排了航空材料生產基地,并促進了航空材料研究機構的建立。 我國第一個五年計劃期間,由冶金、化工、機械、紡織、輕工等工業部門直接組織,挑選了一批設備和技術力量都比較好的企業,承擔航空材料的試制生產。陳云副總理率領冶金工業部部長王鶴壽到撫順、沈陽等地現場研究解決高溫合金的試制問題。決定把撫順鋼廠擴建成第一個高溫合金生產基地;把沈陽橡膠四、五廠建成航空橡膠制品基地;把錦西化工廠建成航空有機玻璃生產基地;把沈陽橡膠三廠、天津油漆廠分別改建為飛機輪胎和航空油漆生產基地等等。在改造和擴建以上老企業的同時,國家還投資興建了一批以承制航空材料為主要任務的大型企業,如哈爾濱鋁合金加工廠、鞍鋼第二冷拔無縫鋼管廠等。 隨著以上企業的建成,航空材料的自給率顯著提高。如在哈爾濱鋁合金加工廠組成了航空鋁合金材料試制組,經過近一年的努力,試制成功了近20個牌號的板材、棒材、型材、管材和絲材,滿足了航空工業使用的90%變型鋁合金。鞍鋼第二冷拔鋼管廠投產后,航空工業所需管材的93%得到了解決。當時,我國成批生產的初教5飛機、М11ФР發動機和殲5飛機、渦噴5發動機所需原材料的自給率分別達到98%、96%、81%和78%。
1956年3月,由撫順鋼廠、鞍山鋼鐵公司、鋼鐵工業試驗所(北京鋼鐵研究總院前身)、沈陽發動機廠和航空材料研究所共同試制我國第一個高溫合金ЭИ435,并成立了以冶金部劉彬副部長、鋼鐵局李振南副局長為正副組長的領導小組,蘇聯專家也參加指導,但兩次試制都告失敗。同年6月試制過程中,強化了脫氧制度,才軋出板坯,送鞍山冷軋出板材,在沈陽發動機廠制成火焰筒,1957年在渦噴5發動機上通過了長期試車,至此,宣告我國第一個高溫合金試制成功。因為當時未及時成批生產,直到1960年正式投產,但在成批生產后,又發現板材焊接性能不穩定,火焰筒出現裂紋。為排除故障,1961年組成工作組,由航空材料研究所吳世德和鋼鐵研究院傅宏鎮負責,在榮科、師昌緒等專家指導下,經過頑強努力,解決了一個又一個技術關鍵,于1962年合金質量問題終被攻克。這一事實,使我們深刻認識到,試制一個合金,只簡單地達到技術條件的要求遠遠不夠,還必須經過批量生產,掌握合金的生產工藝,經過嚴格考驗,才算成功。這也為以后研制高溫合金積累了經驗。
以上是航空工業創建初期,為解決航空材料立足于國內而改建和擴建的第一批航空材料試制生產基地,正是由于這些企業的艱苦努力,及有關人員的積極配合,保證了我國飛機和發動機試制工作的順利進行。
2、自力更生,大力協同,千方百計,保證航空材料供應
為適應航空工業的需要,把航空材料研究所的建設列入蘇聯援建重點156項之一,在蘇聯專家指導下,于1956年正式成立。同時各工業部門和中國科學院對新材料的研究與開發也予以加強。如中國科學院金屬研究所由以為鋼鐵服務為主,1957年轉向新材料、新技術研究與開發;冶金部鋼鐵工業試驗所、有色金屬研究所的科技力量大大加強而改為北京鋼鐵研究院、北京有色金屬研究院,主要從事新材料、新技術的研究與開發。此外,上海鋼鐵研究所、錦西化工研究院、北京化工研究院、北京橡膠研究院、長春應用化學研究所等單位也都開展了有關航空材料研究與開發工作。同時,還陸續興建了一批材料生產或加工基地,如上海鋼鐵三廠、上海鋼鐵五廠、長城鋼廠、大連鋼廠、東北鋁加工廠、西南鋁加工廠等。還有一些高等院校,如北京航空學院、西北工業大學、北京鋼鐵學院、南京航空學院、上海交通大學等,除培養材料技術人員外,還承擔了許多科研任務。北京鋼鐵學院及東北工學院成立了高溫合金和精密合金等專業。
1960年,前蘇聯中斷新材料的供應,中共中央、中央軍委分別召開專門會議,決定組織全國力量,全面解決航空材料的供應問題。薄一波副總理到撫順鋼廠,研究安排高溫合金的試制生產,并由冶金部以104號專案任務,緊急下達鞍山鋼鐵公司、撫順鋼廠等全國10大鋼廠共同完成各項任務。為解決殲6飛機所需關鍵材料,1961年又下達了105號專案任務。為了完成高溫合金研制任務,成立了由冶金部鋼鐵司司長劉伯樂、航空工業局副局長方致遠、鋼鐵研究院副院長吳峰橋、航空材料研究所所長魏祖冶等組成的試制協調小組,組織鋼鐵研究院、航空材料研究所、中國科學院金屬研究所、撫順鋼廠和沈陽發動機廠協同攻關。經4年多的不懈努力,終于掌握了高溫合金的冶煉、軋制、模鍛等工藝,取得了成功。至1965年,航空工業所需的高溫合金滿足了需求。 為了突破高溫合金的關鍵,冶金部在撫順鋼廠、齊齊哈爾鋼廠、大冶鋼廠和上海鋼鐵五廠、重慶102廠建立了真空冶煉爐和電渣冶煉爐。為了解決高溫合金原料問題,加速甘肅鎳礦的建設,改造了上海冶煉廠以承擔金屬鎳的提純。第一機械工業部副部長、著名機械工程專家沈鴻親自抓高溫合金冷軋機的制造。
在此期間,冶金、機械等部門在馬鞍山、德陽、重慶建立了大型鍛壓和軋制加工基地,解決了航空大型鍛件和鋁加工問題;在西南建立了長城鋼廠作為特殊鋼的生產基地之一。
到1965年,批量生產的殲6飛機所需的12319項原材料和直5所需的9019項原材料,全部由我國756家廠、所提供。我國自行設計的高空高速殲擊機殲8所用整體壁板、耐高溫透明材料、氟塑料高壓軟管、金屬軟管等關鍵材料也都是靠自力更生,全國各單位大力協同解決的。
3、利用國內資源,開發我國航空材料
新中國建國初期,冶煉高溫合金的鎳、鉻奇缺,又受到國際嚴密封鎖。所以1957年中國科學院金屬研究所高溫合金組工作一開始,便提出我國應開展以鐵基代鎳基高溫合金及稀土金屬在高溫合金中的作用兩個研究課題,并分析了當時鎳基高溫合金用量最大的是ЭИ437Б(GH33),于是與撫順鋼廠合作設計出808合金(GH135),并軋成棒材,模鍛出渦輪葉片,但在試車過程中發生了共振而告失敗。隨后,北京鋼研院和上海鋼研所分別開發出可代ЭИ617作為渦輪葉片的紅星13(GH130)及JF43(GH302),雖然都通過了長期試車,但沒有真正代替ЭИ617作為葉片用于發動機,卻廣泛用做增壓器等部件材料。由于20世紀60年代初我國最常用的ЭИ481(GH36)渦輪盤經常出現故障,困惑著從事高溫合金研究的科技人員,于是用于葉片失敗的808合金又轉向渦輪盤;在北京鋼鐵學院主持下又開發出美國常用的兩個渦輪盤牌號A286(GH132)及V57(GH136),為了解決引進斯貝發動機的需求,又組織全國力量試制了Incoloy901(GH109)。根據《中國高溫合金40年》的統計,我國開發了30多種鐵基高溫合金,其中18種為獨創。GH135(808)作為棒、盤材料起到開路先鋒作用,而GH140(GR2)作為板材在我國開發的所有鐵基高溫合金中最富成效。 GH140(GR2)是航空材料研究所于1958年開始研究的我國第一個板材鐵基高溫合金。它是以ЭИ703合金為基礎,利用我國富有的鎢、鉬、鋁、鈦元素對合金進行綜合強化,經過多項試驗研究,突破冶煉和變形兩個難關,確定了合金的基礎成分后,與撫順鋼廠、鞍山鋼鐵公司、沈陽發動機廠合作,進行半工業性擴大試驗,制成渦噴6發動機火焰筒,經二次長期試車考驗。1962年在撫順鋼廠進行工業性擴大試驗,克服了“重皮”和晶粒度偏大的問題。1966年生產定型,并逐步擴大在10多種發動機和飛機上使用,材料品種有薄板、中板、棒材、熱軋管、冷拔管、絲材、環形件、鍛件等。目前幾乎所有特鋼廠都能生產這種合金,成為我國航空工業使用最廣,生產量最大的高溫合金牌號之一。截止到1977年,各鋼廠累計生產7000余噸,節鎳3000多噸。
鈦是重要的航空航天材料,我國資源豐富。所以1956年鈦的研究與開發列入了《我國12年科技規劃》。因而冶金部很快建立了海綿鈦及鈦的生產基地(撫順301廠、蘇家屯有色加工廠)。航空材料研究所建所之初就組建了以顏鳴皋為首的鈦合金研究室,從建立設備開始,于1958年煉出了第一個用于研究的鈦合金錠。與此同時,冶金部有色金屬研究院、上海鋼研所及中科院上海冶金所等單位也都開展了鈦合金的研究工作。
1965年航材所與有關科研院所、鋼廠及航空發動機廠研制成功鈦合金中用量最大的TC4(Ti-6Al-4V),用于渦噴6發動機壓氣機盤及葉片。
1979年航空材料研究所與上海鋼鐵五廠、北京有色金屬研究院等單位合作在原蘇聯BT9的基礎上開發出了用于500℃的高溫鈦合金,他們采用先進鑄錠工藝,解決了偏析問題,采用高低溫交替鍛造工藝,解決了大鍛件組織不均勻的難題,綜合性能超過國外同類產品水平。作為盤件材料用于多種型號發動機。
4、與時俱進,鑄造高溫合金及精密鑄造工藝取得令人矚目的成就
上世紀50年代末,我國提出“以鑄代鍛”的戰略方針。航空材料研究所榮科副所長在這方面做出了突出貢獻。在他的指導下,航材所開發出在前蘇聯已定型的鑄造鐵基高溫合金(K11、K14)及鑄造鎳基高溫合金(K1、K3),采用精密鑄造工藝,制成形狀復雜的導向葉片和渦輪葉片,用于渦噴發動機。要強調指出的是榮科協助各航空發動機廠建立了精鑄車間,發展精鑄工藝,為我國鑄造合金的應用創造了條件。 關于鑄造渦輪葉片材料,“東風113”航空發動機方案提出以后,國內航空材料界給予極大的關注,據了解,鋼研院設計了511合金,金屬所則設計了539合金,都比當時蘇聯最高牌號ЭИ929有更高的高溫性能。但當時變形十分困難,雖然利用蘇家屯有色金屬加工廠1200噸擠壓機擠成棒材,并使用包套擠壓工藝得出了棒材,但是畢竟設備噸位太小,難以滿足要求。于是金屬所便利用1957年從瑞士進口的5kg真空感應爐開展精密鑄造高溫合金的研究,最后確定了一個不含鈷而性能與當時國際水平相當的916合金,盡管從高溫強度或塑性來看都不亞于正在開發的變形合金,但是當時工廠不具備生產條件,只好作罷,這應該算是我國第一個鑄造渦輪葉片用鎳基高溫合金,合金雖然沒有得到應用,但推動了我國真空冶煉和真空精鑄工藝和真空感應爐的發展。1962年為使我國直升機能飛入西藏上空,又仿制了當時美國最成熟的鑄造合金IN100(M17,K417)作增壓器,航空材料研究所及鋼鐵研究院于1965年前后開發K5、K6及仿IN713C的K18。這就是早期我國鑄造鎳基高溫合金發展的一段歷史。從中可以看出,一方面需求牽引十分重要,另一方面知識儲備(確切的說是人才儲備)、技術儲備與裝備儲備是完成急需任務最重要的條件。
鑄造高溫合金的發展關鍵是鑄造工藝的不斷改進。1958年我國就開始用真空感應爐冶煉加真空精鑄,從而開發出鑄造渦輪葉片、空心渦輪葉片。1988年采用泡沫陶瓷開發出鑄造高溫合金過濾凈化技術,對返回料的應用創造了條件。
20世紀60年代中期,美國開發了定向凝固技術,1967年航材所率先在自制定向凝固爐上開發了高溫合金定向凝固技術,20世紀70~80年代研制出幾種定向凝固高溫合金(DZ3、DZ4、DZ22),其中不含鉿的DZ4已批量生產,并在10多種發動機上得到應用。90年代,航材所又發展了單晶高溫合金葉片制造工藝,并開發出單晶高溫合金(DD3、DD4、DD6、DD402等),同時還發展了單晶渦輪轉子葉片鑄造工藝。DD3成分簡單,強度高,但有熱裂傾向,未能推廣,在加入適量的鉭以后,不但解決了熱裂傾向,而且高溫性能有所提高,現已推廣到多個機種,成為我國真正用于航空的第一代單晶合金。
中科院金屬所在國內最早開發了用于工業燃氣輪機的耐熱腐蝕高溫合金K38(IN738),后又進行了改進成為K38G,為了滿足斯貝發動機用于艦艇的要求,與西安發動機廠合作開發出用作渦輪葉片的DZ38G及DD8合金。
另外,在鑄造高溫合金方面有幾項原始創新的成果,那就是低偏析高溫合金、Ni3Al基的合金及快速定向凝固工藝。金屬所在深入研究合金凝固時發現某些微量元素是高溫合金在凝固過程中發生偏析的重要因素,因而控制這些元素的含量,可以降低偏析,這就會提高合金的性能和穩定性(長期使用不出現脆性相)。再者對定向凝固合金可以不加鉿(如DZ125L),如此等等。
西北工業大學利用磁場約束及高溫度梯度技術研制定向凝固葉片,完全免去與坩堝接觸而得到高純度材料,現已具雛形。 航空材料研究院開發出以中間化合物Ni3Al為基的葉片材料(IC6),成分簡單,初熔溫度高,已制出導向葉片,首次以鎳基中間化合物做成葉片應用于航空發動機。
5、新型航空材料----先進復合材料和功能材料發展迅速,取得了一系列成果
所謂先進復合材料是指以樹脂為基,以有機纖維、碳纖維或玻璃纖維為增強劑的復合體,具有高比強度、比剛度、消震好的一類材料。先進復合材料在航空工業中十分重要,如美國20世紀70年代生產的F22機中用量占24%。現代民機占14%左右,現代直升機所占比例更高,有的超過了50%。
近10年來,我國復合材料科研、生產、應用技術得到了大幅度提高,其中包括了“七五”、“八五”、“九五”預研和型號任務的成果并在飛機上得到較多的應用,不僅用于軍機,在民機、直升機、發動機上也得到應用。例如沈陽飛機設計所、航空材料研究院和沈陽飛機廠共同研制殲擊機復合材料垂尾壁板,比原鋁合金結構輕21kg,減重30%。這是“六五”期間研制成功的最大的航空復合材料構件。北京航空工藝研究所研制并生產的QY8911/HT3雙馬來酰亞胺單向碳纖維預浸料及其復合材料已用于飛機前機身段、垂直尾翼安定面、機翼外翼、阻力板、整流壁板等構件。西北工業大學與復合材料特種結構研究所共同研制和生產的4501A雙馬來酰亞胺樹脂及其復合材料已用于成形人工介質雷達天線罩和其他類型的高性能雷達天線罩。由中國科學院化學研究所研制并生產的KH-304熱固性聚酰亞胺樹脂和由中國航天工業總公司北京材料工藝研究所研制并生產的KH-304/HT3復合材料,已應用于航空發動機外涵道。由北京航空材料研究院研制的PEEK/AS4C熱塑性樹脂單向碳布預浸料及其復合材料,具有優異的斷裂韌性、耐水性、抗老化、阻燃性和抗疲勞性能,適用于制造飛機主承力構件,可在120℃下長期工作,已用于飛機起落架艙護板前蒙皮。 當前,我國復合材料總的水平相當于國外20世紀80年代中后期的水平。復合材料還用于衛星、兵器、電子工程等,也用于體育用品,醫療器械、紡織機械等方面。
先進的復合材料還應包括金屬基復合材料及陶瓷基復合材料,但目前在航空工業用量極少。 功能材料在當今信息時代無疑是最重要的一類材料,因而發展非常迅速。對航空飛行器來說,信息功能材料也愈來愈重要。從1991年海灣戰爭實踐證明:機載電子設備能力提高一倍,飛機戰斗力可提高7倍;裝有電子裝置的戰斗機損失率僅2%~3%,否則高達20%。所以現代飛機的機載裝置所占比重愈來愈大,一架先進軍用機的機載設備費用占到整機的1/3左右。機載設備的關鍵材料主要是各種微電子、光電子、傳感器等光、聲、電、磁、熱等的高功能及多功能材料,種類繁多。要求高:高靈敏度、高可靠性、小型化、智能化、高準確度、抗干擾能力強等。例如,由電子工業部研制的摻釹釔鋁石榴石,已廣泛應用制作各類激光器件;由中國科學院上海光學精密機械研究所研制并生產的激光玻璃,已用于制作大功率激光聚變系統以及材料加工、激光測距、激光通訊跟蹤、激光干涉等領域用的激光器;由電子工業部、中國科學院半導體研究所、北京有色金屬研究總院等研制的GaAs半導體激光材料是制作激光器的主要材料,已廣泛用于制作半導體激光器;由兵器工業總公司、航天工業總公司、電子工業部和中科院上海技術物理所等研制的碲鎘汞(MCT)n型材料,已成功用于制備長波多元光導型MCT紅外探測器系列和短波光伏型MCT紅外探測器;由北京玻璃研究院、電子工業總公司、兵器工業總公司等研制的高雙折射偏振保持光纖已用于光纖傳感器;由上海硅酸鹽研究所、清華大學、上海大學、南通中海氮化物公司等研制的微波介質陶瓷材料已用于介質諧振器(濾波器、振蕩器)、集成電路基片和衰減材料;由清華大學、西安近代化學研究所研制的液晶材料,作為顯示材料廣泛用于航空、航天和電子工業;作為有序溶劑用于立體選擇反應;作為固定相應用于色譜分析以及各種顯示屏。
用功能材料所制成的各種器件、機載設備、火控系統、各種傳感器和電子設備,是現代飛機的“眼(雷達)、耳(電臺)、腦(計算機)、神經(電纜與光纜)及血管(油管)”,此外,為提高飛機的生存能力還要穿上一層外衣(隱身)。功能材料繁多,用途各異,發展很快,而且很多功能材料寓于元器件之中,更是五花八門。
6、鋁、鈦合金及復合材料具有先進性和帶動性
從現代飛機機體使用的結構材料可以看出,除性能很高的F22以外,鋁合金仍占重要地位。鈦合金及復合材料的比例隨飛機性能的提高而增加。
20世紀90年代國際上最先進的戰斗機以美國的F22為代表,民用飛機以波音777為代表,其機體用材特點是大量采用了高比強度、高比模量的輕質、高強、高模材料,顯著提高了飛機的結構效率,降低了飛機結構重量系數,具體表現為鈦合金代替鋼,樹脂基復合材料代替鋁合金。因此,大力發展高強高韌高比模的鈦合金及樹脂基復合材料是航空材料發展的重要方向。但是鋁合金在現有飛機結構件中仍占十分重要位置,所以近10多年來,我國高強、高韌、高耐蝕新型鋁合金進一步得到發展,除了提高了原材料的純度,降低了雜質外,還通過熱處理進一步提高了鋁合金的綜合性能,延長了使用壽命。 對于鈦合金的研究,我國雖然起步較晚,但從1986年開始的第7個五年計劃,對鈦合金研究的投入顯著增加,研究成功了近代飛機所需的各種類型的鈦合金。目前,我國飛機上鈦合金的用量與國外相比,顯然仍很低。 航空發動機的要害是提高推重比和降低油耗,因此高溫材料是決定性因素。在一臺先進發動機上,高溫合金和鈦合金分別占發動機總重的55%~65%和25%~40%,所以研發高溫合金及鈦合金對提高發動機性能來說至為重要,其中渦輪葉片及渦輪盤材料更為關鍵,因受力復雜且處于高溫高速高壓的狀態中,工作時間又長。總的來看,我國高溫合金已形成了比較完整的體系,但從水平來看與需求還有不小差距。 此外,還有一大批先進樹脂基復合材料、座艙玻璃材料、橡膠密封材料、先進涂層和鍍層、功能材料等,體現了20世紀90年代國際航空材料發展水平,滿足了我國現代批量生產飛機、發動機、機載設備對材料的需求,也為設計新一代航空產品做了一定的技術儲備,具有鮮明的先進性。
航空材料質量要求高,品種規格多,和其它高技術一樣,對我國材料制造技術和制造業有很強的帶動性。如發展很快的工業燃氣輪機所需高溫材料,在很多方面是在航空用高溫合金的基礎上進行開發的。只是工業燃氣輪機所要求的葉片與輪盤尺寸大,工作時間長,又要耐熱腐蝕,難度更大一些。
7、強化檢測是現代航空材料的一個重要標志
航空材料由于把安全放在首位,除了對材料的原料選擇及對每一項生產工序必須嚴格掌握以外,就是加強檢驗和嚴格測試。測試項目隨設計思想的演變而變化。以發動機用高溫合金為例,1960年前發動機采用靜強度設計,對材料只要提供“五大指標”(σb、σ0.2、δ、ψ、αk)再增加持久性能就滿足要求了;1960年以后,進入安全壽命設計,要以高周疲勞S-N曲線來評估;1970年以后,采用有限壽命設計,用應變疲勞ε-N曲線來評估壽命;1980年以后,發動機設計在斷裂力學基礎上,提出了損傷容限設計、概率設計,對材料性能要求越來越多,越來越高,除基本性能外,還要求有統計性能、使用性能、斷裂韌性和疲勞裂紋擴展速率等等。設計部門提出:渦輪葉片材料必須具有6種溫度下的短時力學性能(σ0.1、σ0.2、σb、δ、ψ、σ-ε、σbH、τ0.3、τb)、4種溫度下的持久曲線(L-M、σ-t)和蠕變曲線(ε-N、σ-ε)以及斷裂韌性(KICDa/dN)等97項性能數據;低壓壓氣機零件材料需要79項;轉子葉片材料需要85項;燃燒室材料需要78項;渦輪盤材料需要76項性能數據。 中國航空材料體系形成 回顧我國航空材料由仿制,到仿中有創新的發展歷程,使航空材料從無到有,品種規格逐步齊全,質量達到產品要求,實現立足于國內的目標。通過改進工藝路線,提高材料質量;同時,結合國內資源創造我國自己的航空材料,擴大航空材料研究、生產的規模,增加品種,逐步形成了有中國特色的航空材料體系。
現僅就高溫合金為例,討論體系的形成過程和特點。我國早期為保證發動機的生產而開發所需高溫合金。
1956年在撫順鋼廠生產第一個高溫合金板材ЭИ435(GH30)時,曾得到前蘇聯專家的幫助,而后幾乎所有高溫合金都是自主開發的,有的參考國外成分,有的是自行設計的,由研究、生產和使用部門共同開發,一直達到投產。由于每引進一種發動機就要仿制一批高溫合金,所以我國高溫合金牌號的數目在國際上都居前列。 總的來看,中國高溫合金繼英、美、前蘇聯之后已形成了一個完整的體系,雖然還需要進一步調整,也還存在空白需進一步開發等等。 中國高溫合金在生產工藝方面也有自己的特點,如中國是最早采用電渣重熔工藝,并發展為真空電渣重熔工藝,不但可以減少夾雜物,也可降低氣體含量。早在1958年就采用包套擠壓工藝使難變形合金錠變為棒材;而后發展為包套軋制,包套鍛造。不但用于軋制棒材,而且用于生產餅材或盤材,解決了我國壓力機能力不足的問題。 可以說,我國高溫合金從20世紀50年代中期開始至70年代末,只用了20多年時間就基本形成了具有中國特色的體系。高溫合金是這樣,其它航空材料走過的道路與高溫合金相似,也都有結合國情、結合國家資源創新的成就。因此,航空材料形成了有中國特色的體系。
盡管我國航空材料研制取得了令人矚目的進步,但我們的路還很長,任務還很艱巨。當我國在發奮努力工作并取得成就的時候,一些發達國家在許多方面可能以比我國快得多的速度取得新的突破,例如飛機隱身材料、金屬基和陶瓷基復合材料、納米材料以及原有材料的改進,一材多用的技術等等。當我國正在研究推重比高的發動機和新一代飛機的時候,發達國家已經研究更高推重比的發動機和第五代、第六代的飛機了。我國不僅要在科學技術付諸很大努力,也要在體制上打破部門壁壘,充分調動有關科技人員和企業的積極性,全國一盤棋,向著一個共同目標--為實現我們的航空工業現代化而奮斗!
免責聲明:本網站所轉載的文字、圖片與視頻資料版權歸原創作者所有,如果涉及侵權,請第一時間聯系本網刪除。
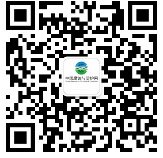
官方微信
《中國腐蝕與防護網電子期刊》征訂啟事
- 投稿聯系:編輯部
- 電話:010-62313558-806
- 郵箱:fsfhzy666@163.com
- 中國腐蝕與防護網官方QQ群:140808414